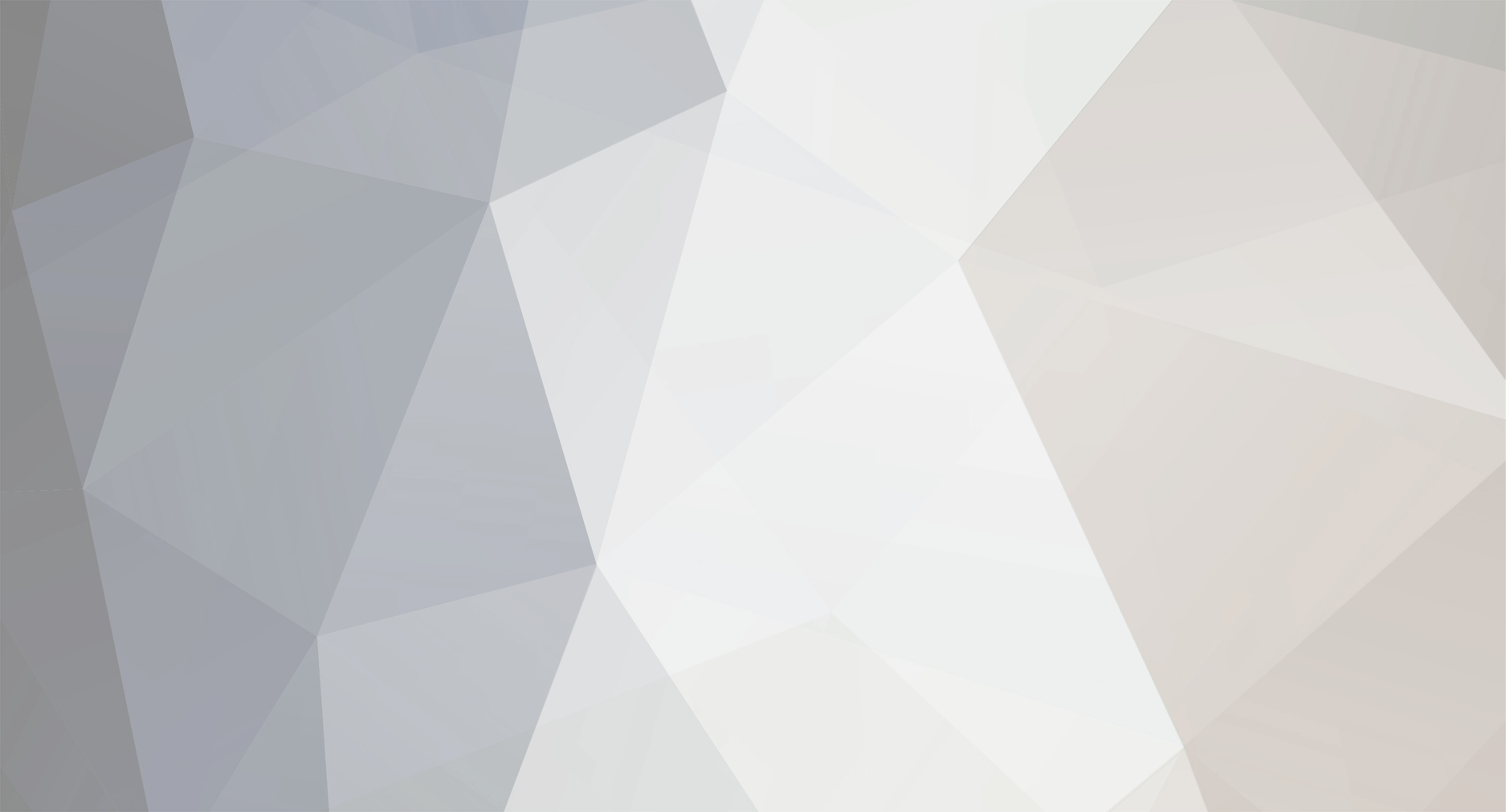
gilmour
Member-
Posts
793 -
Joined
-
Last visited
Content Type
Profiles
Forums
Events
Shop
Articles
Everything posted by gilmour
-
[quote name='Spacehog' post='965934' date='Sep 23 2010, 06:30 PM']Nice build Gilmour, i'm now starting 2 112's. what pu adhesive did you use?[/quote] [url="http://www.screwfix.com/prods/44485/Sealants-Adhesives/Adhesives/Wood-Glues/Polyurethane-Adhesive/Joiners-Mate-Adhesive-500ml"]Joiners Mate[/url] from Screw Fix, you gotta watch which one you use there's two types, they're both fine, the clear needs water to cure properly.
-
I've had my laptop back just shy of a week now (wound up rebuilding half of it myself!) so am busy catching up on 6 weeks worth of work. Anyway just for my fellow bass anoraks I used the Jack as a bass cab last weekend, it was not the best venue in the world but... The cab sounded fine, not as bright as I would have anticipated, but there was a smoothness to the top end that I found very pleasing. The cab goes quite low for what it is (a 2x10) certainly lower than an Omni10.5. I found it required more EQing to get a sound I was happy with than other cabs. My biggest concern is still the Piezo array and it's fragility, once it's all glued together an screwed to the wood it's certainly a lot stronger, but still feel like it needs some extra bracing somewhere - I even used solid copper to wire the piezos, definitely overkill for sound, but added a bit of strength. I'm surprised but just how loud these are as PA cabs, for most gigs I'm doing they will actually be overkill, which I hadn't realised at the start, but two of these, running at 4ohms each, is a 1k rig! I don't need that for 80 people at a wedding lol. Anyway because of his they can cope with just about anything I throw at them, which is nice. I'm pleased with the way these cabs have come out, but if I had my time again I would probably have built more Omni 10.5's as I prefer the sound (although they won't go as low) and they are a much simpler build. I'd still like to do an AB at some point, but I'm off on tour for a bit, and then have a few gigs, I think my next weekend off is the first weekend in Nov, when I will be lying in bed eating chips, but maybe towards the end of Nov I'll find some 'comparison time' I'm sorry to let you guys down on that, but just can't find a spare minute atm.
-
I'm loving the look of this bass [quote name='pantherairsoft' post='962633' date='Sep 20 2010, 07:46 PM']... It was an unforeseen addition, but required due to the radius of the fingerboard clipping into the side dots due to the massive width of the board...[/quote] I think it looks awesome and just assumed that it was a clever design feature you'd spec'd because in my head it really makes sense. If you'd never said anything we'd have all thought it deliberate
-
Refinishing my Yamaha RBX775 - help me decide !
gilmour replied to Machines's topic in Build Diaries
For the logo you can buy water transfer paper. Print logo onto it. Cut closely around the edge. Stick on, then apply loads of layers of clear to even out. If you want to retain the matt look then you can get matt spray on varnish -
I'd second that, for the most part stingray copies are pretty poor - but the Ibanez ATK is an excellent bass. It's been ages since I played one but IIRC it wasn't to dissimilar to a 'ray.
-
Awesome, I'm so jealous
-
[quote name='Phil Starr' post='942467' date='Sep 1 2010, 06:45 PM']Bad luck[/quote] Yes it's a real pain in the arse TBH. My insurance policy states old for new, most cases dealt with in 48 hours. It's now been nearly a month, and they've told me they're fixing the old laptop, but only the screen, not the case, damaged CD drive or corrupted hard drive. I'm at a bit of an impass with them at the moment.
-
[quote name='Phil Starr' post='941596' date='Sep 1 2010, 12:00 AM']Got that laptop fixed yet? Hope so, I can't be the only one looking forward to the next post.[/quote] Sadly no - the insurance company are really dragging their heels, it looks like the whole thing will have to be replaced as not only is the screen damaged but the CD drive is knackered and the hard drive corrupt So I only have intermittent internet access.
-
[quote name='bumnote' post='929538' date='Aug 19 2010, 11:03 AM']have you tried these with a bass?[/quote] Oooh, not yet. TBH the thought hadn't even occured to me mostly because when I'm testing I've been playing audio through them so I can hear all of the frequencies better. I don't doubt that they'd sound very good with bass. At some point I'll do an A-B against the Omni10s and Omni15 maybe some commercial cabs to if I ever have the time. Just so busy with gigs and stuff I never seem to find the time to finish my geekier pursuits
-
Just in case any of you were doubting me I did finish these in time, and we gigged them on Friday night. Here's the proof (very very bad mobile phone pic) The lack of updates is due to the cat killing my laptop (knocked it off a cupboard and shattered the screen) making updates very awkward at the moment. Here's what everything looks like.... At the gig one of the piezo arrays crapped out on me - but that was my bad wiring and is now fixed, and sounds much better. I'll do a full review and pics once the insurance company have gotten back to me (they said 5 days, 6 days ago!). But first impressions, [list] [*] These are heavy cabs, I didn't use neo drivers which would obviously make a difference, but even unloaded they weigh a lot. That said we're talking about 500W cabs and I'm not sure equivalent Mackie's would be much lighter. [*] To my ear there's significantly more bottom end than from two Omni 10.5s [*] They sound a little more 'boxy' and require a lot more EQing - but will reserve judgment on this as one of the cabs had faulty piezos. [*] The woodwork is much more involved than the Omni's - If you've not made cabs before these will be a push - for the easiest of Bill's builds I'd recommend an Omni15 (or Omni12) - the O10.5 is also an easy build, but no longer available to buy. The extra woodwork contributes to the weight. [*] They're bloody loud [*] Next gig I'll be happy to throw Vox, keys, trumpet and kick drum through these - without sweating too much about whether they can handle it (it is after all a 1K rig) [*] TBH I'm not sure if the improved bottom end has been worth all of the extra hassle of the build - I think this has taken me 3 times longer than If I was to build a pair of Omni10s - that said the improved bass is nice to have, and means I can chuck a kick drum through the PA, so I'll give it a few more gigs whilst I reserve judgment. [/list] I'll do some decent pics once I have a laptop that isn't a complete PITA to use (at the moment I'm having to run it through an old PC monitor and the resolution is all funny).
-
The Jazz Cafe's a great venue, always a really good sound and vibe, although last time I played there the supplied back line was some horrible ashdown 8X10 thing. Hope the gig goes well.
-
...cont So today I got off my arse and decided to finish these bad boys. I've been bothered by the holes in the piezo array, they're from the screw holes already in the piezo horn, when you trim the piezos and glue them together two 'half holes' join together to form a whole hole:D. My concern is that if I attach the array to the cab via these holes and tighten it too much then it could damage the array, so I decided to fill them. I used [url="http://http://www.milliput.com/"]Milliput[/url]to do this - those of you who've done any model making will probably know what it is. For the rest of you it's a two part epoxy putty that you need together into a turd like lump and then mould it into whatever you want. So I filled the wholes, and stuck the excess on the back for a little strengthening. This'll get a light sand and spray. Not sure what colour though - I do have some chrome paint Once this was done the weather started to warm up so I got outside and rattled through two cans of primer. I spent an age trying to attach the struts to hold the Piezo array, and they kept moving around, after a while I decided I needed something exactly the same size as the piezos to act as a little gluing Jig - then I decided not to bother and just used the Piezo's! Looks cool: Then made busy with the carpet and adhesive, I like this part of the build as it's the part I feel really confident in. An hour or so later it was getting dark so shoddy pics from inside: And for size comparison here's my Omni15TB: The pics still look a little spanky, but all the inside needs done yet, and I might try and paint the horn as the primer on it's own looks a little like blackboard paint, but all in all a good day. Tomorrow I make busy with the soldering Iron and hopefully will be making some noise
-
Last time I posted a proper update I'd just done the horn sides. Next up I had to install the top and sides - the only shock about this part of the process is that it was all relatively uneventful, and they went straight on! Filled the holes, then took my new router and rounded the edges, quick sand and hey presto woodwork done (more or less). Looked like this: Then the weather was bad and I was ill. cont...
-
Shame about the bridge, but great that Robbie's getting a new one in, and I'm not sure that 1mm will make that much difference. I think the slotted Rim bridge looks really smart, I love all the little touches in Robbies work, the bridge, headstock, way the logo sits in. It's really nice attention to detail that shows he cares about what he's doing.
-
Wow looks awesome. I'd love to know more about the woodwork processes involved.
-
Hmm, Interesting I've been using my omni 10.5's for PA and they have a straight 4 piezo melded array in each. I juat run straight into the cab no crossover or bi amping. They'd always been used for small acoustic type gigs up until recently when I had to use them for maybe 100 people, we had 4 vox, horns and keys going through the PA. It was the first time the drums have struggled to keep up. We'd originally taken the Omni 10.5s along for monitors and some yamaha 15" jobs for FOH, but at soundcheck realised that the Omnis sounded better so swapped. I was asked about EQ on another forum here's the results. [url="http://finnbass.com/showpost.php?p=110442&postcount=33"]http://finnbass.com/showpost.php?p=110442&postcount=33[/url] Dave Perry also did a lot of more scientific tests of Comp Driver Vs Piezo and the results were surprising. TBH if I were buying everything from scratch I'd go comp driver as it's now the cheaper option! But I had all the piezos lying about. Ho hum, we'll see how it goes I hope to be testing next week.
-
I actually find the covering the easiest bit of the build. But I do a lot of street art and stencilling (legally) so am very used to the adhesives and craft knives etc, the first time I covered a cab it already felt like a very familiar process. If you're going for a grille then the covering of the res of the cab is easy - just wrap a large piece all the way around, then a separate bit for the back - all the cuts and potentially uneven parts will be covered by either the grill, or the back plate.
-
FWIW I'd recommend individual cabs rather than a single 2x12. The build cost will be marginally higher, and of course you'll need an extra lead but the flexibility is worth it. I have two Omni 10.5's (the single driver precursor to the Jack10) and for rehearsal I use a single cab, then for gigs I can use two. They're a one had carry, although the jacks will be heavier given all of the extra wood in them, I doubt these will be a 'lightweight cab' but still a single driver one would be a single hand lift - much easier than a 2x15! That said if you use Neo drivers, and source some good quality light spruce (IIRC) ply then that should keep weight down. The reason Im going for 2x10's with this build is because they are for PA duty, so will have more strain on them more of the time, also if we have a small gig I already have the Omni's [quote name='discreet' post='912588' date='Aug 2 2010, 10:38 AM']Er... sorry Rob, I've gone OT a little... :blush: [/quote] Haha no worries I welcome it - distracts from m shoddy woodwork! and I'm glad to know I've inspired others - If I were you guys though I'd get making hay while the sunshines, or at least cutting up ply while it's not raining (unless your lucky enough to have a workshops/garage). As well as get on with the build I have really been working on my tan [quote name='bumnote' post='912612' date='Aug 2 2010, 11:03 AM']Gilmour are you going to paint them or cover them?[/quote] I'm not sure atm, I have some carpet left over from other builds, but carpeting these bad boys will be tricky, however the carpet does hide a lot of sins in the wood work I also have some fake alligator skin (bit like marshall cabs) that I could use,or I've even been toying with pimping them out and doing them in cream faux leather However all these options leave them open to kitten attack! My kitten is six months old and likes nothing better than scratching bass equipment. Because of the cat situation I may go with paint - but I'm gonna see how good my wood looks first.
-
[quote name='Scot Bass' post='912524' date='Aug 2 2010, 09:38 AM']Hi Gilmour, Looking good. I had the same problem with sh*"e plywood but my 2 J110s sound really good. The one thing that I forgot to do was breaking in the drivers. They loosened up with use and you might want to break them in so you can run the cabs at full pelt from the word go. Cheers, SB[/quote] Cheers dude - glad to know I'm not the only one who's ply provides a problem. This is my 3rd BFM build so I know about breaking in drivers, two of the four I've got are second hand so should be broken in already. Just need to get around to doing the others - I've only had them in the cupboard for 18 months!
-
After a week stressing about work, and chasing around bits of paper I decided to give myself the weekend off and do something I enjoy - get pissed off with bent ply and glue crap to my hands First of all, remember this.... My misaligned vent duct hole. I needed to fix this, first thing I tried was a circular hole cutter, do popped one out of ply It was a little large, but I thought I could sand it down - but it was too big and that pissed me off too much, so I sought out another solution. Whilst looking for inspiration in the shed I found an old curtain pole, it was a perfect fit I cut 12mm off of the end, and popped a screw in the middle to hold it by. Then PU'd it in place, and redrilled the hole in the correct place. Not perfect but at least it will work. then on to the real work. First job was all the baffle braces, 12 of the bloody things, they were quite fiddly. I was quite engrossed in the work and forgot to take pics. Then I aligned everything and glued the bottom on. Then I popped them on top of each other: Felt quite proud until I noticed I'd somehow used only 2 braces on one side of one of the cabs! Aaarrggghh. I've decided to leave it in the hope that it will be solid enough, If not I guess I'll go back and add two additional braces *sigh* One of the best things about the baffle braces is that they make a very hand work station Note that the cuppa takes first place. Glues up the horn sides next. These had been pre cut. These were a right PITA, largely because of that sh*tty ply I've been using so nothing quite lines up. Note the spirt level/straight edge in the pic - In an effort to make the ply straighter a method I've adopted is to Clamp my straight edge to it whilst gluing In the hope that when the glue goes off it will hold the pieces straight - It's worked to a point, but not perfectly. I doubt very much these cabs will be 'as advertised' given the warped ply and my cock fingered attempts at cutting and gluing, in fact it'll be a miracle if they don't wobble all over the place! Oddly though (given the performance of my O10.5s at the last gig) I'm still confident that they'll be better than anything else I could have afforded. Then the driver spacer went on, and the phase plug extension, I imagine it works in much the same way as throat filler in the O12s (and DRs ?). FWIW it would have been easier to do this much earlier in the build when I was making the phase baffle. Then stripped excess pu, filled any holes where screws had come out and a light sand (full sand at the end of the build) and I have something that's closely resembling a pair of Jack 210s Tops to go on next, then the sides and it's onto installing the electrics. I also will probably get a top hat to install before doing this. Putting the top on will be interesting as it will reveal how out of line eveything is curtesy of my ply, bad technique, impatience, general woodworking ignorance... I can't wait I have a deadline to have these finished by Monday 9 August, as we have a gig on 13 August with no budget for PA, and I'd like to give them a run at practice first. That is all.
-
Some simple syncopation suggestions?
gilmour replied to Annoying Twit's topic in Theory and Technique
Whilst reading and working from charts is important, and will really help develop and understand ideas, I'm not sure anything replaces listening to music. That slightly off topic comment is relevant, but Im guessing if you're aware of it then you're already making steps to remedy it. Last week at Womad I got to watch Tony Allen and some of that AfroBeat syncopation is incredible - he hardly ever hits the bass drum on the one! But it still gooves like hell...notice how the emphasis is all on the '&' so much so it almost becomes the 1. Anyway that's my small though on syncopation - listen to something I saw just last week -
Robbie's really going for it on this one, at this rate you'll be playing it this summer It's good to see given the length of some of the other build threads on here.
-
Why did I just read this thread I really want a Wal, but just can't justify the money when the instruments I have are serving me fine. But then, maybe just maybe if I concentrate really hard it is good value for money....
-
[quote name='Finbar' post='904341' date='Jul 24 2010, 09:41 PM']Probably would have used the offcuts the other way up, so they have more area in contact with the assembly? I'm watching this with interest though Might need to build myself some BFM stuff soon D:[/quote] I had initially done that, but then changed my mind. I felt that that flat part of the bracing will add more strength that way around (effectively creating box tube) as opposed to the other way around. The 'airfix' glue melts the plastic a little and then when is sets forms a pretty tough bond so that should be ok. But time will tell, part of me still feels they should have been the other way.
-
I'm interested to see how this comes out as a bolt on - I love playing through necks, but always feel that bolt on's sound better. I don't think I've gigged my through neck in the last 5 years, probably more.