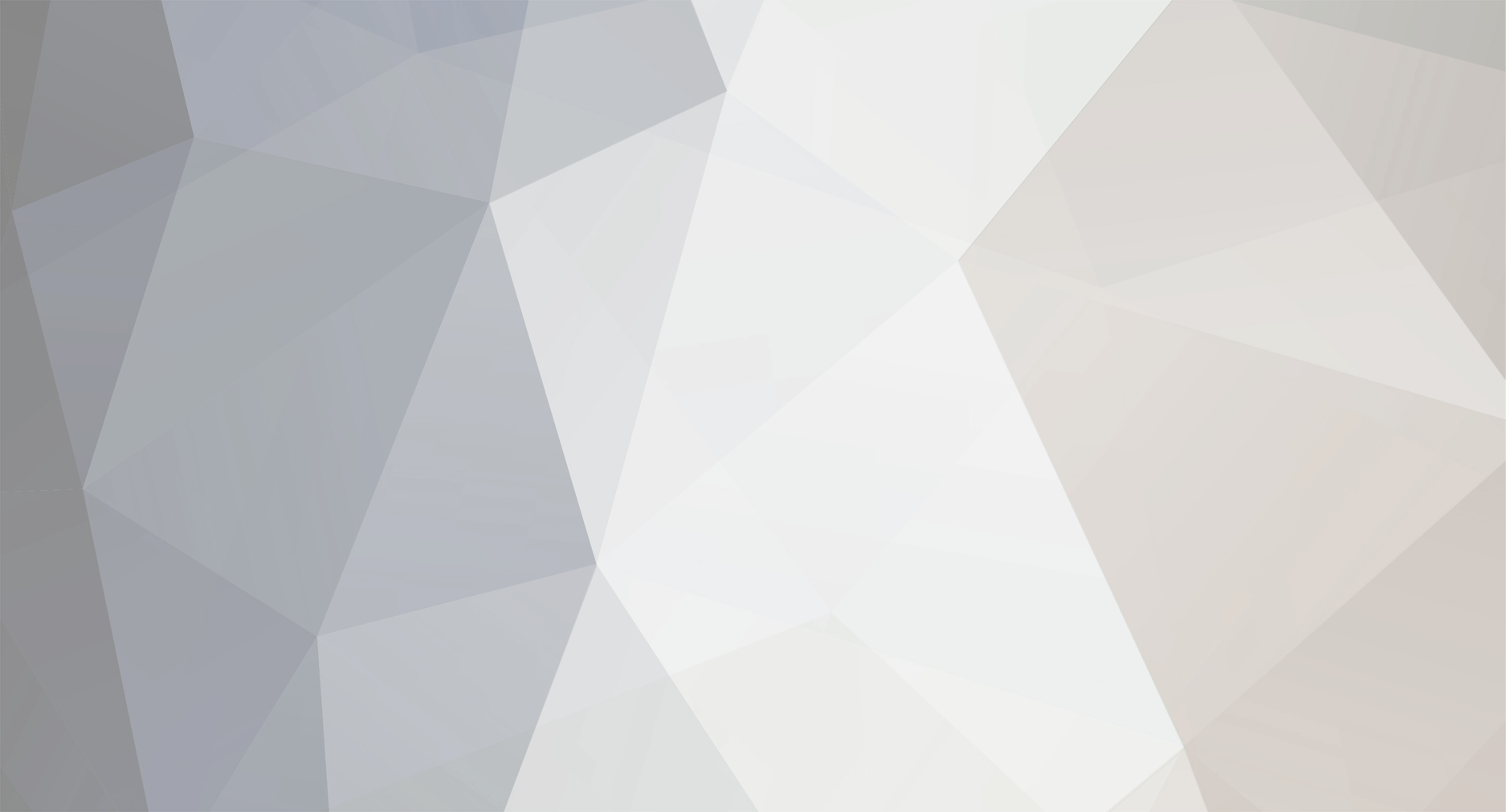
BOD2
Member-
Posts
1,112 -
Joined
-
Last visited
Content Type
Profiles
Forums
Events
Shop
Articles
Everything posted by BOD2
-
Strap button screws constantly coming loose!
BOD2 replied to EskimoBassist's topic in Accessories and Misc
[quote name='neepheid' post='516276' date='Jun 17 2009, 11:34 AM']Cocktail sticks are made of stronger wood than matches and are better for this particular fix.[/quote] +1 to cocktail sticks and white wood glue (not superglue). Remove the screw and clear out any loose bits inside the screw hole. Dip a cocktail stick into the wood glue and push it as far as it will go into the screw hole. Trim the protruding end off flush. Do the same with another cocktail stick. Repeat this until you cant push any more cocktail sticks into the hole and it's all nice and tight. Trim the ends, wipe off any woodglue with a damp cloth and leave overnight to dry. Once it's all set nicely you might find you need to drill a new pilot hole for the strap button screw. Don't use too large a drill for this and everything should be all tight. -
YES ! Your speakers contribute a great deal to the sound you hear and the DI feed bypasses those completely. Your DI sound is then EQ'd on the mixing desk and played through PA speakers which will affect it again.
-
+1 to what High score said above. The only things I would add (and only AFTER all of the above have been tried) is to check the EQ settings on the singers mic channel. If there's a "rumble filter" switch on the channel (cuts out frequencies below 70Hz usually) then switch this on. You could also try cutting the low EQ on the mic channel a bit - not much, sometimes a little is all that's need to keep things in check. But the main thing is to try and limit or control what is going into the mic.
-
Rewiring a 5 knob bass from active to passive?
BOD2 replied to allighatt0r's topic in Repairs and Technical
[quote name='allighatt0r' post='513521' date='Jun 14 2009, 07:37 PM']Where is the best place to pick up some pots from? I guess I'll need some caps if I'm having tone knobs too right? I think i like the idea of having two volumes and two tones at the moment. I had a look in the cavity the other day and didn't really know where to start. I think i will take the pots out with most of the wires attached rather than try to disassemble it one wire at a time in the cavity... Thanks for the help so far! As you can tell I'm quite a novice at this![/quote] Pots and other electronics [url="http://www.axesrus.com/axeknobs.htm#CTS"]http://www.axesrus.com/axeknobs.htm#CTS[/url] Wiring diagrams [url="http://www.seymourduncan.com/support/wiring-diagrams/"]http://www.seymourduncan.com/support/wiring-diagrams/[/url] The actual configuration you want will not be listed as you don't get "standard" basses with 4 controls (i.e. basses that Seymour Duncan sell pickups for) so you'll need to combine the information from different diagrams. Here's a good starting point - [url="http://www.seymourduncan.com/support/wiring-diagrams/schematics.php?schematic=std_p_j_bass"]http://www.seymourduncan.com/support/wirin...ic=std_p_j_bass[/url] -
Rewiring a 5 knob bass from active to passive?
BOD2 replied to allighatt0r's topic in Repairs and Technical
The sensible passive options are probably ( P1 = pickup 1, P2 - pickup 2) P1 Volume, P2 Volume, P1 Tone, P2 Tone, dummy P1 Volume, P2 Volume, Master Tone, dummy, dummy Master Volume, Blend, Master Tone, dummy, dummy Once you decide what you want someone can probably post a diagram. Passive pickups usually use 250K or 500K pots. Active circuits often use 25K or 50K pots so you may need to change these. -
[quote name='phil_the_bassist' post='510366' date='Jun 10 2009, 04:44 PM'].... mayhaps an email to EBMM customer service is req'd![/quote] Just make sure you kiss bottom in your email and don't suggest for a moment that this might be.... God forbid ... a fault !!
-
Thanks for the prompt replies. I'll make an allowance for a possible 20% on import duty then and see how the prices fare based on that. Cheers
-
Has anyone ordered parts from - [url="http://www.guitarpartsresource.com/"]http://www.guitarpartsresource.com/[/url] What are the shipping charges like and do we have to pay import duties on goods received ? Thanks
-
[quote name='bigjohn' post='509989' date='Jun 10 2009, 10:51 AM']I'll have a go at that. I haven't got any XLR cables, but I'm going to a rehearsal tonight where there will be some. The two problems I can see do this though are... 1) I'd need an XLR > 2 XLRs for both channels. 2) It leaves no balanced out for the desk.[/quote] I realised that as well ! But this is initially just a test to see how it works on one channel using that method of input. If it works well then there are ways you can resolve the other issues.
-
I'd be inclined to try connecting from the balanced out on the Ampeg and not the main outs. The level switch sets the signal level at this connector to be microphone level (low) or line level (higher). I would expect it to work at the line level setting but you could experiment with both settings of the switch.
-
Nothing here that takes your fancy ? [url="http://www.axesrus.com/axehardware.htm#BASS"]http://www.axesrus.com/axehardware.htm#BASS[/url]
-
[quote name='obbm' post='509190' date='Jun 9 2009, 04:21 PM']Simply put you shouldn't use an instrument cable with anything more than say a 50-watt amp. I think I got that right. Anyone care to comment?[/quote] That sounds about right - I wasn't sure of the actual figures. The trouble is, you'll always get people who say "I've used instrument leads for my speakers for years and never had any problems" and from these figures you can see that if it's a good quality instrument lead and the amplifier is less than 50 Watts then they might get away with it. Use a 300 Watt bass amp with the same lead, however, and you'll have problems ! The other issue here is that some cheaper instrument leads are very poorly made and the solder connections to the jack plug can be pretty poor as well. So you might get away with using a high quality instrument lead but if you pick up a poor quality one then it's a different story. Much better to make it a rule never to use instrument cables for speakers and avoid any potential (and very costly problems). Incidentally - it's always a good idea to clearly MARK speaker cables (e.g. with brightly coloured or something highly visible) so that you can instantly identify them on a dark stage.
-
Phil Lynott could hold a tune and sing pretty well at the same time....
-
That information is VERY bad, possibily m,ore so for bass guitar where the amplifiers tend to be higher powered than 6-string amplifiers. The problem is that an instrument cable is designed to handle the very low signal levels (voltages) that are generated by, for example, a guitar pickup. There are two conductors - a central conductor that carries the signal and a braided "screen" that shields the signal from interference. The central signal conductor is very thin - perhaps 8 strands of very thin copper wire. A speaker cable, on the other hand, has to handle the output power of an amplifier which might be anything from 30 Watts to 1000 Watts RMS. 1000 Watts (1 kilo Watt) is the the same power as the average single bar electric fire. Now imagine connecting an electric fire to the mains with an instrument cable and you'll get some idea of the potential problem. A good speaker cable has much heavier gauge wire than an instrument cable. The conductors inside will look more like a mains cable than an instrument cable in order to handle the higher power. In addition to this the connections to the jack plug will also be heavier duty to cope with the higher load. Yes, it is possible to use an instrument cable as a speaker cable and you may get away with if the power passing between amplifier and speaker is low. But if this power is high, then the instrument cable will blow like a fuse, leaving the amplifier outputs potentially open or short circuited, which can cause very expensive damage to the power section of the amplifier. For this reason, never use an instrument cable as a speaker cable - not even in an emergency. The shop gave very bad advice.
-
[quote name='dlloyd' post='508927' date='Jun 9 2009, 12:02 PM']Is this bass different from this one? [url="http://www.dv247.com/invt/48164/"]http://www.dv247.com/invt/48164/[/url][/quote] Yes, I believe it's from this range.... [url="http://www.fender.co.uk/products/search.php?partno=0194762752"]http://www.fender.co.uk/products/search.ph...rtno=0194762752[/url] [url="http://www.dv247.com/invt/41119/"]http://www.dv247.com/invt/41119/[/url]
-
If it's a Bass POD XT Live then there should be a "Phones" output for your headphones and an "Aux Input" for attaching a CD or MP3 player. [url="http://line6.com/basspodxtlive/ins_outs.html"]http://line6.com/basspodxtlive/ins_outs.html[/url]
-
Well the mounting holes are in a completely different location to a normal "Fender" bridge so you would have to position the bridge correctly and drill new holes. Not a major problem in itself, but you'd have to be comfortable with that. Can't really get an idea of the quality from that one photo, though.
-
Is this an active bass ? If so, try changing the battery. If not, or if a battery change doesn't work, it's worth trying to squirt a contact cleaner into the inside of the noisy pot. A squirt of "Super Servisol" or equivalent, into the workings of the pot will often help.
-
From the Ampeg manual - [url="http://www.ampeg.com/pdf/SVT-2PRO.PDF"]http://www.ampeg.com/pdf/SVT-2PRO.PDF[/url] "16. STANDBY/POWER/FAULT INDICATOR LED: This is a multi functional LED. In Standby mode, it glows red. In the On mode (when the high voltage comes on) it glows green. If it does not turn green in the On mode, there is no high voltage present and the unit needs servicing. If the amp detects a fault in the power tube circuit, the high voltage is turned off and the LED flashes between red and green. This usually indicates a bad power tube. The amp will remain in this condition until the unit is turned off." If you've got a flashing red/green LED then it does suggest a problem with the power valves.
-
[quote name='Kongo' post='504841' date='Jun 3 2009, 04:57 PM']I can NEVER seem to get the solder on the pots to melt! I have always cut mine because of this but would really like to solder them out next time. ANy particular soldering iron I could use? It's also worth asking, what's the best solder as well. [/quote] Soldering pots - this is how to do it [url="http://www.youtube.com/watch?v=swfQi7GtK78&feature=player_embedded"]http://www.youtube.com/watch?v=swfQi7GtK78...player_embedded[/url] He uses a 25 Watt soldering iron. Any lower and you won't get enough heat into te pot shell. You can use higher (e.g. 40 Watt) but then you have to be quick so as not to "roast" anything ! Use a "cored" solder (that has "rosin" cored through it to help it flow) and follow that tip on "tinning" the wires before you join them - it makes a big difference.
-
[quote name='Metalmoore' post='504574' date='Jun 3 2009, 12:05 PM']Yeah this is what i really wanted to know, the body doesnt have anything to link between the control cavity and where the bridge will be... Any tutorials to do it?[/quote] Mark where the bridge will be going. You know this area will be covered so it doesn't matter too much if you make a mess here ! You'll need a long drill bit to drill at a very shallow angle from under the bridge position and into the control cavity. Getting this hole started might be tricky as the drill will tend to slip because of the shallow angle. It's probably best to use a bradawl and get a good, deep starting point first. This will help get the angle right too. Just make sure the angle is shallow enough that you come out in the control cavity.
-
This is how you place the bridge. Seems complicated but follow it step by step and it will makes sense. First you need to know the scale length of the neck. For a Fender Jazz or Precision bass the scale length is 34 inches. If it's something other than that then you'll need to establish that first. If the body is finished, protect the finish of the bass against scratches before you start. You'll need to draw lines in the body so stick masking tape over those areas. 1. Insert the neck into the neck pocket and hold it in place with 2 or more screws. You can clamp it if you prefer butdon't damage the frets. 2. Use a long straight edge to draw two lines from each side of the neck to the back edge of the body. Run the straight edge along the edge of the neck to ensure the lines are parallel to the neck. 3. Accurately measure 3 inches from the last fret, along each line, and mark this point on the lines. 4. Draw a line across the body between these two marks. 5. Measure the distance along one line from the last fret to a point about an inch from the back edge of the body. Mark this on the line then mark the same distance from the last fret on the other line. 6. Draw a line across the body between these two marks. 7. Measure the centre points of the two lines drawn at step 4 and 6 above. Draw a new line the length of the body through these two centre points. If you have measured everything accurately so far, then this last line represents the centreline where the neck passes through the body. This line is one of you datum points. Check visually that this looks to be in the correct position. 8. Measure back from the nut 34 inches. Draw a line at right angles to your centreline at this 34 inch point and make it wider than the bridge width. This new line is the "scale reference line". 9. Pickup the bridge and move one of the saddles to its furthest forward point, then move it back 1/16 inch. Measure the distance from the string break point on this saddle to the front edge of the bridge. Measure this distance from the "scale reference line" (step 8) towards the neck. Draw a line at right angles to your centre line at this point - this line represents the front edge of the bridge. It will be closer to the neck than the "scale reference line" 10. Measure and mark the centre of the bridge. Place the front edge of the bridge on the line drawn at step 9 with the centre point of the bridge on the centre line. Mark both sides of the bridge (these marks should be parallel to the centre line). You now have a front edge and two sides marked for the bridge. Check the positioning of the bridge visually. Does it look right ? If not check your measurements and start again, if necessary. Note that the strings will always intonate longer than the 34 inch scale, not less. Thicker strings will intonate farther than thinner strings. Because of this, only the G string will be relatively close to 34 inches. Apologies for the "imperial" measurments but the scale length is 34 inches. This sounds easier than 863.6 mm and I didn't want to mix inches and mms in the same text !
-
The RCF ART310A ("A" for active - note there is a cheaper passive version) is a 350 Watt speaker with a 10 inch drive. This is more equivalent to the Mackie SRM350 (which is also available now in a lighter "V2" version). Both units are very high quality, lighter and cheaper than the SRM450. They might be worth considering. [url="http://www.mackie.com/products/srm350v2/"]http://www.mackie.com/products/srm350v2/[/url] [url="http://www.dolphinmusic.co.uk/product/8711-rcf-art-310-actives-pair-.html"]http://www.dolphinmusic.co.uk/product/8711...ives-pair-.html[/url]
-
You also need to run a ground wire from a ground connection (i.e. a pot shell) in the control cavity and trap it between the underside of the bridge and the body. This will ground the strings and prevent all sorts of noises when you touch the strings. There should be a hole drilled from the bridge location to the control cavity to pass this wire through.
-
Moving the bridge towards the neck will have the same effect as moving the pickup towards the bridge - the pickups should sound a little brighter. Beyond that it's difficult to say - and how much change you would actually notice (especially given the other changes - new neck, new bridge - which are fairly major) is anyone's guess. Judging by the variations you see in pickup placement, there doesn't seem to be an "optimum" pickup position at all.