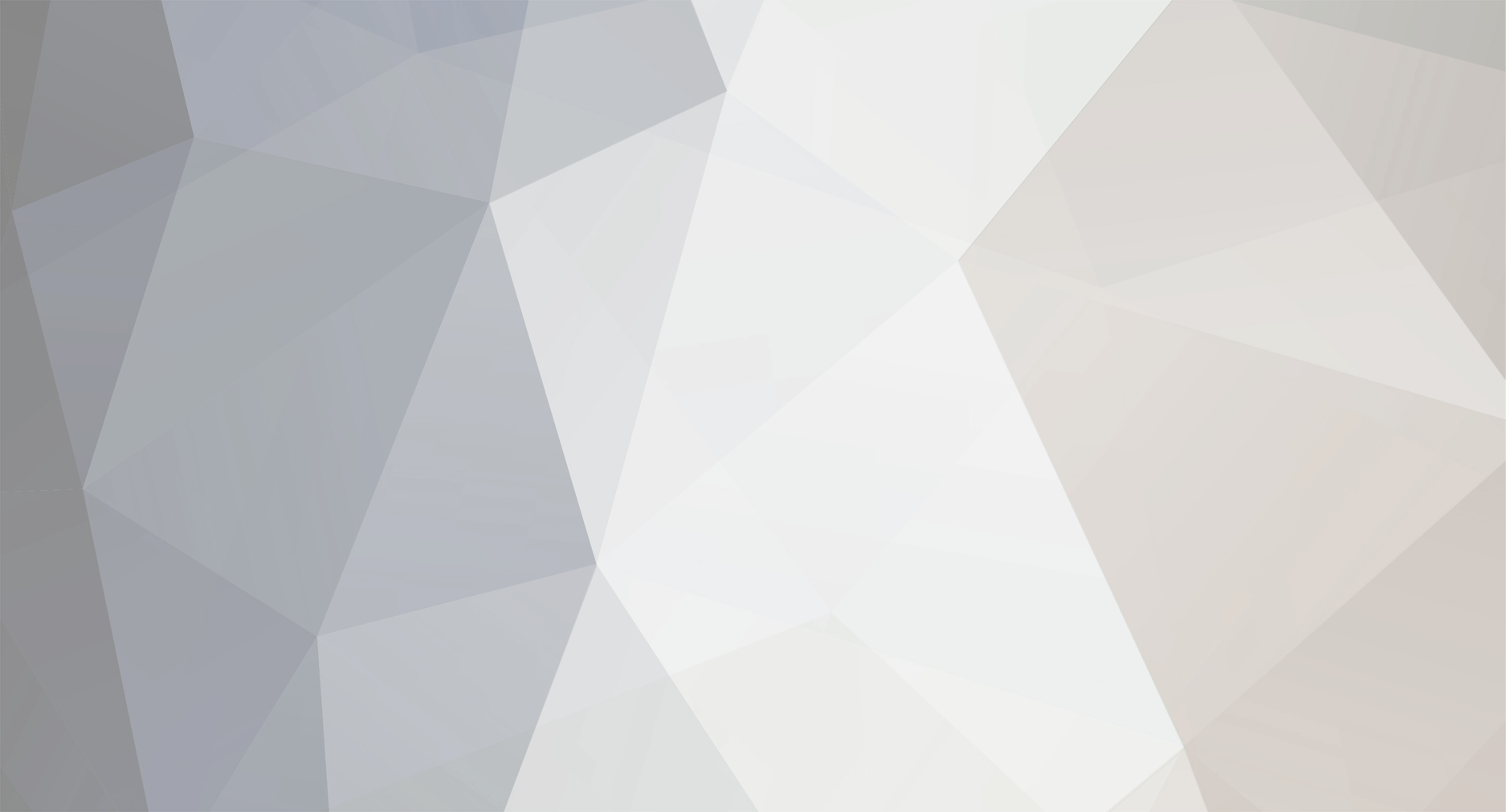
BOD2
Member-
Posts
1,112 -
Joined
-
Last visited
Content Type
Profiles
Forums
Events
Shop
Articles
Everything posted by BOD2
-
Some info here [url="http://basschat.co.uk/index.php?showtopic=193"]http://basschat.co.uk/index.php?showtopic=193[/url] I would tend to agree with you basic point - there are lots of other bridges that are equal to, if not better than this one.
-
The "scientific approach" would be to eliminate standing waves or resonant frequencies. Standing waves are caused when the certain frequencies of sound reflect off surrounding surfaces in phase with the original sound thus reinforcing it and making that frequency louder. Moving the cabinet on the stage may prevent this from happening - try moving it a foot or so backwards or forwards to see if it makes any difference. Resonant frequencies have the same effect - the room resonates on certain notes (or harmonics of a note) and makes that notes sound louder. As suggest above a parametric notch filter, set to cut the problem frequency, will help here. If you set the width of the parametric filter to be very narrow it will only cut around the problem frequency and hopefully won't affect the sound too much. So what frequency would you cut ? Use a chart like this [url="http://www.phys.unsw.edu.au/jw/notes.html"]http://www.phys.unsw.edu.au/jw/notes.html[/url] Figure out which note causes the problem, identify the frequency, and try cutting around that frequency. It's the same as the suggestions above bit takes a little of the guesswork out of ut.
-
[quote name='Huge Hands' post='498554' date='May 27 2009, 10:31 AM']I had another think about this on the way to work - I figure that as the nut is fixed, then angling the neck is in effect doing the same thing? I guess to drop the action across the board you'd have to grind out the nut?[/quote] Maybe, but think of it this way.... If you were to put a 1 inch thick block under the bridge and a 1 inch thick full size "shim" in the neck pocket so that both bridge and neck were raised by exactly the same amount.... would the action change at all ? I don't think it would (it would make cleaning the body under the strings easier, though) I think it's more of a cosmetic thing - no one wants to "see" shims in the neck pocket so using a partial shim keeps it all hidden. (Good luck with Mini-Hands !)
-
Good question Huge Hands. I've thought hard about this and, to be honest, I can't see much difference in the result you would get from either technique (i.e. shimming the whole pocket or shimming just the back of the pocket). Given that the problem, in this example, had been cause by fitting a BadAss II which is slightly higher than the original bridge, then it makes sense that raising the neck by the same amount would also fix the problem. However, if you ANGLE the neck with a partial shim I think you need less thickness in the shim that you would with a full length shim to achieve the same result - because the angling has an effect as will as the shim thickness. Less shim thickness in the neck pocket is probably a good thing. Also, cosmetically, you cannot see a shim at the back of the neck pocket - it's completely hidden by the neck join. A full length shim would be visible and would not be very attractive. So these are the only two reasons I can see - less shim thickness and you cannot see the shim. However, I'm no luthier so there may be some other reason that I am missing, but full length shims are uncommon.
-
[quote name='skankdelvar' post='498065' date='May 26 2009, 03:45 PM'].... A weber beam-blocker also helps with dispersal, I'm told.[/quote] Yes, but aren't the DiLithium Crystals you need to power that quite hard to get a hold off....? [attachment=25995:Scotty.jpg]
-
15 Watts of valve power through a good cabinet (1 x 12" or a 2 x 12") will be plenty loud ! Plus you can crank it up and get the power valves to start distorting - that is the key to the valve guitar sound, power amp distortion. The only potential drawback to (most of) these lower power valve amps is that they tend to be single channel. So if your guitarist is used to having 2 or more different sounding channels at the flick of a footswitch then he may have to rethink his ideas a bit. It might be time to learn what the knob marked "Volume" on his guitar actually does....
-
Some links here [url="http://www.guitarthings.co.uk/cge-pot-center-detent-blend-250k-1178-p.asp"]http://www.guitarthings.co.uk/cge-pot-cent...250k-1178-p.asp[/url] [url="http://www.allparts.uk.com/electronics/250k-pots-c-277_1_81_83.html"]http://www.allparts.uk.com/electronics/250...77_1_81_83.html[/url] [url="http://www.wdmusic.co.uk/product/POT_CENTER_DETENT_BLEND_250K_WD250PAN"]http://www.wdmusic.co.uk/product/POT_CENTE...D_250K_WD250PAN[/url] I think most of these look like "mini" pots - but there's nothing wrong with that and they work perfectly well but just take up a little less space.
-
[quote name='stinson' post='496319' date='May 23 2009, 09:13 PM']That Sir, was superb. Well done. That JV brings a tear to my eye, reminds me of one I let go years ago [/quote] Thanks stinson. It's not actually a JV. It's an "SQ" serial number which, as far as I can determine, means it came out just after the JV series but still some time in the mid eighties (I bought it secondhand and pretty beat up around 1986). It certainly seems to share the same neck but I think the body and fittings were a little more budget and not as "historically accurate" as the JV-series.
-
If the neck screws are loose then you need to plug the screw holes in the neck with something. Cocktail sticks and wood glue will do this job perfectly well and allow the neck screws to grip again. A shim place at the back of the neck pocket (as described above) will change the neck to body angle by effectively pushing the headstock backwards. This has the effect of lowering the action. A shim placed at the front of the neck pocket (furthest away from the body) will effectively push the headstock forward and should slightly raise the action. Thanks for reading this - I hope someone finds this useful.
-
Step 14. Adjust the action. You should find that the action has been lowered by putting the neck shim in place - the strings will probably rattle on the frets. You can now raise the bridge saddles to get the action you want. Job done.
-
Step 13. Finish Off. Turn the bass over and remove the capo/elastic bands. Retune the strings to pitch. Once they're up to pitch check the tightness of the neck screws again.
-
Step 12. Tighten the screws. As with removal do NOT fully tighten each screw individually. Go around the screws and give each a single turn, then mve on to the next one. Tighten all the screws evenly in this way. Make sure they are all good and tight, but do not use excessive force - just tighten with a normal screwdriver.
-
Step 11. Refit the screws. Leave the screwdriver aside for now. Drop each screw into the hole then finger tighten them - you should feel each screw grip the wood in the neck. Go round each screw and get them all finger tight.
-
Step 10. You now need to turn the bass over onto its front, keeping the neck in the pocket. It doesn't matter if the neck moves a little here but try to minimise movement and keep the back edge of the neck against the body so as the shim doesn't move.
-
Step 9. Replace the neck. With the shim in the back of the neck pocket, carefully replace the neck in the socket. Put the neck straight down and don't wiggle it from side to side.
-
Step 8. Cut the shim. Cut inside the line to ensure the shim will fit. To allow you to lower the action the shim should be fitted at the back end (closer to the bridge) of the neck pocket. Check the fit is ok with no wrinkled or bent edges - it should be perfectly flat in the neck pocket.
-
Step 7. Make the new shim. There's a big debate over what material the shim should be made of - wood veneer, sandpaper, cardboard. But remember - it needs to be thin. In most cases, cardboard the thickness of an ordinary business card will be enough to allow you to lower the action. Sandpaper to grip the neck ? Well it's held tight by 4 screws so it's not going to move, so what will the sandpaper do (apart from being thicker than a business card). Wood veneer ? Yes, if you have some thin enough then this is a perfect material. Wedge shaped tapered shim ? Well if you can make a tapared wedge with the thickest part as thin as a business card then that is perfect too. For simplicity I have used an ordinary cardboard business card. Place the neck over the cardboard and use it as a template to draw around and mark the shape of the shim.
-
Step 6. Check the neck pocket and the underside of the neck for any signs of a previous shim. If there is a previous shim you can either remove it completely or replace it with a new one.
-
Step 5. Now - nothing is holding the neck on. Lift the bass carefully. If the neck slides out then that's ok, but if it doesn't then it's just a tight fit in the neck pocket. Turn the bass over onto it's back. If the neck is still in place, carefully ease it out straight up - don't wiggle it from side to side, you may damage the neck pocket. Move the neck, with the strings still attached, to the side.
-
Step 4. Use a well-fitting screwdriver to avoid burring the screws. Unscrew each screw a little at a time so that they are all loosened evenly. DON'T unsrew one screw completely then move to the next - this will put pressure on the neck. Undo each one a turn or so, then go back to the first and do another turn, and so on until they all come out. Remove the screws and the neck plate and put them aside.
-
Step 3. Turn the bass over onto it's front. You'll see the neck plate and (usually) 4 neck screws. You'll need to remove all 4 screws.
-
Step 2. Now put your capo on at the first fret. This will hold the loose strings in place when you remove the neck. If you don't have a capo use an elastic band - it's just to stop the strings falling out of the nut. If you don't have an elastic band then follow your postie around for a day or so - he'll be dropping those pinks ones all over the place so you can use a few of these. You can put a second capo/elastic band halfway down the neck if you wish, but it's not essential.
-
Step 1. Ok. You've got some space and a covered surface to work on. First step is to loosen (but don't remove) the strings. Loosen them off until there is no tension on the neck and they're all flappy.
-
How Long Will It Take ? Once you know what you are doing it can be done in abouit 10 minutes. If it's the first time then allow up to an hour. Can I Undo it if it Doesn't Work ? Yes. The neck shim can be removed easily and quickly, returning the guitar to excatly the condition before you started.