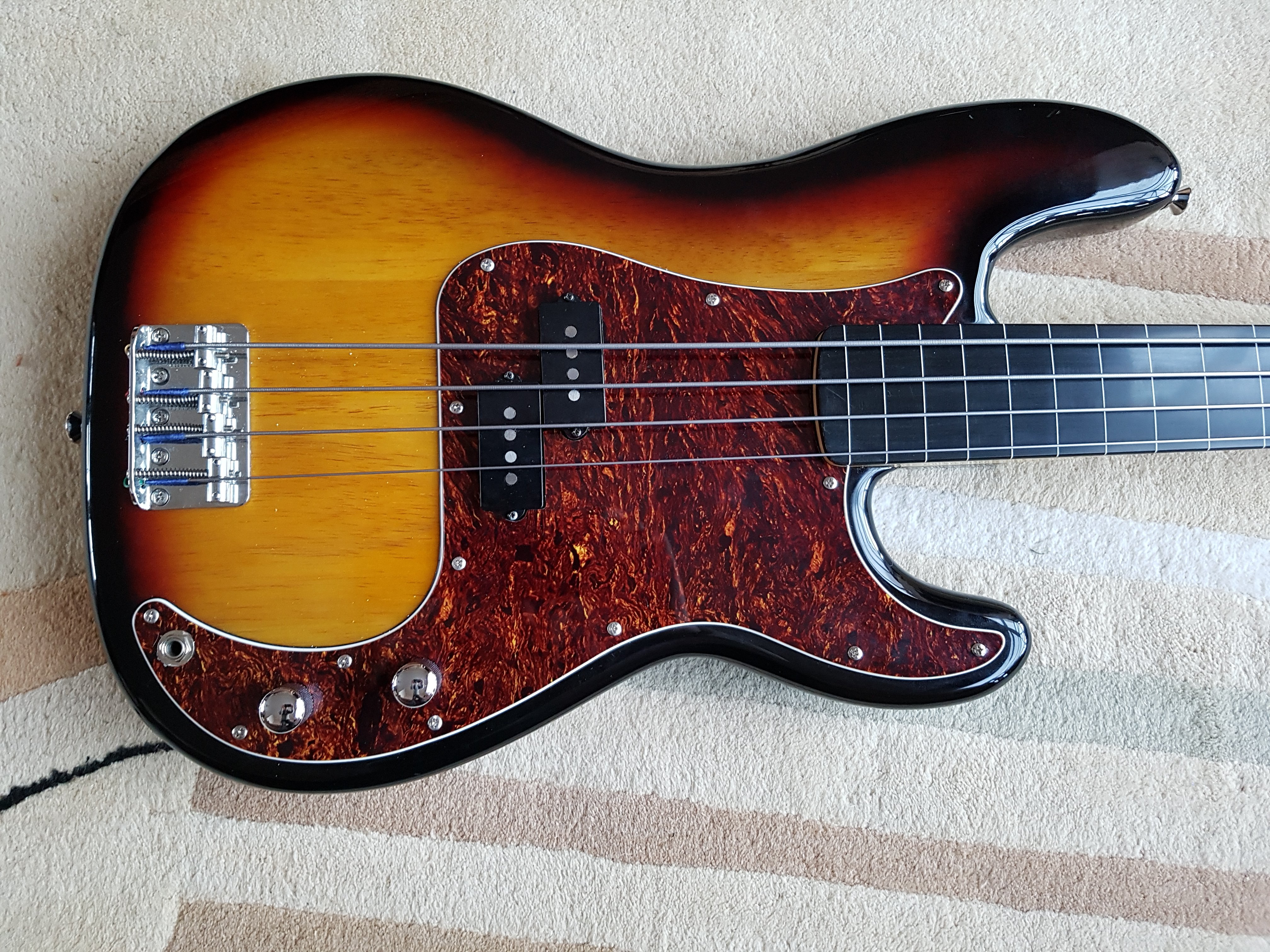
Grangur
Member-
Posts
5,281 -
Joined
-
Last visited
Content Type
Profiles
Forums
Events
Shop
Articles
Everything posted by Grangur
-
We know Tanglewood have been making instruments for Overwater and Overwater have spent a lot of time with them getting the quality better. Maybe they're now looking to get some rewards for this themselves? In other sections of Chinese industry the workers are beginning to demand higher pay, so the costs will inevitably move up too. Times, they are a-changin'.
-
Squier Precision MIC re-birth * FINISHED!*
Grangur replied to Jonnyboy Rotten's topic in Build Diaries
[quote name='JazzRay' timestamp='1388255413' post='2320074'] What you want for the screw is a set of screw extractors, they aren't expensive either. They look like a cone shaped screw with a reverse thread. You drill the screw you want to remove then screw the right sized extractor into it, as you turn it anti clockwise it gets a bite of what's left of the screw and screws it out [/quote] This works if you're talking about the bolts on an engine, or similar, but the screws on the bridge of a bass are far too small for this. As this is a re-worked bass and new holes won't be a killer, I'd be inclined to move the bridge. Take a look at the bridge as it is with the intonation set up and ask yourself if the saddles could be moved back away from the neck by 7mm. If the answer is "yes", then remove the bridge and re-drill the holes 5-7mm in front of the current ones. Otherwise you could move the bridge back towards the foot of the bass. If you've never fitted a bridge before: You need to make sure, when you fit the bridge, you get the side-ways position right. The back-forwards isn't critical, but the side to side is. First get some masking tape and put this on the bass round the sides of the existing bridge as a guide for the position. It may also be useful to remove the pups and put tape from the neck to the bridge on each side of the neck to each side of the bridge. You can then get a long straight-edge and mark the line of the sides of the neck as they project towards the foot of the bass. This will give you the line for the outer edge, so we can make sure the strings won't be pushed so far to one-side as to go over when you're playing. Another note to the wise - fit the bridge using 1 screw at first, then check the line up and drill 1-2 more and keep checking. Filling holes - matchsticks are softwood. They're ok if you're screwing a wardrobe together. Fill the ones on the bass with cocktail sticks. It's a harder wood and will be better for long-term use - secure them in place with PVA glue. Good luck. -
[quote name='BassBus' timestamp='1388268353' post='2320316'] This is why these build diaries are so useful. Doing a great job. [/quote] Pleased to think this may have helped. Quick update: I've picked out the hole some more and stuck the sticks in there. I've been scraping at the check and it's really insignificant. More filling tomorrow to make it up some more...
-
I've been thinking about the amount of grey in the wood. I was wondering if this is truely paint or is it the nature of the wood? Looking at wishbass.com I see he uses Poplar wood for some basses. So I looked this up: [indent] [url="http://www.wood-database.com/wood-articles/wood-color-appearance/"][b]Color/Appearance:[/b][/url] Heartwood is light cream to yellowish brown, with occasional streaks of gray or green. Sapwood is pale yellow to white, not always clearly demarcated from the heartwood. Can also be seen in mineral stained colors ranging from dark purple to red, green, or yellow, sometimes referred to as [url="http://www.wood-database.com/lumber-identification/hardwoods/rainbow-poplar/"]Rainbow Poplar[/url]. Colors tend to darken upon exposure to light.[/indent][indent] [b][url="http://www.wood-database.com/wood-articles/wood-grain-texture/"]Grain/Texture:[/url] [/b]Poplar typically has a straight, uniform grain, with a medium texture. Low natural luster.[/indent][indent] [url="http://www.wood-database.com/wood-articles/hardwood-anatomy/"][b]Endgrain:[/b][/url] Diffuse-porous; small pores in no specific arrangement; solitary and radial multiples of 2-3; tyloses occasionally present; growth rings distinct due to marginal parenchyma and noded rays; rays not visible without lens; parenchyma banded (marginal).[/indent][indent] [b][url="http://www.wood-database.com/wood-articles/wood-durability/"]Rot Resistance:[/url] [/b]Heartwood is rated as being moderately durable to non-durable; susceptible to insect attack.[/indent] This would also explain the yellow colour in the wood on the back, and the worm holes in the timber that are found in about 3-4 places. BTW, there was some discussion about playability of these and getting above the 12th fret. I've found this is very playable beyond the 21st fret, never mind the 12th
-
Under the black, tar-like exterior I found there were a few flaws. As you can see in the pic here, there are 2 screw holes either side of the pup. I recon someone put a cover over the pup. Also, to the right of the pup hole here, you can see a line below the purpleheart. This is almost like a woodworm trail. There are a few of these. If it was woodworm, then I think it's dead, but it leaves a mark all the same. In one or 2 other places there have been other gaps and a few checks in the timber. (Checks - this is splitting due to movement in the wood as it's seasoned and dries out) This shows poor wood selection, but I don't think it'll continue to move much now or there would have been splits in the black paint. To deal with this I glued the sharp ends of cocktail sticks into the screw-holes. Knocked the sticks down into the holes and painted the tops with PVA glue. To get a perfect colour match to fill the holes I used saw dust from the body wood. To get this I got a blade from a Stanley knife and scraped this across the body and it creates fine sawdust; perfect for pushing into the hole. I repeated this and you can see the result in the above picture. You can still see a slight blemish, but it's better than a hole. I've also stared working on the gap you can see to the bottom left of the shot. It's a gap between the woods. I'm filling the worst with cocktail sticks and shaved down sticks, then filling with PVA and sawdust in the same way as above. On bigger splits its a bit of a drag repeating it until it's full, but I'm not paying by the hour, so it's ok. When I bought the bass the big one on the bottom was filled with wax wood filler, but I'm a pedantic sod and I don't recon it's hard enough. So I dug it out and I'm filling it my way. I'm aiming to do the wood check on the right in the same way. No sticks on that one, but glue and sawdust. Incidentally; the check looks far worse in the pic than it really is. It still has some black cr@p in there making it look bad.
-
I'm about to order the push-pull pot for the tone and series/parallel. The volume is 500K. I usually use 250k, but I believe 500K pots should be used with twin-coil pups. Can anyone advise on if I should stick with a 500K, or a 250K for the tone? [quote name='Billy Apple' timestamp='1387908588' post='2317150'] I've played ACG's with a zero radius (as in flat) fret-board. it's probably the way I'll go when I do mine, very nice feel to play [/quote] Thanks for that Billy. Today I've also been sanding the fingerboard - flat. I'm told the 20" block went in the post today. But I'll give "flat" a go. Actually I recon the fb on my LTD ESP is pretty flat too. I like it.
-
Evening guys! Today I've been sanding and filling, gaps, holes etc, more sanding, scraping and sanding. It's beginning to get there. I've also ordered a jack socket cover. I've read guys saying how after standing on a lead they've managed to rip the jack socket from the wooden front, so I'm going to move the socket to the edge. I'll then put a tone control on the front in the jack hole, with a push-pull for the series/parallel. [size=4][quote name='Sambrook' timestamp='1388237048' post='2319768'][/size] My Wishbass sounds better each time I pick it up. It's ace. [/quote] Sounds great. I can't wait to get at this one. I'm also beginning to think about strings. I've got a set of Elixir Nonoweb roundwounds sitting about. I might use these, or I might order in a set of XL Chromes. I've got a 5-string set here and I love the feel. I think I'll get a 4 set on order. Today I've also reshaped the headstock a bit. Nothing drastic, but taken the sharp edges off.
-
In fairness the wording is a bit "cart before the horse" and could be mis-read to give the idea that it's a genuine Fender. That said, is it really like the Fenders of the 60s?
-
Interesting. What controls did you incorporate? Series/parallel? What wood did you use for the body? I'd imagine it's the main contributor of the weight?
-
Hey, Many thanks for the info!!
-
To Lowdown: Many thanks for the comments, it's good to hear your insight, but please can you attach as "pdf" format for those who don't have an iphone? To Ambient: Thanks for posting. You certainly have Mrs G's adoration. We both listened a few times and it's sounding good - will be watching to hear the final version. I'll be sending a link to this to my Bro-in-Law - pro Cellist and teacher.
-
[quote name='Roland Rock' timestamp='1388186894' post='2319375'] Great stuff everyone. Thanks Dad for the spoiler tutorial. I'm going to test it now... [spoiler]Dad got my vote this time round. It really captured the quirky humour of the picture and was a really well composed piece. Well done all. Skol was a close second[/spoiler] [/quote] Agreed, for me it was Dad who completely captured the feel of the pachyderm in bed, which was the task set.
-
If you want to be successful, do you have to dress up?
Grangur replied to xilddx's topic in General Discussion
In one way he's right. If you're selling any product the punters need to have confidence that they know what they're getting. If One Direction went on stage displaying tattoos, greasy hair and somehow managed to put on a heavy metal act, they could be finished. Their "success" could be over. If The Rolling Stones went on in "Boy Band" gear, they'd capture the front page of every paper in the country. [size=4]David Jones proves Mr Dunnery wrong though, or maybe he proves him right too in a perverse way. In the 70s he invented a character and played that character on every album. Yet he re-invented that character on every album. On the other hand maybe his "thing" was that "David Bowie" changed all the time?[/size] -
The other day I stripped the back and today I stripped the front of the body and most of the neck. In the past I've used a blowlamp, but this time I used paint stripper. As you can see it left the paint well soaked into the wood, but we're beginning to see the real bass under all the black brush-marked paint. After a lot of more sanding and scraping we now have this: I also worked on the neck. I have ordered a sanding block for the neck, but today I used a long, sharp blade and scraped the fingerboard. Doing this removed most of the saw-blade marks and some of the hump in the radius of the neck. I wanted to remove the hump as it's uneven. The FB is quite smooth now and we can see it's mahogany. I can't say I've heard of too many necks being made of mahogany, but it is a hardwood. I don't know how it ranks against rosewood or purple-heart. My guess is it's softer. Well, it's softer in texture/touch anyway and that's what matters. After all balsa wood is technically speaking a hardwood, but I don't' recon anyone here's going to be using it for a fingerboard any time soon. There still appears to be a lot of black in-grained in the wood. Does anyone here know of a good way to deal with that, other than the obvious: 1 - Live with it. 2 - Keep sanding. I've just put a straight-edge on the neck and I can see it's bowing back slightly. Presumably this will change when the strings are back in place. For those keen to see other images, there are more [url="http://s1175.photobucket.com/user/Grangur/library/BC-pics/Wishbass?sort=3&page=1"]here[/url]
-
The entries this month have set the bar high again this month. It's always good to listen to all the submissions. Well done guys!
-
You can only use oil on an oiled finish wood. If its lacquered, the oil won't soak in. It'll just lay there on the surface.
-
I use boiled on both basses and furniture.
-
Thanks Graham, I've ordered the radius block. I was wondering on the radius to use. There's quite a range to chose from. I believe Fender use sizes from 7.5" - 17". Warwick use from 20" - 47". I've found I think I like a flatter radius fingerboard, so I've gone for 20". It will then also be the same as my SS1. Today I'm aiming to strip some back. Went an bought a new gas canister for the blow-lamp. I may also use Nitromorse on some parts. I've stripped the bass of all electrics and metal parts and we're down to the basic body/neck. With any luck, today I'll get some time to get stripping.
-
Thanks all for your interest. BigRedX has me thinking.... It'd be good to not have to change the FB, of course. So just now I've been playing round the 9th - 12th frets and the mwaaa is seriously random. I like mwaa, but it needs to be consistent imho. Also, I like the action on my LTD ESP 5 fretless. (Discreet, do you need pics of this too? ) The action on the 2 compares like this: LTD:- Nut; 0.38mm, 12th fret: 1.78mm WB:- Nut; 0.96mm, 12th fret: 2.3mm The height at the bridge is about 15mm on both. So looking at this I'd like to lower the nut on the Wishbass. If I lower the nut to 0.4mm then, in theory the height at the 12th will be about 1.78mm. Which is looking good so far, but I think I need to investigate: 1 - What does the FB natural wood look like? 2 - Can I lower the pup if needed? More tomorrow.....
-
[quote name='Billy Apple' timestamp='1387736834' post='2315077'] Subscribed. I've got a couple of Lobes waiting to be finished. Interesting to see what is under the black crap [/quote] it'd be great to see what your Lobes look like. Today I've opened the electrocs cover and seen the MM style pup has 2 coils connected in series. I'm probably going to fit a push pull switch to make series/parallel possible. Tomorrow we get out the blow lamp. Even if I only strip some of the back to get a preview.
-
[quote name='discreet' timestamp='1387737145' post='2315085'] So you're expected to finish the bass yourself..? If you took that idea to it's logical conclusion, you could just sell the customer a log for the price of a bass, get them to make it themselves and supply their own hardware... I don't think it looks too bad. I like the mininal approach, one pickup, one volume control, no frets. Depends how much more finishing you're going to do I suppose... [/quote] Having shelled out for this on Ebay and getting it and finding the fb is as uneven as it is I'm inclined to agree with you. If I sand it flat, or pay a luthier, the action will then be higher than it is now. So I'm thinking of getting someone to maxhine off the FB. So I need to ask myself, how much an I open to spending on this? Family commitments have stopped me from working on this today, but I'm already wondering what I should do if after stripping the body I find it looks boring as hell like a pine board. Wishbasses I've seen have been interesting. But there's always a first time.
-
[quote name='tommorichards' timestamp='1387735082' post='2315036'] they dont have trussrods, do they? Thats the only real thing putting me off getting one as id want it fretted. Otherwise, i reckon thats a beautiful bass! [/quote] You're right, they don't have a truss rod. They/he used to make a fretted version. As I see it the only disadvantage is that you can't change the amount of relief on the neck. But isn't this the same for fretted or fretless? In both cases you want just the right degree of relief. As I understand it, its this lack of adjustment that makes him use Purple heart wood in the neck because it holds the neck solid. Older Wishbasses also had thicker necks for this same reason.
-
-
Hey there. I've listened to the Youtube vids and like the tone and the rustic, drift-wood looks of the Wishbass. OK, so these aren't to everyone's taste. I know that, but I like the rustic appeal. I do think the overall shape of it's curves are spoilt by the packing-crate look of the headstock, but at least it's not yet another Fender rip off. I love the grain and character of real wood and they've got good tone. IMHO I've seen few ugly ones. So when I saw one going on ebay I went for it, dropping in a bid at the last minute and she was mine. And now I've become the new owner of this ugly bass. It's otherwise known as Wishbass serial number 1314 and it's a "Lobe shaped" instrument. This is the worst looking Wishbass I've ever seen and I'm wanting to find the diamond in the rough, if there's one hidden in this beast. Actually it's possibly the ugliest bass I've ever seen. Edit - More pics: [url="http://s1175.photobucket.com/user/Grangur/library/BC-pics/Wishbass?sort=3&page=1"]click here[/url] I don't know much about the woods except it's mainly light coloured, with Purple heart wood in the neck. And it's hand painted, mostly in black. With a fingerboard that looks like it's been painted in Ronsons red fence paint. The fingerboard is not only a revolting red/orange, but it's not flat and saw marks can be seen. Wishbass don't finish their basses, they make great basses, at a great price, but expect their loving owners to finish them and this one's been "done" badly. As you can see in the pics, even the curves of the body are lumpy. The pick up is a Kent Armstrong, and I LOVE the tone. First job - strip this babe back to the wood and see what I've got. I'm also looking out for a luthier who can make me a nice purple-heart fingerboard. Oh, and btw. This is my first real build. The one other before it was simply a Squier strip, re-spray and pimped with all the trimmings... here goes!
-
[quote name='artisan' timestamp='1387371970' post='2311163'] this i think is spot on & absolutley true in my case too,my brother is 5 years older than me & even though i am 46 i still get this exact treatment. [/quote] You're not alone. I get that from my bro and I'm 54