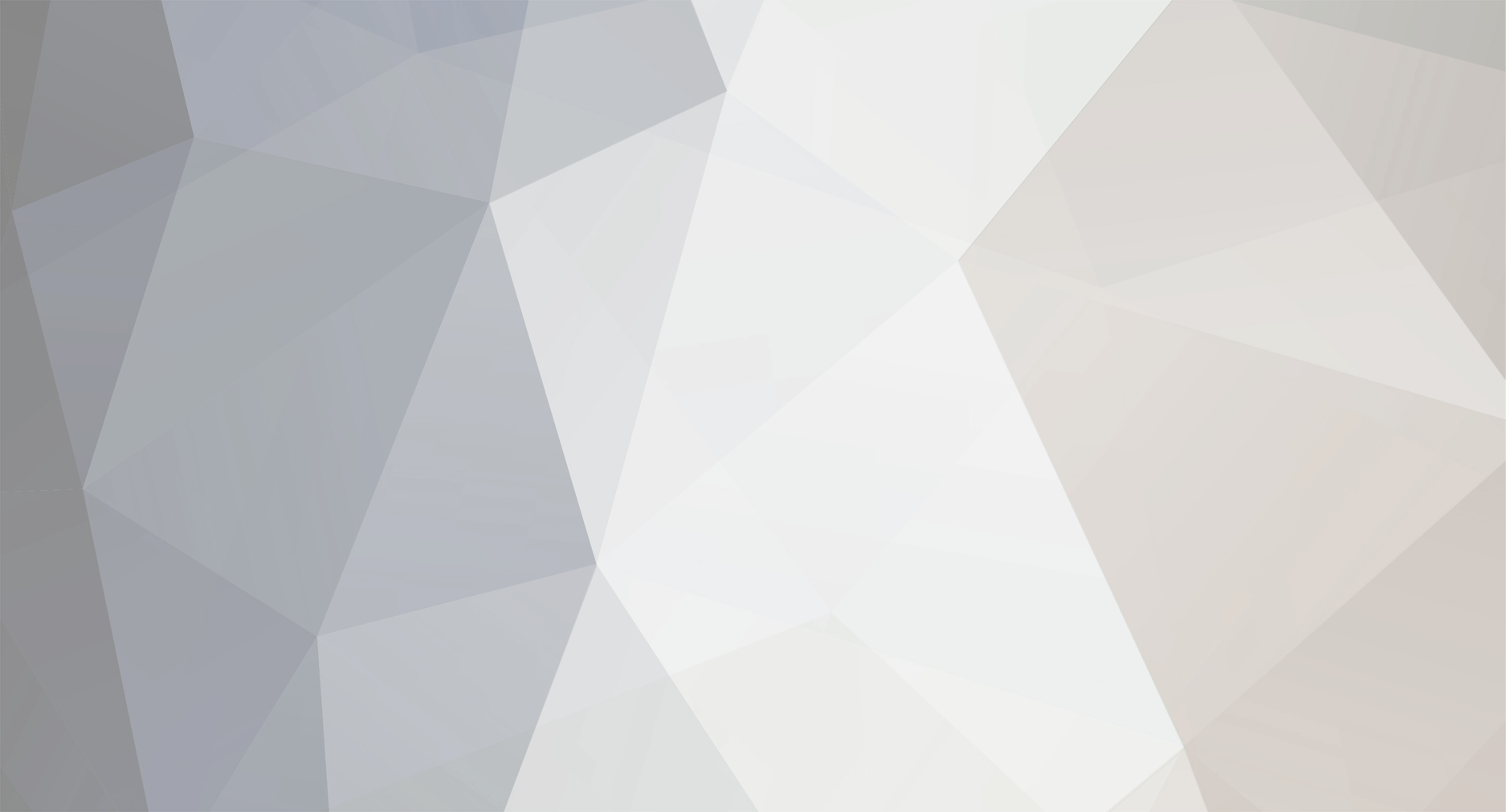
rmorris
Member-
Posts
1,300 -
Joined
-
Last visited
Content Type
Profiles
Forums
Events
Shop
Articles
Everything posted by rmorris
-
Yes. Or just take out the tone control completely and increase the pot value as suggested. Or to be more radical bypass the volume altogether and make sure the input of your amp or DI etc is high ie 1M0 or above.
-
and a lot more time ??? filing f.ay, 0.105" string I think they are more of a guitar thing tbh.
-
Good Point 🙂
-
Doesn't that only apply if tightening the truss rod ? If loosening then string tension would seem to be helping ? Willing to take advice on this.
-
eg https://cpc.farnell.com/duratool/d03048/multimeter-digital/dp/IN07222
-
What did you dislike about the original bridge ? Sound / Tone ? Or aesthetics / ergonomics ?
-
Yes - but isn't the 'slight bend' the key thing here to give better access with a typical headstock end truss rod adjustment ?
-
Right. I'm going to ask the question that never gets asked? We play (relatively large) bass guitars - often through even larger/heavier amp/speaker/combo rigs - so why the obsession with the size of relatively tiny effects pedals ??? Yeah - I know stage sizes etc but really ...
-
yeah - the circuits load each other resulting in loss of level (and a likely change in frequency response).The loss will be equal in each output only if the output impedances are identical.
-
What was the 4 channel line mixer ? Seems something wrong if that didn't work properly. Bear in mind that a ABY pedal will simply join the outputs of the two chains together. Whether that works properly depends on the output impedances of your fx chains and the input circuit you're going into.
-
Copper tape &/or Conductive paint - sources and suggestions
rmorris replied to Woodwind's topic in Repairs and Technical
I see. I don't think I've ever used Aluminium tape, Probably due to the reasons you outline - adhesive / soldering. But I've used 'loads' of aluminium foil in testing scenarios to good effect. On an anecdotal level from my EMC test lab mate - it's worth getting the 'Turkey Foil' mainly sold around Christmas time that is a bit thicker than normal foil. After that the law of (exponentially) diminishing returns means it's not worth going further 🙂 -
Copper tape &/or Conductive paint - sources and suggestions
rmorris replied to Woodwind's topic in Repairs and Technical
yeah - I was really just expanding on the point. (You may have guessed that this sort of thing is part of my 'dayjob' so may as well share here). But, as you say, essentially the shield/screen needs to be at a fixed potential (voltage) with respect to the circuitry. This is best achieved through a 'solid' connection to the circuit 'ground' or 0V. Cheers. -
Copper tape &/or Conductive paint - sources and suggestions
rmorris replied to Woodwind's topic in Repairs and Technical
Basically - in a hand waving sort of way - a shield reflects most of the rfi and a small amount is absorbed depending on the Surface Transfer Impedance (STI) of the shield material, the frequency of the interference and the thickness of the shield. A small finite amount 'gets through' the shield. Basically the better a material is as an electrical conductor the better it is at screening eg Copper is better than Aluminium. The important thing about implementing a shield is that it is held at a fixed potential with respect to the electronics. This almost always means a good solid connection to 'ground' or 0V. This may, or may not, be connected to the actual 'Earth'. (The 'Earth' connection is essentially for electrical safety - think about a car or aeroplane where there is no galvanic connection to earth but screening considerations still apply) Bear in mind that different considerations apply where the interference has a large magnetic field component (as opposed to electrical field) component. In practice this means mains hum caused by transformers etc. -
Help needed setting the action at the nut
rmorris replied to markdavid's topic in Repairs and Technical
Might be the relative output levels I guess but also the wax or resin potting on the J might be suspect ? Hopefully some pickup experts might chime in... -
Copper tape &/or Conductive paint - sources and suggestions
rmorris replied to Woodwind's topic in Repairs and Technical
All things being equal Copper is a more effective shielding material. -
The pickups are (Alan) Entwistle. Not Entwhistle. I'm not trying to be pedantic but it reminds me that there was an 'amusing' debate on TalkBass about whether (John) Entwhistle had really in some way 'authorised' these pickups. I think someone put them right in the end but...you know...Americans 🙃
-
No. Copper is non ferrous ie not ferric. Metals with Ferric properties contain Iron (Fe in periodic table) so basically irons and steels. Aluminium is also non ferrous.
-
Sounds like that cable may not be proper "High Impedance Instrument Cable". It should have a semiconducting layer between the core and the screen to attenuate noise due to cable movement.
-
Beyond contamination of the windings a metal string is liable to loss of tension over time.
-
It sounds like it's survived. wooden floors are generally fairly 'bouncy' in contrast to concrete etc.
-
Power BLOCKS/BRICKS, Voltage & Milliamps FGS
rmorris replied to The GroovyPlucker's topic in Effects
Yes - it's misleading. 'Isolated' has a specific and generally accepted meaning wrt electronics and power sources. They should be described as having individual short circuit protection. -
Or you could use foam instead. Might be easier to handle ?
-
Both 'TR' and 'Q' have been commonly used for transistor component references. Similarly an integrated circuit may commonly be 'U' or 'IC' etc...