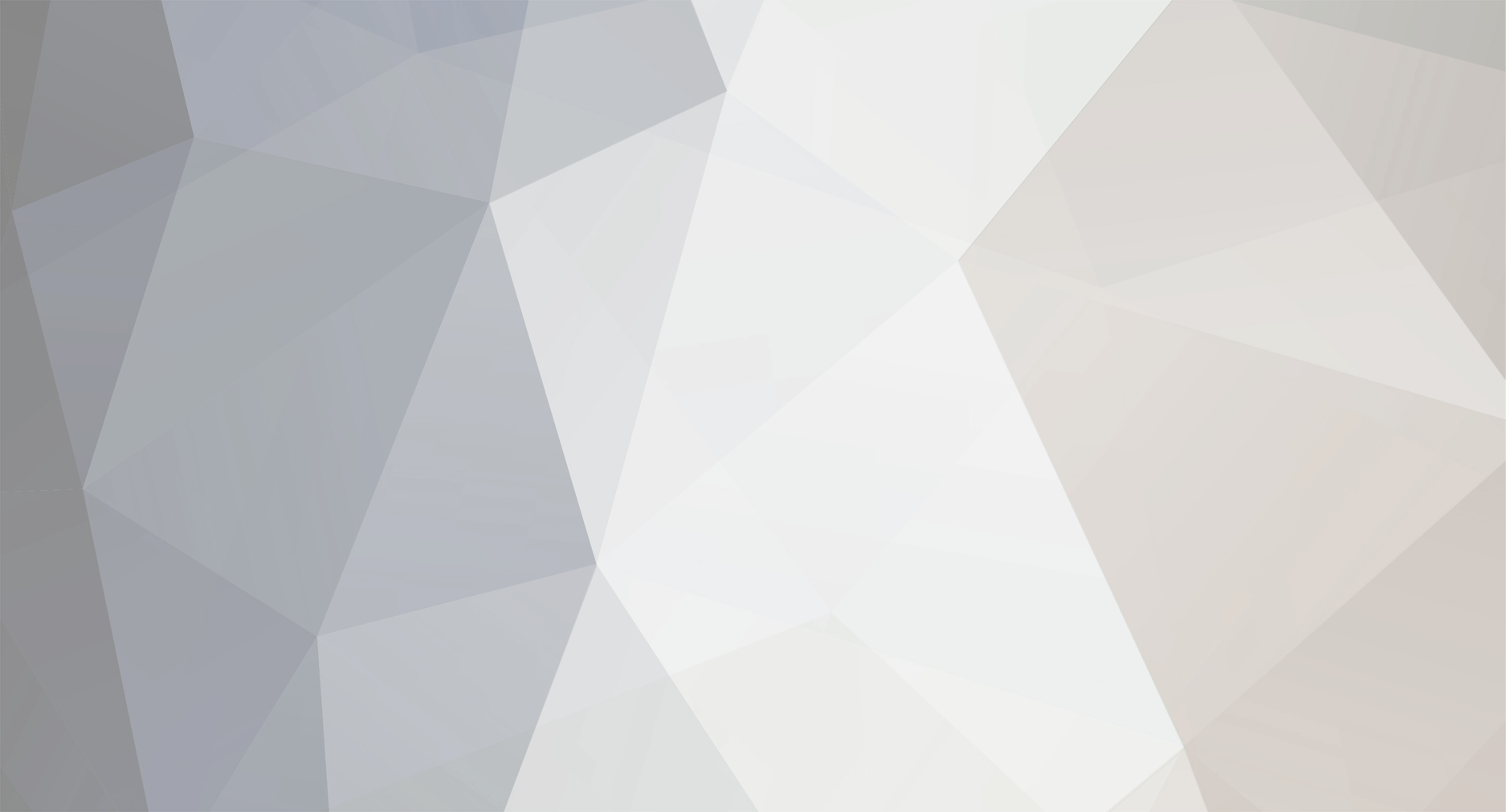
agedhorse
Member-
Posts
996 -
Joined
-
Last visited
Content Type
Profiles
Forums
Events
Shop
Articles
Everything posted by agedhorse
-
If the amp is quiet with nothing plugged into the input, this means that the interference signal is entering from the bass or wiring. Now, when it's quiet using humbuckers but noisy using single coil (or split coil), this confirms that the noise is environmental and is entering the bass through the pickups. In humbucking mode, this cancels common mode environmental noise, which is working as it should. The same thing applies to the Nordstrand pickups, which allow you to sweep between single coil and hum bucking, and the noise nulls out when fully humbucking. Also, the noise profile is mostly 50 (or 60Hz) with very little second or third harmonics which also indicates that the noise is radiated from the power source and is unrelated to the amp's power supply. I bet the noise changes with your position in the room, or just turning it around a bit? Things that cause this include an amp with a noisy line frequency (lead sled) transformer that has a loose radiated electro-magentic field, large motors, some lighting, and some old school fans. There is a slight possibility that the noise is due to circulating currents in your power ground/earthing system, but unlikely since the amp would usually have some noise with nothing plugged into it.
-
Except that this is not true for well designed amps, class D or otherwise.
-
IEM rigs work great for some players, doesn’t work at all for many players. It depends very much on the particular application and situation. I don’t like it where a player denigrates another player’s choices based on only their particular choice, even if that choice may not reflect the other player’s needs or situation.
-
Tube power stage vs Class-D (effective power)
agedhorse replied to Paddy Morris's topic in Amps and Cabs
Other ware some models that used the same module operated at 8 ohms with lower rated power. Much of the emulation/simulation involves significant dynamics processing which limits the power into their respective rated loads. Otherwise those poor speakers would fail at an unacceptable rate. It’s a combination of both approaches depending on the specific product. Active power management while maintaining musicality is a game changer. I remember when such adaptive algorithms (including dynamic HPF’s, adaptive multi-band compressors/limiters, dynamic crossover points, HF lift circuits (came into existence in the pro audio world in products like Meyer, Renkus Heinz, Appogee, etc), they are now ubiquitous in today’s pro audio products at all levels. That’s one reason why reliability has dramatically improved. -
Tube power stage vs Class-D (effective power)
agedhorse replied to Paddy Morris's topic in Amps and Cabs
A quality power amp designed for 2 ohm operation should have no problem driving 2 ohm loads with no reliability issues, I have been doing so for >30 years. -
Tube power stage vs Class-D (effective power)
agedhorse replied to Paddy Morris's topic in Amps and Cabs
Often this is done intentionally, to give the impression that the amp “gets louder” more quickly as the control is turned up. This comes at the penalty of usability and control. It’s more common in lower quality, lower priced amps, but not always. -
Tube power stage vs Class-D (effective power)
agedhorse replied to Paddy Morris's topic in Amps and Cabs
There are a couple of reasons for using a 200 watt module… the first being that the amp is not operated at 4 ohms, therefore the rated power is only 100 watts. The second reason is for duty cycle management combined with the modeling algorithms, specifically relaxing the compression and limiting attack time versus how hard the amp is driven. There’s a ton of stuff going on under the hood. -
Tube power stage vs Class-D (effective power)
agedhorse replied to Paddy Morris's topic in Amps and Cabs
I've heard the name but never run into him, or any of his amps. I was indeed fortunate to have grown up in the right era, learned from the right folks and took every opportunity that I possibly could. For example, my supervising engineer while I was working for one of Fender's companies was Bill Hughes (lead engineer behind the SVT and some of Fender's big bass amps like the Fender/Sunn 1200S, Bassman 300 Pro, along with the PassPort PA series). He was pretty old school, talking with him was always a learning experience. In the pro audio side of things it was even more interesting because many of the concepts that we take for granted today were just being discovered and I got to experience it first hand. It was smaller companies and more personal interactions, much more enjoyable (IMO) than with today's very large business entities. -
Tube power stage vs Class-D (effective power)
agedhorse replied to Paddy Morris's topic in Amps and Cabs
Mike’s still here, doing mostly legacy repairs and touring support of legacy products. There are lots of things being done with solid state that can address most of the feel issues, your example of the MOSValve amps is one approach that was originally designed by BK Butler, we acquired the brand after it fell on very hard times (we built cabinets for TubeWorks for a while, before they shut down) and developed some new products, but the brand reputation was just too damaged to overcome the legacy issues. The work on solid state power amps for guitar continues on under the radar, Pat Quilter’s efforts are probably some of the most successful but then there’s also the Tonemaster series that’s gaining ground and popularity. It’s a very complicated balancing exercise to develop new technology that convincingly emulates both the tone/voicing and the feel of the older technology. Of course you already know this with your products, specially the SansAmp. -
If he's a truly qualified service tech, he should know this already,and have the tools to figure it out.
-
Tube power stage vs Class-D (effective power)
agedhorse replied to Paddy Morris's topic in Amps and Cabs
Yes, I currently work for Mesa Boogie, I'm the principle engineer behind all of the Subway bass products but also handle various aspects of the guitar amp world as well. I work(ed) hand in hand with Randy, John, Jim and Doug, spent a lot of time with them, in addition to all the other folks. While I'm the "new guy", I've been designing Mesa for about 12 years, and prior to that I designed for Genz Benz/Fender for about 30 years, plus all my pro audio designs, so I've been around the block more than a few times. I've spent quite a bit of time quantifying guitar amp distortion characteristics (not surprising given our experience in the hard rock and metal world) and in general the desired distortion tones (especially lead) run between say 25% and 40%, but there are a whole family of tones that go beyond this too. Of course the amp is ~1/2 the instrument, the texture and tone of overdrive and distortion are a big part of the creative elements of "guitar tone", specifically how it sits in a mix. Randy's a very cleaver, creative guy, he quickly recognized what players were desiring and through a lot of work (including trial and error since there weren't many if any to copy from) developed the driven tones through cascading gain stages, then voicing these gain stages to be more and more useful for particular genres. If you were to study his products and their progression, you would see that he was constantly learning and evolving his designs as the music styles and player demand evolved. John has taken over the guitar amp design work now that Randy retired. At 80 years old, he had earned the opportunity for some new adventures that didn't involve day to day obligations. I have designed several solid state guitar amps as well, mostly with tube preamps, and I haven't run into any limitations of solid state power amps, especially when they were designed with guitar amplification in mind. Some of these turned into commercial products, some are just stepping stones to other implementations of technology. Hope this helps explain my perspective. -
Tube power stage vs Class-D (effective power)
agedhorse replied to Paddy Morris's topic in Amps and Cabs
That’s not really the reason why lower powered guitar amps sound louder. The biggest three factors are that the guitar signal resides in the most sensitive portion of our hearing, guitar speakers are very efficient in that range, and that when distortion is used (common for guitar), the THD is often 30-40% which often is part of the desired tone and this increases average power delivered to the speaker. -
Tube power stage vs Class-D (effective power)
agedhorse replied to Paddy Morris's topic in Amps and Cabs
This really only applies to guitar amp designs. We never made a production amp with tube rectifiers, not did our competitors in their higher powered amps... Ampeg SVT and V4, Fender PS-300/400, Bassman 300, Bassman 135, Trace V series, for example. It turns out that what sounds good on guitar (and maybe on lower powered bass) doesn't sound all that great on higher powered designs. -
Tube power stage vs Class-D (effective power)
agedhorse replied to Paddy Morris's topic in Amps and Cabs
Both this PLUS the dynamic (burst) power factor and voicing into the perception of loudness. There are switchmode power supplies that are far more stout than line frequency supplies, and have very high duty cycles as well. Like everything in life, there are good and bad examples of both line frequency and switchmode power supplies. -
Tube power stage vs Class-D (effective power)
agedhorse replied to Paddy Morris's topic in Amps and Cabs
This is an important aspect of both perception and actual power. When a typical tube amp is driven hard by players looking for that kind of tone/texture, they are often driving the amp well beyond 10% THD which represents both an increase in power as well as an increase in volume due to the harmonics falling into a region where the ear is more sensitive. In fact, this is one reason for the popularity of some Darkglass models (using solid state power amps plus drive algorithms). The native voicing of an amp will also come into play, as well as the increase in average power (a form of compression) when these amps are driven hard. The same thing can be done (with varying degrees of success) with solid state power amps and suitable engineering, but it comes fairly naturally with many (not all) tube power amps. -
Tube power stage vs Class-D (effective power)
agedhorse replied to Paddy Morris's topic in Amps and Cabs
Part of the reason for Randy's statement is because the burst power was significantly higher than the continuous power. The power supply is not typical, there is an awful lot of energy storage which holds the supply voltage higher than is typical. While it's a little harder on the tubes, the clean (or undistorted) dynamic power increase is few dB over the continuous power rating which, along with the voicing choices, contributes to a loud, dynamic sounding amp. While the continuous power is around 350-400 watts RMS, the dynamic (also called burst but rather than 20mSec, it's closer to 100mSec) power is closer to 600-800 watts RMS. This is on the 400+ with capable tubes. -
Separate preamp/power amp question. I want more volume...
agedhorse replied to Yorkshire Bottom End's topic in Amps and Cabs
Maximum output level depends on the capability of the output stage, it has to have enough voltage swing capability to reproduce whatever input level x gain requires for undistorted or unclipped output. -
Separate preamp/power amp question. I want more volume...
agedhorse replied to Yorkshire Bottom End's topic in Amps and Cabs
(Voltage) Gain is output level divided by input level. Maximum output level it the voltage that an output can deliver without clipping. You can have high gain but all it does is clip because there’s not enough output level to reproduce the unclipped signal, that’s the basis for distortion pedals. The two parameters are relatively unrelated, you can look this up on a good engineering website. -
Separate preamp/power amp question. I want more volume...
agedhorse replied to Yorkshire Bottom End's topic in Amps and Cabs
It's NOT gain that's the issue, it's the maximum output level which is an entirely different parameter. -
Yes, as Paul said, this is one of the things that the direct output covers. While the owner's manual addresses interfacing with mixing consoles in detail, exactly the same applies to recording interfaces. Be sure you identify what signal level(s) your interface wants to see.
-
Separate preamp/power amp question. I want more volume...
agedhorse replied to Yorkshire Bottom End's topic in Amps and Cabs
And this is WHY a full set of specs is so helpful. There are very few products in the bass/guitar world that provide this necessary information, which requires an unhealthy amount of guessing to arrive at a solution. Then again, it's also necessary to understand the specs. -
Separate preamp/power amp question. I want more volume...
agedhorse replied to Yorkshire Bottom End's topic in Amps and Cabs
Go watch Eurovision The Movie. It's silly, campy, in marginal taste, but funny and very well done. -
Separate preamp/power amp question. I want more volume...
agedhorse replied to Yorkshire Bottom End's topic in Amps and Cabs
It’s not gain or gain structure but limited maximum output level of many (not all) pedal preamps that’s responsible for not being able to drive a power amp to rated output. if a power amp has an input sensitivity of +4dBu (power amp sensitivity is measured with the input level control all the way up), the preamp must have a maximum output level capability of AT LEAST +4dBu (I recommend 6dB more if possible) in order to achieve rated power. The output impedance of the driving device (preamp) should be roughly 1/10th (or less) the value of the input impedance of the driven device (power amp). If not, there will be additional losses. In the case where the output impedance is 12k and the input impedance is 10k, there will be a ~6dB loss. Unfortunately, these specs are often omitted (or unknown/unmeasured) by manufacturers which makes matching a crapshoot. As an example of a pedal preamps that’s that can easily drive a power amp to rated output, the Genzler Magellan Pre-Di is one. It also includes all of the important, necessary specs to document the performance: Specifications DIMENSIONS: 6” (152mm) W x 4.3” (110mm ) D (w/ jacks) x 2.5” (63mm) H (w/ knobs and feet) WEIGHT: 1.1 lb (0.5kg) POWER SUPPLY: 9VDC-18VDC (low noise type), either polarity, 80mA POWER SUPPLY JACK: 2.1mm center pin with 5.5mm barrel (standard Boss pedal dimensions) INPUT IMPEDANCE: 1 Meg Ohm INPUT SENSITIVITY (nominal): -10dBu to -20dBu (instrument level) INPUT SENSITIVITY (maximum): >0dBu (9V supply), >+5dBu (12V supply), >+10dBu (18V supply) HIGH PASS Filter Range: 25Hz – 120hz, 18dB/oct variable EQ Filter Points: LOW: +/-15dB shelving below 75 Hz MID: +/-15dB peak-dip, between 150Hz – 2.8kHz HIGH: +/-15dB shelving above 6kHz PREAMP OUTPUT IMPEDANCE: 1k ohm (unbalanced), 2k ohm (balanced) PREAMP OUTPUT LEVEL (nominal): -10dBu to +4dBu (line level) PREAMP OUTPUT LEVEL (unbalanced maximum): +8dBu (9V supply) +12dBu (12V supply), +16dBu (18V supply) PREAMP OUTPUT LEVEL (balanced maximum): +14dBu (9V supply) +18dBu (12V supply), +22dBu (18V supply) DIRECT OUTPUT LEVEL (balanced nominal): -30dBu (mic level) DIRECT OUTPUT IMPEDANCE: 2k ohm (balanced) AUX INPUT IMPEDANCE: 10 K Ohm AUX INPUT LEVEL (nominal): -10dBu, stereo (sums to mono) AUX INPUT LEVEL (maximum): +10dBu, stereo (sums to mono) HEADPHONE OUTPUT: Drives headphones and IEM buds from 8 ohms -200 ohms, stereo output, mono signal path. (Higher impedance headphones, such as 600 ohms, will result in less output and headroom.) -
That’s the reason for annealing and part of the reason for the dome shape (the other primary reason is to improve the HF radiation pattern). Work hardening and subsequent fatigue fracturing occurs when there is repeated flex in a material that is stiff in nature. As a practical example, JBL successfully perfected this process on their aluminum dust caps and high frequency diaphragms, they can last a lifetime if not abused.
-
Mesa Subway d800+ repair and replacement parts
agedhorse replied to columbusrobbie's topic in Repairs and Technical
My suggestion is to contact Surrey Amps, this is pro level service and Stan Lawrence is a highly qualified and experienced service engineer who is fully capable of taking care of Subway amps. I can support him at the factory level too. https://surreyamps.co.uk/contact-us