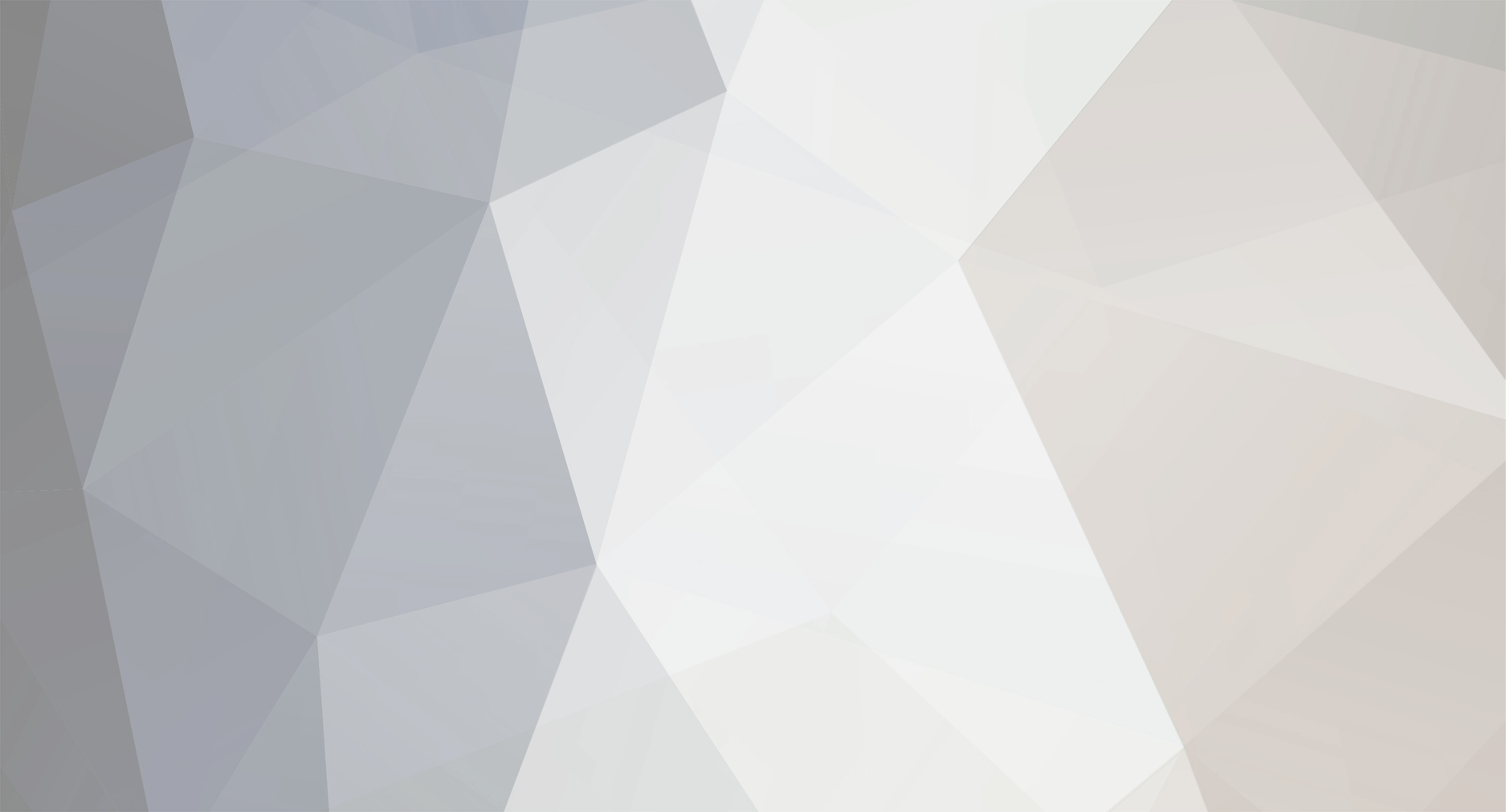
agedhorse
Member-
Posts
965 -
Joined
-
Last visited
Content Type
Profiles
Forums
Events
Shop
Articles
Everything posted by agedhorse
-
You ought to try some of the newer SMPS/class D offerings, you might be pleasantly surprised...
-
With the benefit of hindsight, I am in the unique position of being able to evaluate the reliability and lifespan history of many of my speaker and amplifier products. Speakers, when powered reasonably can last a virtual lifetime. We have many customers that have used speakers that are 20, 30 and 40 years old without a single issue and they are still perfectly fine. I had plenty of (pro level) PA speakers that I used in a touring environment 4 or 5 nights a week that lasted 20 years without any work necessary and continued to work fine for years after they were sold. All of our speaker products came with a 5 year warranty too, so 7 years is not well out of warranty and I would be horribly disappointed in me designs only lasted 7 years... that's a shameful expectation IMO. Bass amps generally last 10+ years without attention but I am now seeing bass amps in after 15-20 years of hard use that need refurbishment. It's not the SMPS and Class D part that needs work, it's everything else that suffers the wear, tear and handling accidents. Out of a hundred amps a year that I see through the shop, I replace maybe 2 or 3 power modules. So much for the urban myth that "all" modern bass amps are unrepairable/unservicable.
-
Certainly those who are under-qualified tend to struggle, but qualified pro techs generally don't have many issues. We have factory techs that can turn around 4 or 5 amps a day (depending on the problems of course), but they are excellent and good troubleshooters too. It's no different than for any product, the better qualified the tech is, the easier it is to fix. When I work on class D bass amps, I typically spend less that 1 hour on each amp. I find them easier and quicker to repair than my older class AB/G/H designs.
-
Don’t forget that sone of us have designed these products commercially for decades and have a much larger view of the results of “player versus speaker” interactions.
-
Sag is both measurable and subjective. It can be responsible for perceptions that are at odds with what’s really happening. Some of it is related to “perceived compression” and some is due to distortion harmonics that are generated. For some players this is good, for others it’s undesirable.
-
Reasonably powered, a quality bass guitar driver shouldn't wear out for many decades. Accidental damage and defects are a different matter of course.
-
Agreed, a 4 ohm load from 2 x 8 ohm drivers does. It suffer from the driver design sensitivity challenges that most 4 ohm drivers face. It’s also not impossible to design an equally sensitive 4 ohm driver, it’s just much more difficult and may trade off against other important parameters.
-
Driver construction has improved greatly over time, especially the bobbin materials and adhesives used. Also, for bass speakers, more attention has been placed on improving mechanical limits. This means that in general, matching the rms rated power of the amp to the rms rated input of the speaker is generally pretty safe. The main exception to this rule is when using heavy distortion and/or heavy compression. Under these conditions, I recommend some derating of speakers (maybe to 75% of their published rating) but conservatively rated speakers may not need this. There were two parts to JBL’s recommendations, unfortunately they get mixed up in the discussions… the part Bill quoted was for the HiFi industry and addressed the high frequency distortion impacts on tweeters mostly. There was also a section for OEM (original equipment manufacturer) customers regarding low frequency drivers for MI (musical instrument) applications which recommended a 50% derating for use with distorted and compressed program material. This was also incorporated into the OEM warranty agreements. I completed the JBL reconing and service school back in 1978 and worked at a service center that was JBL certified very early in my career.
-
In theory, it will be 3dB louder BUT in practice, it's very difficult to design a 4 ohm version of an 8 ohm speaker with the same sensitivity (based on power). Typically, the 4 ohm version will be from 1-3dB less sensitive, which offsets the increase in power. Additionally, if a 4 ohm speaker is being driven closer to maximum rated power than the 8 ohm version, there will be some additional losses due to thermal and electro-magnetic power compression.
-
Just a quick note... a nominal 8 ohm speaker can have different definitions but under IEC-268-5, will have an average impedance of 8 ohms with a minimum impedance of no less than 20% below the nominal value within the defined pass band. In reality, many manufacturers play fast and loose (or highly creative) with this definition, something that amp designers must anticipate (and that regulatory safety test labs will test for).
-
Sorry, this is not true. No, it's impossible to have DC offset on a tube amp, the output transformer prevents this. Sorry, not at all true. Sorry, not true. Woofers don't care about distortion and clipping as long as the distorted/clipped power is within their RMS rating (and the rating is honest) That's fine until the player has an accident (ie. cable pulled partially out of the bass causing a high power transient event) or the player has a lapse in good judgement that typically goes hand in hand with unrealistic expectations.
-
If you are looking for a brighter tone with a little sheen on it, the TT-800 will get you there by using the bright switch on the front. That's exactly what it's there for.
-
Or you can increase the Fb of the enclosure a little bit which will shift the ~43Hz peak upwards a bit while at the same time increasing the max SPL in the 50-70Hz range. If you want keep the LF extension the same (especially F10), then a slightly larger enclosure will offset this. It's very much a balancing act between variables, but IMO better choices could be made. Yes, this was much more common with vintage drivers, especially with extended low frequency tunings.
-
Because the tuning that produced that plot was a poor tuning choice and one of the impacts is poor mechanical power handling in exactly that region. It's no surprise, and no experienced designer that I know of would choose that either. They would quickly recognize that they were well beyond the optimized zone. This is the plot for an equivalent 212 at 600 watts RMS with an appropriate tuning. Note that the driver I developed had 0.75mm greater winding height than the stock 12PR300 and a different mid voicing, but the majority of the improvement is a better tuning choice. The ideal HPF setting would be 4th order BW, ~50Hz. The cabinet F3 is 57Hz, the F6 is 51Hz, and the F10 is 45Hz.
-
That’s with an overdamped tuning which is NOT representative of the NX2 nor the customized version of that driver. You are comparing apples and watermelon, the only similarity is that both are fruits.
-
In most older (solid state in particular) power amps, the placement of the caps is such that they don’t get very hot. For example, a cap that’s rated for 1000 hours at 85C might be good for ~30k hours at 35C. This depends somewhat on the construction of the cap and the electrolyte used. Think about this for a moment, there are caps used in equipment that runs 24/7 for decades without issues. That’s 175k hours in 20 years, so clearly there’s a disconnect between needing a cap job on an amp used intermittently over 10 years and the above example. I have a test amp (Genz Benz ML-200 that I designed ~20 years ago) that’s been running continuously in my shop for 14 years, that’s 123k hours without any issues. By urban folklore, it should have needed multiple cap jobs. In fact, there are thousands of these amps out there and none have needed a cap job (that I am aware of, but since I handle the factory service for the brand, I would expect to hear about the need for parts. IME, the promotion of cap jobs is way overdone, but they are a highly profitable way to extract money from a gullible customer if that’s the business model you are ok with.
-
I see old amps all the time, in very old amps around 50 years I do sometimes see the beginnings of electrolytic cap deterioration, but then again I see plenty that old with no issues whatsoever too. Since this amp came out in the early to mid 90's, and used the newer style caps, I would leave them alone unless there is an actual issue.
-
That's not the box and tuning of the NX2, and the mid voicing is much better (IMO) on the 12PR300 (as well as our custom variant). That's a way overdamped application which I have always stayed away from.
-
It's very uncommon to see a failed driver in those cabinets. The best replacement is the 12PR300, it's not exactly the same but the primary difference is in the mid voicing (the 12PR300 is a little more polite) and the original parts have a slightly longer VC winding height. The important part is that the 12PR300 will work with the same cabinet tuning as the GNX-12350 without any fuss. I do not recommend anything else.
-
I very rarely find defective electrolytic caps, my experience is that caps made in the last 40 years are likely to last 50 years or more provided the designer respected the design requirements of the part. In amps that I designed on the past, going back over 30 years, I have yet to see a bad electrolytic cap (other than one that was damaged by a repair attempt). When sample caps are tested, they are fully within acceptable spec. I have seen plenty of PCB’s damaged by techs or adventurous users doing cap jobs (without the proper knowledge, skills, experience and tools) and creating expensive paperweights out of their formerly perfectly fine amps. I generally recommend leaving well enough alone, it it isn’t broken, don’t break it!
-
It doesn't even need to be synchronized for the benefit of increased power efficiency (though it may be necessary for other reasons such as EMC control, THD reduction or purely functionality depending on how the topology is achieved.) The PWM frequency is high enough that it all averages out with the lower audio frequency and the reactive power reclamation still works.
-
Generally, no. The output stage is configured as either 1/2-bridge or full bridge depending on the power supply and the design of the power amp.
-
This particular mechanism doesn’t apply to class AB/G/H amps, so the increase in efficiency doesn’t apply for these types.
-
Bridging (internally) on class D amps is done for very different reasons. It allows reactive energy stored in the electro magnetic field of the voice coil moving within the motor to be transferred to the the opposing rail(s) of the power supply rather than to be dissipated as heat. This improved efficiency.
-
It may not be a bridged output either, which helps by eliminating some particular failure modes.