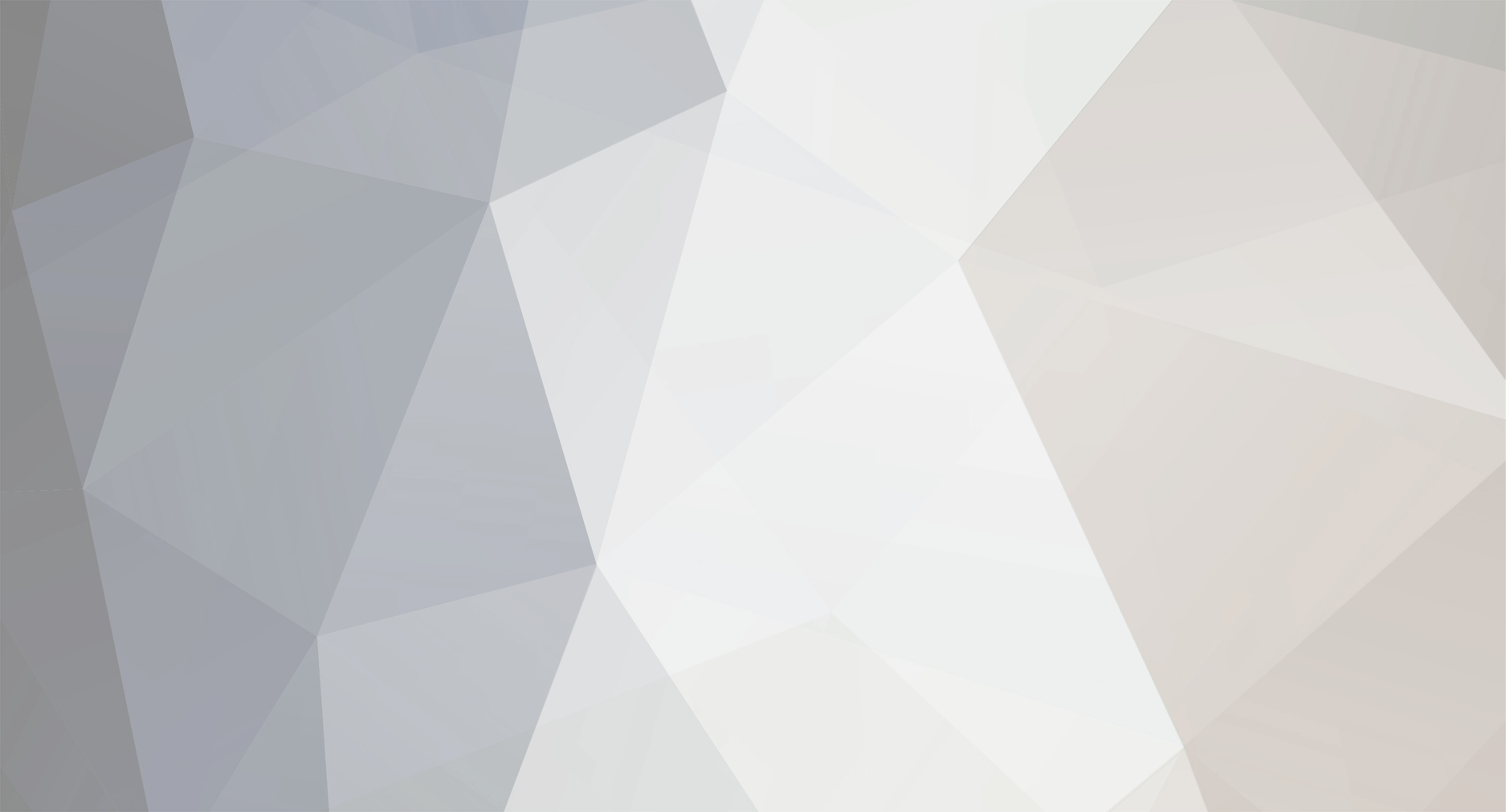
Al Heeley
Member-
Posts
1,806 -
Joined
-
Last visited
Content Type
Profiles
Forums
Events
Shop
Articles
Everything posted by Al Heeley
-
Sorry guys, black really does it for me. Here's the first primer/undercoat.
-
Moving on nicely. Finished profiling the neck. Wings jointed and glued on. Neck block planed flat and flush with wings. Top wing routed and binding fixed. Next job: Rout for pickup cavities and stick on the fretboard. Then it will be painting time.
-
Wiring up the pickguard. Nothing fancy in the end. 500k pots, 0.047uF caps, no extra 'bright'(bass cut) cap or push-pull, output will go to a single mono jack.
-
Made some good progress on the neck carving this evening. Sadly doesn't really show up well in the photo. It's immensely pleasing to see a slim neck carve slowly emerging from a thick slab of wood. Getting this done is a massive milestone in the guitar build. Once it's done, it's time to attach the fretboard and glue the wings. Then she'll really begin to take shape. Ric Pups arrived today, courtesy Rosetti London. Now waiting for the bridge pup mount ring and cover to arrive, which had to be sourced US-side. Watched a 4003 bridge mount and cover soar to a ridiculous price recently on ebay. HORROR! Been searching for a jackplate narrow enough for the slim ric body. Yet another non-standard item with all the UK parts shops selling only the Les Paul and Epiphone generic types, which are too wide. Luckily I have a friend who is a master of metalwork and has promised to fashion me a nice little chrome piece to fit the body.
-
Yesterdays progress: I now have a ric-shape headstock and a roughed-out control cavity to tidy up.
-
Finally got some time to get back to the bass build today. Here the lower wing has been sanded smooth, binding channel routed and binding glued and trimmed flush. MArked on the routing area for the ctrl cavity. Work started on shaping the neck/headstock; a real pain without access to a bandsaw. Annoying miscalculation with the jigsaw in cutting the headstock to thickness means it's now a little thinner than i would like before final sanding, and there's a bit of an ugly gouge out the back. Maybe I can glue on a 2mm laminate to get back up to thinckness before drilling for the tuners.
-
Here the thru-neck block has been planed and sanded level, fretboard position and nut marked on, and truss rod channel routed. (Yes I know, rod is wrong way up here but the blue colour makes for a better pic ). On either side of the truss rod channel I've routed a 6mm channel to take the carbon fibre reinforcing rods. Hopefully this will mean I can carve the neck down nice and thin and still retain good stability.
-
Maple cap on the mahogany wings has been planed to thickness and edges sanded smooth. The maple will be routed for the binding later once the wings and neck-thru have been joined. Here's a quick mock-up to show the body and neck together. Next it's time to start carving and shaping the neck.
-
More work on the body. Mahogany base and maple cap cut to size, being glued together. the pencil line marks the final thickness of the cap - a lot to plane off over the weekend. This brings the body depth to the regulation ric 1 1/4 inches and also the maple cap thickness will then match the depth of my white binding.
-
I have a single (dual action) modern truss rod to fit, and will insert 2 carbon fibre spars into the neck either side of the truss rod to help stiffen it up. Started on the neck; Here she is, all clamped up and oozing PVA. Luverly.
-
Scored some wood today. A small departure from authent-rickity - just cut the rough body wing shape out of mahogany; this will get a maple cap (well it works for Gibson and PRS) The neck is 2 pieces of maple with a central cherry strip to add a little flavour.
-
Quite pleased with how the side dots came out - I was too lazy to order some black dot rod so I used up a little left-over white rod and pushed it inside small sections of a black scoobie I stole from my daughter. The result - tiny little liquorice allsorts that glue into the holes and make a cute little circle marker.
-
Not much building progress this weekend, due to band practices. Got the pickguard and TRC made from the white blank.
-
Fingerboard finished today: bound and fretted.
-
This is Indian rosewood. Fretboard sized, radiussed, slotted and dotted. Sorry, not brave enough to attempt the triangle inlays yet.
-
Here we go then: Stage 1 I've really always wanted a Ric 4003, but I can't afford one or wait for x months for one to come up so I decided to have a go at building one. Here's stage 1 - the full -size plan drawing from which the varioous templates will be cut. Construction planned: traditional maple body wings, thru-neck maple (maybe walnut sandwich), 4003 electronics with push-pull bright cap on the bridge pup tone. Finish: most likely black rattle can with Rustins plastic 2-pack resin. White binding (of course) :cool: Now the shopping begins. [color="Navy"][font="Arial Narrow"][size=1]Disclaimer: I am building this bass for my own pleasure as a home hobby and do not intend to sell or profit from the guitar in any way - should the finished item bear any resemblance to a real Rickenbacker, then it is purely coincidental.[/size][/font][/color]
-
[quote name='BigRedX' post='362775' date='Dec 24 2008, 01:20 PM']Nice to see that again (and the slightly scary eggs!) Any extra news to post since this was up on TalkBass? Have you upgraded the pre-amp yet? You should post your Rickenfaker build here - there's more than a few people who would be interested in that who might have missed it.[/quote] Thanks mate! I've reset the neck and added an active/passive switch since last time but stuck with the same pre-amp. Need to start playing it more, at the moment I'm in love with my jazz bass. I will port the Lemonbacker project over shortly...
-
This website may help you in your quest: [url="http://www.drtube.com/marshall.htm"]http://www.drtube.com/marshall.htm[/url]
-
Beautiful basses, some lovely choices of wood, you must be a very happy man.
-
Finally got the machine heads on and a set of strings. Nut cut rough, needs a good setup now but she's all working and making some of the right noises. A fair bit of fret buzz in places for now but nothing that a bit of levelling won't solve. I must say it does feel very comfortable virtually striaght off the bat playing fanned frets, far easier than I was expecting. I've really enjoyed putting her together and learning a bit more about this great craft. I think a decent pre-amp system is on the shopping list for the end of the month.
-
Some more progress. Neck trimmed flush (pocket routed deeper) and the electrics all wired up. Neck given a few wipes of Tru-Oil - more to follow. I also inlaid a little copper-ring bloodwood circle into the headstock. Now just waiting for the machine heads, then the nut can be cut, and frets levelled. Then she's done
-
Small inlay detail, bloodwood set in copper. Fingerboard's still a bit damp from the oil
-
face-on shot with the hardware positioned and fretwires cut, ready to be bashed into place with the heel of an old shoe.
-
More progress; fingerboard trimmed, radiussed, slotted and dotted. Body has acquired a jb bridge pup and a mini three-way toggle. Wierd perspective tricks with these fanned fret and staggered bridge builds, the photo makes it look like the pickups are skewed but they are perfectly perpendicular to the centre line. I have a few MOP inlay circles left of various size, and was going to add some sort of extra design at F12, but with the small and simple circle markers against the dark ebony, i think it looks a lot more classy.
-
Fingerboard arrived, nice thick slab of ebony. Almost feels like stone. Started cutting the fanned frets. [Note to self for next build: I'd be happier with the pickup an inch or two further back, and about quarter of an inch wider neck to play with where it joins the body.]