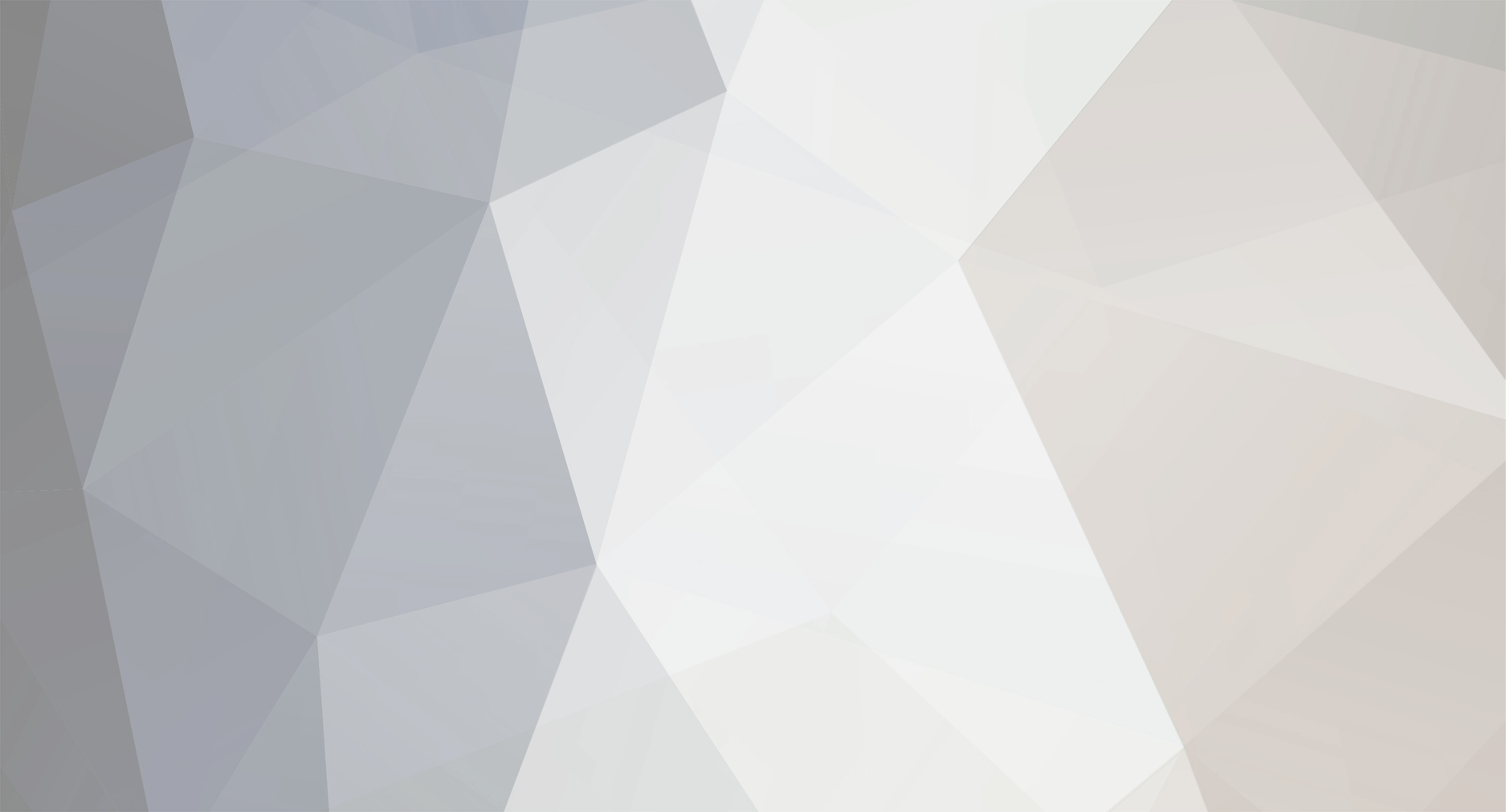
3below
Member-
Posts
2,656 -
Joined
-
Last visited
Content Type
Profiles
Forums
Events
Shop
Articles
Everything posted by 3below
-
Apologies to @Dom in Dorset, I had also misinterpreted the op and with hindsight (looking at the guitar quality) had stated the obvious that you will know. The extraction by drill hole was neat.
-
Assuming a dual action rod...... If it has come out from the headstock end (without any drama) then drive the new one in from the headstock end, unless I have missed something obvious. Prior to insertion check the welds on the new rod for any 'lumps' that might bind in the channel and grind them down. Round the edges of the fixed end to prevent 'digging in' and wax or PTFE spray the rod. Might be worthwhile getting the same into the channel somehow. Finally, I would give the new rod some hefty adjustments both ways. Better a duffer fails beforehand so be bold.
-
I am lost for words but am so glad to hear that you are alive and well (that is a relative term). Don't know what I can offer to help with from this distance. Can certainly give you a bass, though it will be long or medium scale.
-
@Silvia Bluejayis on the money (pun intended). Feeling idle, rather than making my own, I looked into the same problem for a different make EUB that I own. The time involved will soon mount up for a one off luthier made bridge which makes the Gollihur offer a no brainer. I have used Gollihur for strings, made in France, sent to the USA, then back here and duty applied. Still cheaper than here
-
Missed that, however turning off unwanted peripherals: wifi, BT, lowering clock frequency and using a single core will have a substantial effect on current draw. some data here gives an indication: https://www.mischianti.org/2021/03/06/esp32-practical-power-saving-manage-wifi-and-cpu-1/. At 10Mhz cpu frequency (more than adequate to control leds and make sample voltage measurements) the current draw is about 13.2 mA. In reality it will be higher even before the LEDs and potential divider currents are factored in. These could be switched e.g. > 60hz with LEDs, battery sampled every 10 mins? 5 mins?
-
NND- New Neck Day for by Custom P Bass Body
3below replied to Old Horse Murphy's topic in Bass Guitars
Late to the party gorgeous looking bass, natural no scratchplate or control plate, my favourite combo. Dimarzio j types might be one answer. I have a set that have moved over several basses, humbucking split coils, so virtually a p pickup in a straight line. Lol autocorrect put humouring split coils at the first go. -
1x15 would be of considerable interest, I have a pair of 3015 kappalites awaiting use
-
That is a genius idea (and once mentioned is obvious). I like it I also like your UC choice, my time has also recently been focussed on ESP32 with WiFi and BT.
-
A good trip out . If you are going to use a microcontroller with the marker LEDs you could use a simple potential divider and a GPIO with ADC to determine low battery voltage. There are also various Arduino ready made voltage sensor modules available very cheaply.
-
From Middle English fetlen to shape, prepare; I did not know the origin of the word until I looked it up, it can also refer to a person's health - e.g. to be in fine fettle. In a more useful vein, the multi channel piezo pre amp https://www.bassparts.de/epages/61038859.sf/en_GB/?ObjectPath=/Shops/61038859/Products/PPX. They also make other interesting stuff at £££.
-
Fully understand the string balance issue, I have had to fettle several piezo guitars and basses to get reasonable results. I can see the appeal of Individual string outputs, particularly if you want to use midi. The last question probably has the easy answer, Individual string intonation gives better results than bar bridge types.
-
Adjustable bridge something like the one I made (and pretty generic) , this will give you height and radius adjustment and allows a simple rod or flexible piezo. You have the luxury of being able to print something fancy. You could sink it into the body, have a look at this https://www.liutaiomottola.com/instruments/libellula.htm. I have owned a fretless acoustic bass with a simple bar bridge since 1980. The original Roto Tru Bass strings lasted 40+ years, intonation has not been an issue. If you want individual string piezo amplification and are going down the diy route, in principle I would use two quad JFET op amps, with individual op amp buffering of each string in unity gain non inverting mode (you can get octal JFET op amps, however afaik these are surface mount so present a further complexity). These outputs would then feed into an inverting summing op amplifier to allow the individual string outputs to be equalised (through some variable resistor arrangement). Input capacitance, consequent high pass filtering, and setting the bias voltage, depending on what your proposed voltage supply is will need to be considered. There are plenty of good examples about to study e.g. https://www.analog.com/en/analog-dialogue/articles/avoiding-op-amp-instability-problems.html and this one. the title is so understated a mere 464 pages. https://web.mit.edu/6.101/www/reference/op_amps_everyone.pdf Hopefully more experienced Electronic engineers / designers will be along who know what they are doing, or someone knows the commercial product that will do what you want. I have seen a suitable commercial bass piezo pre amp that has individual string inputs but can't for the life of me remember what it is . Me, I would go simple in the first instance. If it does not work (i.e. strings too imbalanced) then look at mk3 bridge with the added complexity.
-
Onwards and upwards Battery indicators are a whole bundle of interesting electronics as you will discover. It made me think of a simple alternative. Dual battery compartment with a two way switch over in the event of one running down. My ex military Land Rover had dual fuel tanks which made me think about dual batteries. I can not imagine the cost of filling it, or running it, if I still owned it. This JFET pre-amp looks really useful (and small) and can be ordered with 10 MOhm inpout resistance for piezos. https://www.ebay.co.uk/itm/272951584025?hash=item3f8d2ea519:g:-CUAAOSwoFtfBGX8 They also make a version ready made with jack plug etc. In terms of bang per buck, I really rate the Joyo 504 / 505 preamps, however they are probably too big for Flo2.
-
All the above points are totally sensible and a means to using time effectively. I personally don't see the problem with reading music as you play - being at a certain age I can sometimes forget basic chord sequences of things I have played many times but have not played recently. Remembering the fills, passing notes, tricky bits does not seem affected. I do have a problem with people not putting the time in beforehand.
-
I really like the realist pickup as do many others, however, it can develop faults such as intermittent, low or no output at all. The good news is that they can be repaired and if you are lucky it is a an easy DIY job. Failure with the piezo dots version seems to be caused by the conducting adhesive giving up with age or through corrosion on the strip metal contact inside the pickup. First fix: They can be 'fussy' about how well the bridge foot is seated on the piezo dots. Ensuring the bridge is sitting 'upright' and making good '90 degree' contact on the piezo dots , is one factor. Also where the dots sit under the foot can have a significant effect - experimentation is worthwhile. Second fix: If you have the version with the obvious piezo dots, try pressing firmly on the dots with a piece of wood (e.g. kitchen knife handle, pencil, with the pickup supported on a worktop/cutting board). Next gently rub the foil against the piezo dots on both sides. This has been successful in getting reluctant ones to work again. Third fix: Major surgery, this involves taking the foils apart, rebuilding / replacing corroded parts / new conducting foil inside the pickup and some soldering. It will usually be visually obvious that this is needed. Even with this level of repair I have not (yet!) failed to bring one back to life.
-
Useful link, https://vmascagn.web.cern.ch/LABO_2020/LTspice_and_wav_files.html.
-
Frequency plots are really informative (remind self, must get a life other than physics/electronics). It will be interesting to hear the results of taking a J or P bass (as a starting point), and applying the plot boosts/cuts using a free VST graphic equaliser e.g. the Moss Equalizer, a 265 band FFT equalizer.
-
Inspiring work , well built valve amps are a thing of true beauty. I also value that they can be easily repaired in the event of component failure - smt technology is not friendly to those of us with ageing eyesight. Any reason for choosing eyelets over turrets other than personal preference?
-
A good bit of lateral thinking. If it does not work to your satisfaction, you would still be able to try carbon rods in the channel(s).
-
Neck Time - Looking for experience & suggestions
3below replied to SamIAm's topic in Repairs and Technical
The finished neck will have the same overall depth whether it is your one piece design or a neck plus fingerboard. The only way a separate fingerboard will improve stability is if the board is stiffer / more twist resistant than the wood that you would use in the remainder of the neck. I see no (obvious) reasons why your route from the back + skunk stripe approach will not work with a dual action rod. One subtle benefit you can gain from a separate fingerboard is the ability (to some degree) to adjust the relief / fall at the top end of the board by judicious levelling if needed. Despite my physics/engineering former life, I can not reach any conclusions about carbon fibre rods in necks (nor do I have any practical experience with them to go on). It seems to me that it would be all too easy to over stiffen the neck and thus needing the truss rod to add relief ( I unintentionally achieved this state on my last build with a very thick fingerboard and deep chunky neck, no carbon rods). Careful choice of rods seems to be required. -
Neck Time - Looking for experience & suggestions
3below replied to SamIAm's topic in Repairs and Technical
Ben Crowe Crimson guitars video is informative. https://www.youtube.com/watch?v=RHV_LN8F1Qw Others may have different views. IMO one of the key aspects is to use well seasoned wood. Cut, glue, rough shape whatever and then give it a few days before doing more. I have had well seasoned wood move after cutting / thicknessing. This video https://www.youtube.com/watch?v=AU_vdW_HgI0 shows the joys of multi laminate construction aka greased piglet wrestling. Clamps are your best friend, you can never have enough I can see how using a three (or 5) piece laminate neck might aid the truss rod channel and skunk stripe construction by removing the need for a routed channel. Make the centre laminate just slightly wider than the truss rod. Cut out the truss rod slice to the correct depth, length and profile. Keep the 'cut off' slice and cut it down to create the skunk stripe. The ends of the rod where the threads are can often be wider than the main rod and may have dots of weld that need smoothing down. You will have to ponder that a bit. Hopefully the pictures explain. -
Fitting tuners if headstock holes are too big
3below replied to Paolo85's topic in Repairs and Technical
When you bring the strings up to full tension any remaining play will be pulled solid. This happens even when the holes and bushes are a really good fit. Tuning stability is then not a problem in my experience. -
Fitting tuners if headstock holes are too big
3below replied to Paolo85's topic in Repairs and Technical
Same problem when I fitted them to my Gibson. I cut strips of plastic milk carton which then filled the gap perfectly. Has worked perfectly for the last 10 years or so. Hipshots sorted the neck dive on the SG bass, they also improved another bass I fitted them to. -
I have a similar effect with my G&Ls. TI flats on the SB-1, the mutts nuts, current set 11 years old and going strong. TI flats on the L1505 just seem floppy but I keep persevering and try to use a lighter right hand. Defies all logic.
-
Neck Time - Looking for experience & suggestions
3below replied to SamIAm's topic in Repairs and Technical
David Dyke https://www.luthierssupplies.co.uk/ElectricG.htm is frequently mentioned by @Andyjr1515 in threads. I have used 'old' oak and mahogany for necks without problems. The mahogany was from broken down snooker tables, really old, very stable and a pleasure to work with, £4 for a side that would make a body and neck. I wish I had bought much more of it at the time. Maple or Wenge will be fine with flatwound / tapewound strings. Keeping maple clean in the long term might be an issue (or not if you want roadworn). From wikipedia: "The dust produced when cutting or sanding wenge can cause dermatitis similar to the effects of poison ivy and is an irritant to the eyes. The dust also can cause respiratory problems and drowsiness.[citation needed] Splinters are septic." A dual action rod will install in a flat slot. All types of adjuster appear on basses at all price ranges, choose what you like @Andyjr1515 and @Jabba_the_gut are the masters of finish. I find Tru oil or Danish Oil very easy, Osmo Polyx wax was incredibly good on an Oak floor I once owned, have never used it on a guitar build though.