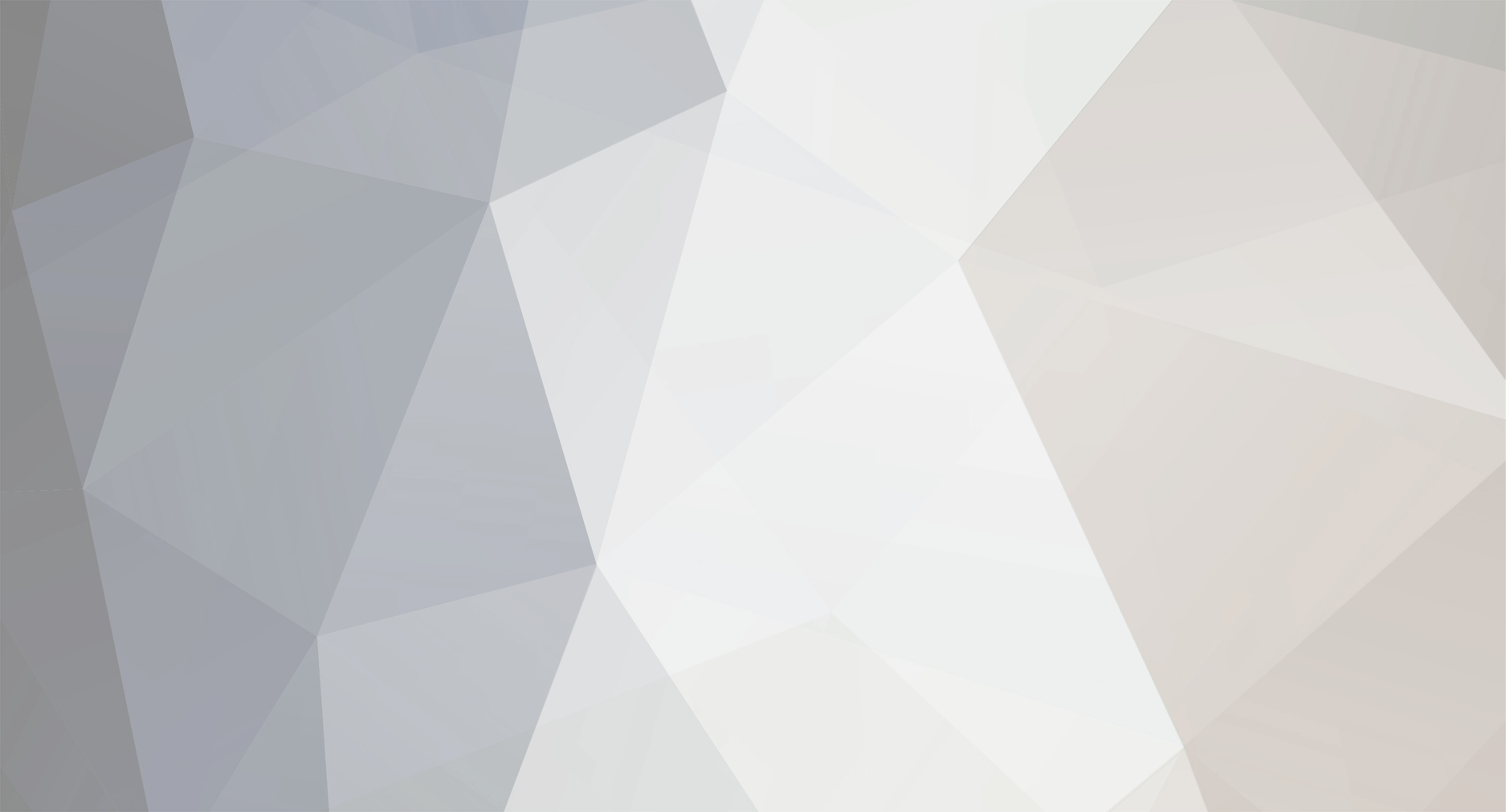
3below
Member-
Posts
2,670 -
Joined
-
Last visited
Content Type
Profiles
Forums
Events
Shop
Articles
Everything posted by 3below
-
As fitted to all but one of my far too many basses. Longest life so far, 11 years on a regularly used bass :). Long way to go to match the Rotosound trubass strings that did 40+ years on my Eko acoustic bass bought in 1980.
-
Cylindrical rods will have a tendency to rotate and twist the string as the tension increases. Print cylinders with some flats on the sides so the rotation is stopped by the neighbour.
-
Finishing an unfinished bass body a necessity?
3below replied to shoulderpet's topic in Repairs and Technical
I bought one of those from a BC member. The wood is really good and lightweight. The fit of the cavity to pickguard screws required work. The finish is ok, at some point I may sand it back and improve the body contours, they are a little crude. I also had to widen the neck pocket. -
Gibson - an enigma (1974 EB-3 content)
3below replied to Andyjr1515's topic in Repairs and Technical
There are cheapy multimeters that will do inductance, capacitance and resistance LCR, (often do transistor / diode testing as well), they are pretty good value. -
Gibson - an enigma (1974 EB-3 content)
3below replied to Andyjr1515's topic in Repairs and Technical
The very reason why I build with bolt on necks. It allows me to cover up my lack of skills at your level The build advantage of through necks in this respect is also obvious. Quite why they could not build basses accurately within the desired time/cost constraints in that era is a mystery (or cynically because they could get away with it and did not care). On my 2014 SG bass (surely cnc machined?) it should be an absolute doddle and is really inexcusable. The 'box of bridges' is a classic bodge, reminiscent of British Leyland cars. More time rectifying a car at the end of production than Toyota etc spent building one I seem to remember. -
Gibson - an enigma (1974 EB-3 content)
3below replied to Andyjr1515's topic in Repairs and Technical
7mm of bone under the string is (probably) more than that under F style and some acoustic bass bridges. No idea why Gibson would fit bone, I can just imagine the amount of breakages when trying to thread it. I believe they also had a spell of fitting nylon saddles to the 3 point bridge. After the correct neck - bridge alignment is achieved, another issue that may crop up is neck pickup alignment. I ended up rotating mine, with the polepieces further away from the bridge, resulting in a reasonably ok alignment. No real discernible tone difference to my untrained ears, instant Andy Fraser/Jack Bruce is readily available. -
Gibson - an enigma (1974 EB-3 content)
3below replied to Andyjr1515's topic in Repairs and Technical
It is good to see that the neck/bridge alignment is a 'traditional thing' and has carried on from EB0/3 into the later SG bass. The alignment issue is the same (though much more extreme) that my bass has. I can't visualise a solution other than plug and remount the bridge mounting post screws. This then creates the problem of hiding the affected area (Easy with a Hipshot bridge since it will cover it over). @bertbass Interesting insightful observation -
Gibson - an enigma (1974 EB-3 content)
3below replied to Andyjr1515's topic in Repairs and Technical
A much improved design over the bar/rod with holes extender, avoids the ball ends contacting the body issue. The bridge alignment on my SG bass is less than perfect, if I had not fitted a Hipshot (with sufficient lateral adjustment) it would have ended up being a plug and re-position the posts job. On the plus side the quality of the fretwork is very good, only bettered by the Jon Shuker board I have on a bass he repaired. -
Gibson - an enigma (1974 EB-3 content)
3below replied to Andyjr1515's topic in Repairs and Technical
I encountered exactly the same problem with my SG bass (same bridge design defect all these years later). I made a 10mm (from memory) aluminium rod spacer. I seem to remember needing to take care with the ball ends and body contact due to the extension back, hole angles and height. It worked perfectly well. Bass now has a Hipshot which is just fine. -
You are correct , I was thinking in radii, (R + S/2) and diameters at the same time. With a diagram it became obvious, overall diameters require (D+2S/2) - the string wraps round the post on both sides.
-
^no need to get out more, plenty of entertainment with engineering mathematics. It is the kind of thing I also do for entertainment, lifelong physicist / engineer here. You have me wondering do you need (b+c)*pi or (b/2+c)*pi, what is the effective diameter causing the length change, however in real world mode, the difference is negligible so I will stop @Smanththread wander. perhaps I need to get out more 🙄
-
Having never owned a headless bass I am interested to know how much tension you need to get on the strings before locking and tuning, and as @Si600asks, how much movement is needed. Me, I like headstocks, stops my left hand falling off the end of the bass
-
Not at all mad, Mrs 3below dabbles with lap steel guitar, paper print outs under perspex are sometimes used for the fret position markers, although there is obviously no string contact.
-
Bought some strings from Pete. Good all round, deal with confidence
-
Like it To prevent the tuner L brackets rotating could you could print a baseplate with guides? I am thinking about the guides (fins?) in this hipshot bridge, not the whole assembly.
-
-
Closer to E for wooden fretboard, that way the tangs press into the wood. Fretting saws seem to be 0.022" or 0.5588mm in new money, so a little under 0.6mm. Since you are using a printed carrier, you have decision to make depending on the toughness and craze / crack resistance of the polymer being printed. Either a tight fit 0.6mm and the tangs press in - with a possible risk of crack/crazing, or a loose fit up to 0.95mm and epoxy it in. I am going to throw another item into the ring, my Warwick fretless has an adjustable nut, it works really well for dropping the strings just onto the fretboard. This imo helps get the same(ish) open string tone as fingered notes on a fretless. I personally really rate them, solves a whole lot of nut fabrication issues (for me). Available on the well known internet auction site dead cheap.
-
Yes, notably when I put the octave marker inlays at the 13th fret on a slotted fingerboard I had made..
-
DiMarzio P in one of my basses with TI flats. Aggressive, thumpy, no shortage of highs, can be tamed with volume / tone. Approaches my G&L SB-1 MFD for hotness :). Cheapy (but very good) Wilkinson Alnico vintage P in another bass with TIs (again). Thumpy, complex, darker, good highs if needed. Much more relaxed than the DiMarzio. When you take a basic P pickup and analyse it, fibreboard, magnetised Alnico rods and copper wire of a given gauge wound to a given resistance and inductance, how hard is it to reproduce 'vintage' or other specs? Hence (imo) the quality / price ratio of Wilkinsons (and some others).
-
You have been very busy looks very good.
-
Barefaced Price Increase - Are They Still Worth It?
3below replied to Ultima2876's topic in Amps and Cabs
I went to buy bulk Guinea pig nuts today (the ba***r*s (10) keep eating), 25% price increase in 6 weeks. My car insurance has risen by 15%, no claims and the camera did not clock the 155mph I was doing at the time(in my dreams). We won't mention fuel price rises. The 20% on BF cab is not untoward and unexpected, although unwanted. Luckily I have owned a BF cab since 2011 and have no thoughts of moving it on. -
^ available in 5 string version as well.
-
Careful with the 2x4 ideas, that will lead you down the rabbit hole of cigar box guitars, diddley bows, 2 string basses, or one of my favourites Longbow bass etc.
-
Looks promising, my only concern would be the brass inserts. Warwick corvettes (German at least) use similar to hold the j bass pickups in. I have had them pull out/work loose. My 2p worth, I would use some rod e.g. 8mm, 10 mm that has a suitable size hole and thread. Make them the full thickness of the headstock and ca or epoxy them in. They will withstand the turning forces that the string will create.
-
The brass collet idea looks pretty nifty, but it got me thinking about another solution (inspired by my 1970s Kramer aluminium neck bass). Construct a small flat plate of appropriate spacing / size for the headstock with the keyholes / slots that the ball ends slot into. No moving parts to drop and lose. I have never got the hang of (or had the inclination to) draw in CAD etc so you will have to imagine what I am getting at