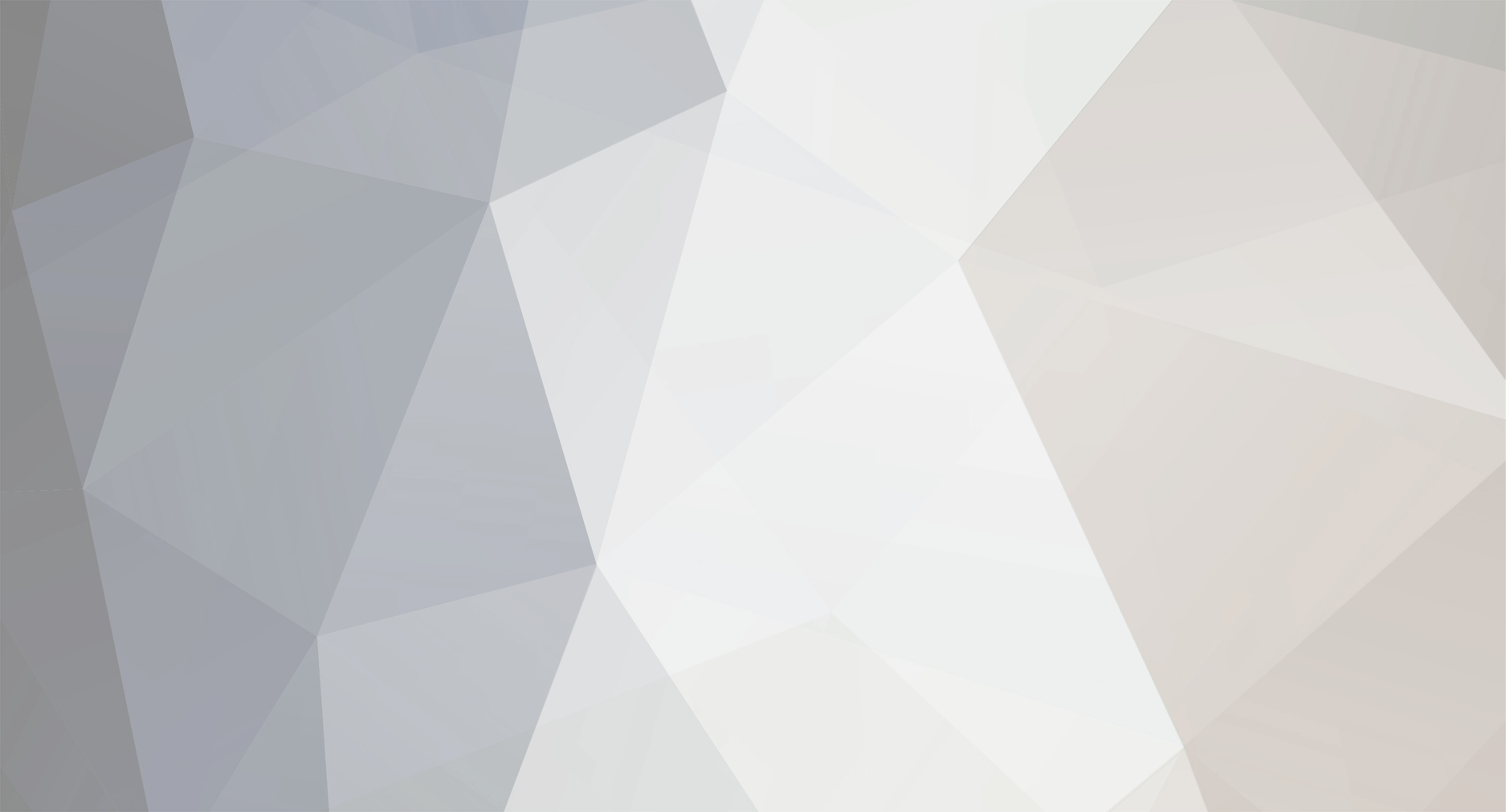
3below
-
Posts
2,656 -
Joined
-
Last visited
3below replied to Raslee's topic in Accessories & Other Musically Related Items For Sale
3below replied to Raslee's topic in Accessories & Other Musically Related Items For Sale
3below replied to BritBass 2's topic in General Discussion
3below replied to Slappindabass's topic in Build Diaries
3below replied to bigthumb's topic in Accessories & Other Musically Related Items For Sale
3below replied to bigthumb's topic in Accessories & Other Musically Related Items For Sale
3below replied to therealting's topic in Bass Guitars