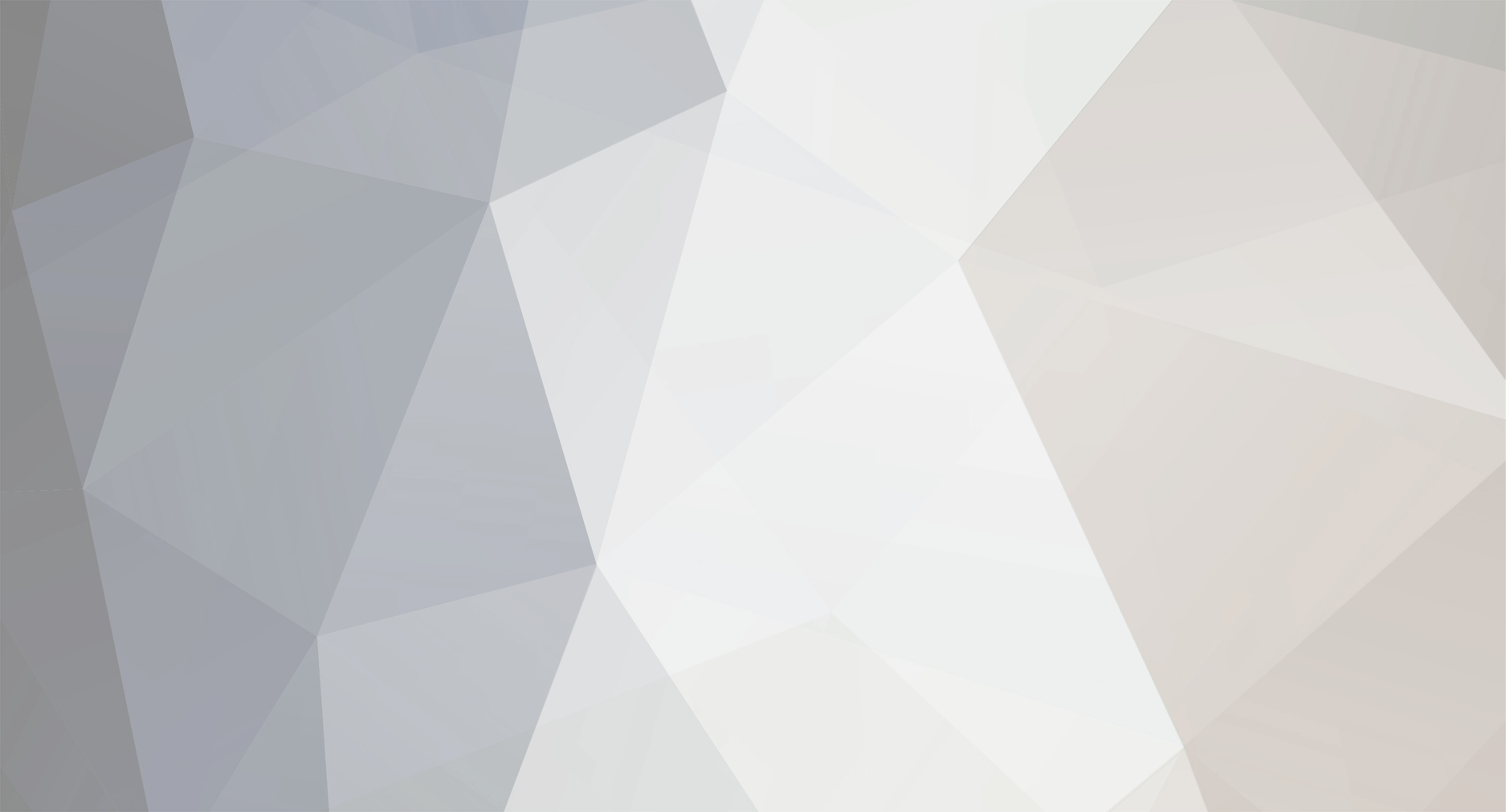
3below
Member-
Posts
2,670 -
Joined
-
Last visited
Content Type
Profiles
Forums
Events
Shop
Articles
Everything posted by 3below
-
[quote name='3below' timestamp='1475560036' post='3146850'] That was mine, it was stolen in 1981 during a gig at the Dog and Ferret. [/quote] [quote name='yorick' timestamp='1475591873' post='3147178'] Tort? [/quote] Tort? I would rather have the trifle if at all possible. I know it was stolen at that gig, I remember being amazed that the bass player did not notice me unplugging it mid song and walking away with it. Are the handles still in good condition?
-
Very interesting, particularly the order of operations, gives me thought about my next build. I am surprised how much was freehand work. The other part of me was taken aback at the amount of high speed cutting tools without guards and the methods used. Wonder what the attrition rate on fingers, hands (and arms) is at the factory.
-
-
[quote name='Norris' timestamp='1475488740' post='3146235'] Cool - can you come round and find the two centre punches that are somewhere in my garage? I've spent hours looking [/quote] Centre punches, £2.50 for a set of 3, time to find them 2? hrs at £???? Somehow it does not seem right to view tools with the cost benefit analysis method.
-
[quote name='Andyjr1515' timestamp='1475428247' post='3145836'] Brilliant! Thank you so much, 3below. That does indeed look right to me [/quote] And thank you, I will be seeking advice later about finishing when I get that far. Shed is now somewhat clearer and my 'long lost' no5 plane re-appeared.
-
After some pencil, paper and brain effort I think I have the solution. In the Gibson circuit, at switch position 4, the neck output signal (lower pickup in Gibson diagram, 0.05uf capacitor) is routed through through the RC combo then to the jack tip. At the same time the neck output signal is also routed through the inductor to ground. (Gibson circuit has the bridge pickup on as well as neck position 4). In the modified Andyjr Mk1 circuit above , the neck signal is fed into the RC combo for positions 4 , 5 and 6. These then provide a connection to jack tip' and the various inductor tap connections then to ground.
-
Random thoughts removed, goes to get pencil, paper and brain
-
What you have drawn was what was in my mind. In the cold light of morning I am not sure this is correct either. I need to get pencil, paper and brain in the job. I also need to help swmbo who wants to clear my workshop
-
After a couple of months with the lessons you have under your belt I would say get yourself into a band. At the same time use Scott's (and others') lessons if the price is right (do not spend big bucks). In many ways progress is much faster these days, Youtube is your friend. Then again I spent a lot of time listening to singles and LPs to figure out what I was hearing (no internet then) which I now think was invaluable experience - automaticity between ears and hands (and even correctly some of the time....)
-
Yes is the short answer. Longer answer is, put the parallel CR combination in front of the '4' connection on switch, neck pickup. This gives CR into switch into L then ground. Your circuit is easier to follow than the Gibson one.
-
At a first run through that appears to match what you specify. Although being somewhat 'rusty' with my electronics I am figuring that the additional resistor and capacitor at the tail end of the Gibson circuit (0.22K, 0.02uF?) are part of a parallel CR series L notch filter. Figure 8 [url="https://en.wikipedia.org/wiki/RLC_circuit#Other_configurations"]https://en.wikipedia..._configurations[/url] gives the circuit and relevant maths. Are these the extra 'extra resistor and capacitor' you are thinking of dispensing with? If so you may find you need to keep them. Like you I may have also missed something obvious in working through this. Any proper Electronics/Elec Engineers please confirm or correct the ageing Physicist who ironically is currently teaching active and passive filters.
-
In related quality control and perfection issues, whilst playing my Kramer DMZ4001 this evening what do I notice? The 12th 15th and 17th fret dots are well adrift of even spacing between the frets, probably 2 ~ 3 mm. Unlike Andyjr I do not intend to relocate the dots
-
Why will they not make a short scale EB2D at sane prices, or an Epiphone release of the same (Rivoli)?
-
Quality of pictures sets new higher bar for build accounts In other news Gibson apparently discontinue SG basses and Andyjr now steps up to meet UK demand.
-
Another good 'fix'. Attention to detail just seems to get sharper as the build progresses and like you minor imperfections start to bug me. It is a downhill (or uphill) slope.
-
What is the world coming to, 1/4 mm error. Gibson managed much more than that with my SG bass .The bridge alignment was / is out by 2mm at least. How the bass escaped with the obvious uneven string spacing on the neck is anyone's guess. Supertone adjustable saddles sorted that one out. Looking good
-
sanding a defretted fingerboard - is it necessary?
3below replied to alyctes's topic in Repairs and Technical
[quote name='Twincam' timestamp='1474926480' post='3141625'] Another tip. I find marking the board with chalk with a tight crosshatching pattern really helps to properly get a flat board once leveling so you see were any high low spots are. [/quote] Thank you . This tip will be used on my 'compact short scale build' soon, since the board radiusing and surfacing is approaching. Edited for punctuation. Txt, Email and SocMed are rendering me illiterate..... -
Nostalgia: Or the depressing reality of my fast approaching mortality.
3below replied to paul h's topic in General Discussion
[quote name='leschirons' timestamp='1474925883' post='3141617'] Our (my) first gig was £15 between us AND, we'd hired the van You had a £100 gig 40 years ago? You are John Paul Jones and I claim my £5. [/quote] Ceilidh band I started in (see above) was £80 to £120 for 4 piece in that same 40 ish year ago era. To quote myself, "[color=#282828][font=helvetica, arial, sans-serif]Downhill ever since really"[/font][/color] [font=helvetica, arial, sans-serif][color=#282828]Ivansc well in the lead as a bass player, but in the scheme of things a fair way to go. Cliff Crockett (a[/color][/font][color=#282828][font=helvetica, arial, sans-serif] relation of my vocalist / guitarist) [/font][/color][color=#282828][font=helvetica, arial, sans-serif]played the drums till 100. Started at age 7. [/font][/color][url="http://www.jazzandjazz.com/2014/05/celebrating-cliff-crockett-100-years-young-and-still-drumming/"]http://www.jazzandja...still-drumming/[/url][color=#282828][font=helvetica, arial, sans-serif]. [/font][/color] -
sanding a defretted fingerboard - is it necessary?
3below replied to alyctes's topic in Repairs and Technical
Just another perspective, gained from refretting a defretted bass (go figure, it was an Artcore bass, cheap as chips project to learn how to refret a bound neck). Once you have defretted you may well have chips and / or tearout with the slots. Obtain some PTFE sheet (same thickness as slots) and cut to sit in the slots (scissors or Stanley knife). Use some rosewood (or whatever the board material is) to make some sawdust. Compact the sawdust into the divots against the PTFE and then drop CA glue onto the sawdust. I use a magnifying glass which helps with this. Repeat this for all the divots and chips. Allow the glue to harden and then sand. Clean the sanding dust out of slots and then carry on with veneer inserts. My take is that this method will give clean, 'sharp' slot edges against the veneer. The CA and sawdust will hide some surprising damage. This is just a technique I found on the internet. -
Nostalgia: Or the depressing reality of my fast approaching mortality.
3below replied to paul h's topic in General Discussion
Celidh band, 42 years ago - I was a young 15/16 at the time. Downhill ever since really, where did all those years go? -
Purchased a P neck from John. Excellent chap, great communication. Buy/ Sell with confidence. John also knows how to package kit really well which defeats rogue couriers . Many Thanks.
-
ColinB, thanks for suggestion. They are good but the cost will add up for several. I am' just' up the road from you, near Kerry. So there are at least 2 of us in Powys.
-
Thanks again for kind words . Next mission, being a 'cheapskate' I am going to build a radiusing jig to route concave fingerboard sanding blocks. A one off at £20 ish is ok, if I build other radius fingerboards it is not tenable. Have to consume all this oak strip flooring I have
-
Small steps onwards. Headstock shaped and showing very approximate position of machine heads (stuck on with blu tack). The design will work with straight string pull, it is an amalgamation of two basses in my possession. As always after the event I can see minor details that I would do differently next time. The upper 'A' string oak strip should be a bit larger, in keeping with 'd' string piece. However next time I would stick to 5 laminations and not put the extra stripes on headstock (another miscalculation). It is as if I have to make mistakes in order to fix them and the underlying issues in my mind and thus prevent next time. This might be due to needing to do more woodwork
-
Looking good, must get moving on mine again.