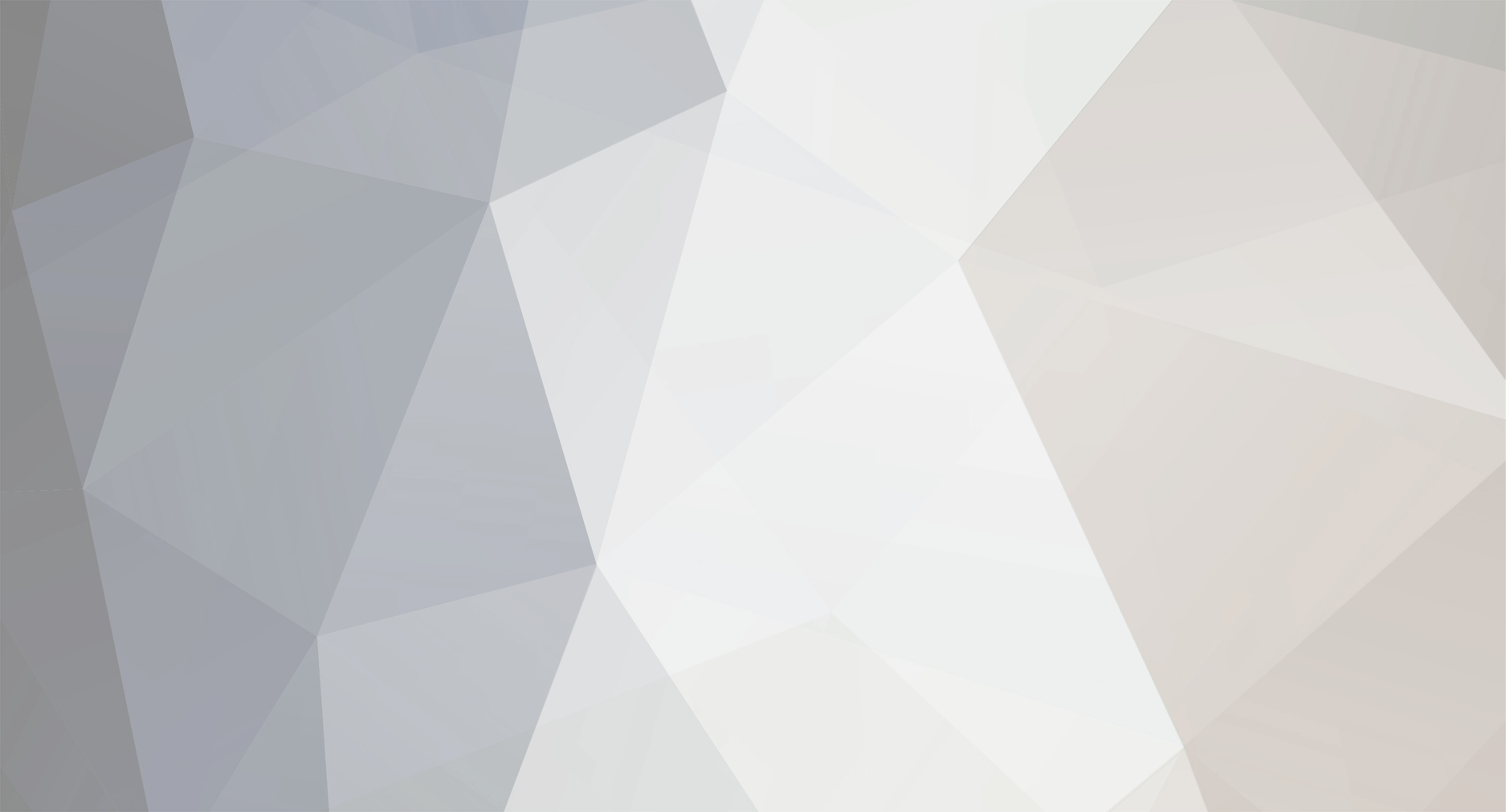
3below
Member-
Posts
2,670 -
Joined
-
Last visited
Content Type
Profiles
Forums
Events
Shop
Articles
Everything posted by 3below
-
Looking good, must get moving on mine again.
-
Keepers - G&L SB1 1986 which I traded a John Hall R* bass against and have owned it for 26+ years. I got the best deal. Second is a Kramer DMZ4001, I always wanted one when i was a student in the 70s/80s but had to make do with a new Fender P bass in 1977 (long since gone). Both basses are keepers due to the difficulty in finding equivalents again. My main playing bass these days is a Gibson SG bass. No problems with this one going, replacements are readily available.
-
[quote name='bluejay' timestamp='1474319362' post='3137168'] Here we go again with the sexist assumptions... I'm still of the opinion that a bassist whose other half is constantly complaining about instruments and gear around the house has hooked up with the wrong partner. (Yes that sentence is carefully non-gendered because it really doesn't matter which half of the couple does the complaining.) [/quote] Totally correct However if you get a fail on this, you can with time wear the resistance and complaints down. YMMV [quote name='discreet' timestamp='1474040322' post='3135229'] What, this one..? [/quote] That is not backline. It is in fact the latest on stage monitoring system. It allows you and your fellow band members to simultaneously hear and perceive the 'heft' of the bass sound. Backline, no, not at all, wherever did that idea come from.
-
[quote name='Pinball' timestamp='1474319021' post='3137163'] I would go further, I have a mixture of Chinese, Korean, Japanese and USA instruments and the quality of all is excellent. G&L's and stingrays (Ray35's) are a good example. [/quote] The Chinese Rockbass 5 stringer I owned for a while had an outstanding build and finish quality, totally on a par with my USA G&L bass and Telecaster guitar (and that is a well made one). When these well built Chinese, Korean, Indonesian etc basses are made with quality timber (ash, maple, mahogany etc as many are) what 'magic' does the name and 'Made in USA' ticket carry anymore?
-
No connection with 4 Strings at all. I will just say (from 26+ years of G&L ownership of a 1986 ish SB1) the quality of the 3 bolt bi-cut models is outstanding. I used to call it a string tester. Put strings on, tune, play put back in case. Later, open case, plug in, play (no tuning) . It just stayed (stays) in tune for many weeks.
-
[quote name='Schnozzalee' timestamp='1474311010' post='3137048'] Buy yourself a G&L. [/quote] 'Buy yourself a 'vintage' G&L'., some real value for money about. Failing that just buy used German Warwicks, quality all day long at very sensible prices. I have owned a plethora of US guitars and basses, 5 at present, I have a liking for them but now feel that far eastern and Chinese basses offer 85 - 95% of the quality at bargain basement prices, especially s/h. Quite what Fender can do to compete remains to be seen. I have seen the same with my wife's business, luxury specialist products turned into high quality, low cost 'white' consumer goods over time. Country of origin no longer matters. I no longer buy German or Swedish cars either, better value for money elsewhere.
-
[quote name='White Cloud' timestamp='1474308947' post='3137017'] Swoon - be still my beating heart. Absolutely fantastic! ...however, is there anything that I can say or do that will make you reconsider fitting the 3 point bridge??? An instrument of this quality deserves better [/quote] Retrofit of Hipshot 3 point bridge will be quite feasible. I could live with the lack of individual string adjustment on my SG bass 3 pointer. What annoyed me most was having to make and use an extender bar so that the silks stopped before the saddles. I thus went to Hipshot from this parish. Hipshot is not perfect either but I worked around that.
-
Please help me fix a route on my bass?
3below replied to DawnPatrol1990's topic in Repairs and Technical
A simple less sophisticated solution is a surface mounted plate (early Musicman Sabre style) that just sits on the back surface. No reccess needed, the plate can be large enough to hide the 'mess'. -
Basses, unlike children, pets, cars, houses, significant partners etc do not usually consume money. Seems OK to me on this basis.
-
SOLD Mighty mite P/J neck SOLD
3below replied to oldslapper's topic in Accessories & Other Musically Related Items For Sale
-
The body will look very 'classy' in natural. A good 'hidden' bonus.
-
Protruding Skunk Line on back of neck - pics added
3below replied to tonyclaret's topic in Bass Guitars
In a sort of related way, I had the Koa? truss rod plug in my USA telecaster gradually come adrift and work its way out. Pushed back in and sorted with thin CA glue. You are unlikely to have the skunk stripe coming adrift but as advised above get someone who knows to have a look. -
In my youth I had a 58 EB2, well made, serious quality but muddy. About 2 yrs ago I bought an SG bass from this parish. It has become my get to go bass with TI flats ( I have a lot of bass choice including several 'classics', Warwicks etc). The SG does Instant Jack Bruce, Andy Fraser when needed. It will also approach a DB tone. It has a thick compressed tone at low volume (think singer playing acoustic), Nothing else I own gives me 'thick, compressed, 'CD playback' bass tone at low volume. DI recording just needs mild compression. Neck like a baseball bat which suits me. Light weight and compact which suits the vertically challenged bass player (me). Now for the bad: Mild neck diver and the 3 point bridge is in need of some updating (now done on current versions and on mine). Bridge on mine was out of alignment by about 2mm - sorted with s/h supertone bridge but not really acceptable. The satin finish is 'pants', shows every mark and scuff. Once I gave it furniture wax it has become a thing of beauty. What is not to like, especially as SG basses crop up at bargain prices.
-
[quote name='Andyjr1515' timestamp='1473621876' post='3131762'] The bit where I'm a bit unconventional is that I do the final, final scraping once the bass is finished and all strung up. Then I can really feel whether it plays comfortably. [/quote] And thank you again . I can see myself doing a final scraping / fettling with the bass strung up before finishing . I am finding that my level of 'perfection' and attention to detail is increasing as the build progresses (some old skills being re-awoken). 'Top Notch' will be getting a finish approaching one of yours, you have set the bar high Andy!
-
Neck now profiled, fingerboard and headstock still to finalise. Did back of neck first as this allowed clamping against the flat fingerboard. The Fender type bolt on heel and headstock style will give a flat clamping surface when the fingerboard is radiused. I am leaving the headstock shaping until the last stage thus preventing damage by dings (my careless handling) etc. Pictures not great, should have used different camera angles. Neck profile was all done by hand: shinto, file, scraper, sanding blocks and emery cloth (the oak is so hard it just ignores sand paper). Initially I was apprehensive about profiling the neck. After watching videos / Internet research I had considered: jig(s) for router, sanding belt, sanding belt and cam jig, 3/4" radius router bit in jig or router table (yikes). I thought I would need various profile templates to get the shape correct. In the end I just got on with it by hand, after all double basses, cellos etc are all hand shaped. It was straightforward and did not take much more than an hour from start to finish. The most surprising part was that I did it all by eye and hand with only one measurement. The one measurement was to confirm what my hand was telling me, there was a slightly thick portion at one point. Measurement revealed all - 1.5mm in 26mm. It is fascinating how hand / eye coordination intuitively sharpened up as the level of detail finishing progressed. All in all I am pleasantly surprised at how easy and satisfying this stage has been. I have a neck that suits my hands, it is a "baseball bat" as planned. No mistakes today
-
Warwick Rockbass Corvette short scale. Edinburgh. £250
3below replied to solo4652's topic in eBay - Weird and Wonderful
Capo 2nd fret and tune accordingly will be the way to go then Dots will be in all the wrong places, could be interesting unless playing Jazz. -
Warwick Rockbass Corvette short scale. Edinburgh. £250
3below replied to solo4652's topic in eBay - Weird and Wonderful
[quote name='Evil Undead' timestamp='1473191733' post='3127920'] Definitely worth bearing in mind but for people limited to shorties it's not really an option. German short scales are really rare and go for a lot more when they do pop up [/quote] +1 and I would rather like a German short scale Corvette but have not seen one yet. -
The colour is funky and 'fun', will be unlikely to see many of them about. Will be interested to see the pickguard develop, I have an old Peavey Fury that needs a pickguard, another project another time....
-
Why thank you A much better day than the last time. Headstock now profiled to 15mm (allowing for smoothing) and neck bandsawn to slightly wider than template. It now starts to look like a bass neck (Photo to follow). Creeping small errors though, my laminations in the neck have ended up not being square. Again not a critical show stopper, just annoying when I get into perfection mode. I am reminded of my school woodwork lessons, 'Face, Face edge', all those lessons with a try square are flooding back. Somewhere on this journey, despite taking time to square up planer etc, check stock I have blundered (thinking about this some more I suspect I know where the issue started). Next time perfection
-
Back to it with brain now functional. . Neck template (headstock detail not finalised yet). Again found that no 4 hand plane is a thing of joy to use when smoothing down the bandsaw ripples. Router locking and depth stop fettled and now working which resulted in problem free routing of the truss rod channel. Camera makes channel look more 'off centre ' than it is. Despite care setting up it ended up about 1 mm off the centre line, not world ending though. Had to open the channel out at the adjuster end using a chisel. I even succeeded at my bete noire, chisel sharpening. Dabbed some lubricating wax on the truss rod screws. Covered rod with masking tape and clamped and glued the fingerboard on. Whether the glue fingerboard on then shape is a better approach than shape then glue remains to be seen. The Irwin clamp copies in the background are a waste of time, they worked well for about a year but now do not exert any real force. Should have bought the real thing in this case.
-
Warwick Rockbass Corvette short scale. Edinburgh. £250
3below replied to solo4652's topic in eBay - Weird and Wonderful
A very nice bass for someone, just bear in mind that German (long scale) can be purchased for £75 to £100 more. The quality on the RBs I have had in my hands has been excellent. -
Ibanez Artcore AGB is a similar looking bass. [url="http://www.ebay.co.uk/itm/Ibanez-bass-artcore-/252512669459?hash=item3acaed8f13:g:CXkAAOSw-itXs1fN"]http://www.ebay.co.uk/itm/Ibanez-bass-artcore-/252512669459?hash=item3acaed8f13:g:CXkAAOSw-itXs1fN[/url] Disclaimer: this listing has nothing to do with me at all.
-
Measure the internal dimensions of the cabinet, the port slot width, height and the shelf length and post them up on here. You can then use the modelling software WinISD and see what drivers might work. You might find nice people will come along, model some speakers for you and make suggestions about drivers and suitable port sizes.
-
Cheap tuners - good value or waste of money?
3below replied to Grangur's topic in General Discussion
[quote name='Beer of the Bass' timestamp='1472661121' post='3123048'] I've got a set of these for a bass that's waiting to be built, and they do feel like decent quality - they have less play in the gear than some of the generic cheapies. They look like they'd drop into the Westone without any modifications too. I'm not certain they're really made in Germany though, despite the stamp. Surely they would cost more? [/quote] My thought was that Warwick purchase them in bulk and thus get OEM pricing which is passed on to customers. The quality seems good and they work well enough on Warwick basses which is why I also have a set waiting to go in the current bass build. Now what can I call it that begins with W? -
Cheap tuners - good value or waste of money?
3below replied to Grangur's topic in General Discussion
I have also just bought some cheapo £6 tuners for a friend's budget 1980s acoustic. They seem ok, nothing more, better than what it has at the moment.