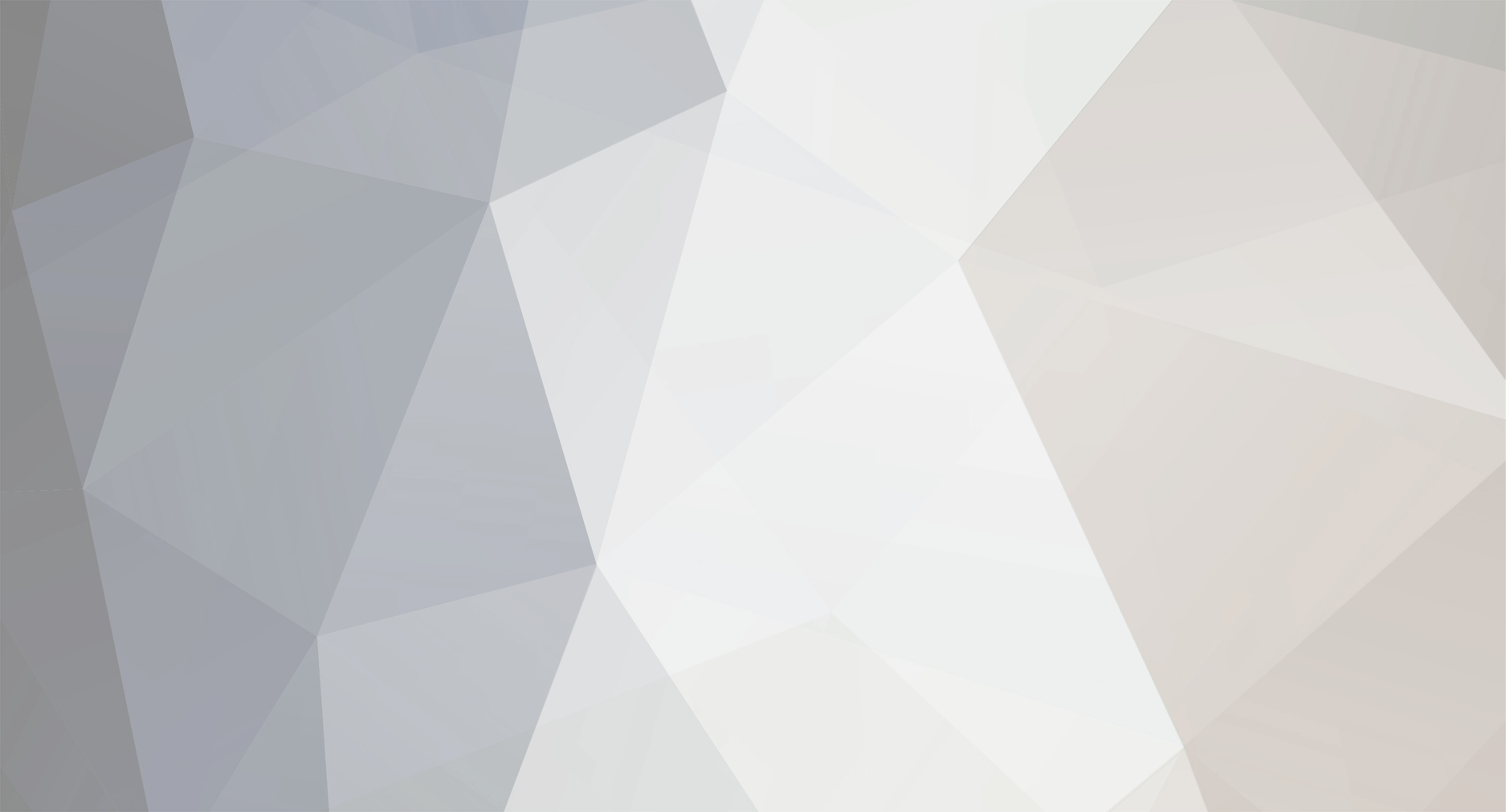
honza992
Member-
Posts
520 -
Joined
-
Last visited
-
Days Won
2
Content Type
Profiles
Forums
Events
Shop
Articles
Everything posted by honza992
-
Rocklite ebano, or at least that's the plan at the moment, but like all my builds all could change at the last second!
-
Does anyone have a guitar that has wood binding on the neck, but plastic on the body?? Does it look ok, or is it a bit odd? It's just that I'd like to do wood binding on the neck, but there's no way I can bend wood binding round the lower horn. So I was thinking maple binding on the neck and cream binding on the body. Weird?
-
Finished Pics! Psilos Phoenix Dreadnought Acoustic
honza992 replied to Andyjr1515's topic in Build Diaries
What a great technique. I love the way you come up with your own solutions, it really shows a creative mind. Bravo! Any chance I can get you to develop a similar technique for plastic binding? 'Aint no way I bend wood round the tiny lower horn of a Les Paul..... Is this the sort of thing: https://wheelspinmodels.co.uk/i/293658/?gclid=Cj0KCQjw4s7qBRCzARIsAImcAxZhpbFX0V4uRy44IL2HgQlIz022NzrqVxaxEh6Tk25hMk7RiAh--lcaAvpnEALw_wcB -
I've made a little bit more progress. First up the body. I glued on the top veneer, using the vacuum bag/wine pump. On top is a plate with air channels in that allows the air to get sucked out from all around the guitar. Like dis: Taking it out and it looks like this. Looking pretty awful☹️ But fear not. Partly that's the rubbish colour contrast thing on my phone throwing a wobbly, and partly it's bleed through from the glue. I used (West System) epoxy to glue the veneer for exactly this reason. I knew it would bleed through, but I also plan on using it for grain fill so any bleed through now is simply reducing the number of pores I need to fill later! I'm not sure if this is a recognized veneering technique, but I was worried that bleed through using a different glue (like the Titebond Cold Press) would be difficult to hide. Anyway, we'll see, my theory could be complete a_se and I'll have made splotchy lump of expensive firewood. Next up was the neck blank and scarf joint. I'm cutting a 12 degree angle and I first tried doing it on my radial arm drill (another eBay score). It was not a success. I got about half way the blade stuck and the motor cut out, luckily before doing any damage to the blank. (I should say the guard is always on before I cut anything). So having sworn a lot, I finished the cut off on the band saw then turned to my despised belt sander. The Clark 4" 6" Belt sander is like most other new stuff I've bought for the workshop. It's sh_te. Built to no tolerance at all that I can see, slop all over the place, poorly designed and sat unused for months after it was obviously not up to the original job that I bought it for. But one thing I've found is that even sh_t machines eventually have a use found for them. Sometimes unexpected ones. I now do my nuts (ahem...) on it for example and it works brilliantly. Anyway, this is how I ended up using it: I just stuck a piece of scrap to the underside of it, then hooked that against the guard that the belt sander has very helpfully got in exactly the right place. A quick bit of trigonometry on the bank of an envelope meant that the piece of scrap was stuck in the right place to give a 12 degree angle. Here's the guard in case it's not too clear: It's too early to say how successful the technique has been cos I havent glued the too halves together yet, but the angle is 12 degrees exactly and the two surfaces look pretty good. We'll see tomorrow when I glue.
-
@Christine That's interesting, I'd never noticed any difference in hardness after using the drum sander, but bear in mind I don't use hand tools at all. I have zero training and am too impatient with building guitars to learn how to use them! I'm sure I will one day, I'd love to be able to whip out a hand plane for flattening a board, but for the moment I'm taking the easy option! Also, I keep the paper clean and depth of cut very shallow, so I don't generate much heat though it is something I look out for. Exacto. Air pressure is loads strong enough for what I'm doing. It's made by these lovely people, and I really can't recommend enough, especially given the alternative is many many hundreds of pounds.. https://roarockit.co.uk/ I didint' do the neck laminates that way. I just glued it with lots of clamps in a more traditional way. Even with 9 pieces using Titebond Original is no problem, even with it's pretty short open time as long as you are oganised, pre cut all the pieces to roughly the same size and work at full speed. 😂😂 Funny you should mention that.....but actually, no! This one will get grain-filled then finished probably with a home made wiping varnish.....though that is some way off.... Thanks all for your interest😁
-
Yes so far I really like the rocklite. It seems to work very easily, and less prone to chipouts than ebony is, at least with my mediocre skills. Also I'm becoming something of an Extinction Rebellion eco-rebel, so am (very very reluctantly) using up any exotic wood I've already bought, but won't be replacing them.
-
Thanks all, so far so good. The drum sander is probably my favourite machine. It just does what it does well. I bought it on eBay for £350 as water damaged stock. And it was. It looked as though it had been standing in a swamp. But it is rock solid. I've had it for about 3 years and I've adjusted it once. A slow feed rate and a very shallow cut and it will do a marvellous job till the cows are at home, feet up, drinking cocoa. It was just one of those ebay bolts from the blue. It was cheap as chips and was 3 miles from my house. Never will that happen again. For the benefit of @Jabba_the_gut here's a photo of the beauty in its natural habitat: The vacuum bag is less impressive, but I have to say just as effective. Here it is gluing on the matching mahogany veneer headstock for a tele that is finished bar the fret levelling: So here's where I am. Both ash plates glued on. Still completely rough cut, but some lovely side grain. I'm half tempted to leave it as it is, rather than gluing on the walnut veneers..... Oh, and @Andyjr1515 you'd be really welcome. Your scarf joint expertese would be pure gold......😁
-
A little bit of progress. I've hollowed out the inside of the walnut core, drill press followed by router. I routed a wiring channel for the switch and drilled a small hole (that you can't see) that will hopefully line up with the bridge ferrule so it can be grounded. The back ash plate was already glued on when I took the photos, and the front plate is in a vacuum bag being glued on to the front as I type. I also glued together a neck blank using wood from a beautiful Walnut board I picked up at Brooks, my local builders hardwood yard in Nottingham. The board was a perfect 8" wide and about 8 feet long. It's got really beautiful grain and some flame, even if a bit hard to see in the photos. For £80 it was really a bargain. It was also almost at the top of the pile. Sods law clearly had taken a day off. Here I've glued it together as a 9 piece neck - Walnut/maple/rocklite ebano (an artifical ebony) with black & white veneer accent lines. I forgot to take any pictures of the gluing process (and anyway it's somewhat hectic), but it's really a great moment when you scrape back the dried glue to reveal a perfect striped blank. Any in my limited experience they are stable in a way that non-laminated necks never are. A gratuitous stripey shot.... (Diagonal lines are from the drum sander, not the wood)
-
Ha ha it's true. But the only way I can generate leftovers and scraps of wood to use on future builds is to buy new wood now. See? 😬🙄😂
-
Believe me I have it bookmarked!
-
Hi All It's been a while since I did a thread in real time, so I thought I'd start one for my new build. Especially since it's got some elements I've never done before - LPish, neck angle, scarf joint, set neck - so will shamelessly pump you all for information. My plan is to build a g*itar loosely based on the Gibson ES Les Paul. So it will be LP shaped, chambered, f-holes, probably P90s. Wood wise it will be mostly walnut, with figured walnut veneers front and back, double bound. I'm not looking to do a carved top yet, so it will be flat a bit like a B&G. Like a B&G I'm also thinking of having a slotted headstock and tailpiece. So imagine these two had a love child.... Here's a wood pile, and a neck blank I've already made. I'm trying to use wood that I've accumulated for no particular use, or that is left over from something else. So far I've got: - A one piece walnut body. It's too thin, so I've jointed some ash plates to be glued on front and back, just to bring the body up to 44mm or so. They'll be hidden by the binding & veneer. - Some walnut veneer, for front and back. The body will be double bound, probably in ivoroid. - A 9 piece neck blank - (fake) ebony/maple/sapele. I made this for something else then never used it. I'm a bit in two minds whether to run with this one or to make another one with walnut rather than the sapele. Given everything else is walnut, I think the slightly orangy sapele may clash, colour wise. So if I can nip down to Brooks to buy some rough cut walnut, I may glue up another multi-laminate neck with walnut rather than sapele. Here are the veneer sheets: And doing some very rough layout on the walnut core, just for fun. Thanks for looking!
- 119 replies
-
- 11
-
-
Thanks all, some good stuff for me to look up. I love biarnel and Wood & Tronics, and lots of others I hadn't come across so I appreciate all of your posts! Any amateur builders in Tuscany/Liguria? @Silvia Bluejay She's from Massa Carrara, so Tuscan, though we may head up into Liguria. Chiavari is a possiblity.....Where are you from? If you can ignore the politics and the bureaucracy (and that's a pretty big if), then Italy has lots going for it. They really do like children there. In restaurants the neighbouring tables will actually talk to Natasha (who's 3 and needs no encouragement), rather than just put up with her as mostly they do here. The waiters will happy whisk her away to go and meet the chef leaving you alone for a precious 5 minutes without a tiny person asking 'why' repeatedly..... I've got one starting this very day! 😁 There's a bit of time before we go....like ummm 6 months....so I shall shamelssly keep stealing Basschat communal knowedge before unleashing it on the unsuspecting Italians..... HH, today has been record breaking, but when I mention that to Mrs Honza she looks at me witheringly then says she's cold and can I find her jumper. Honestly, it's as though we are biologically different animals....
-
Alembic neck laminates. I laughed till I cried....
honza992 replied to honza992's topic in Build Diaries
Hee hee, I knew this was a can of worms! @chris_b I'm sure no one here would claim to be better at making guitars than Alembic, I know I'm not, fact. But we are definitely more honest in the marketing of the guitars we do make. Physics, unfortunately, is not something you can have an opinion about. It simply is. (Well, maybe at a sub-atomic level, but even Alembic don't make claims about that). The body and neck of an electric guitar simply provide two anchor points (the nut and the bridge) for the string to vibrate between. I'm not claiming wood doesn't effect sound, it does. I'm pretty sure a guitar with a solid ebony neck would sound slightly different to a balsa wood neck. More or less its a matter of how 'floppy' the neck is. A more floppy neck absorbs the strings' higher frequency vibrations and slows the attack, that would make sense to Isaac Newton. So if you make a neck from multiple veneers it will still have one 'floppiness' value, but Alembic claim that by adding in different veneers into the neck construction you can add in particular sound characteristics. Add in mahogany for upper mids, ebony for lows, etc etc. Cosmetically it sounds like an appealing theory, but I'm pretty sure it's wrong. But then I did A Level physics 30 years ago, so what do I know. Any PhD'ers out there that can give a definitive view? -
I'm designing my next build and thinking about what laminates to use for the neck. This page makes me laugh every time I visit. It's like a salad bar for choosing upper mids or crushing lows. I know I'm not supposed to knock the legendary builders, but this is utter rubbish. In my opinion of course😁 http://www.alembic.com/info/wood_neck.html
-
My other half is Italian. But as happens to all Italians who have been here for more than a few years, the lack of sun has finally defeated her. She likes the UK, she even likes us, for God's sake, but she simply can't understand how any country can have such consistently dreary weather. She can't accept that it's possible to go through all of July and two thirds of August before you get a decent day of sunshine. I've tried to introduce her to the joy of a deserted, wind-swept Welsh beach, 15 degrees in summer and sand in your sandwiches, but I'm afraid she just doesn't get it. So long story short we're moving to Italy, most likely at the beginning of next year. So I was wondering if there are any Italian builders out there? We're probably going to be in Tuscany/Liguria, somewhere between Pisa and Genoa. Ciao for now!
-
That's really worked out beautifully. There's quite a dramatic difference between the rough cut top and the final photo you've got. Did Jon spill any beans about whether he had dyed it, or what finish he used? That's going to look top shelf.
-
Sorry for the derail, but @Jabba_the_gut was there are build thread for the sycamore/wenge/LED bass? That is outstanding!!
-
Finished Pics! Psilos Phoenix Dreadnought Acoustic
honza992 replied to Andyjr1515's topic in Build Diaries
Brilliant work, very elegantly done. Pro instruments, for pro players. Top man. -
Quick follow up if you don't mind. For grain fill I've been reading about microballons, do you use them, or just neat?
-
OK, that's interesting that you say it's easier to sand. I'll give it a go. Just out of interest, do you use the 5 or 30 minute? And do you sand back to bare wood? Really appreciate the info!
-
The back is one piece walnut.....
-
All, thanks so much for your comments. This one took a long time to finish, especially the finish😬, so it means a great deal to me that you like it..👏👏 @Manton Customs Thanks for advice re grain fill. And yes, it's really annoying that something like Aquacoat is marketed in that way. I've tried it multiple times using different application techniques, and never get anything other than rubbish results. And it 'ain't cheap..... Thanks for the advice re Zpoxy. I've tried West Sytems (which I use a lot for gluing) in the past with varied results. I should probably give it another go. @Unknown_User Grain fill is one of the those things that sounds easy, but most people seem to find pretty difficult. As far as I understand it, the basic options are: 1. Sand and slurry with truoil or similar. This works pretty well in my experience, but is messy. Ideal if you are using truoil as a topcoat. I'm not sure how compatible it is with other finishes. I think @Andyjr1515 uses it under oil based varnish, and I use waterbased polyurethane over tru oil when I am burying my logos. 2. Paste filler like Stewmac's Colortone (waterbased) or Rustin's Grain filler (oil based). I've tried both and not had great luck with either. I never seem to be able to sand back to a smooth finish while keeping the gunk in the pores. But this is probably the most used grain fill technique. 3. Epoxy. I've tried West Systems in the past, and @Manton Customs uses zpoxy, I imagine they're very similar. I'll probably return to this next time. Epoxies are two part and you need to be careful that your ratios are correct otherwise curing can be a problem. West System I've never had a failure with, but I have with Araldite and another one (forgetten the name though), and I'm pretty careful to measure everything out as accurately as I can. Assuming you've got the ratios right, it also dries rock hard so you want to get as much off the surface of the wood otherwise sanding flat is a right pain. 4. Endless other options - egg whites, shellac, etc etc etc Like all of guitar building, you probably need to go through a few of these to see what works for you. I'm still searching for the easy and failsafe answer to grainfill. If I find it, I'll ket you know. And by next year I'll be a millionaire......
-
I'm not sure whether anyone is interested, but I've just finished a guitar with a brushed nitrocellulose lacquer finish. I always swore that I'd never use nitro - too poisenous both for me and the planet. However, a friend asked me to make them a Tele using a beautiful piece of flamed spalted maple, and nitro was the only finish that worked. Polyurethane, oil and CA glue turned the test pieces into a dull splodgy brown mess, not exactly the look I was going for. Nitro though brought out all the beautiful colours and let the flame really sing. Here's the piece of wood before I started.... Although I do spray waterbased polyurethane, there's no way I can spray nitro so I thought I'd try brushing it on. The internet though had almost no information about whether it was possible to brush it on, how to do it, or what the results would look like. So, hopefully this thread will help you decide if you want to do it. It is definitely not an easy option, but.....let me get up some finished pics, and you could decide whether it was worth it. This is what I used: This is Rothko & Frost's standard gloss nitro that they sell neat, ie not in aerosol. This was a 250ml bottle and I used the whole thing plus a bit more on the body. I brushed it on with an artist's brush, a trick I stole from @Andyjr1515. You need to make sure that it's a brush for oil paints, with natural bristles, otherwise the solvents can melt them. I used a Daler Rowney Bristlewhite hog hair fan brush, size 4 (though a size 6 might have made life a bit easier). They are comically long so I cut mine to a more manageable length. Schedule was something like this: 1. Sand to 220 2. Grain fill with Aqua Coat 3. Ignore the fact that the grain fill was pretty poor and crack on with finishing (john, john, john, will you never learn?🙄) 4. Brush on R&K Nitro, thinned with 30% R&K cellulose thinners, probaly about 10 coats. 5. Curse myself repeatedly for failing to grain fill properly. I've made enough guitars to know that preparation is everything, and if you want a smooth finish grain fill is critical. Impatience though sometimes clouds my already pretty poor judgement 5. Wet sand with Wet/Dry paper (water with a drop of Murphy's oil soap) with 600 grit. 6. Another unknown number of coats. It felt like hundreds, but was probably another 5 or so. 7. Wet sand 1000 grit 8. 'wet' sand with Gerlitz Carnauba wax on a piece of Mirka Abralon 1000 grit. This left exactly the satin sheen I was after. I found the key was to brush the nitro on in one stroke, never go back over somewhere you've just painted. Because the nitro dissolves the layer before, I found the brush would start 'sticking' as it got caught in the previous layer. My approach was to do lots and lots of layers, knowing that I would have to go back and wet sand quite a lot of it off to get it completely flat. In reality, because my grain fill was....well, shite.....I had to do many many more layers than I otherwise would have had to have done. If I ever do this again, I'm hoping that 10 layers in total would be enough, assuming a flat surface to begin with. I lay the guitar flat on a 'lazy susan' turntable, did the top and the sides at the start of the day then turned it over and did the back and sides. Would I do it again? Ummm....yes, and no. Yes, if the wood was crying out for nitro, as this piece was. I'd be a bit reluctant to do it again on an entire guitar body though. Even though it was brushed rather than sprayed, the fumes were still pretty bad, and I wore a proper mask with organic filters at all times. On a guitar with a binding like this one, next time I'd probably brush the top with nitro, as above, but do the rest of the body with something else, tru oil probably. The binding would provide a natural break between the two finishes, so the two finishes wouldn't ever touch. And on a flat surface like a guitar top (rather than the fiddly curved inner horns) you could whizz through the process in no time. It's worth mentioning that the Rothko & Frost nitro specifically says it is not suitable for brushing, though I'm not quite sure why, as far as I could tell it went on perfectly nicely. The process also used much less nitro than you would get through if spraying (I think). With a proper grain fill I'm pretty sure I could do a whole body with one 250ml bottle. An aerosol contains about 150ml of nitro, so I used probably the equivalent of two aerosols worth. I've never finished a guitar with rattlecans, but I'm pretty sure it would be many more than that. So all in all I'm pleased with the result (but the next one is going to be Danish Oil, which I can do on the kitchen table😂😁). And some photos.....
- 25 replies
-
- 21
-
-
33" Reverse P/J Jazz bass, blocks & binding (FINISHED PICS)
honza992 replied to honza992's topic in Build Diaries
Thanks everyone, really appreciate your positive comments! It really does make the heartache and frustration worthwhile..... @Andyjr1515 Andy give me a shout if you want to talk turbines....If I had my time again I wouldn't have what I have now..... -
33" Reverse P/J Jazz bass, blocks & binding (FINISHED PICS)
honza992 replied to honza992's topic in Build Diaries
Finally, my work here is done. It was the normal story for me, woodwork went more (or less) smoothly, finishing was a nightmare. Anyway, at third attempt I am very, very, very happy with how it's turned out. I really like the 33" scale - with careful positioning of the bridge the overall reach is probably 2 inches less than a standard Fender 34". The weight is just under 8 lbs, so very light for a jazz, but the balance is absolutely perfect - it sits naturally about 30 degrees above horizontal. The finish is like double cream, silky smooth, really incredibly smooth, but matte at the same time. It really makes you want to touch it....or even...no enough. Get on with the specs....... Scale: 33" Shape: Slightly undersized Jazz Body wood: Alder (no weight relief) Neck wood: Maple, flatsawn Fretboard: Rosewood Pickups: House of Tone '62 PJ set, installed with the P pickup reversed Electronics: Passive, 500k pots Tuners: Ultralites Bridge: Wilkinson Other: Mother of Pearl Blocks, white plastic binding Weight: 7lb 14oz (3.65kg) Balance: Absolutely spot on Colour: Vintage White (1:2 General Finshes Snow White & Antique White) Finish: General Finishes High Performance clear coat, sprayed with HVLP Strings: D'Addario XL Nickel wound 45-105 Other than for the purposes of set up, I haven't really had the chance to play it yet. I like to get proper photos does immediately (before I drop it), then I just haven't had the chance. First impressions though are very very positive, particularly of the P pickup, which sounds massive! More dets to follow. Anyway, here are some studio shots..... And a few I took at home....- 130 replies
-
- 12
-