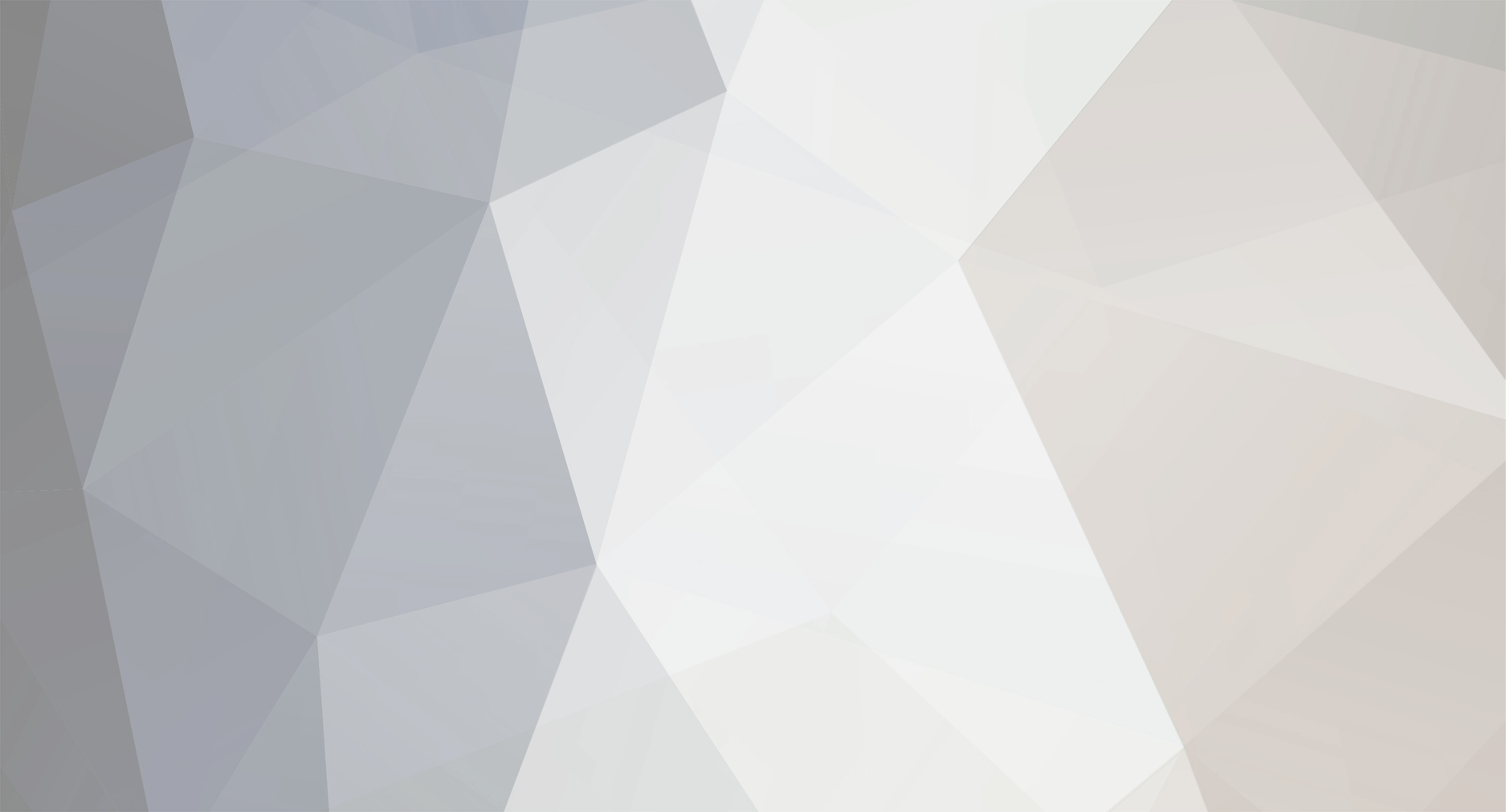
honza992
Member-
Posts
520 -
Joined
-
Last visited
-
Days Won
2
Content Type
Profiles
Forums
Events
Shop
Articles
Everything posted by honza992
-
Thanks for posting this, really interested to see how you do your finishing. I've been following your progress elsewhere for a while, your results are outstanding. I really love your holistic approach to design, your instruments have a coherence that is rare to find. Really great work. So am I right that the process is: 1. Solid grey primer 2. Clear coats with gold pearl mixed in 3. Clear coats with candy apple (in your case made up using Bloodshot and Mile High candy) So the only solid 'colour', is the grey primer. The rest of the colour is provided by the candies mixed in with the clear coats? Can't wait to see the end result.
-
33" Reverse P/J Jazz bass, blocks & binding (FINISHED PICS)
honza992 replied to honza992's topic in Build Diaries
Finally, an update. The neck is finished, tru-oil slurried and currently waiting overnight for the water slide decal to dry before sparying some poly over the top of the logo to bury it. Tomorrow, hopefully. The body is mid-finish. I brushed on a few coats coats of General Finishes High Performance to act as a sanding sealer - providing a flat surface for the colour - which will be a (hopefully) beautiful creamy white. I'm using 1/3 Antique White and 2/3 Snow White, both (fake) milk paints from General Finishes. They're basically just a low gloss acrylic (no lactose involved) paint, but they spray nicely and are completely compatible with the High Performance, which I'll also use as the top coat. I spray using an HVLP turbine, but I turn the pressure down really really low. Being an HVLP I don't have a pressure guage, but my guess it's only running at 1/3 or so of it's capacity - basically just enough to 'flop' the paint out of the gun in big gobs and onto the surface - it'll flatten itself nicely as the water evapourates. I've found that increasing the air flow simply fills the air with clouds of vapourised paint that bounces off the surface, but doesn't improve the quality at all, but does make me nervous about what i'm breathing in, even with a full mask. Here are a couple of coats: -
My methdodology for the neck was roughly the same as the body. Here's a completely rubbish photo: Necks are really hard to photo, but the tru oil finish came out really really nicely. It has a great clarity to the finish and gives enough colour to really warm it up with a nice amber tone, but without going over the top. I hate those necks that look like they've been covered in fake tan. The finish is very very smooth but with none of the 'squeakyness' that you get with gloss finishes which I hate. I think this may well now be my go-to neck finish. It's really hard to fault. The process was as follows: 1. Sand to 400. 2. Two seal coats, 24 hours apart, wiped on with cotton rag. 3. Slurry sanding using either wet/dry paper or Abralon pads (I had a mixture of grits), sanding with the grain. Wiping off really carefully with kitchen paper. Grits were 400, 600, 800 & 1000, 24 hrs apart. The last couple of grits you have to be really careful to wipe off the excess pretty quickly (no more than a few minutes max) and make sure you get all of it off, or you'll get ridges that are impossbile to sand away with the higher grits. And that was it. Because maple is closed grain wood, the whole process is much much quicker than the body as no grain fill was necessary. For my logo I waited 7 days for the Tru Oil to be really dry then I applied a water-slide decal - I get mine from Rothko & Frost, they are really expensive but worth it. The paper they use is very thin and can be buried in many fewer coats than previously when I've used decals I've printed myself on paper bought off t'internet. Once the logo was on, I waited overnight for it to dry then sprayed 4 coats of General Finishes High Performance top coat, which is a water based polyurethane. GFHP works really well being sprayed over Tru Oil (in the past I've finished entire necks in this way). I think I did them all in one day, then the next day I lightly dry- sanded with 1000 and then 1500 Abralon. I taped off round the face of the headstock, so the join (ie where the polyurethane started) was right on the roundover. Because GFHP is crystal clear, it's really hard to tell that the face of the headstock isn't finished in exactly the same way as the rest of the neck. Again, this is now my standard finishing procedure for headstocks & logos. As you can see, the finish is consistent with the rest of the neck, and no lines at all round the edge of the logo: Finally, a quick word about the fretboard, which was a lovely piece of pau ferro: I've started doing all of my fretboard finishing before fretting. Trying to do anything once the frets are in is really really hard, almost impossible to get a consistent finish. So for this one I sanded to 1000 before fretting, then applied 3 coats of Liberon Finishing Oil, just wiping on with a rag, once per day. I used this rather than Tru Oil mostly because it's a lot thinner, which allows it to sink down really easily into the quite open grain. It's a lovely combination of browns, reds and oranges that is brought to life by an oil finish. And that's it. A Tru Oil guitar, apart from the fretboard done with Liberon Finishing Oil, and a polyurethan clear top coat to hide the logo. Job done.
-
He he thanks very much๐
-
Finally I manage to update this thread. Albeit I'm going to cut it into a few different posts. I'll cover the body first, then the neck in another post. I took the guitar home and took a couple of photos in natural light coming in through the window. By some bizarre, never-to-be-repeated, quirk of fate, Nottingham wasn't grey and overcast. This is what the Tru Oil finish looks like in natural light, really nice colour and chatoyance: I would describe the finish as being a high satin, or very low gloss. I'm sure it could be polished to a much higher gloss, but it's not the look I was after. It's 90% grain filled, meaning it feels incredibly smooth and shiny, but has a tiny bit of texture to it. It's lush! I could have gone for a complete grain fill...but again, not the look I was after. There's definitely a time and a place for a dipped-in-glass type high-gloss finish (Mmmm....sadowsky), but not when I was asked to create a Bruce Springsteen inspired guitar. Anyway, here's the lustre: Here's my finishing schedule. 1. Sand to 400, 600 on the end grain. Obviously, sanding is critical. All scratches have to be gone otherwise they get amplified by the oil. The end grain is always difficult, especially on baseball-bat ash (which this was). Wetting the body with a sponge helps identify scratches (and raises the grain prior to finishing) as does going outside into natural light where the scratches are easier to see. 2. Seal the wood. I applied two coats of Tru Oil using a cotton rag. There's no science to this bit. Squirt some oil on the rag or the guitar then rub it in. I wiped off any excess after 5 minutes. I did this twice, 24 hours apart. 3. Grain fill using the slurry method. Using wet/dry paper on the back of a sanding block (a bit of scrap MDF) I sanded with the grain using Tru Oil as the lubricant. I know other people sand in circles (including the chap who made the video above, and his results look great) but that just makes me nervous - I don't ever like sanding other than with the grain. The idea is that the sanding dust/slurry gets trapped in the grain. I found that sanding with the grain, then using my finger to 'swirl' the slurry around worked well, and there was no danger of visible sanding scratches (which is the danger when using a circular motion). I found the best way was to divide the body up into sections and move from one section to the next (the top for example I would divide into 4), rather than trying to do the whole thing in one go. You then want to wipe across the grain to get rid of the excess. You do want to make sure you wipe off all the excess, otherwise you find that you end up with ridges or streaks, which can then be hard to sand away when you move up to the finer grits. If you are anythnig like me you'll find it a pretty messy business - always dripping down the sides, or onto the top you've just wiped, and onto your work surface which then get's smudged onto you newly wiped guitar top etc etc. None of which is a problem, just wipe. I wiped off with standard kitchen paper. Keep lots and lots to hand. I repeated this process twice, both times using 400 wet/dry and seperated by 24 hrs. I found that his filled the grain to a bout 90%, which was the look I was after. A third time would probably have been enough to get the grain completely filled, if you were wanting a completely smooth surface on which to build a high gloss finish. I found the slurry was very happy to stay in the grain, wiping with the kitchen paper took the oil off the surface but leaving the grain nicely filled. 3. Smoothing. I find it usefull to seperate in my head the process of grain fill, and sanding smooth. The process is much the same as above - using wet/dry paper on a sanding block, sanding with the grain then throroughly wiping off the excess. I did the following grits: 600, 800, 1000, 1200, 1500, 2000. It was really at 1500 where there was a sudden change in lustre, from what I would call satin to a low gloss. The great thing about tru oil is that you really just keep going until either your arms fall off, or you've got the appearance you want. It is quite a physical process - from 800 and above I would vigorously rub off the excess oil (again, in the direction of the grain), pressing hard to generate a tiny bit of heat. I did only one grit per day, but I'm told doing 2 per day is no problem. Another thing I tried was using Mirka Abralon sanding pads rather than wet/dry paper. It worked really well, and was definitely less messy as the oil gets absorved into the foam of the pad. It did, though, use a lot more oil. I'm not sure the effect was any different though, both worked just as well. I left it at that, ie my last coast was sanded with 2000 grit. For a higher gloss (without buffing) I understand you can just apply a very thin coat with a cotton rag as your final coat. I didin't as I liked the finish as it was. 4. Waiting.......I wait at least a week before putting the guitar together. I think Tru Oil takes that long to harden sufficiently. Overall, I'm very happy with how it turned out. Using Tru Oil on ash is not an easy option. Then again, ash is never an easy option whatever the finish you're using, the grain is just so open. But if you don't want to spray then it's a finish you can apply on the kitchen table. Just make sure that you have wiped away every trace of oil at the end of each session or you'll have to go back down the grits to get out the ridges. I'll go through the process for the neck tomorrow. Cheers all. And thanks very much to @Andyjr1515 for his help and advice re Tru Oil (amongst many other things!)
-
https://www.guitarbuild.co.uk/collections/bass-bodies/pb-body+swamp-ash?sort_by= (no affiliation, but I have bought from them before)
-
I wish I knew how to cut those partial fretlines. They look great and dont detract from the beauty of the ebony in the way that full fretlines might. Anyone know what the technique is?
-
Sorry, I thought I was actually going to post something about how to you know, apply tru oil. Unfortunately my worst nightmare has come true. My wife is ill..... For the father of a 2 year old they are the four most frightening words in the English language. And at the weekend when nursery is closed. I may not make it till Monday.....
-
Neck carving - what do you use and how do you do it?
honza992 replied to honza992's topic in Build Diaries
Ha Ha ha! Brilliant. I should be on commission. Post your thoughts here as to whether you like it. For me it's the neck transitions when it really shines. -
Was it this one? There's no doubt he gets a great result, though tru oil is a lot easier on closed grain wood like walnut than it is on ash. Having said that the back of his also looks great, and it does look like Ash. Either he's done an outstanding job of grainfill (in which case I'd love to know how) or the back is a really nice piece of alder. Either way, it looks great.
-
Hi All I thought I'd do a thread about an (almost) completely Tru-oil finished guitar. I've gone through lots of different finishing options that aren't nitro - waterbased, oils, wax varnishes etc, with varying degrees of success. This one though, is definitely a success, and it;s also one you can do with absolutely no equipment, other than a bottle of tru oil, some sandpaper and opposing thumbs....I know there are lots of builders who can't spray for whatever reason (neighbours, the spouse, exploding extraction etc) so I think in the right circumstances Tru oil is a good option. I should point out that much of my success with using Tru oil comes from our very own @Andyjr1515 who was kind enough to share his knowledge and techniques with me. Mine are largely based on his. I thought I'd show you all a guitar I've just finished for a friend. He wanted a Springsteen inspired tele. Not a copy, just something in that ball park. So I made this.... The pictures in all honesty don't really do it justice. It's still at the workshop at the moment, but if I have time over the weekend I'll bring it home to take some shots in natural light, that's when the oil finish really comes alive. I'll go through the process in some detail, so bear with me......
- 62 replies
-
- 12
-
-
Finished Pics! Dreadnought acoustic (guitar) for me?
honza992 replied to Andyjr1515's topic in Build Diaries
Lovely job,beautiful work. -
33" Reverse P/J Jazz bass, blocks & binding (FINISHED PICS)
honza992 replied to honza992's topic in Build Diaries
I've just weighed all the parts and I think final weight will be about 3.4kg (7.5lb). Perfect. -
33" Reverse P/J Jazz bass, blocks & binding (FINISHED PICS)
honza992 replied to honza992's topic in Build Diaries
I'm deep into the neck carve at the moment. This time I'm doing it slightly different to my normal method. Only slightly differently, mind, and if you look away you;ll not notice. But, this time I have cut my facets only as far as the start of the transitions like this....(rather than trying to cut facets through the transitions, if you see what I mean). And I sanded the bulk of the neck to 90% of the finished shape before starting work on the transitions. It's worked out really well. Having the neck virtually finished meant I could 'feel' the transitions more clearly somehow. I should finish the carve tomorrow and I'll post some pictures.... -
33" Reverse P/J Jazz bass, blocks & binding (FINISHED PICS)
honza992 replied to honza992's topic in Build Diaries
Ha ha, yes the pain and suffering is definitely a feature of guitar building. In fact, the more my skills grow the more I realise that guitar building is, like tennis, mostly about avoiding unforced errors. The lapse in concentration, the inexplicable routing using a template that's upside down, drilling too deep, or too shallow, or not at all, not checking fret slot depth etc etx..... I've done them all. Several times. New swear words have been invented. The occasional infantile tantrum. But as @SpondonBassed says, it's inevitable and you just have to rely on your skills or improvisation! -
33" Reverse P/J Jazz bass, blocks & binding (FINISHED PICS)
honza992 replied to honza992's topic in Build Diaries
I haven't actually routed the pickguard itself yet, I won't do that till the last minute. The one's I've done before though have been no problem, no melting, though I do turn the router down to a slower speed. -
Finished Pics! Dreadnought acoustic (guitar) for me?
honza992 replied to Andyjr1515's topic in Build Diaries
Thanks Andy, really really useful info. I've heard of eggwhites being used before but only ever on accoustic guitars. Very interesting. Yet another technique for me to try at some point! -
Neck carving - what do you use and how do you do it?
honza992 replied to honza992's topic in Build Diaries
Oh sh_t๐ฒ I didn't realise there were so many. And all so.... beautiful ๐. That's great @Jabba_the_gut. Yeah, really thanks for that. Like I need more tool GAS.... ๐ -
Hi All I'm just starting the neck carve on my current build, and I noticed that the tools I use has completely changed over my last few builds. I started using rasps and files, mostly a dragon file sold (at great expense๐ฒ) by Stewmac. Recently, though, I've started using one of these, an iwasaki carvers file. It was actually the first file I ever owned, bought on the recommendation of some random poster on some random guitar forum. I remember being singularly unimpressed when I tried to use it, too unpreditable and niggly to use, and it sank down onto the bottom shelf. For this build I dug it out to give it another go, and my god it rocks. It's not like using a file where you file harder to take off more, in any direction, any speed. This needs a much more subtle touch. The angle you use it, the pressure you apply and the direction of the grain all make a huge difference to the effect it has. It can go from taking off massive amounts of wood with little effort, to almost burnishing a completely smooth finish. It really is a remarkable tool. And while not cheap at ยฃ20, it's a joy to use. I use the facet method of neck carving, and previously I've always used a spokeshave to smooth down each facet before moving onto the next one. With the Iwasaki there's really no point. It leaves a surfacce plenty smooth enough. It does though, need a careful touch. If you apply too much pressure at the wrong time it can dig in but if you're careful it really does a great job in a very rewarding way. I just thought I would share! I'd love to hear what anyone else uses, and what method you use. If you don't use the facet method what do you do?
-
33" Reverse P/J Jazz bass, blocks & binding (FINISHED PICS)
honza992 replied to honza992's topic in Build Diaries
Into the grunt work. I re-did the frets. Cursing as I went ๐. Though to be fair, all went smoothly. I then filed them level with the edge of the neck, then added the bevel, taking it down slightly into the binding so there isn't too sharp an edge. I then did the neck taper, going from 20mm at the first to 22mm at the 12th. Slim, but not too slim. It's then on to the neck carve. I use the facet method, which makes for a lovely photo! Oh, and the body needs sanding. Lots and lots of sanding. But is at least looking more or less bass shaped. -
33" Reverse P/J Jazz bass, blocks & binding (FINISHED PICS)
honza992 replied to honza992's topic in Build Diaries
Sounds strange, but in some ways I think making the pickguard is the most difficult thing about building an electric. Unlike wood, plastic is completely unforgiving, and there's something about it that means you really have to be accurate for it to look good. It has to follow exactly the curve of the body, fit exactly round the neck pocket and have exact placement of the pickups and control plate. I've finally got a process that I'm pretty happy with, but it's taken me a long time to develop it, and it still takes a long time to do. Of course, if you're doing a standard size P or J bass then you can simply pick one off the shelf, or use a pre-made template like I've got in the first photo. Everything I do is custom size, so no such luxury for me. First up I do a drawing on some baking parchment (one of the most useful things in the 'shop). I use this to rough cut some 12mm mdf to size. Next I rout the pickup hole into it. At this point the rest of the pickguard template is just rough cut. Having got the pickup rout done, I mount the pickups and make sure that I'm happy with their positioning. Then without moving anything, I use a guided bit running along the edge of the body itself to do the lower horn (where the pickguard runs parallel with the body). At the same time I also rout the neck pocket, using the pocket itself as a guide. This means that the fit of the pickguard is perfect. I then use a guided router bit with different size bearings to rebate into the pickguard template along the lower horn. This results in a template that is smaller than the lower horn, but runs parallel to it. Finally, I cut out the 'V' shape where the pickguard meets the control plate. And that's it! Several hours work. My last insurance policy is that I don't drill the holes for the control plate till after finishing and I'm fitting the plastic pickguard itself. The positioning of the control plate has a couple of mm wiggle room, so if the thickness of the finish, or who knows what else has moved everthing by a mm or so, I can absorb that by moving the control plate slightly, and everthing still fits together perfectly. I told you it was the hardest bit of making a guitar! -
33" Reverse P/J Jazz bass, blocks & binding (FINISHED PICS)
honza992 replied to honza992's topic in Build Diaries
Sometimes I really despair. Last week when I was lying on my (2 yr old) daughters floor as she held my finger to go to sleep, I specifically remember thinking to myself, Honza don't forget to check that the fret slots are deep enough before you glue the binding and start fretting. Well...I didn't, and they weren't. Even more annoyingly (and for the first time ever, what was I thinking) I started fretting from the nut end rather than the heel end. Which meant the first dozen or so went in perfectly before they started bottoming out. So to cut a long story short I had to take them all out.... Pulled 'em out with this... There was virtually no tearout, apart from one small chip near the end. I used a feeler guage and some baking paper as a dam to stop the CA medium glue getting into the fret slot. Ended up being virtually invisible. Then I deepened the slots using this teeny tiny saw. All in all it went pretty smoothly, but I wasn't expecting to have to do a re-fret quite so soon๐. I'm going to have a whiteboard surgically attached to my forehead so when I have these thoughts in the middle of the night, I don't immediately forget them in the excitement and impatience of building.... I've re-sanded the fretboard and it looks pretty good. I just need to put on a few layers of finish then I can re-fret. But can someone please remind me to remember the things I have forgotten. Thanks. -
Finished Pics! Dreadnought acoustic (guitar) for me?
honza992 replied to Andyjr1515's topic in Build Diaries
Can't wait for the finishing de-brief ๐ It's amazing that man-on-the-moon is almost half a century old, but there's still no recognized method of sealing, protecting and enhancing the grain of a piece of wood.... Andy, you're doing great work. -
Guitar build.co.uk can do whatever you need. Edit: Ah, sorry do you mean you want a guitar shaped lump of wood? Or a finished guitar minus neck, knobs and control plate? If the first then guitarbuild are good, if the latter then ebay or gumtree is your friend. Buy a cheap bass body and most sellers will throw in the neck for free๐ ๐
-
33" Reverse P/J Jazz bass, blocks & binding (FINISHED PICS)
honza992 replied to honza992's topic in Build Diaries
The body is now nearly finished. The arm/belly contours are done. I filled in the old pickup rout, and re-did it for a reverse P. I spent ages cutting out paper control plates of different shapes (including the Sandberg style suggested by @songofthewind , which look great) but just couldn't get anything I was happy with. Because of it's location (nearer the bridge) there wasn't much contour to it, which meant it just ended up mostly looking like a not-very-happy penis. And I'm not sure that's exactly the look I was after ๐. So in the end I simply decided to re-shape the body so that it followed the shape of the control plate, rather than the other way round. I think it's ended up looking pretty good. I also did drilled the holes for the pickup and bridge ground wires. Because the bass is going to be painted, the easiest way to do the bridge ground was just to drill through the side of the bass. I don't have a bit anywhere long enough to drill all the way through from the bridge pocket. One thing I forgot is that those long bits drop, so by the time it came out into the control cavity it was worryingly near the bottom. Luckily there were a few mm to spare, and I may fill the bottom with a bit of epoxy just to make sure it remains strong enough. Tomorrow, fretting and doing the roundovers on the body.....