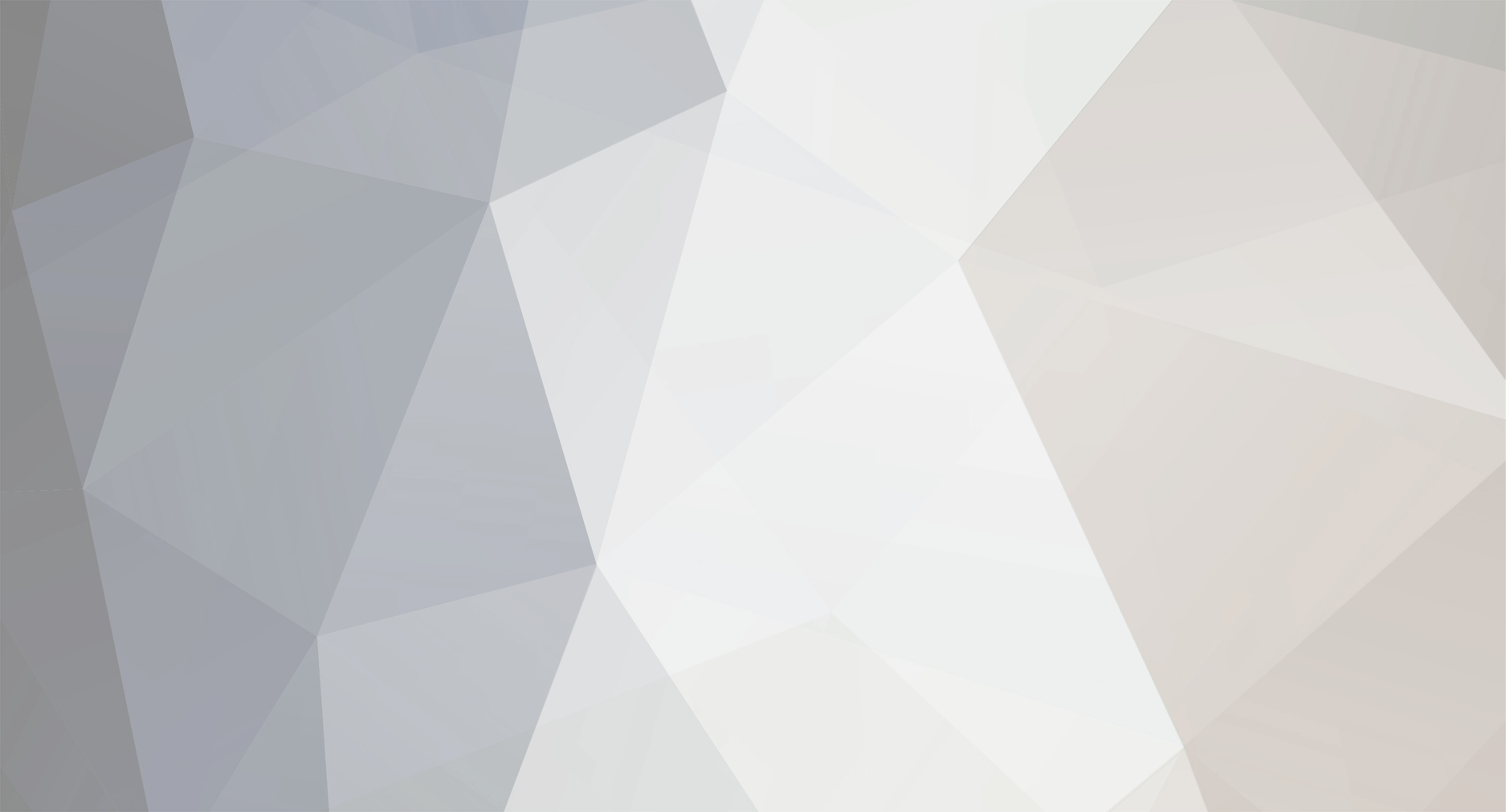
honza992
Member-
Posts
520 -
Joined
-
Last visited
-
Days Won
2
Content Type
Profiles
Forums
Events
Shop
Articles
Everything posted by honza992
-
Andy, thanks so much for posting this. A radius jig is next on my list of things to build, once I finish the two work tables, the work bench, wood rack....oh and the unfinished guitar and bass that keep on looking at me making me feel guilty. But sanding radii is pretty much my least favourite part of a build, so I shall be re-visiting this thread shortly, compass and stubby pencil in hand.....
-
Thanks for that! At the moment it's also sitting unfinished in a case. Nothing major, but the electronics need finalising, it needs a string retainer, and a couple of imperfections in the finish need sorting. I finally got to the point where the mess and chaos in the workshop was sapping my motivation - the endless tripping up over power leads, dragging a shop vac around from one machine to another, the endless looking for stuff! So, I am in the middle of completely re-organising, getting power and extraction to every machine, assigning everything it's true and proper home from which it will never move (honest guv, I'll be tidy in the future). And building a new table, workbench and shelving. This will be finished in January, I promise. Probably....... Merry xmas to you all, see you in the New Year. Basschat is without question the friendliest place on the 'net
-
And here come the professionals! Yes, nice elegant simple solution. Why is it that those are always the sort that elude me? Thanks Jabba, That certainly sounds like the most straight forward way of doing it. Any idea if a couple of standard 6, 8, or 10mm dowels would be enough to hold that much tension?
-
SB, we are as one, very beautiful, mind......
-
OK, time to share a slight setback with you all. When I was designing this bass I had always imagined a 'floating' bridge, held in place by bridge tension. I thought this would solve the intonation problem - you could slide the bridge around till you got the ideal position. What I've found though is that because it's a string-through, and because I've got the bridge so near the edge of the body (to help with balance) the angle at which the strings cut over the bridge means that they are 'pusing' the bridge towards the neck. And as you bring the strings up to tension the bridge is pushed out of it's correct position, meaning the intonation is shot. I've even tried clamping it down as I tune up but again the bridge just moves as soon as you loosen the clamps. Looking at the design, it's now pretty obvious that this would be a problem. So, I think I've got three solutions. 1. Drill holes in the bridge and screw it down as you would any other bridge - I'm sure this would work fine, but the though of drilling holes in my beautiful bridge is not filling me with joy. Not my preferred option. 2. Glue the bridge down. Hmmm.....I'm not sure about this. I'd need to strip the finish first from the top, though that in itself isn't a problem. I'm just not sure I love the idea of permanently attaching the bridge. Possible though. 3. Rout an indentation into which the bridge would sit. I'm thinking it would only need to be a couple of mm deep, just enough to stop the bridge moving. Rob Allen sinks his bridge into the top, as does Jerzy Drozd. So I've been experimenting to see whether I can make a template accurate enough that everyone doesn't laugh and point at the gaps round the edge. Watch this space. Does anyone have any observations? Advice?
-
Ha ha, very good. One of my favourites, actually (albeit Madman Across the Water is better). It's a shame Sir EJ has become a parady of himself. Like Rod Stewart. Both of their first few albums are fantastic, and almost completely overlooked now. And the quality of their backing bands is also incredible. Puts 99% of modern music to shame...... Of course anything produced by either of them in the last 30 years makes me want to retch, but there you go. I'm a fickle bugger.
-
I've got a Cafe Walter PZP1 in there, which was designed specifically for the Fender AE, of which this is a copy. It may be time for me to check my wiring!
-
Ok I finally managed to get round to looking at the piezo issue. It turned out to be two things. First the bottom of the saddle wasn't flat and second the saddle was a bit tight in the slot. Once I was tuning up to full tension the break angle of the strings over the saddle was forcing the saddle sideways into the wall of the bridge, meaning it then wasn't transferring the strings vibrations effectively to the piezo elements. Again a bit of sanding the sides of the saddle and that finally gave me all four strings sounding at equal volume. Less pleasing is the sound itself which is a bit nasally. Goddam! I noticed though that the bridge itself is not sitting flat on the top and I wonder if that is affecting the bass response. So I've sanded it flat and then.....ran out of time So tomorrow I'll string it up again and see if that's helped...... Fingers crossed.
-
Thanks guys, I'm really pleased you like the bass. I've put it aside for a week or so for the finish to properly cure then I'll get some real photos done. The mahogany at the back has also come out nice!
-
Ok here's a teaser photo. Proper ones will follow....
-
Sub 7lbs is definitely do-able (and I realise that is not your goal!), though I would say only with ultralites. My fretless build I'm doing here on Basschat is basically what you are suggesting, ie a P bass build with chambering and an f-hole. I haven't weighed it yet, but my guess is it will be 6lb6oz pounds, 2.9kg. Thats a maple top and mahogany body so probably fairly similar to swamp ash in terms of the overall weight of the wood. Overall thickness is 39mm. I've got a wooden bridge which will save a bit of weight and there's no magnetic pickup. The balance is perfect, though I've designed it so the strap pin is level with approx fret 10 and it's a 33" scale. The lightest 34" scale bass I've ever done was a 2.4kg (5lb5oz) chambered 'f-holed' P bass. That had a standard fender style metal bridge and P pickup. The body wood was horse chesnut though (or at least I think it was, my memory is atrocious, ditto my record keeping) which was very very light. Although the bass was ridiculously light it wasn't really a success. Even with the bridge close to the edge of the body and with Ultralite tuners the balance was still a touch neck heavy. That made it much less comfortable that the one I'm just finishing. In my book balance is more important that absolute weight. 7lb and perfect balance is ideal for me. Looking forward to seeing the build!
-
Finished Pics! To the dark side Build One - Alembic-esque Electric
honza992 replied to Andyjr1515's topic in Build Diaries
Really really nice Andy. Hats off -
Well the woodworkery type stuff is done. FInish is finished, as in my experience it isn't wont to do. So I strung her up, connected the wires, decided on the red pill then plugged it in. And there was noise. Beautiful noise Or at least there was from the E string. Nothing at all however from either A or D string, and only a bit from the G. Now I'm the sort of player where even one and a half sounding strings is probably overkill, but purely for academic interest I should try to get the other two and a half strings up and running. I literally wired, stringed and plugged it in about 20 seconds as I was late picking up the little one from nursery (and they charge one pound per minute, yes one pound per minute if you are late) so I may well have missed something obvious, but I couldn't wait till next week to see if anything was going to come out at all. My instinct is that the difference in output between the strings is due to the bone saddle not being flat on the bottom. That or I guess the bottom of the channel in the bridge may not be flat, but that was routed in one go so that seems less likely. The transducer itself is one similar to this: So it looks as though it's got seperate sensors for each string. Whether it actually has or not is a different matter. If anyone has got any immediate pearls of wisdom I'd love to have them. As I said it was a bit of a rush job so I may be missing something obvious. I'll take a more leisurely look next week. And THEN you'll get the some photos. Promise.
-
Photos? Of course. Without those none of this ever happened.......
-
The bridge turned out nice didn't it! Finish is, well, umm, finished. Bit of curing time than string it up and ride it out......
-
Thanks all for the advice re dust. Tried all in the end, so there....was....no....dust.... And this one has not long gestation left. The body needs one or maybe two more coats of osmo. The water slide decal is on and buried on the headstock, so the neck just needs a couple more coats (of General Finishes HP) then it's electronics and out kicking and screaming into the world! Happy days Oh, and Honza. Please be careful. Don't drop it. Don't drop anything on it. Like that Brad Point. Step away very slowly.........
-
Man this thread has slowed to a snail's pace....first Foot & Mouth, then flu, then this, then that....aghhhh very frustrating. Anyway, I'm ready to start finishing. I've sanded the mahogany body till I can sand no more. This is what it looks like: The observant of you will notice the light coloured flecks of the grain. My question is whether this is sanding dust which needs to be blown out, or whether it's just the grain pattern. I've vacuumed it with the shop vac but I don't have a compressor to try blowing it out (if indeed there is anything to blow out). A guy in one of the next door workshops has got a big old compressor but isn't here for a few days. What do think? Is it dust (and I should be less impatient and wait for Mr Compressor's return) or am I being paranoid, just get some oil on there Honza.....
-
OK the body is sanded to 400 so time for some fini... No, bugger. I forgot about shielding the cavity. Best do it now cos I'll only drop the brush onto the top or something . I haven't used this paint before, but it needs 3 coats with 24hrs in between. What? 3 days!?! It's only a guitar, not a lightening rod.....nevermind, in the meantime I can finish sanding the neck (or start on the tele! )
-
[quote name='Si600' timestamp='1508927371' post='3395360'] They hated your suggestion of building a non-standard Tele didn't they [/quote] He he they were certainly none too keen! It's strange, were I on here or Talkbass and talking about making modifications to the P bass design no one would think anything of it. I thought I would get two replies each telling me I can do whatever I like. Instead of which it was 10 pages of.....well anyway, it was an experience.
-
Finished Pics! To the dark side Build One - Alembic-esque Electric
honza992 replied to Andyjr1515's topic in Build Diaries
[quote name='Andyjr1515' timestamp='1508775843' post='3394337'] Not terribly sure I'd get a banana either For what it's worth, I use a fine flat needlenose and also a triangular one where I've ground one of the apexes smooth. With the flat blade I round it from the fret through 90 deg to the fretboard edge and then with the triangular one, with the smooth edge in the corner between the fret-end and the fretboard wood first take off the sharp edge on one side and then round to the fret apex, then the same on the other side. If any of that makes any sense! [/quote] I've bookmarked this technique to come back to in the future. Very swish, as we would have said in the 80s. -
I don't know if any of you are interested in those six string toy things (ok, I know you are!), but I've started my next build thread here: http://www.tdpri.com/threads/shifted-bridge-short-scale-tele.776185/ It's a Tele, so I sort of thougt that was the obvious place for it!
-
I need to drill holes for the knobs and the jack and then very very final sanding and we're done! Finish will be Osmo Raw on the top and standard Osmo on the mahogany. The neck will be sprayed with General Finishes HP Satin, and kept very thin. Now that sounds easy doesn't it Dear Gods of Finishing, please look kindly on me, your faithful servant.....
-
[quote name='SpondonBassed' timestamp='1508570592' post='3392967'] Calm down, calm down. I understand your frustration. I was puzzled by this too. It is of no relevance to what you are doing and if you overthink it like I did once, you may be at risk of a minor stroke. The reason you noticed it from what you've said is that, in this instance, you did not slacken the string before moving the saddle. In my humble bumblings I say that is better practice to detune until the tension is enough to retain the string but not enough to cause much static friction between saddle and string. Static friction being greater than dynamic friction, you will find fine adjustment to the saddle is facilitated when you reduce the tension of the string because you wont get that sudden release and overshoot when the bridge starts to move. Without going into Applied Mathematics, that's as simple as I can put it. On standard bridges, if you keep the string at tuning tension, there is the additional risk of bending the longer grub screws in the saddles or damaging the finish beneath the screws as they are dragged by the string length adjustment. For those reasons it would be counter-intuitive to keep string tension on standard bridges during fine adjustment. Of course, on a standard bridge you also have string height to consider every time you change the string length. Have you any provision for that on yours or are you aiming to file the boney bit (saddle-nut?) to a final height for your chosen strings? The unexpected phenomenon that you're describing is worthy of a topic all of its own... if anyone wants to take the job? Maybe a BC masterclass on bridge and saddle placement has been done already. When we have the migration behind us the forum search engine might throw up some improved results from our older topics. [/quote] Minor stroke indeed! But, it's done and the holes are drilled. I've over-sized them to give a few mm in either direction of travel in case I want to change string height in the future. I think the final intonation figures ended up being something like +6mm for the D string and +9mm for the E string. It's a bit more than I imagined, maybe because of the shorter scale For string height, adjustments are a question of either sanding down the bone saddle (from the bottom using sandpaper on a flat surface) or sanding down the bottom of the bridge itself. Raising the action....I guess options would range from adding a shim to the bottom of the saddle, making a new saddle, adding a shim to the neck pocket, routing the neck pocket slightly deeper....let's cross that bridge when hopefully I don't come to it.... A quick question. When the bone saddle arrived it was a beautiful white colour, presumably from bleaching. As I've sanded it it's turned into a cream colour that actually matches the binding pretty well. However, it's also got brown/grey staining on it, which I guess is the natural colour of the bone. Does anyone have any experiencing of bleaching bone? Ideally I'd like to keep it cream colour but without the brown staining. If I decide to bleach it any idea how to do it? Bucket, bleach, meet bone? Is there more to it? Cheers all.
-
Doubt has set in again Sorry, but are these two statements not contradictory? [quote name='fftc' timestamp='1508529783' post='3392856'] If you move the saddle back then you increase the break angle and the string tension. The relationship between the anchor point and the saddle will determine whether the increase in string length (lower pitch) will overcome the increase in tension (higher pitch). [/quote] I feel as though what you're saying here is that break angle affects intonation. Clearly as I move from the secondary bridge in the jig to through-the-body stringing, the break angle will be significantly increased. [quote name='fftc' timestamp='1508529783' post='3392856'] [color=#282828][font=helvetica, arial, sans-serif][size=3]Intonation should be limited to strictly what happens between the nut and the saddle[/size][/font][/color] [/quote] But here you seem to be saying that break angle doesn't affect intonation. Not tryng to be rude, honest! Im just trying to get my tiny brain to understand what for most people is no doubt obvious.....
-
[quote name='fftc' timestamp='1508529783' post='3392856'] On a conventional bridge the string breaks over the saddle and goes down to the anchor point. If you move the saddle back then you increase the break angle and the string tension. The relationship between the anchor point and the saddle will determine whether the increase in string length (lower pitch) will overcome the increase in tension (higher pitch). There is a lot of discussion between guitar owners (Les Pauls specifically) about break angle and how to set your stop tailpiece for the best feeling. The theory is that a lesser break angle will feel 'slinkier' than a higher break angle. This is while tuned to pitch, so the tension is the same. Apparently there is proper physics to explain this but I can't remember it or understand it! Intonation should be limited to strictly what happens between the nut and the saddle, so your secondary bridge shouldn't affect that adjustment, even if it would affect string feel. [/quote] Great, thanks fftc. I feel warmly reassured.