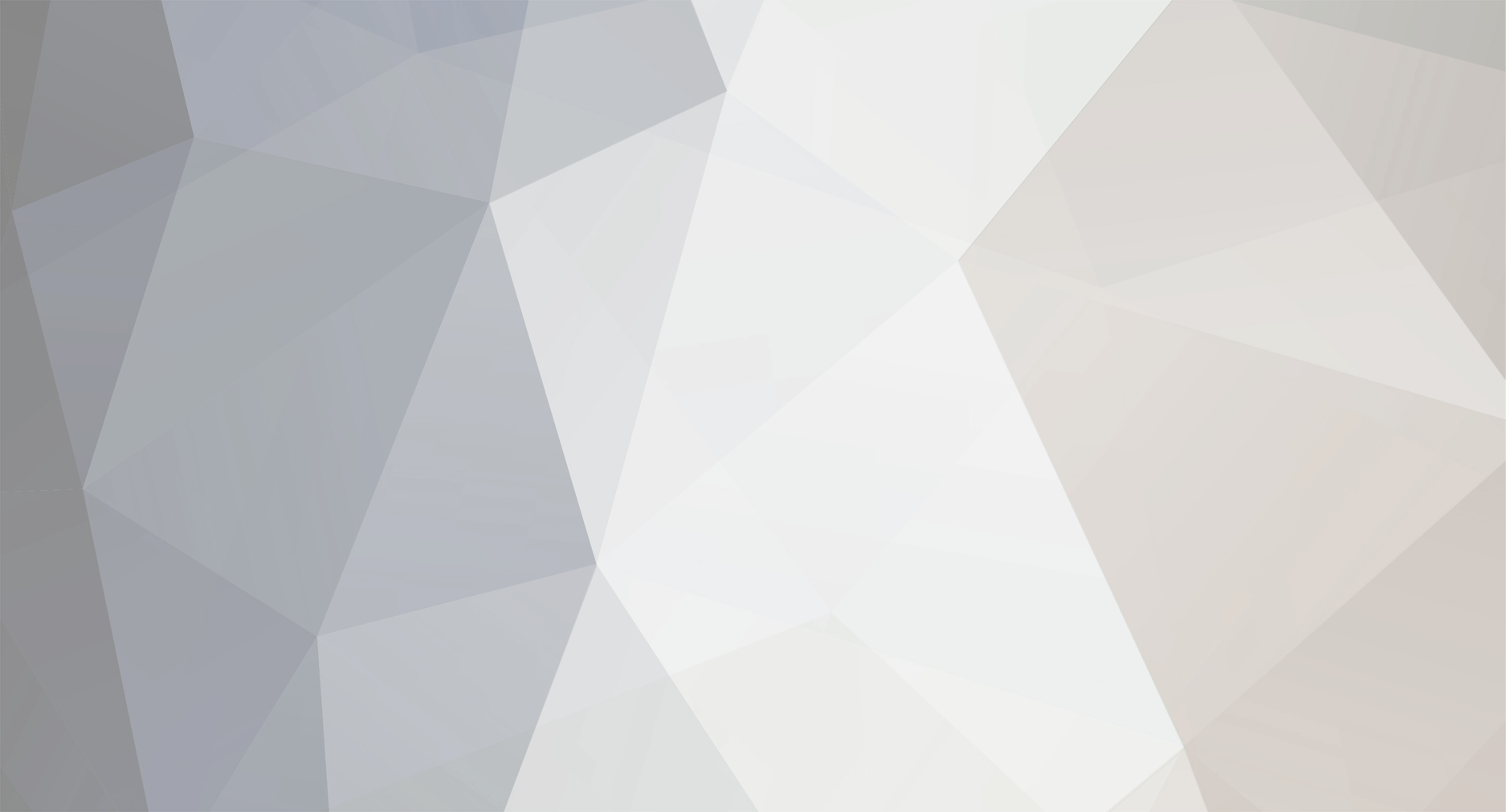
honza992
Member-
Posts
520 -
Joined
-
Last visited
-
Days Won
2
Content Type
Profiles
Forums
Events
Shop
Articles
Everything posted by honza992
-
A quick look at the back and side together. Nice.....
-
True that. I've got unlimited respect for anyone that does this only using hand tools. Those are subtle skills that are long in the making!
-
Thanks @LowB_FTW and @AndyTravis. Guitar building is a solitary sport, so company is always appreciated. Apologies that all this is coming in one go. Daily updates would obviously be better, but come cocoa time I'm shattered.... Anyway, up next is side bending. My experience of guitar building is that it's mostly one bum clenching task after another. Each one perfectly capable of taking your expensive 'tonewood' and turning it into kindling with frightening speed. Side bending is definitely one of those tasks. I'm doing it now because I bollocks it up and have to throw the sides away, it also means any work I do on the back is also wasted (since they have to match). So get the bending done now...... I use a bending iron and do it by hand. Ha! Man do take some sh_t photos. No wonder my Instagram followers all share the same surname as me. Some guitar makers take photos and videos that are so beautiful it makes me weep, grown man or not. Me on the other hand, bam! have a bending iron. Slightly out of focus, teetering on the edge of my table. Random other junk lying round. No context, no action, adding no value, other than using up a tiny amount of the planets finite resources...I blame my cheap android phone. Every time i pick it up it makes me long for my old Canon D40 (or even my Canon AV1).... Anyway, learning to bend sides by hand has been really satisfying. I take it slowly, going back to the guitar mold often to check the fit like this: That's what I call a nice fit And done. One side anyway, sleeping happily in the mold. If I get the chance I'll do the other one over the weekend or monday. The cutaway side. The difficult one......
-
I’m not quite sure why, but next I made the kerfing. It’s not the obvious next step, but there you go. Making kerfiing is pretty tedious. And mostly pointless. You can buy a guitar’s worth pre-made for about a tenner. You can’t though buy flamed maple kerfing which is why I make my own. Bugger me it’s boring though. I cut the blank using a radial arm saw. Each. slot. Cut. one. At. a time…. I then cut the blank into four strips, then onto the router table where they get tidied up and the round over added till they end up looking like this: Job done! Was it worth it? For something that probably only I will ever see? No clearly not. Just buy the bloody stuff, John, for god's sake. (Kerfing, if you don't know provides more gluing surface for when you glue on the back and top. Here the last one with the kerfing glued in, waiting for the back to be glued:)
-
First job is gluing the back together. To get an invisible glue line the joint has to be pretty perfect. The best way I’ve found is using a hand plane. For any plane nerds out there, up till now I’ve used a number 4. I’ve just bought a number 6 though which is joy to use, and nearly as long as the back itself. You can see it here with a single shaving it’s taken off from the entire length of the board Joining the two boards together I used the ‘tape method’, which is the easiest clamping technique ever - raise one edge of one board off the table and put tape across the join. Add glue, then put both pieces flat and the tape pulls the boards together. Here it is taped, already glued:
-
Hi all The acoustic bass I’ve just finished is such a success that I’m going straight into building another, albeit this next one is a bit more complicated - the top will be carved from solid wood to create the arch,rather than being a thin piece of wood pushed into an arch by the braces, as the last one was. I’m already a couple of days into building, but just in case anyone is interested, I’ll show the process from the beginning. First up, a pile of wood: (apologies for the washed-out pics, my phone takes terrible pictures, I must get a proper camera) For the top, Italian spruce. Back & Sides - Italian walnut Neck - multi laminate, flame maple and walnut Everything else we’ll work out as we go. But fretboard will probably be crelicam ebony….
-
Should exactly this tragic chain of events befall poor @Frank Blank, you better have a pretty solid alibi to hand....But yes, under those limited set of circumstances, it's yours.
-
Yep, instinctively I feel as though phosphor bronze isn't right. But it's probably worth at least giving them a go. And Chromes could be a good choice. Even the 40-95s are significantly higher tension than tapewounds though. And until it's been strung up a while with something lower tension, the additional tension of the Chromes worries me a bit. But it wouldn't surprise me at all if they aren't the final choice. Or La Bella Flats as @Frank Blank suggests. I think I've got some Deep talkin tapewounds - does anyone know if they have blue silks?
-
Ha ha hold your horses! Did I mention the feedback? Wait for the full rundown before you send me the monopoly money🤣 But thanks for the compliment, it really means a lot.
-
Strings - if anyone wants to chime in with string suggestions, that would be great. I've tried some D'Addario black tapewounds, and Thomastik TI Jazz flats, and I think I prefer the TIs. I need to buy some phosphor bronze to give those a try as well. The scale length is 31.25 inches, but because of the tailpiece, standard 34" strings fit on perfectly.
-
The finishing is ...finished. This is 100% prototype, so I've not too worried about imperfections. Both the french polish and the Osmo I think have worked nicely. I'll do a proper write up on the finishes another day. There's still a bit more setup to do. Albeit with only a tiny amount of curve in the neck there's no fret buzz, so I may not bother fret levelling, they're level enough already. And the neck joint I designed to have shims inserted to dial in the correct bridge height, but again it's pretty much spot, none needed. There was a lot of new stuff for me in this build, including a pretty complicated neck joint, so to have the geometry all line up is really satisfying. The nut and saddle need work, and there's a bit of tidying here and there, but mostly it's done. I'll try taking some proper photos not under the clinical lights of the workshop, but here it is warts n all:
- 50 replies
-
- 13
-
-
Shellac and french polishing is such a joy. No drama, no drips and a low gloss finish is achievable very quickly. This is 6 very relaxing sessions of 20 minutes. I skipped the 'polishing' part of french polishing and I'm leaving it like this. Assuming the guitar doesn't explode once I've strung it up, I may go back and polish it up to get it high gloss.....
-
Ummm...yes, it was me🙄 With my fingernail. What a numpty. The Osmo definitely goes on soft to begin with. I think I remember this from last time. It does get hard, but is takes a couple of weeks. I should try steaming it out.
-
Fair comment. Even i had to go looking for it...And given my real worry is that the top explodes 3 days after stringing i t up, scratching the back hardly even registers. 😟 I like it. The old turn a mistake into a feature routine. Nice.
-
Bugger, just scratched it. That's it, it's going for firewood... 🤣
-
Thanks Andy, you've got a nice looking pair yourself! The one on the left is obviously acoustic, but the Yamaha? I don't think I've seen particular model before. Semi-acoustic? If you don't mind can I ask what you like about the ABG thing? What's the sound in your head that an ABG helps you with? Are you after a double bass sound? Or something else completely?
-
Thanks Richard, I appreciate it! The real test will be to see if the top collapses once it's been at tension for a while.... I fumbled my way through the electronics today. It's my least favourite part. It's got a K&K Pure piezo glued on the inside of the top and a 2 band EQ by EMG. Not complicated but my tiny brain blue screens whenever I start reading about impedence and resistance and potentiometers.....
-
Hi Andy, on the body I haven't grain-fllled so my goal is a low satin finish at most. I've used Osmo Polyx gloss, on the body and the neck. On the body I think it's gone ok, I'm a bit less convinced by the neck. But I haven't quite finished, so I'll do a full report once I have. The bridge & tailpiece are unfinished ebony. I've just done a quick test using Dartfords Spirit wood dye (which sounds pretty similar to the Fiebings you mentioned, both alcohol based dyes) using mostly black with the a little bit of brown added in. The ebony definitely has some brown in it. I think they match ok. Once it's dry tomorrow I'll do some light sanding, then put some Osmo on it and see what happens....
-
I also want to have a finger rest/pickguard thing that you get on archtops. The bridge is ebony but I get more and more uncomfortable using exotic woods, so I wondered about using some nice figured maple, then ebonising it. Which I guess means dying it black. Here's the maple. Does anyone know anything about dying wood? Any idea how deep the dye goes? Deep enough to sand I would guess? I was also going to bind it, which means scraping off glue once it's glued. The binding will be wood, so dying after gluing the binding isn't an option....I don't thnk. Any idea what sort of dye? The Americans sites talk about using a leather dye, no idea if you can get that in Italy. Anyone with any ideas or pointers?
-
While the finish is finishng, I made a bridge....
-
Others with more knowledge of Poly/nitro will I'm sure offer more help, but Osmo definitely won't work. It bonds to the wood itself and isn't a film forming finish. There are film-forming oil finishes, eg Truoil, but I've got doubts it would bond to poly....
-
OK, the body and neck are ready for finish. This is the plan... Spruce top - sand to 600, then wipe on a seal coat of West Systems Epoxy, wipe off after 15 mins. I'll then french polish with shellac. I got this from Ken Parker (who does the most detailed instructional vids ever which are amazing) who does epoxy then Tru oil. I quite like french polishing though..... Body - sand to 400, then Osmo 1101 (which is the thinned version), followed by Osmo Polyx rubbed on. Neck - sand to 1000, then Osmo 1101/ Polyx. That's the plan, how it will actually turn out is anyone's guess. I have a history of applying a finish, sanding it off, applying a finish, sandi.....well you get the idea.
-
Thanks Andy. Having no workshop for several years has meant this one has literally been planned to death!
-
Thanks SB. Note to self, must take some volute pics....
-
Thanks BigRed. It's good to be here! Good question, I don't exactly know the answer. The body is 60mm at the heel, and 55mm at the neck join. So it's definitely thicker than a standard electric (45mm ish), but not dramatically so. I think the limitation probably doesn't relate to the top/pickup, more the neck joint. 55mm probably isn't enough for a dovetail joint, so I've gone for a mortise & tenon variation. Another thing about a thin body is that although I can get my hand in the sound hole, the body isn't wide enough to do anything once it's in there - the braces get n the way. So the neck bolts need to be done from the outside. I don't think body thickness will affect the amplified tone though. Acoustic volume yes, amplified tone no.