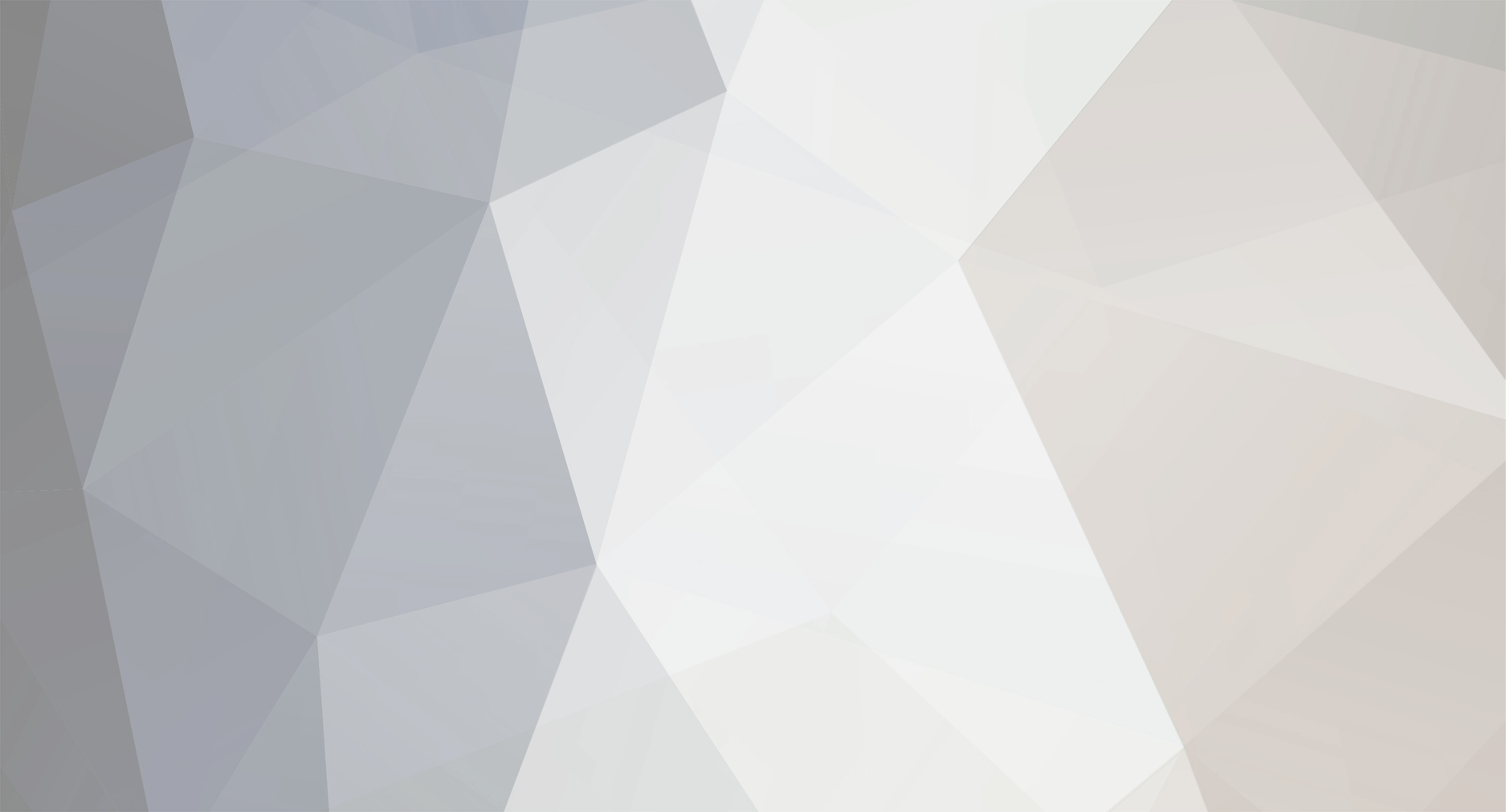
honza992
Member-
Posts
520 -
Joined
-
Last visited
-
Days Won
2
Content Type
Profiles
Forums
Events
Shop
Articles
Everything posted by honza992
-
Hey that's come out really nice. I like it a lot😁
-
Plexiglass ramp/thumbrest/faux top thingymajiggy.
honza992 replied to Maude's topic in Build Diaries
They look really great! Could I ask how you cut the plexiglass? Whenever I've tried it either melts or gums up the blade... -
Here's the logo... I must admit, I can't imagine I could cut MOP with that level of accuracy😮
-
Thanks for that. I understand for metalwork that might make sense, but for woodwork?!? Does anyone routinely ream holes in wood? Frankly it's bloody annoying. Ferrules are another pain. I use them on all my builds with neck bolts. But they are 6mm wide. And drill bits 5.9.... It would make more sense if you could choose either to buy drill bits that were actually the size they say they are, or smaller ones designed for use with a reamer. Ah well, first world problem I realise.....
-
I got quite a bit done on the neck today. First up I glued in the MOP position markers. Sounds easy but is actually tricky. Getting them all centred and looking equally spaced between the fret slots takes some practice. It's made more complicated by the fact that they also aren't accurately sized. Some are well over 6mm... Others less.... The smaller ones are spot on. The biggers ones I put to one side. The problem is that a 6mm drill bit isn't actually 6mm in diameter, it's more like 5.9. So if you try and put a 6.1mm dot in a 5.9mm hole you run the risk of either it getting stuck and not all the way in, or cracking it. If anyone knows why drill bits are consistently manufactured small than their nominal size, I'd be interested to know. The next problem is one I should have thought about before it happened, but I'm pretty ditzy most of the time. The fretboard get thinner as you reach the end of the neck because it's radiused and tapered. When I cut the slot for the binding by the time I reached the end of the neck it was almost 7mm deep, a good 1mm deeper than the binding. So I had to make an extra tall piece of binding by gluing two pieces together. It worked out pretty invisibly, but next time I need to remember to cut the binding slot so that it's a consistent depth. This is what I mean: I did the binding mitres on my belt sander then glued them to the fretboard using CA glue. I haven't used this technique before, but I think it worked well. Basically you tape the binding in place then use water-thin CA glue with a mini pipette to wick the glue down into the join. It has the advantage that you can dry cut all the mitres etc and get everything just right, tape it all into place then casually apply the glue. It's certainly a stress free technique. I'd thought about using it for the body, but I was a bit nervous about the CA glue getting into the veneer and causing blotchness under the finishing. Given how easy it was though, next time I may use it for the body as well. Here I'm wicking the glue in: The great thing about CA glue is that it takes almost no time to cure so I started to trim it back flush with a scraper. Nice shavings! Tomorrow I'll get it all scraped back flush, and hopefully finish sanding the fretboard.
-
OK I'm finally back in the workshop after some time in Italy trying to find somewhere to live, and some time in a police cell courtesy of Extinction Rebellion. I've finally got round to gluing on the fretboard. I've started using these spring clamps more and more. They seem to offer plenty of clamping force when used en masse, but are much quicker and easier to use than G or F clamps, generally less sliding around etc. Because the 'jaws' are moveable you can also easily clamp a fretboard which has already been radiused without having to used a radiused caul. Invisible glue lines are something I get a bit obsessive about (albeit on this build they'll be hidden by binding anyway) so was glad to see a very clean join once I trimmed the fretboard to size.
-
R&K can't do it. They say the MOP will just snap or burn when cut when doing a logo like mine....
-
I've emailed R&K to get some advice. I think the problem may be that the resolution for MOP is 0.8mm, which seems pretty coarse. Pearloid is 0.3mm which seems a bit more plausible.....
-
Hmm.....it's a nice idea, and I've seen the great job that you've done with MOP....I've got some scrap, I'll give it a go, albeit presumably a coping saw is required....
-
Great, let me know😀
-
I've checked them already, they don't......
-
As the title really, does anyone know where to get laser cut Mother of Pearl logos done?
-
Finished Pics! Psilos Phoenix Dreadnought Acoustic
honza992 replied to Andyjr1515's topic in Build Diaries
Yes, of course, I'd forgotten about the curvature. Makes sense😁 -
Finished Pics! Psilos Phoenix Dreadnought Acoustic
honza992 replied to Andyjr1515's topic in Build Diaries
Andy is there a reason you don't use your router to cut binding channels? I know I'm a believer in using ridiculous horsepower for even the smallest jobs (cutting binding on a radial arm saw...😂) but it does make for a very clean channel, and I'm not sure it's any less dangerous than using a low powered dremel and pushing it to the limit of what it can do..... -
I'm sure my tables aren't what you're after (useless for anything bigger than a bass), but behind is a board into which I've glued those little super strong magnets. I put all of the things I use every day so that they are right there. It works brilliantly, everything is held really securely, even the file and the heavy straight edge. It may not be pretty, but it is simple and works really really well. The screwdrivers just live in holes, and the endless rolls of tape live on a piece of off-cut plastic piping.
-
Oooohhh benches😍😍......looooovely.....
-
Ha ha, yes I know what you mean....It'll have MOP fret dots.....but hmmmm.....I was going to do a gold transfer logo but maybe there's room for some MOP as well...Now you've got me thinking.....
-
Phew, the headstock binding is done. It's not perfect, but I'm pretty happy. I also routed the truss rod access cover. Still a bit of tidying up to do, but I think it's time (finally) to glue on the fretboard.....
-
Thats great, thanks Christine. I'll have another go tomorrow.
-
@Christine would you be able to give me some advice on binding the headstock? My first attempt was ok, but I'm hoping I can do better so I routed it off for another go. Here it is... The binding is rocklite ebano with an extra 0.5mm strip of maple veneer on the inside. On the body I glued them at the same time using titebond. It was fine, if very fiddly. What would be your advice about how to bind it and in what order would you glue the pieces on? Would you try and do it all in one go, or glue some first and let it dry so that one half of each mitre joint has got something solid to push up against, if that makes sense. Would you do mitre joints for all of them, or butt joints at the end of the curves? Also, would you try and glue in the maple veneer seperate first? Thanks so much.
-
Believe me, I've thought of it! But I think I've decided to leave them unbound so the white/black/white in the scarf joint is reflected in the headstock slots.....though it was a bit of a battle with my natural inclination to bind everything in sight. Mrs Honza is a bit bored of it......🙄
-
Unfortunately I've just glued binding on to the headstock so some of those lines will get covered up😮 Luckily I'm adding in 3 new sets of lines with the binding😀
-
Wow, double binding the body, neck and headstock, is taking ages! I'm still only about a third of the way through, so to take a break from trying to get titebond sodden tape off my thumbs, I routed the headstock slots......hmmmmm...... Cutting them was slightly precarious: But I think they look lush:
-
Thanks all for some really great advice, have a look at these lovely shavings😁
-
Make sure you mark out the position of the bridge, and get it as near to the end of the bass as possible, that will help with neck dive. Once you've done that have a look and see which fret the front strap button is level with. Most basses have the strap button line up with fret 12 or 13. Personally I aim for fret 11 as I'm pretty sensitive to neck dive. The other critical thing is using light weight tuners. Ultralites can't be beat my opinion, and the non-USA ones are cheaper and are still great. @Andyjr1515 is yer man for funky strap button locations, but yes it will make a difference. I'm also just wondering whether the neck pocket is just a tad on the small side? Of course if you can move the bridge closer to the end of the bass, that will also make the neck pocket bigger.....