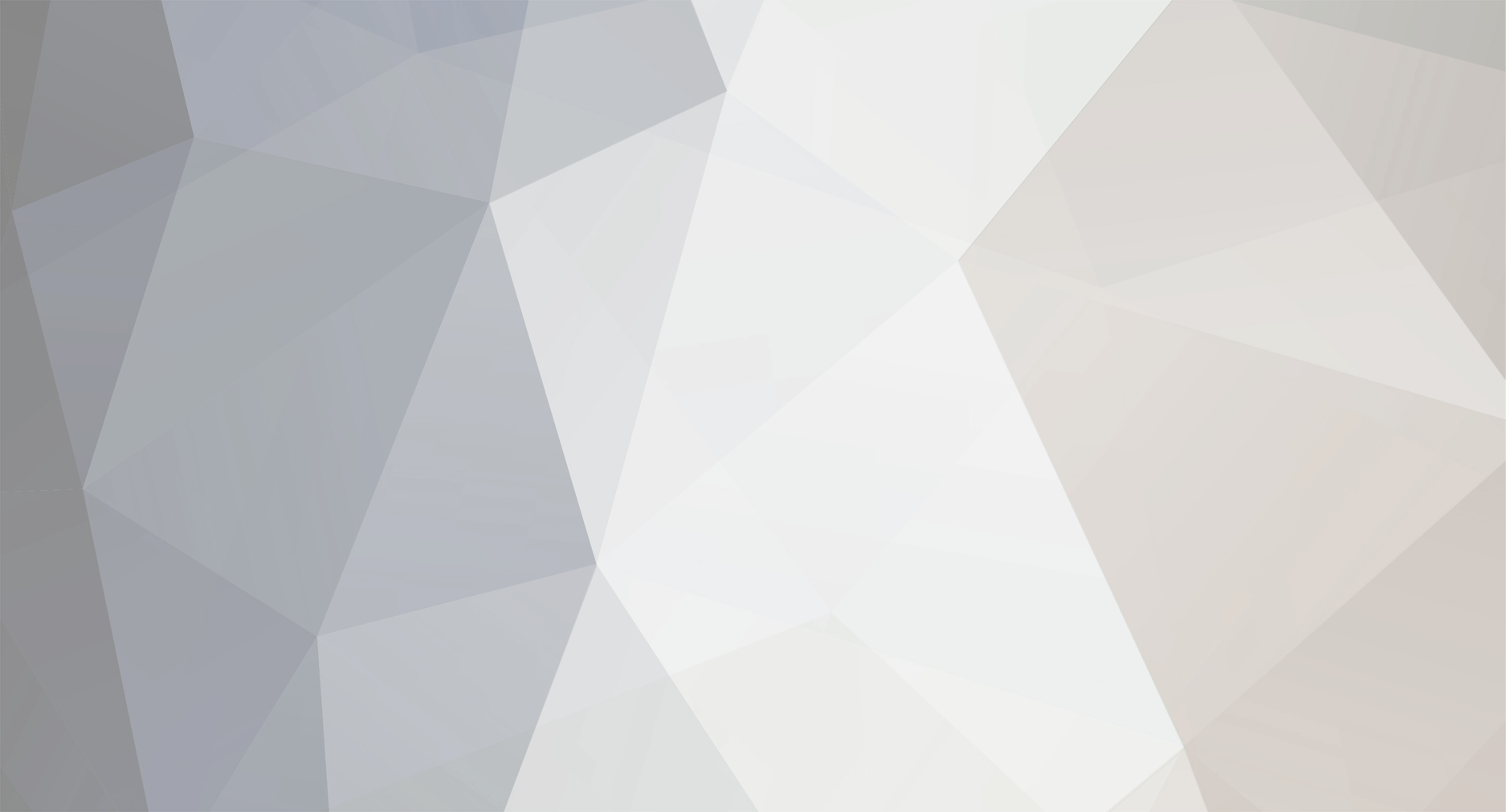
LawrenceH
Member-
Posts
1,836 -
Joined
-
Last visited
Content Type
Profiles
Forums
Events
Shop
Articles
Everything posted by LawrenceH
-
Next up - matching headstocks are in my correct opinion the nuts! I wanted one, so concurrently with the body spraying I had a go at this. First of all I sanded down the polyurethane finish on the front using a 400. I didn't bother trying to strip it off since it was thick, hard and actually made a really good smooth surface for paint application (much better than the body). Plus, this sanding didn't take away the original logo so it's underneath if for any reason anyone felt like going back to the original (serial number is on the back of the headstock anyhow). The hardest bit to start with was masking off the headstock well enough. I used bog-standard tape to begin with but later discovered that you can get special posh stretchy stuff for going round curves and things, which was much better. Nonetheless, thanks to the hard polyurethane finish and some very careful sanding back with a block, I got a good enough clean line on the primer layer just with the normal stuff. Up close it looks pretty clean, better I think than on one of the guitar garage blogs where he shows a close-up of a Lake Placid Blue headstock he has done. You can see in the following photos where there are some serious imperfections before sanding, these were pretty much rectified laterr as can be seen in the final pic (what looks like a white streak towards the left is just a trick of the light). You'll also see where I did go through into the wood a bit round the edges when sanding, this was a bit of a pain to get clean again when painting so if anyone else is having a go, when it comes to the headstock less is more - you don't really need to sand away more than just enough to rough it up. [attachment=64022:DSCF1139.JPG] [attachment=64023:DSCF1141.JPG] [attachment=64024:DSCF1143.JPG] [attachment=64025:DSCF1352.JPG] [attachment=64026:DSCF1355.JPG] [attachment=64027:DSCF1357.JPG]
-
Sanding back that colour layer was a real pain as I said. Eventually switching to better quality paper was the answer to prevent sand-through, and also (obvious tip to anyone but me) the harder the paint the better (so be patient and leave it an extra couple of days), and DON"T press at all hard especially when you're freehand-sanding around the edges where you can't use a proper block. The paper will do the work for you, pressing hard just gouges into it. Once I'd taken off the gross imperfections with 400, I think I jumped from 600 to 1200 in the end since this was the best quality paper I had, it worked ok though obviously it took longer than progressing through the grades. And I felt it was worth going up to 1200 rather than keeping it coarser. I've seen recommendations online that just use 400 but I suspect they're talking about nitro and my feeling is you need to take things finer with acrylic. So next were the clear coats. This was a right pain, the stuff seems to pull in dust like a black hole sucks in light, and it takes a loooong time to harden. As per the usual instructions, I tried spraying a couple of mist layers then added a couple more thicker ones but often, the mist layers would trap dust and I'd have to wait at least a day to be able to sand it out. In the end I started spraying quite thick just so I had a decent layer of clear down before any particles were able to settle on the surface, this meant it took a VERY long time for the paint to harden. Next cock-up: I did stupidly manage to cut back right down to the wood(!) when sanding out an imperfection around the back of the neck join. This was a major pain in the bum and taught me that you must never go onto autopilot when sanding! Fixing this was tricky, I had to sand back immediately around the fault, mask the whole rest of the bass off with tape and white paper and very carefully spray colour (didn't even try priming it as it would have been a disaster) trying to minimise the amount that got onto where the tape joined. The problem then was blending, partly due to pigment separation it's damn hard getting the colour to blend perfectly, especially when you're sanding a mixture of colour and clear coats. Took me a couple of goes at least IIRC, though much therapy has mostly blanked out the ghastlier details. In the end it wasn't perfect, but it was round the back and I hoped that more clear coat would in any case help sort things out once the thing was buffed to a shine (actually it did - woo!). At this point I was far too full of rage to take pictures, and due to various work commitments after sanding it down to 1200 I left it for the best part of a month to harden off. However that turned out to be a good thing because even though I left it longer than the two weeks recommended, it still wasn't really hard enough to buff to a high shine without issues. First I tried the Halfords rubbing compound which although coarse had worked well on an epoxy/polyurethane spray repair to my natural-finish Jap 75. It didn't do such a good job here, although things were improved somewhat when I attached one of those buffing cloths to my drill. T cut next! Better, but. But. I flipping well managed to gouge a couple of damn chunks thanks to the (*&^ thing catching and dragging round, didn't I? AND I overdid it around the neck pocket and took it back into the primer layer on the very edge. Yet another lesson in patience. I put the bass away again for another few weeks while we moved house (!) When I next took it out, it was moderately shiny but still with lots of scratches, not to mention a load of orange peel around the back and on the horns. As an experiment I tried 1500 wet paper followed by rubbing compound/T cut. This helped with the scratches, and I realised that ideally for an acrylic finish you should take it right down through the grades to 2000 if you want a properly good, glassy finish. But don't do what I did and go onto automatic pilot (again!) around the edge, going into the colour layer with a hint of flipping yellow filler coming through underneath (?!?). It's on the bottom, it's only evident if you look really close, and I've decided in the interests of sanity that it just doesn't matter enough to go back. So I also noticed that it seemed to come up to more of a shine this time - evidently the clear coat was still not fully hard when I did the initial cutting a month before. Probably due to spraying all those thick layers. Switching to a proper lint-free cloth also helped with the scratches (lesson - don't be lazy and use a yellow duster for the later bits) and in the end I was getting good results applying T cut with one pretty-much saturated cloth and giving it a good but GENTLE going over, before eventually switching to an 'off' cloth which took off the last bits of T cut and brought out the shine. One final thing, even though it had by now been left for ages, I got best results when there was a day or two between any more sanding and applying the T cut. One bass body, 'Daphne' blue: [attachment=64017:DSCF1388.JPG]
-
Now onto the colour layers. Hurrah! I should point out here that my experience with the headstock (to be outlined later) led me to realise that spraying in a living room, dust is a MAJOR pain in the bum for finish layers. Also that the paint particles get EVERYWHERE! Luckily they dry very fast (in mid air), so they don't adhere and can mostly be swept/brushed away. This meant a) I shifted to the kitchen, and b ) as explained earlier, started using the plastic greenhouse which had a nice transparent plastic cover over it that I could awkwardly spray round the edge of. Later cockups also led me to realise that washing the kitchen floor every time before you spray is a good idea, it makes a real difference to the amount of loose particles floating about waiting to land in your lovely pristine paint layer. Right. Colour spraying was much trickier than the primers. It took me a while to realise that the powdery texture I was getting with lots of tiny pits in was partly because I was shaking the cans to mix them (don't do this, just roll them around and let the ball do the work) and partly because the paint was drying too fast in mid-air. This gave me a very even colour layer but one that I had to cut back loads to get close to smooth, and then before you know it you're into the white and even worse yellow primer layer again F**K! Cue respray, hairdrying, sanding, swearing etc. I wasted several cans of paint and several days before I realised this, and experimenting led me to start heating the cans in warm water before spraying and to spray a shade closer, so it goes on slick. The problem here is then two-fold. First, it's bloody difficult to get that Goldilocks 'just right' distance and speed of movement before you get pooling. And second, it ALWAYS gave me orange peel and, worse, the pigments in the particular paint I was using were evidently different densities because if the paint was on even just a little too thick you got separation into lighter and darker layers. A real nightmare when sanding back. Heating the body of the bass itself with the hairdryer helps the paint dry faster once stuck on, which helped with runs and separation, but I never got this completely right. What I would do if I was trying again with Halfords cans would be to buy a replacement nozzle for the can. The Halfords one doesn't spread enough, it just concentrates the paint in one place which is rubbish. Apparently you can buy a (pink?) nozzle to give more of a fan and I'm sure this would really help apply the coats in a more controlled manner - my dad has sprayed enough cars to suggest this was the problem, along with the Halfords paint really needing a bit more thinner to stop it drying quite so quick. I wasn't sure if I needed to sand uniformly smooth before clear-coating, but I suspected that if I didn't, and only sanded out the dust etc, then any imperfections like orange peel and inconsistencies between sanded and unsanded layers would show through. Plus the Halfords instructions said to sand smooth so I did. Cue more sand-through, repair, rage etc etc. The colour layers are much less tolerant of hair drying and stay tackier for far longer than the primers. You can get away with wet sanding after a day, but it's noticeably better after a couple more and maybe even a week later would be safest. Oh and I can finally reveal the colour scheme - 'Daphne' (cough cough actually Ford Riviera!) blue! I don't think they actually offered this colour on 70s jazzes, you could maybe(?) get it on the late 60s blocked and bound basses but then you probably don't have the 70s pickup spacing. Anyway, I'm not trying to create a forgery and I like blue. Colour's a little off in these pics, more accurate later. I have failed to rotate the 2nd pic but it's hanging in the tomato grower. [attachment=64012:DSCF1381.JPG] [attachment=64011:DSCF1382.JPG]
-
The sealer seems to dry very quickly and is good to sand within an hour or two. Especially if you impatiently speed things along with a hairdryer like I kept doing! Despite what it says on the tin, I'd use several layers of the sealer - I had to go back and re-seal a few bits because of inadequate coverage. By the way, with sanding, don't bother with the Halfords wet and dry paper beyond 600. 800 and up is rubbish, best to buy something decent from an auto shop or online. Next up was priming. I used the Halfords white primer, and this is the point at which you (or I, at least) notice all the imperfections in the body that were previously hidden by the wood grain pattern. It's worth noting that because of the thick polyester finish, I don't think they bother with getting it as smooth as you need to for a good finish with nitro or acrylic. The solution was much swearing, using the Halford's filler primer (unfortunately bright mustard yellow) and as much hair-drying as I could get away with (too much and it blisters), then respraying over with white, more swearing when I cut into the yellow while wet sanding around the edges, more filling, more priming and eventually I had a white body that had been sanded down to 800 wet. If I'd realised at this point how crap the Halfords 800 was I'd have switched to the 600 and probably got less sand-through but that's why I did this one with cheap-o rattlecans! You'll notice the makeshift spray booth made of a stepladder, this was before I switched to the little greenhouse. You can also see where I needed to spray more to hid the yellow filler primer. Why they have to pigment that stuff I really don't know. By the way, for the novice, the primer is much more powdery than the actual colour layers and gives you a false sense of how easy it is to get good, even coverage. For the same reason it also dries quicker than the later layers and you can be (or I was at least) quite cavalier about spraying, speeding the drying with gentle heat, and wet sanding all within a couple of hours. [attachment=64009:DSCF1369.JPG]
-
[quote name='silddx' post='1024735' date='Nov 15 2010, 03:24 PM']In terms of finishing, I have used the Halfords type acrylic and compared to Tonethech Luthier Supplies Pre Cat Nitro Rattle cans, it is not very good at all. I am a complete amateur at refinishing and I got a great finish with the pre cat Nitro. £15 a can. You can wet sand it after 24 hours, well I did, and get a lovely glassy finish quite quickly. If you need the method I can help you, or talk to Tonethech themselves, they are incredibly helpful. EDIT: Oh I see, you have sprayed it already.[/quote] Yup, but thanks for the tip - I didn't want to start with the NC cans as they're quite expensive for experimenting with, especially as I was worried that getting a smooth enough finish before spraying might be tricky. I'll definitely try NC in future though for reasons this build thread will make clear! My father was a mechanic and has a spray gun/compressor, plus some experience spraying both nitro and acrylic, so I'll probably go down that route. By the way, the heat plus scraper thing worked very well with the hairdryer - I think it melts the original sealer layer if you keep the heat on for a bit, and the outer layer softens enough to peel away. A photo of the aftermath: [attachment=63996:DSCF1136.JPG]
-
[quote name='AndyTravis' post='1024511' date='Nov 15 2010, 12:22 PM']Ace, what colour are you going for?[/quote] Wasn't really sure to start with - definitely fancied candy apple red, but for a first go that one felt a bit ambitious - plus red translucent tint isn't readily available at Halfords! Left the decision in the end until after sealing and priming. Will reveal all as the thread progresses, along with the many mishaps, to force the curious to keep reading I realise there's people with proper spray set-ups on here who consider a refinish trivial, but I found it an absolute b****r to get right with spray cans and hopefully my experience will offer some pointers for fellow beginners. To get the paint out of that pointless routing hole so I could fill it, and to scuff up the pickup cavities, I used a Dremel sanding bit from B&Q - basically a little rough stone that you put on the end of a drill. First couple of mishaps were when my slightly unwieldy drill and my ineptness led me to scuff the wood near the edges, but no matter as I was using wood filler to smooth things out where the chisel marks were anyway! [attachment=63993:DSCF1134.JPG] [attachment=63994:DSCF1363.JPG] So lacking the tools to make a proper wood plug, I ended up filling the hole with Ronseal wood filler, in a couple of goes with a night in between layers to help it dry better. I also filled the pickguard screw holes (bodged to fit another pickguard by previous owner so I wanted to start fresh) and a couple of dings, unfortunately I don't have any pictures.EDIT: Yes I do, here: [attachment=64010:DSCF1368.JPG] Next I used an acrylic sanding sealer (Chestnut is the manufacturer). I tried spraying outside first, which was a disaster - even the slightest airflow messed things right up. So at the suggestion of my remarkably tolerant wife, I bought one of those mini plastic greenhouses for growing tomatoes in, to act as an indoor spray booth. And I pinched a couple of 3M masks from work to try and minimise the amount I poisoned myself.
-
So, it has taken me ages but finally my refinish of my Mexican Classic 70s is (nearly!) done. Started off a shiny, pristine black. I know what you're thinking - almost as boring as sunburst! [attachment=63972:DSCF1107.JPG] [attachment=63973:DSCF1117.JPG] Naturally, I had to do something about that. I tried sanding for a few minutes until I got completely bored of it, then decided more drastic measures were necessary. As I mentioned in another thread a while back, I found the most effective way to strip the bass back once I'd hacked into it with a chisel enough to getstarted, was by using a paint scraper combined with a powerful hairdryer! Better than a heat gun in some ways as it made the polyester more plastic but didn't competely melt it into that disgusting sticky gunk. Point of no return: [attachment=63974:DSCF1124.JPG] Forging ahead: [attachment=63975:DSCF1127.JPG] [attachment=63976:DSCF1130.JPG]
-
What cabs do people use with their Orange Terror Bass Head?
LawrenceH replied to Cat Burrito's topic in Amps and Cabs
Gotta be worth trying the sp210/212. Tried the Terror into those in Red Dog here in Edinburgh and was seriously impressed with the depth of the sound given their tiny footprint. I just wasn't a fan of the dirty tone! Bit of a one-trick pony I felt. But I think that's more the head. Made me wonder how much the compromises of an Isobaric design can be overcome by the choice of driver, I'd be interested to know what's actually loaded into those things. -
[quote name='Mr. Foxen' post='1022524' date='Nov 13 2010, 03:22 PM']Kickback shape means more cuts and joints, and [b]compromised internal area[/b], so more work, more wood, more cost, for a compromised amp, that is bigger to pack and ship.[/quote] Mr Foxen has hit the nail on the head, this is probably the real reason. Their internal volume is seriously compromised compared to how much room they effectively take up so you can't really get decent bass response out of them without them being awkwardly large. The awkward cuts don't help either. Much better to use a decent amp stand. The one I have is very compact and lightweight, plus has a fitting for a mic boom - handy for PA guys looking to mic guitar cabs! I loved it for my own bass gigs and whenever I did sound for guitards who turned up too loud through little Fender-type combos, since once their overly-directional little combos were firing directly at their ears they'd turn right down. Hallelujah! recommend it: [url="http://www.soundslive.co.uk/product~name~Ultimate-AMP-150~ID~5498.asp"]http://www.soundslive.co.uk/product~name~U...150~ID~5498.asp[/url]
-
[quote name='Faithless' post='1015644' date='Nov 7 2010, 08:10 PM']Now listen folks.. What's the cheapest and the lightest combo out there? (head and cab must have an option of being separated if needed) I want something really portable. (head + lil' cab, something around 1x10) I really dig the Ibanez Promethean thing, but, 600 pounds for new.. Or am I just too naive maybe? easy Faith[/quote] £600 new is hard to beat. You could maybe pair an Ashdown Little Giant 350 with a suitable cab, but they don't have the most solid reputation as far as I'm aware.
-
Obscure Musical Backwaters - The Great SGC Nanyo Thread
LawrenceH replied to Happy Jack's topic in Bass Guitars
[quote name='Happy Jack' post='1021316' date='Nov 12 2010, 12:50 PM']Those bloody Syrians![/quote] Nice to see a fretted SB330 though, don't often see them. I have the fretless version, it's a great bass. The soapbar pickups are decent, but I'd be interested to know of any drop-in replacements. -
A rather more serious HappyJackShit topic
LawrenceH replied to Happy Jack's topic in General Discussion
There have been several items on here recently that were straight off ebay and re-sold at profit. That's all well and good, but if basschat becomes a marketplace for what is effectively professional trading, then I wonder about fees being more formalised. -
[quote name='dave_bass5' post='1021089' date='Nov 12 2010, 10:21 AM']Badass definitely not, cant comment on the others.[/quote] I think the 50th anniversary jazz bass that comes with covers has a Fender 'high-mass vintage' bridge - may be worth considering? Oh and by the way, I replaced the supposedly US pickups on my own Jap 75RI and the sound came to life. I used the Mexican Vintage Alnicos as seen in the highway 1 and Classic 70s. Cheap but good. I'm sure Wizards, DiMarzios or something would do the job.
-
What's the difference between the 75RI and the VMJ?
LawrenceH replied to waynepunkdude's topic in Bass Guitars
[quote name='waynepunkdude' post='1020562' date='Nov 11 2010, 07:18 PM']I've tried a CIJ 75RI and found it almost the same as my modded VMJ. I think I'm gonna leave it and pick up a surf green CIJ Jazz.[/quote] I think the all-maple construction of the VMJ makes it a bit of a potential tone monster. The weakest link for me was the pickups - they're punchy but they seriously lack bandwidth compared to traditional jazz pups, the high end sounds rubbish. Replace those and you're on to a winner, the acoustic tone on the couple I tried was very warm and resonant. Much more lively than the CV jazzes, though these seem to have better finishing and probably more trad-sounding pickups. -
What's the difference between the 75RI and the VMJ?
LawrenceH replied to waynepunkdude's topic in Bass Guitars
[quote name='waynepunkdude' post='1020083' date='Nov 11 2010, 02:12 PM']There is probably loads but humour me.[/quote] Pickup spacing (70s v 60s), pickup type (Vintage 75s vDuncan Designed), body wood (ash v maple), and based on what I've seen of VMJs, finish quality. Neck profile? Also 3- v 4-bolt neckplate and bullet truss v the other kind. Oh and most importantly of all, the knobs are different I think. -
Not sure about fancy-pants Class D and H designs, which I'd imagine to be quite expensive to make well, but a lot of sound guys with semi-serious set-ups push out the low end watts with things like the EP1500 - they have quite a solid reputation, and reputedly their 2ohm claim is a bit more realistic than most cheap/mid-priced stuff. It's a bit like that LH500 by Hartke - tried and tested old technology put together using cheap labour, the main downside is that they're comparatively heavy by modern standards. +1 to the old composer comment above btw, I felt they punched above their weight.
-
Markbass F1 voltage conversion query
LawrenceH replied to LawrenceH's topic in Repairs and Technical
[quote name='bumnote' post='1018777' date='Nov 10 2010, 01:52 PM']size=4]So the amp is sensitive to 230 or 240V power supply (contrary to what was said above).[/size][/quote] Bit confused with all the quotes within quotes. But for me the issue is clear enough now. The amp is designed to operate within a tolerance range of voltages, it's very likely that most of the time it will be fine at 230 or 240 whatever the jumper settings. However, if the supply voltage fluctuates outside these tolerance bands then it increases the chances of damage. Adjusting where the centre of the band lies to 230 or 240 depending on the nominal supply voltage of a particular region makes sense, as you're operating further within the safe limits and the supply voltage can slip further from nominal BEFORE this becomes an issue. So for me, markbasschat's comments (suitably amended regarding the voltage in uk) are valid and useful, as have others' been. From what I can gather, 268V is way outside the old uk spec of +/-6% or new spec of 230 +10/-6%. I wonder how many odd computer failures could be attributed to poorly conditioned mains. But anyway, surely if Markbass were particularly susceptible to mains voltage changes then I'm sure we'd have heard about more problems by now. I seem to remember their failure rate is overall pretty low - part of what attracted me! But it seems unsurprising that a tiny class D amp like the F1 might be less robust than a whopping great transformer-weighted behemoth. And I've had a few of them fail anyway, for different reasons, so it's all swings and roundabouts! As I said based on the voltage readings people seem to be finding I'm going for 240V setting since probably that's what most uk suppliers are doing in practice. This article from soundonsound specifically talking about problems with mains voltage has been very interesting and informative: [url="http://www.soundonsound.com/sos/jul03/articles/mainsproblems.asp"]http://www.soundonsound.com/sos/jul03/arti...insproblems.asp[/url] I suspect most of what it says is still valid, and dood if your supply is regularly above that level then they're legally obliged to do something about it. Thanks again, I've learnt tons from starting this thread! Now if only that somehow translated to playing better bass I'd be as happy as Larry. Oh wait, that's me. Woo! -
Markbass F1 voltage conversion query
LawrenceH replied to LawrenceH's topic in Repairs and Technical
[quote name='MarkBassChat' post='1018457' date='Nov 10 2010, 10:10 AM']What is interesting with Markbass F1 is that the change means slightly lower voltage for the power amp. And lower voltage means less power. Of course you will not hear the difference but I wonder what Markbass would recommend. And I'm not refering to places where you have still 268V. There, most probably the conversion hasn't been done and if some equipment fails, you can most probably ask the power supplier for a compensation :-).[/quote] Well, given that apparently most suppliers haven't actually changed the supply voltage since 240 falls within the tolerance bands, I think I'll go for the 240 setting and see where it takes me. When I have 500 of the damn things at my disposal, I think I can spare the odd watt Thanks for all the help guys, this has been a really useful (for me) thread! -
Markbass F1 voltage conversion query
LawrenceH replied to LawrenceH's topic in Repairs and Technical
[quote name='dood' post='1018181' date='Nov 9 2010, 09:50 PM'][attachment=63539:UK240VF1a.jpg] [attachment=63540:UK240VF1b.jpg] OK, here we go - as clear as needs to be I think. disclaimer taken as read - this change voids warranty and should be carried out by qualified service personnel.[/quote] This is great! Thanks so much. Very glad I asked this question as no-one's referred to these other jumpers. MarkBassChat, welcome to bass chat and thanks for the clarifications, if you look in the bottom right of your posts you'll see you can edit them so if you want to make things clearer that's an option. Having said that.. According to wikipedia you're correct in that the UK as of 2008 is on 230V +10%/-6%. Most of the EU is on 230+/-10%. So probably the 230V setting would be appropriate, though hopefully I'm right in assuming either would be fine. I'm quite surprised that there is actually a difference in terms of required jumper settings, it makes me wonder if the F1 is going to be a temperamental amp when it comes to things like outside gigs using generators, long cables etc. -
[quote name='phsycoandy' post='1017923' date='Nov 9 2010, 06:25 PM']Last drop to £850. If this doesn't sell it may have to be a mint 3TSB '76 Jazz, double [/quote] I'd take this over the '76, still got what looks like 70s pickup spacing on here for the funky sound (just out of interest can you confirm that's right?), and none of that yucky sunburst rubbish Bump for a serious bargain IMO, just wish I had the cash to metaphorically bite your hand off
-
Based on my experiences I think the spacing definitely has a very noticeable effect on the sound, and the body wood probably too makes some difference. But. As I've said on here before, I thought the pickups in my Jap 75RI (allegedly US) were rubbish compared to the Vintage Alnico ones in the Classic 70s, and now the Classic 70s pickups sit in my ash Jap 75RI while a pair of genuine US 75 Vintages are waiting to be installed in the Classic 70s The (Mexican) Vintage Alnicos made a big positive difference to the tone of the Jap jazz so it'll be an interesting comparison once I throw the US 75s into the mix. Remember also, the 75 Vintage pickups in the US75RI are a different part number to the 'normal' vintage pickups as used in the 62RI! Once I've done a comparison between the three pickups sets then I will report back, I keep meaning to do this but work is getting in the way of my geeky fun
-
Markbass F1 voltage conversion query
LawrenceH replied to LawrenceH's topic in Repairs and Technical
[quote name='dood' post='1017992' date='Nov 9 2010, 07:16 PM']Hell yeah! I'm glad you asked the questioned - otherwise I would have been hassling for flippyfloop in the For Sale forum to sell his F500 instead of trading! There is a fuse in the holder underneath the IEC power socket. No need to lift the lid. Infact there should be a spare fuse in the other half of the little drawer too. The F1 I have here (a UK model) has a 3.15A fuse in it. Sorry I didn't check if it was a fast blow or a surge type. The fuse in the mains plug is designed to protect the lead and can be 13A.[/quote] Right-oh! Thought it was probably so but no harm in an idiot-check. Thanks for the heads-up regarding where it is, and glad to have inadvertently been of help with my question -
Markbass F1 voltage conversion query
LawrenceH replied to LawrenceH's topic in Repairs and Technical
[quote name='dood' post='1017868' date='Nov 9 2010, 05:49 PM']Cha-Ching, shopping done.. come to pa-pa![/quote] Yeah good eh? tombboy, thanks yup that's from the talkbass thread i was talking about, slightly confusingly the relevant picture is titled 'Markbass LMII', hence I wanted to double-check! I don't know about anyone else but looking at US sites, I feel I lose an awful lot in translation What I meant talking about the fuse with respect to safety was that, I'd expect the F1 to still work without changing the fuse when going 120 to 240 just not the other way round - but are we talking about an internal fuse or just the one in the plug? Thanks for all the help! -
Hi all, I've just taken receipt of a US Markbass F1. I'm aware these can be converted to run at UK voltage, and the markbass manual details the fuses required for 100, 120,230 and 240V so that should be all good. Can anyone confirm exactly what the jumper switch change should be? I've seen that picture on the talkbass thread which seems to show an f1 but it's not all that clear, and I don't know if the jumper has alternative settings for 230 versus 240 volts. Also in case it's not obvious which fuse I should change, is it just the one referred to in the manual or should I look elsewhere? I'm assuming down-rating the fuse means changing is just a safety thing, it won't affect normal performance, is that correct? Thanks for any help! Lawrence
-
[quote name='Mykesbass' post='1014568' date='Nov 6 2010, 05:57 PM']If I can ask an additional, related question, if an amp with two speaker outputs runs at X at 4 ohms or Y at 8 ohms, if you run one 4 ohm speaker will you get x or do you need to run two 8 ohm speakers?[/quote] You will get X.