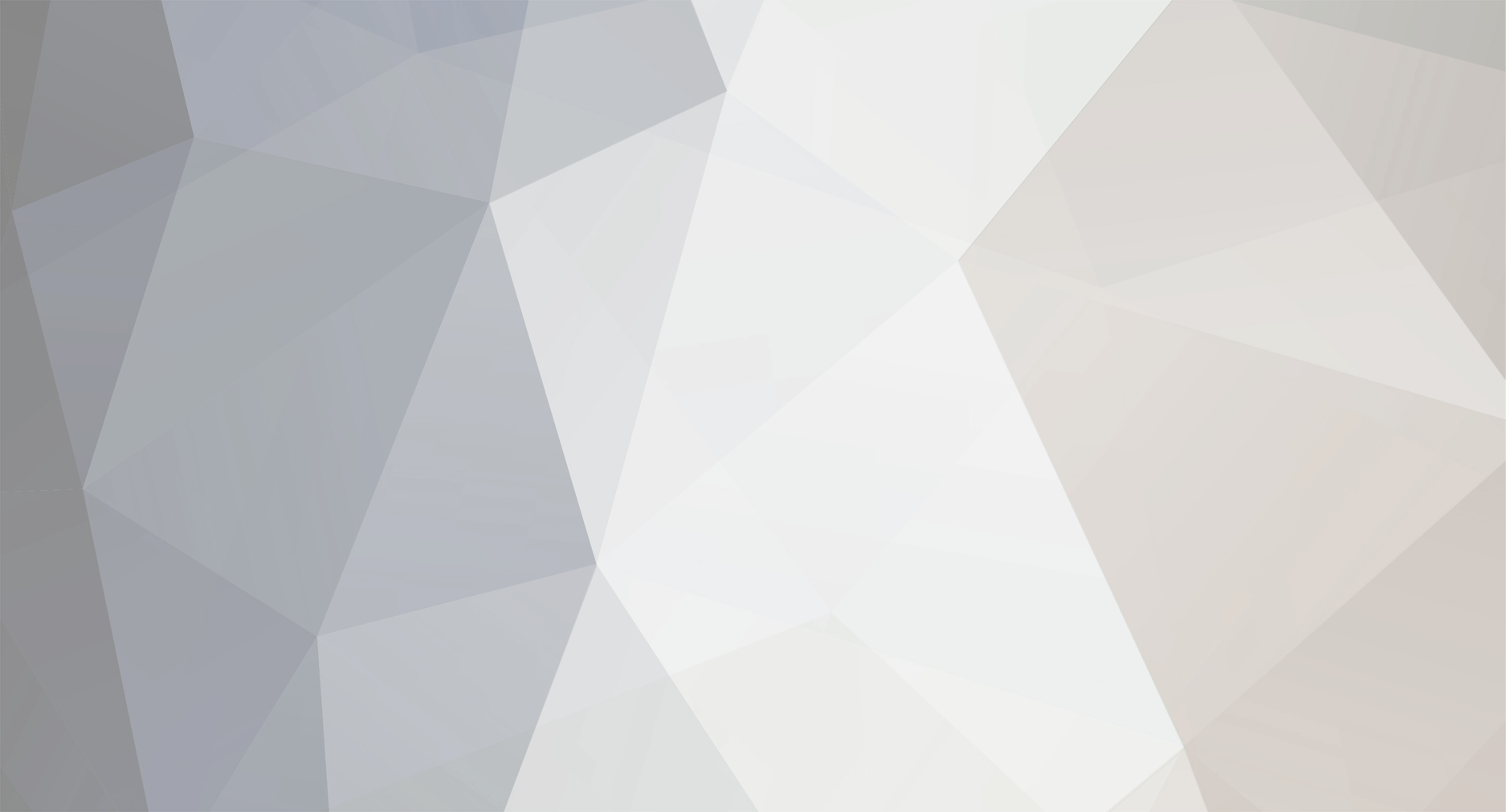
rwillett
⭐Supporting Member⭐-
Posts
1,489 -
Joined
-
Last visited
-
Days Won
5
Content Type
Profiles
Forums
Events
Shop
Articles
Everything posted by rwillett
-
How was Your rehearsal last morning or night ?
rwillett replied to nilorius's topic in General Discussion
It's all.down to your new pedalboard 😊 -
I do have a number of 3d printers but possibly more importantly I have a decent 3d scanner. So if you can't find a 3d model to use, and you have a truss rod cover I can get my hands on for a day, I can scan it, model it and print it. If you need to bend the plastic sheet then a hairdryer may help. It all depends on the plastic. Let me know if I can help.
-
I can see a small amount of unused space on that board. Tut, letting the side down.
-
Motorheadache in Bradford tonight 12/4/25. Suspect I'll be the one at the back, pressed against the wall, with ear plugs in
-
Its wonderful to watch as @neepheid stretches space-time to get all the stuff in. Doctor Who is a mere amateur....
-
Have you changed car since last year? Or still playing Tetris?
-
That sounds great. Bring what you wish, we'll have space and it gives people a chance to try stuff out. I'd be interested in the lightweight setup but I suspect all is of interest. If you're coming from Liverpool, I'd probably come all the way up to J36 on the M6 rather than coming off at Lancaster and threading your weight through the countryside via Wennington and Bentham. My eldest was in Alder Hay for a while so we got to know the Clapham to Liverpool journey very well for six months or so. Rob
-
Technically less than a month to go now I have 11-12 attendees. @rwillett @bigthumb @neepheid @ead @80Hz @GreeneKing @stevie @nekomatic <-- TBC @ossyrocks @peterjam @doomkeeper @Frank Blank Food will be provided, in the form of pizza. So if anybody has any dietary preferences such as vegetarian or allergies please let me know, so we can cater for you. You are also welcome to bring your own food. There is a full kitchen and (I think) a microwave. Tea and coffee will be on tap all through the day. There's no issues if other people want to come or bring friends. @zbd1960 are you coming down? Rob
-
Here's my homemade pedalboard. I'm now swinging both ways and playing guitar and bass. I prefer the sound of the guitar through the Tonex and the bass through the Mod Dwarf. So use the EHX box to mix. The third channel of the EHX box goes to a Mac for recording purposes. The Tonex has some lovely Fender amps which sound great with a Fender Tele or Strat. It's all driven through a Cioks DC-7 mounted underneath. Its bigger than it needs to be, I could save 2-3cm on the width, but its not a big deal. Its very, very solid. You can certainly stand on it, and we got up to 150Kg with zero issues, so possibly too solid Everything is printed including the cable management which nicely slots into the aluminium extrusion.
-
Perhaps they only had a scratchplate sized bit of exotic wood?
-
Sorry to hear you can't come. We'll raise a glass to you...
-
Too late, I've been and gone. Nice gaff. He used to have some really nice guitars Rob
-
First time I've seen it loaded up. Looks great
-
Ah, the wisdom of experience....
-
Many people would shirk at these duties, you manfully stood up and were counted, about five bottles by my recollection....
-
To be fair, you were only being hospitable and keeping me company when we drank.
-
Not with me anywhere it I recall the last time we drank... Rob
-
Jez sold me a pair of four string headless clamps. Zero issues, well packaged, such fast delivery that I couldn't understand what they were as I wasn't expecting them for a few days and looked at them with a blank expression Rob
-
I'll take it and give you a free bottle of wine in exchange
-
Pure random chance The real point of this little experiment is the four little pogo connectors at the bottom with two small (but rather powerful) magnets on the sides. Just seeing if it's feasible to change pickups easily and quickly. Using a guitar pickup as slightly easier to play with. There's the other side of the pogo pickup fixed to a body of a guitar. The three black socket caps raise the pickup up and down. There's nothing too clever there. What this experiment has shown me is that these pickups are so sodding thin, it's really difficult to get them high enough, so this design needs adaptation to be able to handle thin pickups. Humbuckers are not an issue. The grey one in the middle is an a\ctual 3d scan of a humbucker. You can see the tape around the body. Rob
-
An investigative prototype exploring ideas and thoughts, not necessarily for a rail bass but might be,,,