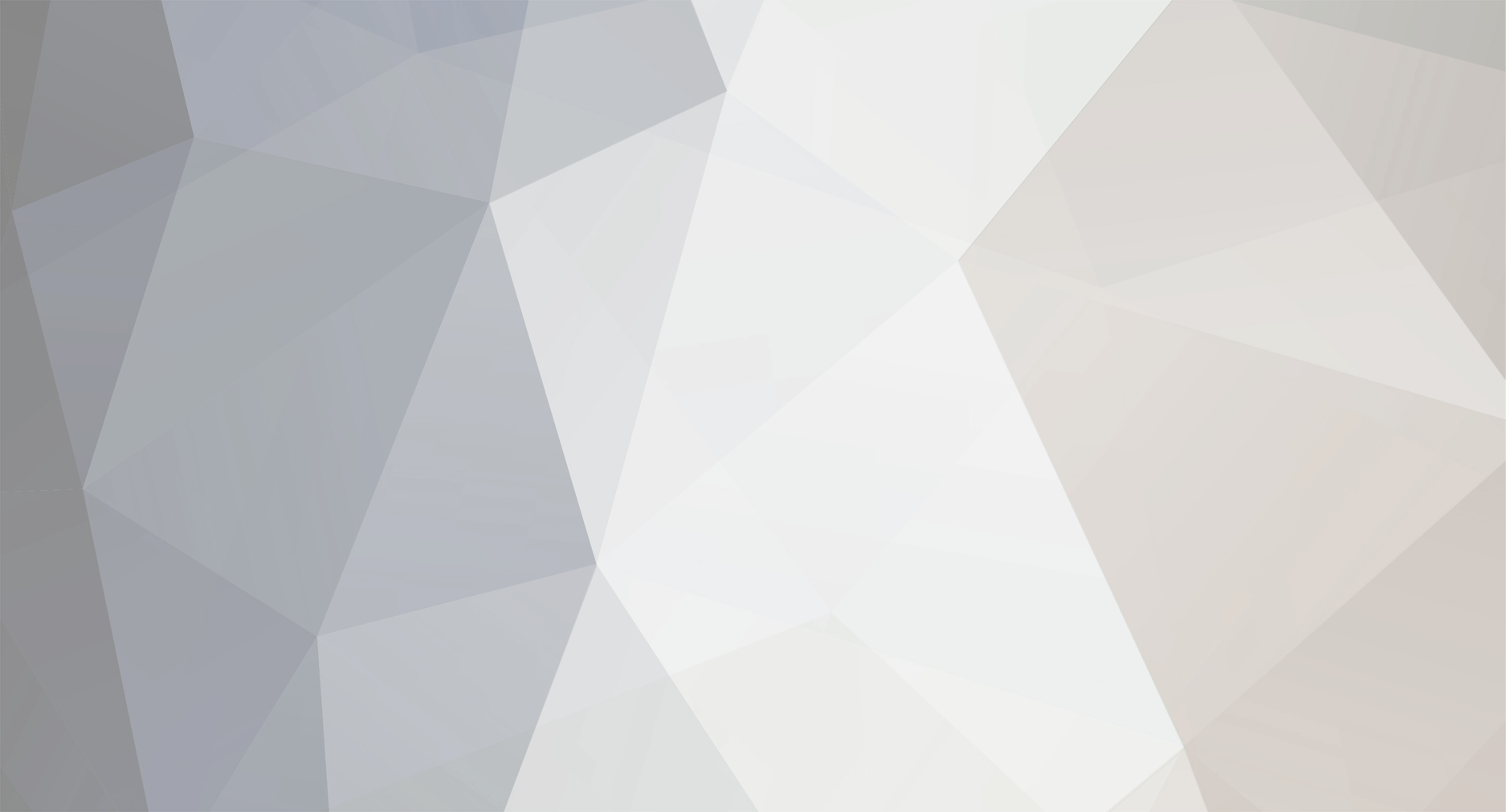
rwillett
⭐Supporting Member⭐-
Posts
1,627 -
Joined
-
Last visited
-
Days Won
6
Content Type
Profiles
Forums
Events
Shop
Articles
Everything posted by rwillett
-
The numbers grow: @neepheid @ossyrocks @doomkeeper @Richard R @peterjam @Frank Blank @rwillett Rob
-
So we have confirmed as opposed to not 100% sure... @rwillett @neepheid @ossyrocks @doomkeeper
-
In your defence, they are very, very nice indeed. If only I played in a band, had some gigs lined up, failed biology 'O' level, had a cabinet to drive and had not already sacrificed a kidney I'd love this. In all seriousness, this is utterly gorgeous. I'd love to be on stage and have this behind me. Unless I was at Wembley, I'd have the quiet satisfaction that I wasn't going be ignored and lost in the mix.
-
RWB guitars are very laid back. They have a lovely Vintage (the brand not aged) semi acoustic which was very nice to play. Quite decently priced as well. There was also a nice reliced non Fender Telecaster which played nicely. T'other half rang me whilst I was there so had to hot foot it out to meet her. Didn't have a chance to look at anything else. Back in York centre now so may have a second trip. If you go, say hi to them. There's zero pressure to buy. Indeed I think they should push more IMHO. Rob
-
We're in York today. Just popped into RWB guitars and managed to avoid spending lots of money
-
My family is from Chesterfield so if you organise one that area, I'll pop down.
-
Most Ethernet cable is sold core so is not designed to be constantly reconnected, coiled, uncooled etc. As previous posters have said, I'd be amazed it lasts a year. It will also go wrong at just the wrong time. Cabling has this inherent property of knowing the worst possible time to fail to cause the maximum chaos. Rob
-
You are more than welcome to come down
-
I've now confirmed the NW Bass Bash for Sat 10/5/25. Format will be much as before unless people have a better idea. If people do want a place to stay Fri night, please let me know as I do have space in the house. We can fit a fair amount in real and actual comfortable beds and we will still have space for camp beds and the like. People are welcome to turn up late as well. There's plenty of space to store gear safely. I'll get the ball rolling with gear I may bring along. As I live next door, it's easy to change. Fender Jazz Bass Fender Mustang Bass Fender Telecaster - Yep six strings, I have no shame 3d printed Jazz Bass 3d printed headless bass Maybe a 3d printed reverse Thunderbird headless bass if I can pull my finger out. Ibanez short scale bass - ex building site by the looks of it Yamaha HS7 monitor A weird and unusual pedalboard setup. That'll probably change anyway.
-
Not sure if anythuing has been arranged for this but the NW Bass Bash (which is in Yorkshire, albeit North Yorkshire) will be on Sat 10th May 2025. It will be in Clapham, North Yorkshire and be all day. We have the village hall basically from the night before to as late as we want it on Saturday. Here's the village hall: https://claphamyorkshire.co.uk/locals/clapham-village-hall/ Here's a link to Google Maps which shows you where we are: https://maps.app.goo.gl/vGE1aCW3TDPBPFVcA If you are interested, let me know Thanks Rob
-
Will Basschat survive the Online Safety Act?
rwillett replied to fretmeister's topic in General Discussion
Nope, i am not proud that we don’t have a absolute right of free speech. Please do NOT tag me with that. I am a great believer in the right to say most of the time most of what I want to say. i was pointing out that the right of free speech is not and should not be an absolute right regardless of what was said. Words can have serious consequences and that people deliberately use words in certain ways to deliberately create chaos and disorder (disorder here is not legal disorder). We see this with people retweeting things that are made up lies to further their own agenda. I chose an extreme example to illustrate how this happens. Americans have their first amendment which gives people a lot more protection than people in this country, as to what they can say, however even that has limits on what people can say, you defame somebody and it can have serious consequences as Rudy Gilliarno has found out. Fox News settled a legal case for libel for circa $700M for stating that voting machines were fixing the election. Where should free speech sit on the censorship continuum of you can say anything without any consequences whatsoever up to the other end where you can say nothing unless it's govt prescribed? I personally am a long way down the say as much as you can end of the spectrum. I have actively supported free speech by speaking at meetings about it, by demonstrating against laws that try to limit it, Section 28 anyone? I donate to free speech campaigns as well. However we are now finding that people are abusing that privilege. It is not a right in this country as its not enshrined simply in a law or constitution. We have a patchwork of laws governing what can be said and what cannot be said. Sophisticated actors take advantage of that to promote hate through various arguments, such as "I was just asking the question that everybody wants to know" when really they are knowingly lying through their teeth to further their own agenda. Free speech is very difficult, people are constantly pushing the boundaries as to what is legal and what isn't. I find a lot of what some people say about immigrants very, very hard to take, I have a lot of close friends from many countries around the world, but I recognise that the law doesn't make it illegal. I also realise that other people have different views to mine and that for me to have my views, other people will have views contrary to mine. That's what a more or less free society encourages. We are not all the same. Laws on free speech have evolved in this country over the last four hundred or so years. I have no doubt they will continue to evolve as our society evolves and that the free speech pendulum will swing back and forwards. (Note I deliberately did not say left and right) America has the first, second and other amendments guarantjng certain rights such as free speech, the right to bear arms, the right to vote and so on. In.this country we do not have those amendments as our civil and criminal laws have changed over time. I do not know which system is better as I can often find contradictory comparisons. However as I have said before, even in the USA, the first amendment right to free speech is not absolute as defamation is against the law. You can say a lot of things that are brutal and hateful and not be prosecuted in the USA which if you said in this country would lead to a prosecution. I worry that we criminalise things that we shouldn't but I also worry that we allow unfettered hate speak that creates violent riots. We can't have it both ways but I don't know the answer. However I am not against free speech, quite the opposite, but I do not know the answer, if there even is one, of how we address the lies that some people clearly make up to stir hatred and violence. I want people to say what they think, I do not want those thoughts and words to create the violence that ensued last time. I really don't want anybody to think I'm against free speech as I'm not. We have now gone way off topic. Possibly more than any other thread. I am happy to have this discussion elsewhere but -
Would love to see that build. 2 x 6" sounds interesting. Rob
-
I'll take you up on that and throw in a slap up meal at Mrs Miggins Pie Shop...
-
Will Basschat survive the Online Safety Act?
rwillett replied to fretmeister's topic in General Discussion
... The TTL is very low and the retry timer is probably a few months for the next brood Rob -
Will Basschat survive the Online Safety Act?
rwillett replied to fretmeister's topic in General Discussion
No. Never been suggested as the UK economy would halt. The govt keeps trying to open up encrypted traffic as they think that this will let them catch paedophiles and drug traffickers. The govt thinks that if they have their own encryption keys and back door to WhatsApp and Telegram then they'll keep it secure and no one would ever break in and abuse the system. Mmm... I believe but do not know, that every tech company has said they will pull their products out of the UK if the govt passes legislation to do this. They will not break their products just for the UK. The EU has also looked at doing something similar. The USA hasn't as most of the elected officials take huge sums of money from the tech companies for their election campaigns so it doesn't come up. -
Will Basschat survive the Online Safety Act?
rwillett replied to fretmeister's topic in General Discussion
Most IT companies will work within the local laws in which they operate. Note the word local. Xwitter makes a big fuss of saying that they are only concerned with freedom of speech, but the moment the local law enforcement knocks on their doors, they wring their hands, shout about it and the quietly do what's asked. See recent cases of Xwitter in India and Brazil. Indeed since President elect Musk took over, it appears to have got worse for users. Facebook is the same. Not one of them will refuse a legal warrant as they can't afford to. The law is against them. VPN operators will work within the law but unless the law says they must keep logs and specify exactly what is in those logs (highly unlikely), they don't keep logs apart from when they lie and do keep logs. For accountancy purposes, they keep logs of who pays them, so that's a good start for law enforcement. In most cases, law enforcement follows the money trail as everybody keeps that information. Sensible people will have a number of VPN's when using TOR, so the use of TOR is slightly hidden in the encrypted traffic. As previously stated TOR was set up to avoid censorship by having multiple data paths such that it is impossible to track. FBI successes against the Silk Road and other Dark Web operators seem to indicate it's not quite as anonymous as people think. I'm not sure what to believe here though. Still can't see how the UK can ban VPN's though. Rob -
Will Basschat survive the Online Safety Act?
rwillett replied to fretmeister's topic in General Discussion
As would the hawks and other birds of prey -
Will Basschat survive the Online Safety Act?
rwillett replied to fretmeister's topic in General Discussion
I'll bow to your greater experience here. I have done it on Linux a few times when working abroad, but it tended to be ad-hoc, then it got to be a fag, so I set it all up on a dedicated laptop and took that with me. I have a tiny matchbox sized unit I use now, which does all the hard work and gives me a private wifi network abroad with a VPN home. One day I'll go back to a sensible simple home network, I'm currently upgrading my Netgear Orbi 5 mesh network to OpenWRT, but until then I'll play. Anyway, I'm off to investigate how to run a true VPN over pigeons Rob -
Will Basschat survive the Online Safety Act?
rwillett replied to fretmeister's topic in General Discussion
My pfsense VPN took around 15 mins to setup as I had to read the documentation, I then had to transfer files safely to my devices. I do feel I was letting the side down by reading the docs though https://www.comparitech.com/blog/vpn-privacy/openvpn-server-pfsense/ Not sure if thats a "true" VPN or not. Looks like one to me, works like one as it uses stuff like Tunnelblk, OpenVPN and Viscosity, all VPN clients. Works on my iPad, iPhone and Macbooks. I don't use Windows at home so can't comment on that. Its not advertised anywhere though. I also sometimes change the ports as some foreign ISP's in ski hotels have blocked the more common VPN ports. The French seem to like to do this for some reason, I have a feeling there's a law. Took a few seconds to sort that out. Thats how easy it is. -
Will Basschat survive the Online Safety Act?
rwillett replied to fretmeister's topic in General Discussion
How is the ISP going to do this? Who is going to tell the ISP the block list that changes every second? Who is going to pay for the hardware and the software to do this? The second it's published it's out of date, mind you it was never accurate to start with. Who.is going to collate all the VPN'S in the first place? No obligation of foreign VPN'S to even publish their IP addresses they use, so how's an ISP going to know? The UK govt wouldn't know. How are you going to know that an https request to a non UK website isnt actually a vpn tunnel? The ISP can't know as it appears to be on port 443. How do you stop somebody tunneling through an ssh session? I run some of my ssh sessions on different ports as it's easier to configure on the firewalls. You'd have to do a man in the middle hijack to look at the initial handshaking, however to do that you'd have to spoof the TLS certificates. You see this with some WiFi connections as they try to manage the certificates and get it wrong. Also not everybody has an ISP. I've setup direct leased lines between businesses. Some people buy their lines. Some people pay to lay dedicated lines. I've had them explicitly laid down that follows certain routes in the road for redundancy so they go through roads. Some large companies have direct international lines. Some companies lease capacity on their lines at different times of the day and night. None of these use an ISP as they want to control what they do. How are you going to control those? The VPN genie is out the bottle now, its like saying to the ISPs to block porn. Too late, you can block the main sites but there are 10,000s of sites out there. You can't put the onus onto the ISP to do this, it would cost 10's of billions. The govt looked at this and backed off years ago. Netflix has tried to block VPN's and failed. There are simply too many and they change all the time. Also setting up a VPN on a home server is a true VPN. Just because its not sold or advertised doesn't make it any less of a VPN. It uses high grade encryption, if I wanted to use even higher grade, i'd probably go for dedicated hardware which isn't that expensive. There are so many different and easy ways to get around anything your ISP puts in place. Never underestimate the skills of a 16 year old boy wanting to look at adult sites. -
Will Basschat survive the Online Safety Act?
rwillett replied to fretmeister's topic in General Discussion
The only way to stop VPN's this is to put a UK wide firewall and take charge of every single communications line in the UK, thats every company leased line, every fibre line, every microwave transmitter, every homemade Pringles wifi (https://www.makeuseof.com/tag/how-to-make-a-wifi-antenna-out-of-a-pringles-can-nb/), every analogue modem line, every satellite link, ever type of mobile connection, every modem. You'd also have to stop people standing at Dover occasionally getting French mobile providers. You'd also have to stop all the ham radio people as well, You them have to route every packet through possibly the worlds largest firewall system (that would dwarf the Chinese one). Check every packet and see where its going. Oh and nobody can use https or any encryption as they need to see everything in clear. So the banks, military, lawyers would love that.... We'd probably have to build a new nuclear power station or two to run all this new hardware. You'd also need Cisco or Juniper or somebody to have a dedicated production line setup just for the UK. The legislation necessary to seize all these comms would also have to be rammed through Parliament without recompense as this is about £1T of value. We'd also need most people in the country to actually run this system. I suppose by this time we'd have a military junta in place so a lot of the legal stuff will have gone by the wayside anyway. I'm trying to work out the most obscure way to set an TCP/IP network that could run a VPN. Of particular note is https://en.wikipedia.org/wiki/IP_over_Avian_Carriers however I'm not sure how to integrate VPN into that particular protocol. As an intellectual exercise it's quite fun. Similar to Pave the Earth https://www.reddit.com/r/pavetheearth/ Of course this is just my opinion. Others may disagree. -
Will Basschat survive the Online Safety Act?
rwillett replied to fretmeister's topic in General Discussion
Unless you ban foreign based VPN’s thats a pointless activity. Anything like a white listed VPN isnt a VPN at all. i run a VPN system at home , i use it to access my home systems from abroad whilst not exposing any ports. I can chose the ports i use so no such rhing as standard ports to block. The Internet was explicitly designed to work around problems such as Washington being nuked and large swathes of infrastructure not being there. Unless the UK govt puts a firewall around the uk (aka China) and stops all traffic, it is a pointless activity. -
Will Basschat survive the Online Safety Act?
rwillett replied to fretmeister's topic in General Discussion
Since the govt uses VPNs all the time, unlikely to happen.