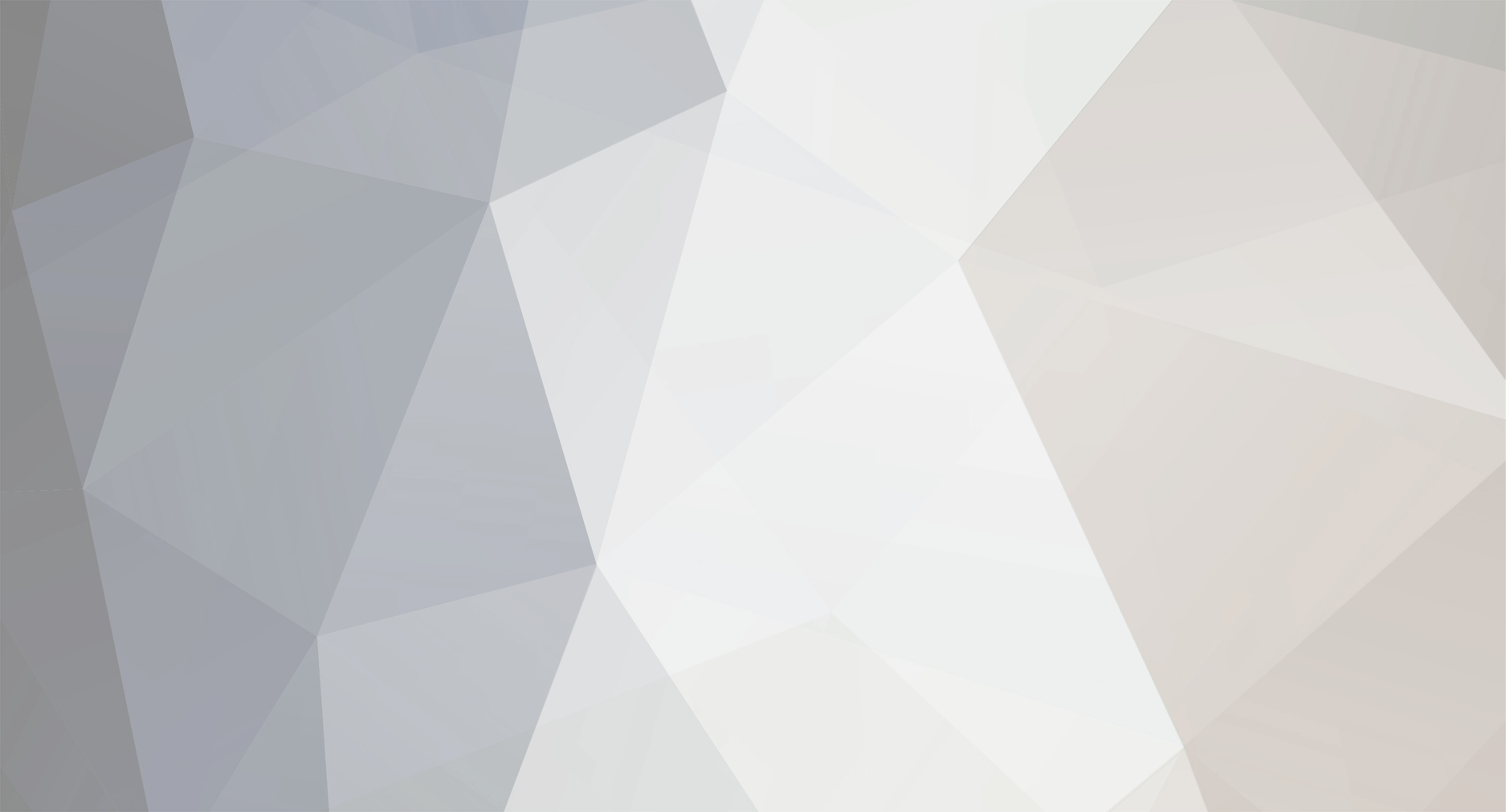
rwillett
⭐Supporting Member⭐-
Posts
1,616 -
Joined
-
Last visited
-
Days Won
6
Content Type
Profiles
Forums
Events
Shop
Articles
Everything posted by rwillett
-
I can print 250x220x220. Practically I'd do 240x215x2.4mm (ish). I can easily change layers so, black/white/black is not a problem, each layer being 0.7mm to 0.8mm. Cost would be negligible and I wouldn't want any money TBH. The issue is, whether the quality of the printing is what you are after. There are tricks to make it better, printing it top side down on the plate OR 'ironing' the top. Ironing does not mean we put a Phillips iron on, but its a special technique using the hot end of the extruder (circa 205-250C) to melt the surface using extra very gentle passes to make the quality better. Can work OK, I don;t use it because it takes a long time if you are doing a lot of prints. One of the issues I had with the original six string was to make the quality of the printing, whilst good for 3d printing, is not as good as I would like. The Prusa Mk4 printer is better than the Mk3 but it's not as nice as a new piece of pickguard in a shiny wrapper. Thats why I'm looking at buying a Dremel router table and some pickguard material. If you have a design for a pickguard, send it to me and I'll print it out. A design in Fusion 360 would be brilliant but a technical drawing with angles, lengths and radii would be OK,. Thanks Rob
-
That's very kind of you to say so. Thank you, appreciate that. However when I look at it, I keep thinking, need to change that, need to do this better. I was the same with IT development, never happy always thinking there's a better way to do it. It does play "Smoke on the water" really well (for a single E string). I am just about to dismantle it again and will shave off the excess aluminium, once that's done. I'll probably assemble it and then go into setup mode. I think the neck is a little too straight and need to get that sorted, but I've ignored all that for the moment. The pickups sounded great before, they should sound as good now. I've also just watched this video on making a pickguard. I can see a Dremel router table and Dremel Moto Saw in my future now. The video below gives me confidence I can make a pickguard without losing a finger or an eye. The woman talking is very good, no "umm's" or "ahh's", edited in a sensible manner, do dead spaces, no fluff or flannel. Wish a lot of people who make YouTube videos watch this to see how they should be made. Now I think about it, I saw another woman making some guitar stuff and she was good as well. Perhaps its a gender thing?
-
I'm actually now in a reasonable state with the six string. Body is done. It's only 34mm thick. As it's so thin, this presents other problems, such as the wiring channels are very narrow as the Voronoi shapes are thin, well that's the way I designed it so I can only blame myself. I designed the parts of the body to split in the thinnest sections to reduce the join lines. There are dowels in these joins to ensure that the parts align. The switch abnd control panels are now printed in situ and it looks a lot cleaner. Aluminium backbone is done. Previously I had screwed two aluminium plates together to form a T shaped. This is the "chassis" of the guitar and the body attached to the wings of the T. That's the holes on the side. I've now bonded the aluminium together using an adhesive for ships. If it can stand salt water and last up to 10 years, it'll keep a guitar together (I hope). This has the advantage of making this piece a lot simpler as no tapping and dieing and no countersunk drilling, contrary to what the diagram below shows. It also keeps the back of the guitar super clean with only four holes for the neck. The aluminium now has a matt brushed look on the back, it still shows some finger prints but I'll do another polishing round when the guitar comes to pieces yet again.... The wiring is all done, I tried very hard to keep the strands of the Voronoi as thin as possible and as the channels are printed in with no access slots, this makes copper tape cladding impossible, so I use a copper braided tube to encompass the wires as the wiring goes from the switch through the body of the guitar to the control panel. Of course, did I allow enough space for the wires AND the copper braid? No. Another lesson learnt and as I had glued the whole guitar up, it had to be thrown away and another body printed. That's around 30 hours and a roll of filament down the drain. Bridge is in and is as low as I can get it. The guitar body is 34mm thick which is 8mm of aluminium backbone, 3mm of aluminium plate on top and 22mm on top of body which is about the height of the pickups. The neck is around 26mm. That's it, I can't make it much lower unless I get or make very thin pickups I managed to find a low level BBOT and that seems to be OK. Pickups are Tesla P90's which are great. They are wired into a pair of volume/tone pots a la Telecaster Deluxe. I only have on string on at the moment to test the height of everything. Plugged it into a Phil Jones Bighead Pro amp and it sounded great (with only one string). I seem to recall playing Smoke on the Water. Seasick Steve eat your heart out Pickguards are a challenge. I have designed them but none of the 10 or so versions I've printed look like anything but sh1t. Currently it's sporting a Prusament Orange pickguard as that's the last one I tried and it doesn't look good. However being orange will force me to think of a better solution. Work to be done: Take it all to pieces to fix a 1mm excess bit of aluminium around the neck joint. Purely for aesthetic reasons but got be done otherwise I won't sleep. Find the three way switch washer and nut which I appear to have lost and could be anywhere in the debacle that is my desk. Buy a chunk of pick-guard material, probably white pearl, and work out how to shape it into a pickguard. If anybody has any good suggestions on how to learn to do this, I'm all ears. I have this guitar to do, another copy of this guitar as I'm making two of them. The second version is a solid body version which I'm making as yet another experiment. I also will be remaking my Fender Jazz copy, I need decent pick-guard for my current headless (which is a really, really nice bass to play). I'm also planning (in my head) a headless Thunderbird bass. I have all the parts but am stressing over cutting the neck down. So that's five pick-guards to make. I'd be happy to buy one, but if its five, I should learn how to make them. If anybody has any pointers to how they have done it, I'd be grateful. Check if I can get rid of the ferrules on the back of the neck. I have some smaller domed screws which I'm hoping are short enough. That would clean the back of the guitar up a lot. Replace the silver screws on the back for the access panels. Black M2 countersunk screws on order.
-
You could make them an offer they can't refuse. Then you can find out earlier What are they worth do you think? Rob
-
Got to be too good to be true, right?
rwillett replied to TheGreek's topic in eBay - Weird and Wonderful
It has more than a ring of truth about it, the reference to the upright bass and the p-bass is nice. No mention of it being an elderly relatives and he knows nothing about guitars or he found it in a cupboard. If I still lived in Greenwich, I'd pop round, check it out and rip his hand off (and take the bass as well). Sadly I'm a little too far north, Rob -
NDBD: Squier Affinity Jaguar H (first D is for damaged, not double)
rwillett replied to neepheid's topic in Bass Guitars
And I'm sure you'll make it eloquently and forcibly... Rob -
NDBD: Squier Affinity Jaguar H (first D is for damaged, not double)
rwillett replied to neepheid's topic in Bass Guitars
Sorry misunderstood. I suspect you can complain and you'll get nowhere. Apologies for confusion Rob -
NDBD: Squier Affinity Jaguar H (first D is for damaged, not double)
rwillett replied to neepheid's topic in Bass Guitars
You should not have to pay return postage https://hegarty.co.uk/legal-q-as/qa-an-online-purchase-arrived-faulty-will-i-have-to-pay-for-return-postage#:~:text=This is something the seller,the replacement goods to you. Their fault, they pay costs. -
NDBD: Squier Affinity Jaguar H (first D is for damaged, not double)
rwillett replied to neepheid's topic in Bass Guitars
It's going to cost them more in returns, paperwork, readvertising etc etc than £25. However that's their business decision. I think you are right to return it. -
Mag strips could well work. You need to look at the battery holder as a whole, lid and compartment. I would hope the screws go into a brass or metal bush, not into wood. That could be part of the battery compartment. I would expect the whole unit to be self contained with a hole for the two? battery leads coming out. The current lid appears to be a latch that you pull back with you finger nail and the lid pops open. I originally thought that was a hinge but is more likely to be a small flange that fits into a slot on the opposite side. The latch is designed to bend and will be probably made of ABS plastic. ABS is not a nice plastic to use or print with as it produces toxic fumes and needs to be printed in a heated chamber. A simple lid with four screws is still the easiest but until we get more pictures it's impossible to say more. I'm off to coach an u18s girls rugby team and will check in again this afternoon after coming back from Kendal. Rob
-
Just got a decent glue gun so that might work. Screws are easiest though as there are screw holes there already and even thin mag stripes add height, might only be a mm but that enough to be not flush. Still can't visualise what's needed though unless it's a simple lid with four screw holes.
-
I can probably print a lid. Not sure if I could easily put a hinge on it. Not 100% certain what this needs TBH. My knowledge of this guitar and the battery compartment is zilch. If it's just a static lid with four screw holes, then given accurate dimensions, including the radius of the rounded corners, that's pretty simple. It appears that what the OP wants is a lid with a border that screws down and a hinged lid inside of that that is latchable using a finger. That's more difficult. However I could be completely wrong and normally am... A simple lid that screws down is dead simple and could be designed and printed in a few hours. Anything with a hinge needs careful thought. The more info the better
-
Anybody pulled together a DIY FRFR speaker/CAB?
rwillett replied to rwillett's topic in Build Diaries
I was looking at pulling the trigger on a Yamaha HS7 but will now read this first. Thanks -
Thank for this. I'll get one ordered.
-
@Richard R Thats such a generous offer. I'll certainly swap my two, almost but not quite feral, cats who are at this point in time doing their best to decimate the mice, rat, and bird population of the village. The cats have no fear of anything and so rabbits and pheasants are also their targets. Its such a joy when they try to bring in a butchered and half eaten rabbit through the cat flap. I have a strong stomach, but not that strong. The only reason there are no foxes is that every fox, as far as I know, has emigrated to the local towns and cities as it's easy food there and because my two ninja cats aren't there. The cats also smell really badly and love dribbling on you at 04:30 in the morning if they can get in the bedroom and the dog hasn't noticed them. The dog classes the bedroom as his turf and tries to chase them out. They also throw up anywhere they can, and their litter tray and the 100,000 acres of Yorkshire Dales literally outside the door,is ignored if they can find a corner of the house to poop in. The vet bills are enormous as well. So I accept your offer to swap cats. I'll be there in around 15 mins. Thanks Rob
-
Looks good. Keep us informed
-
These are when I do my design work in Fusion 360. I've developed the ability to track the call mentally in the background and to anticipate when I need to speak.
-
NDBD: Squier Affinity Jaguar H (first D is for damaged, not double)
rwillett replied to neepheid's topic in Bass Guitars
Those two look very purrty (sounds of six fingered banjo playing in the background). You must bring them to the bass bash. Do you need a van yet? Rov -
A boring MS Teams call....
-
@fretmeister How was the Tonex with the Yamaha HS7 please? I have a Tonex 3 button version and was looking for something smallish for home use. Don't need massive volume at all, but wanted something small that I can use the Tonex with both bass and guitar. Thanks Rob
-
Anybody pulled together a DIY FRFR speaker/CAB?
rwillett replied to rwillett's topic in Build Diaries
I thought I knew which thread you were referring to and after looking for it, I realise I have no idea which thread you mean. There's quite a lot of threads that this could be, any pointers welcomed. Thanks Rob -
Anybody pulled together a DIY FRFR speaker/CAB?
rwillett replied to rwillett's topic in Build Diaries
@JPJ Thanks for the reply. I have read the the 1x12 design thread, but for some reason I missed the bit about it being pretty much an FRFR design, my bad My knowledge of suitable PA amps to pair with the 1x12 design is slightly less than my knowledge of kitten surgery, I dabble as does everyone, but I'm no vet I'll ask in that thread. I did note that somebody had put a small amp with the speaker to make a combo, my intention is to make this simple (once complete) and reduce leads, power cables and what not. Thanks Rob -
Hi, I can see a number of excellent build diaries for cabinets, but haven't seen anything about building a FRFR speaker/cabinet. Given the wide number of relatively cheap class D amps that are around, I would have thought that the more technically minded would have turned their minds to this. My reasons for looking to a FRFR speaker are: 1. I have limited space as t'other half doesn't want the house "cluttered with your crap". 2. I play bass and guitar (equally badly) and would prefer fewer things. 3. I have a Tonex pedal board AND a Mod Dwarf pedal board and would like a decent FRFR speaker to use with them, especially the ToneX. 4. I don't want really want a (supposedly) 2000W Headrush 212 FRFR speaker or a Spark Cab or a Katana Boss or Spark 40 and not use the modelling element. 5. I fancy doing something along with building guitars. <-- This may be the actual reason. Any links or suggestions welcomed please. Thanks Rob