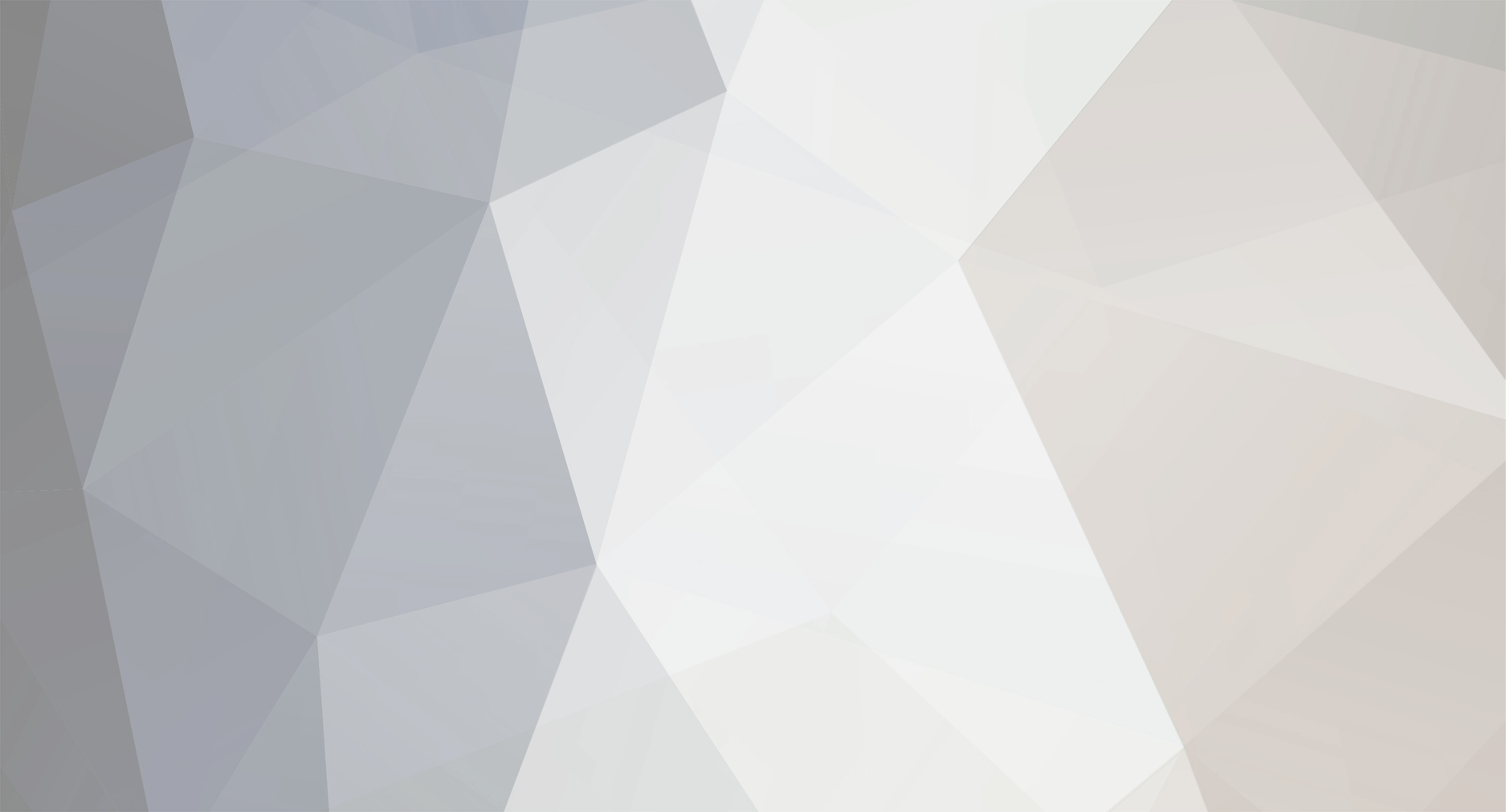
rwillett
⭐Supporting Member⭐-
Posts
1,489 -
Joined
-
Last visited
-
Days Won
5
Content Type
Profiles
Forums
Events
Shop
Articles
Everything posted by rwillett
-
Not forgotten
-
As I need something to keep me going during some hairy times at work, I thought I'd build a simple type of rail guitar. I also wanted a small, light(ish) travel guitar. Unsure at the moment if this is a headless or headed which is not actually a big problem at the moment (or I don't think it is) The Westone "The Rail" is an inspiration but nothing more than that. There's a separate thread on how the earth grounding works on it elsewhere So far I have the mental image in my head, I have an active EMG precision bass pickup(s) which I brought from the parish, but I've never used it or even tried it so who knows. I've got a headless bridge and neck bits and bobs as well as some aluminium tubing to test this out. If it works, I suspect I'd use stainless steel tubes. Printing the stuff is no problem, and I have worked out how to keep build the strength in with some clever (and simple) design (and some more aluminium). The neck will be either an Ibanez TMB100 (I think) if headless or an Aria with Hipshot tuners if it has a head. I'm tending to think it will be headless. The design is based around the pickups working outwards. All my other guitars are from the outside in to get the right curves. This has no curves and is extremely functional. So here's the pickups layout. I need to add in the tone and volume controls as that's what the EMG has. That will determine the width and then the neck and bridge just follow on depending on the scale. What could go wrong ? Rob
-
Westone "The Rail" Bass - A down to earth question
rwillett replied to rwillett's topic in Bass Guitars
Thats helpful and does seem to indicate that the screw was connecting and possibly grounding on the metal tube. I've worked out a way to do it that isn't too complex (or I think I have). I'll build this from the pickup outwards. I have a a choice on an Ibanez neck of some description or an Aria PRO II Std one with Hipshots. One advantage of a rail design is that its quite easy to adapt between headless and normal necks. I suspect though that it might be headless though and the Ibanez might be sacrificed here. Decisions, decisions, decisions... Rob -
Westone "The Rail" Bass - A down to earth question
rwillett replied to rwillett's topic in Bass Guitars
Oddly enough I have that sitting on my desk -
Westone "The Rail" Bass - A down to earth question
rwillett replied to rwillett's topic in Bass Guitars
When I searched for this earlier, a lot of the responses say that the bridge should be grounded. A few say it makes no difference but a number of sites state it is essential to reduce hum and for safety. https://www.google.com/search?q=do+guitar+bridges+need+to+be+grounded+safety&num=10&client=firefox-b-d&uact=5&oq=do+guitar+bridges+need+to+be+grounded+safety We are going slightly off topic here, but I'm interested in safety as its me. A statement such as "There is no safety issue (and an argument the other way)" could do with being expanded as I couldn't see anything that said grounding the bridge could be dangerous. I am not an expert in electrical stuff, so I'm trying to follow best practise here. I recognise that t'internet is sometimes wrong so I'd be interested in finding out why. Thanks Rob -
Westone "The Rail" Bass - A down to earth question
rwillett replied to rwillett's topic in Bass Guitars
I read that with great interest. A good insight into how things were done. -
Westone "The Rail" Bass - A down to earth question
rwillett replied to rwillett's topic in Bass Guitars
The point is how are the steel rails connected to a sliding middle section. Something that rubs against the rail is a poor option as the rails will have grease from fingers. A friction type of option is not elegant and I don't think Westone would do that. My 83 westone guitar is very well made I'm struggling to believe Westone just allowed something to rub against a rail and also some of the rails may be powder coated so that can't be the option there. I could be wrong but I would like to get to the bottom of this problem with a definitive answer. Thanks Rob -
Westone "The Rail" Bass - A down to earth question
rwillett replied to rwillett's topic in Bass Guitars
Still unclear as to how it's earthed though. Given various regulations around the world I would have thought legislation would insist on it. -
it's a while since one of these came up... Westone Rail.
rwillett replied to alyctes's topic in eBay - Weird and Wonderful
Too expensive for it's condition fo me. -
Westone "The Rail" Bass - A down to earth question
rwillett replied to rwillett's topic in Bass Guitars
Thanks for this. It does look like the bridge isn't earthed. One way to check would be see if there is electrical conductivity between the bridge and the ground on output socket. My thoughts here are NOT to build a Westone clone and replicate crappy electrics, but something a little more interesting. I've got decent pickups and decent pots so the electrical side isn't an issue. Building the open nature of the bass is more of a challenge but I've some ideas on how it might work and look. Thanks Rob -
Westone "The Rail" Bass - A down to earth question
rwillett replied to rwillett's topic in Bass Guitars
Seen the diagram. Doesn't show if the bridge is earthed sadly. Thanks Rob -
Westone "The Rail" Bass - A down to earth question
rwillett replied to rwillett's topic in Bass Guitars
It's a puzzle -
Westone "The Rail" Bass - A down to earth question
rwillett replied to rwillett's topic in Bass Guitars
@Stub Mandrel Nothing I've seen shows a contact strip in any picture. If one tube is hot and the other earthed then surely that would create issues if you touched both parts? the current is virtually zero, but your body would interfere (I would think). Rob -
Westone "The Rail" Bass - A down to earth question
rwillett replied to rwillett's topic in Bass Guitars
Hi Si That would probably scratch the tubes, but not definitely. Rob -
Westone "The Rail" Bass - A down to earth question
rwillett replied to rwillett's topic in Bass Guitars
That might be how it's done but that would probably also scratch the tubes and I've seen pictures of immaculate guitars. No scratches at all. Its a puzzle and I can't work it out. It might be that the bridge isn't earthed but I'm sure there would be hum. Rob -
Westone "The Rail" Bass - A down to earth question
rwillett replied to rwillett's topic in Bass Guitars
Yes it could be, but in earlier pictures of the Westone it has different coloured rails. These might be anodised (and probably are), but a piece of copper braid rubbing against the tubes seems a poor way to do it in my book. The tubes will have oil on them from your fingers and would very gently scratch the anodising or the lacquer or whatever. I would have to do something like this if I built it, but it doesn't strike me as an elegant solution. However I might be wrong and this is the way Westone did it. Rob -
Westone "The Rail" Bass - A down to earth question
rwillett replied to rwillett's topic in Bass Guitars
I don't have any machining capability, though I think you are right, polished titanium would be fabulous. I'll just see what my daughter would fetch on eBay to be able to buy the titanium blocks needed The aluminium backbone works for 'traditional' guitars but wouldn't work for this as it needs to be empty in the middle. The issue at the moment is the shear loading on the parts of the neck and bridge where it connects to the metal tubes. There's circa 160+lbs coming from the bass strings and that will break a 15mm plywood backbone and bend 12mm aluminium. Already tried that, so there a lot of stress in certain areas of the guitar. I need to work out what the "art of the possible" is here. I've a number of ideas to explore. Rob -
Westone "The Rail" Bass - A down to earth question
rwillett replied to rwillett's topic in Bass Guitars
@Maude From reading various descriptions it's wood. 3D printing on it's own would not be strong enough. You can't make even a six string by just printing it. My six string and my headless both have an aluminium backbone. This works very well and the sustain is excellent. However the two steel rails will add a lot of strength, and will be somewhat of an alternative to alumnium backbone but will move the forces elsewhere. I'm interested in seeing what the shear forces would be if it's just printed. I *think* that it's not going to be strong enough TBH, but I'm happy to experiment. I also have a Plan B Rob -
Westone "The Rail" Bass - A down to earth question
rwillett replied to rwillett's topic in Bass Guitars
Hi John It is another 3d printing project. If I do it, I'll design an earth for the bridge to the rails. That's the easy bit. It's how a sliding middle earth's (if necessary) thats making me think. I have some simple ideas but am interested if Westone had this issue and how they resolved it. I'll keep thinking it through. The next thing is how strong the bits need to be. The loading of a four string bass between bridge and neck is circa 4x that of a guitar. Previously I have used an aluminum slab as a backbone. That won't be an option here as the load will be taken by the side tubes. However these have to connect to the bridge and neck and that's a lot of stress. Probably the only way to check this is to do it and see 😊 Rob -
Hi I'm looking at building something similar to the Westone "The Rail" bass. Not 100% certain yet, but exploring the idea. It won't look quite like this but I wanted to see what the smallest bass I could make. I can see how it fits together and nothing strikes me as too difficult at the moment, famous last words, apart from where things actually earth on the above basses. AFAIK there is normally (always?) an earthing strap/wire/connection from the bridge to the electrics to reduce hum. All the guitars I've built have that and all the ones I've taken apart have that. I can't see how that works on the guitars above. I know the black side pieces are steel tubes so I would assume that they are involved but the pickup in the middle slides up and down, so there's no wires that connects the bridge to the pickup. Does the pickup section use a friction connection to make the earth OR has Westone found a way to get around the hum using something else? Searching for Westone "The Rail" wiring diagram doesn't produce anything very interesting. Anybody have any ideas how it works. The only thing I can think of is a piece of metal that clamps against one of the steel rods when you tighten the pickup in position with the screw. That might scratch the rods though. Thanks Rob
-
A choice of 2 - which one will you buy ?
rwillett replied to edstraker123's topic in eBay - Weird and Wonderful
I think somebody ought to make the ultimate sacrifice and buy both. They can then hide them by burying them, a bit like Jumanji. This way we can make sure nobody else ever buys them by mistake. What could possibly go wrong? Rob -
DIY Pedalboard - 3d printed & Aluminium Extrustions 400mm x 300mm
rwillett replied to rwillett's topic in Build Diaries
What I do is setup the iPad for what I want. I do this on the desk. This gets saved as a user preset. This was designed as an exercise in packaging and something I could easily take away. I don't tend to change too much from the preset, if I want a slight change, I'll create another preset. The M-Vave foot switch simply moves up and down the presets, plus things like a long press, turns the tuner on and off. Its small, compact and battery powered, easily fits into a small case, and is surprisingly versatile. Is it as good as some of the higher end stuff? Probably not I do have a Behringer X Touch Mini controller as well but its a fag to setup. I agree that touch screens are sometimes a pain, my Seat Leon has a touch screen and I hate it for all the reasons you say above. Rob -
DIY Pedalboard - 3d printed & Aluminium Extrustions 400mm x 300mm
rwillett replied to rwillett's topic in Build Diaries
I can't seem to leave things alone. So I wondered how small I could make a pedal with a battery and a audio interface. So it's now down to 12cm x 11cm x 10cm. So that's a significant reduction from 26cm x 9cm, basically half the size. This new version also allows me to see all of the battery indicator lights and to adjust the iRig input and output controls. It does have a smaller battery than before but it should last 6-7 hours which is far longer than I need it for. It is bigger than a Helix Stomp or a Mod Dwarf or a Line 6 but it's portable and stands me at £15 for a new battery as I had all of the other parts lying around. The iPad display does make it very easy to read and the interface is so easy to use. I can use either an older iPad or an older iPhone 11 that sit on an adjustable rod to get the right angle. The iPad is the easier to use as it's so much bigger display. I have a M-Vave four switch pedal unit which works across Bluetooth. That gives me eight options with short and long presses. It sounds very nice with the Yamaha HS-7 speaker. I tend to use BiasFX2 and I'm experimenting with Loopy Pro. Sorry no banana for size. Rob -
Agreed but I'm still a moron