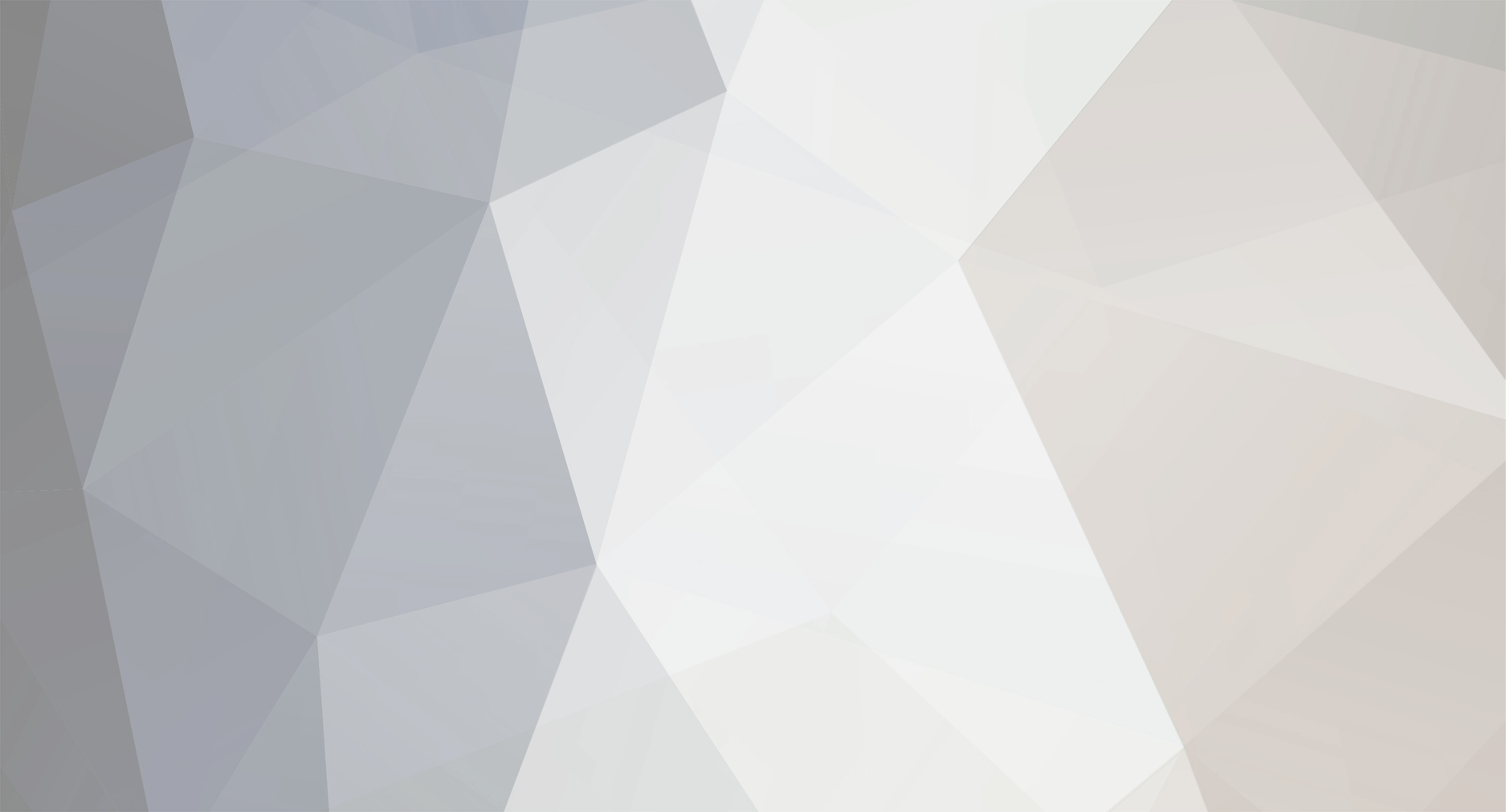
rwillett
⭐Supporting Member⭐-
Posts
1,497 -
Joined
-
Last visited
-
Days Won
5
Content Type
Profiles
Forums
Events
Shop
Articles
Everything posted by rwillett
-
The Pi 4is fine for non GUI use, so make it a proxy server or an Octoprint server (TBH it's over powered for an Octoprint) or anything where it doesn't need to run a large GUI. A retro games server, it's also a pretty good file server if you can get a decent NVME or SSD on it. The Pi 4 is a lot more powerful than the Marvel chip I had in my Synology server, I reckon my washing machine had a faster CPU. No issues as a webserver or to learn python or whatever you fancy. Rob
-
Didn't know that. That could be an expensive mistake to make
-
Spot on....
-
If you can, get an Octoprint server setup. A cheap PI 3 is more than adequate. Saves a lot of time and makes a massive difference. @SamIAm is spot in with her description. First thing I did after unpacking the printer and before I even plugged it in was to setup a Raspberry Pi as an Octoprint server.
-
I have a 3d scanner but not set it up yet. It was Kickstarter from last year. It's on the list but making a bass took priority
-
It is very quick. Just printed at 0.1mm layer, best it can do and the quality is very, very good indeed. This Input Shaping is quick and good. Still need to play and explore the limits.
-
I even checked this with my accountant and she was happy about it. The Pi 5 is the first Pi that is actually fast enough for day to day usage and not a toy desktop. The Pi 3 is a great Octoprint server and the Pi 4 even better. I use the 4 for Astrophotography and its fine for controlling loads of things like cameras and mounts. I have tried each of them for desktop use, and you could use the Pi 4 for ssh work and it was fine. The moment a GUI was put on, down it went in performance. The 5 works well, still nowhere near as fast as a good Windows or Mac machine, but it's about £80 from memory. I'd still like a 16GB version though. I'd always go more memory over more CPU power. If anybody wants an Arduino R3, lightly used, let me know and I'll pop it in the post. Rob
-
This is my R&D budget agreed with the business. I will admit that I own and run the business, so I approved the R&D request. I did ask some pretty difficult questions of myself to justify the time and money though. It wasn't an easy decision and I had to weigh the pro's and con's up. Business is tough these days.
-
IMG_2667 V2.mov here's how quick it is. No idea how to reformat it in the thread so it's smaller. I downsized it to 480pts on my Mac but not sure how to make it tiny here. Rob
-
I have finally managed to get some progress on the winder, its basically a number of sideways steps but at least they are not backwards I got an Arduino R4 (with Wifi no less) to see if the increase in speed would help driving the stepper motors at a faster speed. I decided that simply moving to the R4 from the R3 was too easy, so decided to move my dev environment from an old Macbook (2013) to a Raspberry Pi 5 (8GB) but running a CF card and not an NVE so speeds a bit slow. However it's a proper UNIX box and is dedicated to this. I also decided not to use the Arduino IDE and move to the command line and Emacs. I feel a lot happier with a decent editor and TBH prefer the command line. Its just a quicker way of working with Emacs as you rarely take the hands off the keyboard. Pretty simple as well, I've only taken 30 years to learn it properly. The issue then was that nothing worked on the R4, no LCD display, no keyboard input, no stepper motors. It turns out that the R4 breaks a lot of Arduino libraries. So I started with a blank sketch and simply got the LCD to work. That took a little bit of fiddling about but that worked. The next step was to get the keypad to work. No matter what I did, it looked like random key presses coming down the line. Turns out the R4 has a different set of resistors on their circuits and a simple fix (that took a long time to find) was all that was needed and then I had keypad AND a display. Motors were a pain and nothing worked. It turns out that the AccelStepper library which is pretty much a standard doesn't work at all.It also appears that not many people are using an R4 with stepper motors, but a couple of people responded to my plea for help and a pointers to a working library and I ended up with MobaTools, a library aimed at model railways Their sample sketch also included a wifi server to control the R4 from a website, after a few attempts to get the stepper motor pins right on the CNC Shield and in the code, I got motors to turn, not only did they turn, they turned fast. I managed to go from 6 revs / sec to approx 20 revs / second. Thats 1200RPM. There is no load and nothing else happening so unlikely to keep that speed but thats 3x the max I got from the R3, so I'm a very happy bunny. I need to merge all of the different bits of code together and see if it still works, thats the forward step Rob
-
The auto leveling works very well. The setup consists of tapping the cold nozzle with your finger tip and that was it. It only checks the bed level for the area being printed as well. So that's nice. There already is a replacement firmware that might address the display issue and lack of code. I thought I'd wait at least 24 hours after getting before I hacked the firmware around 😊 It looks like the filament sensor is a big issue for a lot of people. It's been reported on the Prusa Original XL. They start at twice the price of a MK4 and go up a lot more depending on number of print heads. They are enormous though. I'm struggling to understand why it's such a problem but clearly Prusa haven't solved it. Rob
-
I've just taken delivery of a Prusa MK4 to replace one of my MK3S+ 3D printers. A quick heads up in case anybody is thinking of buying one. I've done a load of test printing and there's good and bad. The good is the speed and the quality. It's so much faster than a MK3S+, nearly twice as fast on some pieces. The quality also looks very good indeed. There are new things such as Input Shaping that I haven't got my head around yet, but I'll learn. The bad is that Prusa appear to have deliberately crippled Octoprint to work with it. Octoprint acts as a print server, normally runs on something a Raspberry Pi and provides a fabulous wealth of plugins for users such as emails when the print is finished or when filament needs changing. Octoprint can also drive the front panel of a MK3S+ so you can see how long is left and other usefyk stuff. Prusa doesn't support the specific gcode for that, so the front panel on Mk4 looks very simplistic (see above). It was supported so I think Prusa is pushing towards Prusalink, they can forget that as I'll simply reuse an old tablet for the display and ignore the front panel. There also appears to be a long running issue over the filament sensor not working properly. It detects the filament is out but sometimes doesn't recognise the replacement filament and keeps saying put it in. I had it twice when I tested it but not actually reoccurred for the last 8-10 tests I then did. I'll keep an eye on that. Very, very dissapointing from Prusa. The ticket on it started 6/7/2023 and its still not resolved. Just had anotehr look at a test print and it is very, very good with Input Shaping. .
-
I am reasonably sure it's deliberately designed like this.
rwillett replied to alyctes's topic in eBay - Weird and Wonderful
I'd suggest this as a stand for it -
So long as they use it, thats great. I don't want to give them something that sits in a corner and isn't used. Thats the only criteria. I've downsized some guitars to them as well. If I don't use it, I'd rather somebody else did. I've seen a few of them in use at concerts which is great. Kids break things as well, so I suspect they go through lots of stuff. Rob
-
I am reasonably sure it's deliberately designed like this.
rwillett replied to alyctes's topic in eBay - Weird and Wonderful
He also has three of them... somebody made one of them and thought... "Do you know what the world needs more of? Expensive, hideous and unusable bass guitars with really nice hardware." So they went and elevated their first "mistake" into a crime against taste. If I ever find out who did this, I'd give their care worker and their guide dog a dammed good talking to. Rob -
Santa has come early this year, FedEx have just dropped off a little surprise I'm doing so much printing that I needed a faster printer and better printer, so my old Prusa MK3 which has been upgraded and upgraded and upgraded is now being donated to the local school. Nothing wrong with it, but its a pain changing nozzles, it's not as fast and I wanted to see if the quality was better in Mk4's. I wanted an Prusa Original XL which has a 360mm x 360mm build plate but a) it was circa £4K and b) its enormous. Its ready to be installed once I read the instrucitons and Prusa 2 finishes it;s last ever job for me. Thanks Rob
-
@SamIAm Makes me think of a new book "Famous Five go mad with 3D printing". This is the version of one piece of the body, due to the shape it's full of support. Just no getting around it. The red is the stuff to keep, the blue is the stuff to discard. This took 12 hours to print at 0.3mm layers, the thickest I can get away with. Moving down to 0.15 will give better quality but take 24 hours. I have seven of these types to do for an open body and seven for a closed body So 14 x 12 hours or 14 x 24 hours of non stop printing. So no mater how rough the body is, printing and sanding is a lot quicker than printing high quality.
-
I am reasonably sure it's deliberately designed like this.
rwillett replied to alyctes's topic in eBay - Weird and Wonderful
I presume the circa £2K is given to me to take it away and burn it. -
I've done an awful lot of printing these week to see how I can get a good finish. I've also redesigned things so that body is chamfered on both sides. This involves printing the body on the side so its upright, There are two strands of work. Designing and printing a solid body as opposed to the open body previously used. Designing and printing a very open body with large spaces. Both have pro's and con's. A solid body is far, far easier to sand and finish. as there's really only two surfaces, front and back. The open body looks far better but all surfaces need to be finished and thats hard work. printing in 0.2mm or even lower resolution reduces the layer lines but does not eradicate them. I'm going to get some printing resin (not filament), mix it with baby powder and brush it on the parts. This acts as a slurry and *should* make sanding easier. I'll need a UV torch to cure the resin as nobody makes a cheap extra large UV curing system (600mmx600mm) and whilst I can make one (another rabbit hole to pop down), I want to test the idea out first. Other people have shown that it works OK and simplifies sanding, which is good in my book. Here's the solid body design and the (very) open body design Ignore the lines in the model, they are the join lines. Printing time is much the same as I need to print supports and thats time consuming. And here they are being printed. I'm going to move to gray filament as it's so difficult to see the black This should be sprayable so perhaps some new bright colours can be used.
-
@zbd1960 It was good to see you. Sorry about the anxiety, not sure what we could do to help, but please let us know it we can do anything. The picture makes the village hall look like some medieval long hall which is nice. Thanks Rob
-
As per subject title, need to speak to a site admin about a new account that's been setup. May be legit or may be not, hence the DM Thanks Rob
-
HEADLESS BASS Bridge - Top down tuning system by RIVIERA Gear
rwillett replied to RIVIERA Gear's topic in Bass Guitars
Everytime I see a headless bass (or make one) I think thats clever, there can't be another way to do it and I get proven wrong time and time again. That's very neat, very elegant and that gets my nod of approval. A bit like a Paul Hollywood handshake but significantly rarer. I very much like that. Rob- 13 replies
-
- 1
-
-
- headless bass
- bridge
-
(and 3 more)
Tagged with:
-
Damm, won't post it otherwise perfect.
-
Thats the killer part of this
-
Accidental dupe