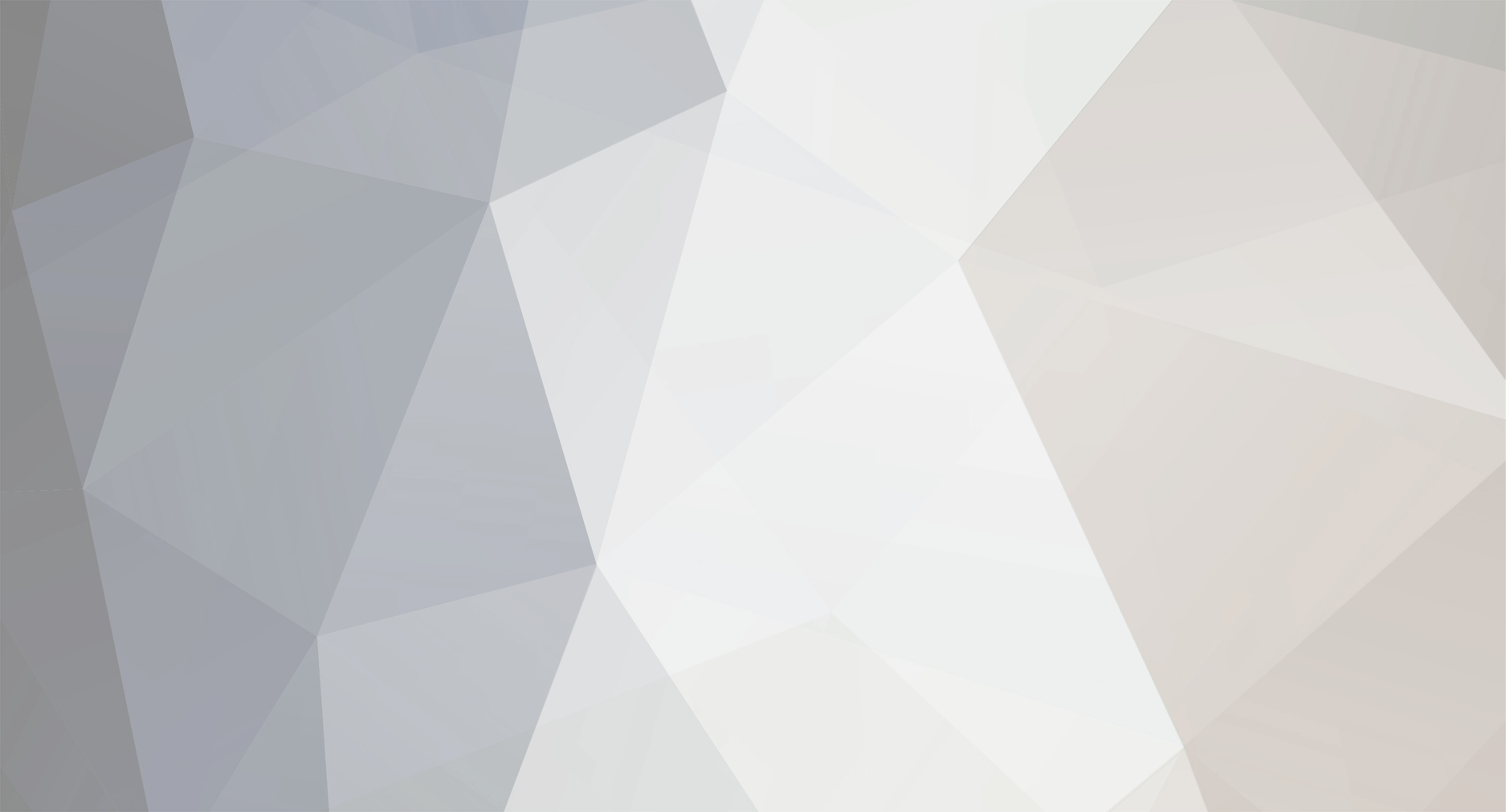
rwillett
⭐Supporting Member⭐-
Posts
1,605 -
Joined
-
Last visited
-
Days Won
6
Content Type
Profiles
Forums
Events
Shop
Articles
Everything posted by rwillett
-
The F2 was a proper camera. Many of the newspaper photographers used the F2, Canon started eating into that market with the Canon F1. A bloke tried to mug one of the photographers I knew for his F2. The snapper slugged him round the head with the F2 knocked him out and then took pictures for the newspaper and the police. Old school camera and one of the finest cameras ever made. Suspect your 72 has appreciated more as a mint F2 even with the 85mm f1.8 is around £600 now. Mind you that F2 will still be working long after termites and cockroaches have taken over the world.
-
Let me think, Andy Baxter vs Trash Convertors? Tough call
-
Somebody may think that they have a bargain. Without a whole load more photos, I don;t think anybody here will drop that some of money on it. I'm absolutely no expert so will leave it to others to comment on the tiny minutae that makes this a genuine bargain or a bitsa.
-
I've been offered a £5 discount if I buy it. It's definitely back on https://www.ebay.co.uk/itm/145890094925?mkcid=16&mkevt=1&mkrid=711-127632-2357-0&ssspo=Zpnag6mYSVu&sssrc=4429486&ssuid=70h8JO93TH6&var=&widget_ver=artemis&media=COPY Tempted... If I buy it as an act of charity, it stops somebody else buying it by accident. It's a selfless act... Decisions...decisions...decisions
-
That sounds like a lot of complicated electrical connections all waiting to go wrong Good luck to them, perhaps thats why it takes so long to make. Rob
-
Ok, thats useful to know. I wonder how it handles bending or slap?
-
You can't have zero latency, unless that have magically changed the laws of physics. Some sort of "spooky action at a distance". I can't see how they get such low values. The string has to be played, the pickup has to register the string is vibrating, something has to work out the frequency which requires an element of sampling over a period of time. C is 440hz which so a string vibrates 440 times a second, so two vibrations in 1/220 of a second. That's 0.05 of a second (ish). Even a battery powered CPU or chip can do a hell of a lot in 0.05 sec but doing it accurately and for even lower notes is quite a feat.
-
I've spent the last three weeks working out the best finish for 3d printing. Whilst you can sand and fill and spray (repeat as necessary), that's hard work. So have tried to use 3d printing to get the quality up so it looks good. The issue I've had to overcome is that the body has an angle on both the top and the bottom as well as the edges being rounded (or filleted). 3d printers obey the laws of gravity, so when you have an overhang, it has to be supported. Nature abhors a vacuum and 3d printers abhor stuff sticking out without a support. A support leaves traces of the support on the material, and a complex shape such as part of the guitar below doesn't have a single dimension that doesn't require some support. I think I have managed to get it so that the top is smooth and speckle free and the back is slightly grooved, which is fine. The new Prusa Mk4 is very quick and I can test this out. The downside to it being very quick is that I have gone through a fair few rolls of filament. Mr Amazon has a beaten path to my door. The other thing I have been working on is a simple system for attaching pickups and easily adjusting them. My aim was to take "standard" pickups and design a system so that most (but not all) pickups can be easily added and easily adjusted using carbon fibre rods. managed to get some Carbon Fibre in at last. They are astonishingly light and rigid, 3mm rods do flex, but not as much as I would have thought. This is the dark brown below and the red pickups are there to see how much adjustment I have. As the body oft he bass is now 38mm vs 45mm, I have made life difficult for myself, but lets see if I can fit it all in I've also been drilling aluminium and taping it with M2.5 and M3 holes. Thats a tedious job. Each hole has to be drilled twice, a pilot hole to go through double materials, one material has three different taps, then countersunk (very slightly), the other material has a different sized clearance hole. Repeat for many, many holes. I still need to redo the electrics, but thats relatively easy in comparison to drilling and tapping. Rob
-
I love the disco ball and might corporate it in my next printed guitar.
-
This is a bass with a lot of potential https://www.ebay.co.uk/itm/145885846114?mkcid=16&mkevt=1&mkrid=711-127632-2357-0&ssspo=Zpnag6mYSVu&sssrc=4429486&ssuid=70h8JO93TH6&var=&widget_ver=artemis&media=COPY rob
-
Perhaps we can do a smaller quarterly one or every six months?
-
- 10 replies
-
- 2
-
-
-
- guild
- semi acoustic
-
(and 1 more)
Tagged with:
-
Just to echo what @WinterMute has said, get as much RAM as you can afford. None of the M series Macs allow you to upgrade RAM as that type memory is part of the main CPU. So the days of slipping in an extra 16GB as you can afford it are long gone. Personally speaking I'd get memory over CPU every time now. Whilst you can run an older version of Logic Pro on the older laptops, I run an older version on my 2013 MacBook Pro, I have a feeling that its quite difficult now to do this as you have to buy the new version on a newer Mac which then allows you use the older version on the older Mac. So you *may* need a newer Mac for a while. I would certainly investigate this further before putting any money down on an older piece of kit just to be safe. The older Macs do work very, very well. though. My 2013 Macbook Pro was used every single day for 8-10 hours for 6-7 years. The keyboard is fine, there are 2-3 dead pixels now on the display, but you don't notice it in use. I only keep and use it really to annoy some of the other people in the teams who have the latest and greatest MacBook Pro which is quite an expensive beast now. If you do want to buy a second hand mac, I would suggest the following: 1. Check the battery %. If it is less than 90% after being charged up all day/night, assume you need a new one. Check the number of power cycles. These can be expensive from Apple. They are more expensive from Amazon as the vast majority of the batteries for old Macbooks are made from second hand batteries and are junk. Learnt that lesson the hard way so you end up buying more of them. They aren't that difficult to change, but it needs some care and attention. 2. Carefully check every single key on the keyboard. The Mac keyboards are excellent on pre 2015 models and after 2021. The middle years are very iffy as they changed the mechanism. 3. Load up a graphics program and make a few solid colour backgrounds or windows. e.g. Red, Green and Blue. Then move that window around the screen to check for dead pixels. Most of the time, you won't see the dead pixel as the screen has different colours but this can find dead pixels quite easily. 2-3 aren;t an issue, 20-30 might be. 4. Check the USB and HDMI connections are OK by plugging stuff in.Sometimes crap gets into the sockets and stops them working. 5. Check the PSU whilst its working. Is it too hot, people scrimp and save and use an under powered PSU. A 3rd party PSU is not a problem, but make sure its the right rating. Unplug the PSU and watch the battery percentage for a few minutes to see if it goes down a lot. My old Macbook won't last more than 45 minutes without being plugged in as the battery is rubbish now and I can't find a decent replacement. 6. See if the lid on the Macbook opens smoothly. Never seen one go wrong, but I have heard of it. If in doubt ask on here. There are loads out there for sale, if you pass on one, don't worry, another one will be along soon. Rob
-
If your budget can stretch to the newer Macs, I'd suggest one of the new Apple Silicon ones rather than Intel ones. Apple is pretty good at keeping their old stuff going but eventually they will end of life the older Macs. Hence the newer CPUs might be better. Apple kit also tends to last physically. I still have and still use a 2013 Macbook Pro as it works OK. Bit slow now and on its 3rd battery. Anyway, I tend to buy apple refurbished. Bit cheaper, dame guarantee and you'll not actually know its refurbished from Apple. https://www.apple.com/uk/shop/refurbished/mac Any of these will run Logic Pro. Rob
-
I don't think that the accordion is many people's fave instrument ...
rwillett replied to Angel's topic in General Discussion
I never thought I'd ever say "Bravo, more, more..." to a bagpipe and accordian duo. I didn't have that on my bingo card for this week... Wonderful playing, skilful and the accordian player was in a world of his own. I am humbled by what you can do here. Rob -
I don't think that the accordion is many people's fave instrument ...
rwillett replied to Angel's topic in General Discussion
Now I've got Stairway to Heaven played on an accordion in a Bulgarian wedding style running round my head. It'll be there for hours now That's psychological torture. -
I don't think that the accordion is many people's fave instrument ...
rwillett replied to Angel's topic in General Discussion
Shades of "I'm sorry, I haven't a clue" there. -
I don't think that the accordion is many people's fave instrument ...
rwillett replied to Angel's topic in General Discussion
Another sign out of view probably said "No playing Stairway to Heaven" -
Moved the Pi 5 to a metal case with NVme so this case is no longer needed. Its the 'official' Pi 5 case for what its worth. It clips together, has a fan that clips in, and it holds a Raspberry Pi 5. Difficult to work out what else I can sat about it, apart from it's raspberry and white coloured. Free to anybody who wants it. Postage is probably a £2.
-
- 2
-
-
I would suggest that people look at it from both sides. The seller knows they have sent it, they have the tracking information, the courier claims they dropped it off, the buyer says he has nothing! The seller has no way to know what's really going on, the courier has lied through their teeth but neither the seller or buyer really know. The seller is in just a big a bind as you as they rely on the courier information. You both think you are in the right and according to the information you have, you are. The dodgy person here is the courier. Personally speaking I wouldn't leave negative or neutral feedback. You've got the amp, it's been a pain but move on. The learning lesson is don't use cheap courier companies. P2Go are bottom feeders here. I am not the seller just to be clear.
-
The Short Scale Bass Appreciation Society!
rwillett replied to Baloney Balderdash's topic in Bass Guitars
I like those. Very much. Very, very cool. -
Just seen the last pictures of the neck. Nope step too far for me. Thanks though
-
My mum lives in Chesterfield 😊 thanks for thinking about me.
-
I don't think that the accordion is many people's fave instrument ...
rwillett replied to Angel's topic in General Discussion
I lived in Hamburg for a while, mid 90s. I lived with people my own age, young professional programmers, slightly nerdy(OK completely nerdy). Ultra cool when going out, often completely in black, ultra cynical. You get the picture. The moment they saw an accordion player in sodding Lederhosen in the street, they became 60 years old, started clapping along with the music, asking for different music. Basically became their parents. I actually have no issues with an accordion. It's not my musical weapon of choice but only in small measures. Rob -
I have the exact same model, apart from the fact mines a 97 MIJ model, mine has matching colour headstock, mine has no neck pickup cover, mine has a different fretboard, mine has updated electrics, but apart from that, its the exact same model, actually now I think about it, mine might be a different colour and could be a Precision and not a Jazz but apart from that, twins Love the picture. A working guitar in it's natural element. rob