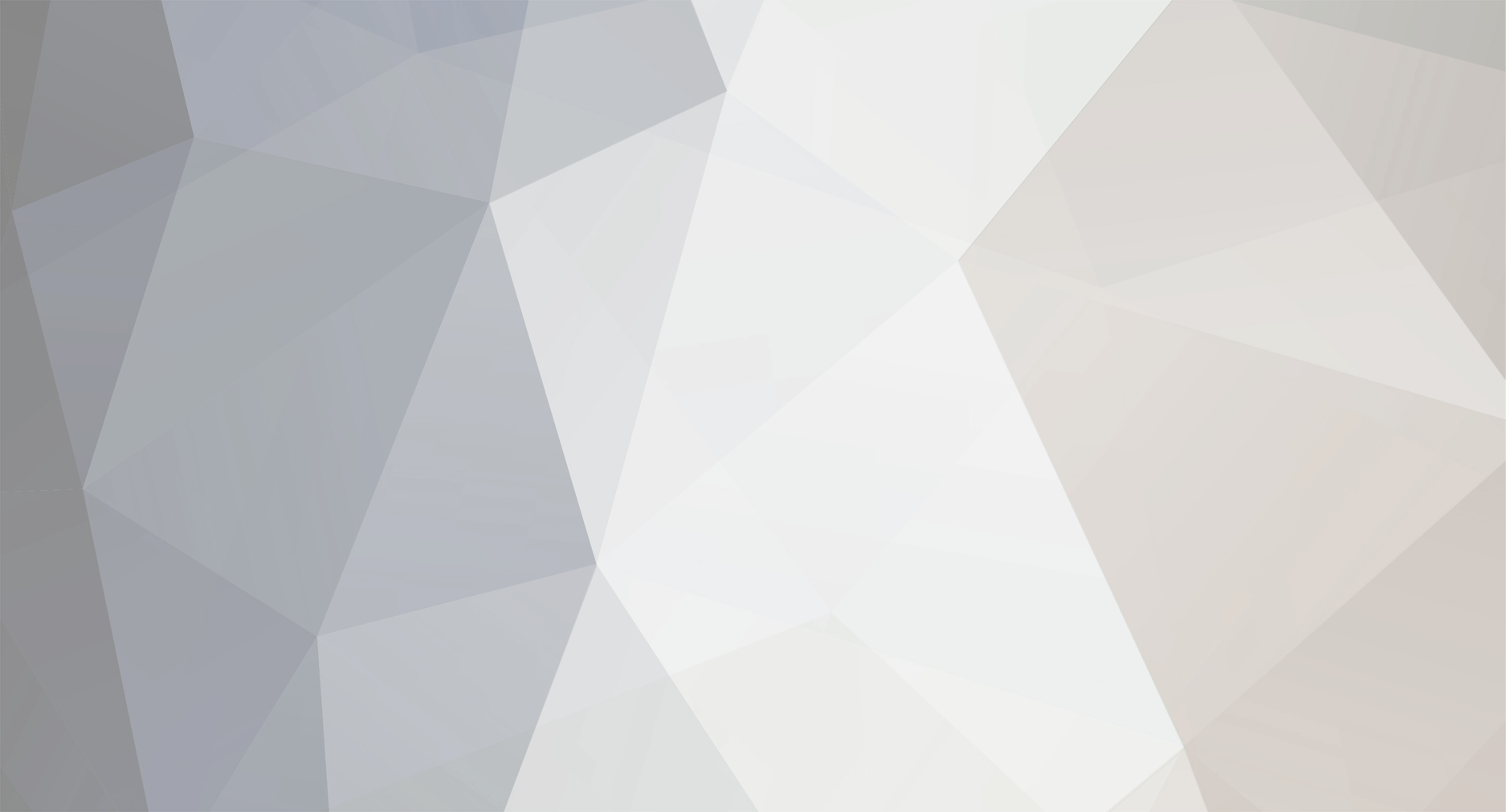
rwillett
⭐Supporting Member⭐-
Posts
1,612 -
Joined
-
Last visited
-
Days Won
6
Content Type
Profiles
Forums
Events
Shop
Articles
Everything posted by rwillett
-
Oddly enough just received an email confirming payment and key access at the same time as your notification. So hall now confirmed. We have the whole hall including kitchen.flr the whole day. My daughters have promised to do some baking the night before. Food, tea and coffee will be free but a contribution to one of my daughters charity's welcomed. Clapham is not a major metropolis not even a small village. We have a village shop, we have a decent cafe at the Old Sawmill, a pub and a bar that has new management and that's about it. I'm happy to do breakfast bacon or sausage butties in the morning at the hall if people would be interested. For lunch i can pizzas in the oven. That might be easiest but am happy with any other suggestions.
-
Just put the spirit level on the neck and its slightly concave at the nut end by about 2mm. It gently lifts off from about the 12th fret. This is on a neck that is not connected to anything and has no tension on it., its just sitting on my desk. I understand what you mean by "The long thin triangle needs to be angled such that the strings would lie flat on the fretboard if you hold them down at the first fret.". Thats a good position to aim for, I can work the maths out now I now I have a target position. I suspect that I may need to shim but printing a shim is relatively easy now I know the target positions. So I think I need to get the aluminium backbone (wood colour) drilled so that I can start to connect the bridge module (white left), the bridge adapter (gray left), the middle module (middle white) and the neck module (white right) Put the neck on and put some strings on it, fret at the first nut and see if the strings lie flat against the neck. If not flat then see if it needs shimming OR a slight change in the torsion rod is needed. I need the aluminium backbone to provide some strength as the 3d printing won't. Thanks Rob
-
OK, understand now. I can see what you mean. I'll have a think about it. never needed it so far, but it's interesting to see it done.
-
A question for the more skilled builders here (thats not me). Is there a maths relationship between the height of the nut and the top of the bridge where the strings will lie? The neckless head I have is 28.5mm thick at the centre of the end of the heal. The other two necks are 27.5mm at the same point so within 0.75mm which is pretty close. Clearly if the neck was 15mm thick it would be far too low, also if it was 40mm thick, it would be too high. So what should it be? I can easily move the neck up and down in the heal module by either printing it differently. I can extrude the blue area below plus or minus a few mm with a couple of key strokes. Printing it at a decent resolution will take around 12 hours though. I can also print shims to go under the neck or under the bridge. which would be the first check. I have a large 120mm spirit level which is the longest flat thing in the house (apart from my wit). If I put the spirit level on the neck nut and get it just right on the bridge, I can see that the gap between the bottom of the spirt level is around 6mm at the 14th fret (or so) and tapers up to almost nothing at the neck. Should it be higher, lower, it doesn't matter so long as its about right as there's a little bit of vertical travel on the bridge and can use the tension rod in the neck? The Nova bridge is significantly higher than the BBOT on my basses so not sure what to do here. Any help or advice welcomed.
-
My eldest is heavily into Oasis, Nirvana, Beatles, Blur, Artic Monkeys, The Pretty Reckless. She was somewhat miffed that I had even heard of Nirvana, much less that a friend of mine played with them in 91 in Reading (?). He got them to sign his bass and then sold it a few years ago for quite a lot of money, sensible man. The youngest is more pop orientated. So I have no idea what she listens to as it sounds the same to me. I am my father. Anyway, progress on the headless bass is good. After spending far too long with the Fusion 360 Vontori generator and giving up, I used an online SVG version which is far quicker and easier than the one for Fusion 360. See https://voronoi-editor.web.app Redesigned the bridge holder to have a cut away for access to the Nova bridge, redesigned the Jazz style body outline for the same. Printed off the bridge adapter and am now printing the two central parts of the guitar. Those are the bits in dirty white below. They'll be finished around 21:30 and then will print off one half of the drill guide for the aluminium backbone and the guitar neck holder. The drill guide makes sure I don'lt cock things up. I've reduced the width of the backbone from 80mm to 60mm to try and get the total weight down to under 4Kg. The backbone is in the wood colour below, though it's aluminium. Still need to think about the control panel and splitting down the frame outline, this is the body that sits on the central monocoque. You can see the mounting holes, there's probably too many but rather too many, than too few. I do not know Finate State Analysis to work out stress and load. I did pure maths and never sullied myself with real numbers or even real world maths. The limits now are the size of the print bed, so I've effectively 200mmx200mm chunks to print out. It looks like there are six chunks to be printed, they have to overlap as I need to join them. Each chunk is probably 12-18 hours If anybody can get this down to five chunks with an overlap, I'll send you a decent bottle of white as that saves a lot of time. The main advantage here is that most of the chunk are simple printing with no embedded nuts so I can start printing and forget. I'll probably draw up a timetable to try and get this done for next Friday
-
One plays jazz sax and is quite good, the other plays flute and no matter how much Jethro Tull I play, she refuses to bite...
-
Nope, I got a Gorilla stand or two. As I also have two more or less feral daughters, two rescue cats and a wild dog as well, vases and knick-knacks are long gone.
-
I'll have a look at those but I'm favouring simplcity over functionality. TBH I've no idea how to make them standup without stands and for me, thats functionality I don't need.
-
Just weighed the headless neck and an Aria Pro neck with Hipshot tuners. Headless neck (without any string locks) = 750g Aria STB-II with 4x Hopshots = 1050g So 300g lighter but need to add in the string lock, approx 75g, so headless apporx 225g lighter. Since most of the 225g is at the end as well, thats a reasonable saving in weight and angular momentum. Rob
-
I'll help you get it done before then, 8:30pm at the lastest
-
It was the bit about not needing a stand that seemed complicated. Not the cut away
-
@tauzero That sounds a lot more complicated than I had thought about TBH. I know this looks similar but 1. It's a wholly different philosophy and design. I know this sounds a bit trite but it's a blank sheet of paper start. 2. It will accommodate different pickups that attach to the body rather than hanging from a pickguard. 3. I'll use a mixture of glue and bolts. This should mean I can change the body shape relatively easily. 4. The build will change to make it easier which should/might/won't make finishing a bit easier. This might be complete bollox as the finishing is now seriously annoying me as I can't make it look good. When I say seriously annoying me, I'm furious TBH. 5. There's lots of changes to reduce printing time and reduce printing waste. 6. Changed the way the neck attaches to simplify and allow it to be changed. Let's see if any of this works Rob
-
After a bit of thought, my next project is a headless bass. I was kindly given some headless bass parts by a Basschatter, I'll not mention who it unless they want me to. The original V1 3d printed bass is basically finished apart from the finish which is currently progressing at the cube root of sweet F. A. Every time time I test a finish out, it looks worse than when I started, so thats progressing very slowly. A body (plastic not human) is sitting in the garage having a lot of sanding done to it. So I thought about the next thing to do, and decided that the headless bass can't be that difficult (stop laughing at the back there). Even though I spent a long time thinking about the bass guitar I still made loads and loads of mistakes so the headless bass has exactly zero parts carried over. The design is completely different and nothing apart from the bolt hole sizes are carried over. The V1 bass guitar could be described as outside design-in whereas the headless bass is designed from the middle-out. The shape of the guitar isn't fixed at this time, but is likely to be fender jazz ish but that could change quickly. The core of the design is the aluminium backbone of which everything hangs. This is the change in design philosophy. Its like a monocoque car chassis on which things such as wheels and suspension are hung. Doesn't sound like a big change but it is So it could be a Fender Jazz (slighly lengthed to handle the headless bridge) or a Thunderbird Or something really weird These are the first bits printed up as a proof of concept The intention is to have the bridge, bridge plate, neck plate and heal plate at least printed by end of this week, which will be tight, but lets see. The headless bridge adds about 30mm extra behind the bridge, hence the design needs tweaking a little. The upside is that I now can easily create SVG files for the outline as I spent some time understanding outline tracing and upgraded my Affinity Designer to V2.
-
Not your fault. It sounded good from the car park. My fault for leaving it too late.
-
I tried to get to the Aspinall Arms. I actually got in the car park and couldn’t find a space , tried to get out and an oil tanker was stuck as people had blocked both sides of the road. Tempers were starting to rise, so I abandoned the attempt. I could see the white marquee and hear music but couldn’t park hope the gig went well. Let me know the next time you’re playing. rob
-
3-6 month wait on Amazon. Never seen that sort of delay.
-
Oh wow, how long did that video take to make? I think that shows that you can put the pickups just about anywhere and still have a decent sound. Whether its the right sound for somebody is for them to decide. Me personally, I like the Jazz positions but I the combination of series and parallel pickups was interesting as well as split coils and reverse coils. Thats made me think. I'm so impreseed with the effort that went into that, hats off to the man for making that. Rob
-
A question to more experienced than me players, which is everyone How critical are the positions of the bass pickups in your opinion? Does it make a difference if pickups are 5mm out in different positions, or 10mm or doesn't it make a lot of difference? All views welcomed. The reason for asking is that I'm looking at a new centre plate for the bass guitar and I wanted to be able to use different bass pickups. These all require mounting holes and they start to collide. It's getting a bit crowded in there. There are holes for neck and bass jazz pickups, thunderbird style pickups and split precision pickups. Also there are backplate mounting pickups and bridge pickups. Not put on holes for the neck yet either or other mounting holes that need to go down the edge either. It does fit but I'm moving things around 2-3mm to avoid collisions.
-
Tesmart Four (three really) 4k hdmi port kvm - Gone
rwillett replied to rwillett's topic in Completed Items
Hi, did this turn up? -
Wow, thats bad...
-
But apart from that...
-
A seller sold a real, old and kind of expensive violin to a buyer, the buyer clained it was fake and PayPal told them to destroy it and refunded their money. The seller was wholly ignored in the process. https://www.cnet.com/news/paypal-dispute-ends-in-destruction-of-violin/ I would never sell anything of value on eBay though I do use it for smaller (< £200) transactions.
-
Are short scale basses really as bad as they say?
rwillett replied to Cheeto726's topic in General Discussion
Not sure why thats controversial... Looks a fabulous bass to me. I don't get all the negativity around guitars, I've a range of six strings and four strings. My daughter has just moved from a Strat type replica, to a lovely Vintage Les Paul (Vintage as in the company as opposed to the year, I can't afford anything vintage apart from the clothes I'm wearing). The LP is great as was the Hohner as is the Westone, she doesn't like playing my Squier MIK 89 Telecaster which is brilliant as I love it, but she likes the Ibanez Short Scale (24") and can;t really handle the Jazz bass. Horses for courses. I may not like the looks of some of the more extreme guitars, but thats just me. If you like them, play them and enjoy them. I am jealous of the Acinonyx though. Rob -
Are short scale basses really as bad as they say?
rwillett replied to Cheeto726's topic in General Discussion
I have the exact same MIM Mustang. I think it's a great bass, it's as good as my MIJ Jazz, a bit smaller so easy to carry round. I also have an Ibanez Mikro bass that looks like to came off a building site. I like that was well. I have zero issues going from one to the other, probably because I'm not very good. Lots of people prefer short scales as they are lighter and easier to handle. Not sure why short scales get a bad press. Just another guitar to me, with good and bad points. -
Which companies are dead to you?
rwillett replied to Jean-Luc Pickguard's topic in General Discussion
Just to pose the counter argument here, Mick the Postie is wonderful for us. He's always punctual, chats and puts things safely in porches or garages. Picks things up and is generally a top bloke.