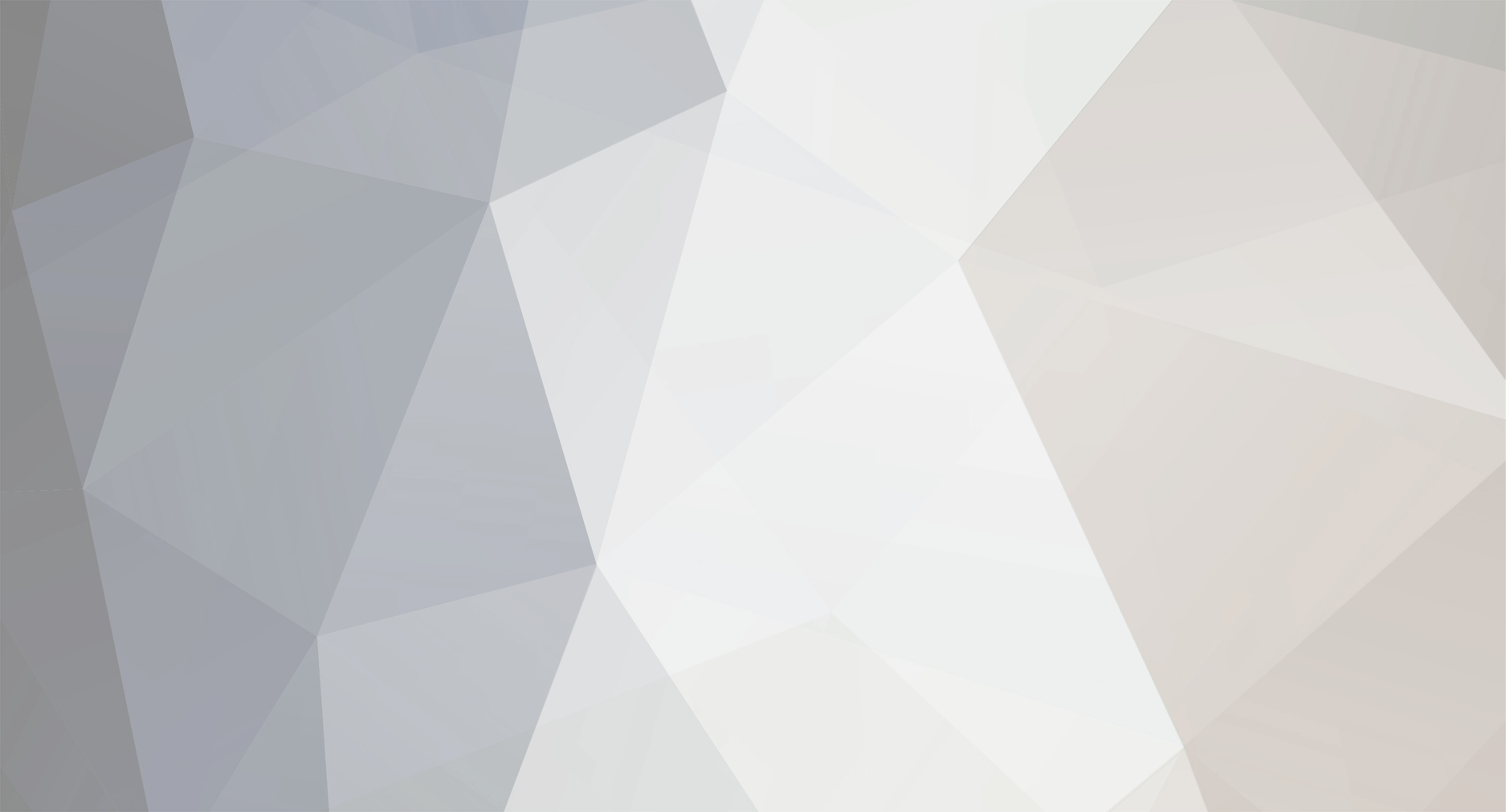
rwillett
⭐Supporting Member⭐-
Posts
1,626 -
Joined
-
Last visited
-
Days Won
6
Content Type
Profiles
Forums
Events
Shop
Articles
Everything posted by rwillett
-
It was the bit about not needing a stand that seemed complicated. Not the cut away
-
@tauzero That sounds a lot more complicated than I had thought about TBH. I know this looks similar but 1. It's a wholly different philosophy and design. I know this sounds a bit trite but it's a blank sheet of paper start. 2. It will accommodate different pickups that attach to the body rather than hanging from a pickguard. 3. I'll use a mixture of glue and bolts. This should mean I can change the body shape relatively easily. 4. The build will change to make it easier which should/might/won't make finishing a bit easier. This might be complete bollox as the finishing is now seriously annoying me as I can't make it look good. When I say seriously annoying me, I'm furious TBH. 5. There's lots of changes to reduce printing time and reduce printing waste. 6. Changed the way the neck attaches to simplify and allow it to be changed. Let's see if any of this works Rob
-
After a bit of thought, my next project is a headless bass. I was kindly given some headless bass parts by a Basschatter, I'll not mention who it unless they want me to. The original V1 3d printed bass is basically finished apart from the finish which is currently progressing at the cube root of sweet F. A. Every time time I test a finish out, it looks worse than when I started, so thats progressing very slowly. A body (plastic not human) is sitting in the garage having a lot of sanding done to it. So I thought about the next thing to do, and decided that the headless bass can't be that difficult (stop laughing at the back there). Even though I spent a long time thinking about the bass guitar I still made loads and loads of mistakes so the headless bass has exactly zero parts carried over. The design is completely different and nothing apart from the bolt hole sizes are carried over. The V1 bass guitar could be described as outside design-in whereas the headless bass is designed from the middle-out. The shape of the guitar isn't fixed at this time, but is likely to be fender jazz ish but that could change quickly. The core of the design is the aluminium backbone of which everything hangs. This is the change in design philosophy. Its like a monocoque car chassis on which things such as wheels and suspension are hung. Doesn't sound like a big change but it is So it could be a Fender Jazz (slighly lengthed to handle the headless bridge) or a Thunderbird Or something really weird These are the first bits printed up as a proof of concept The intention is to have the bridge, bridge plate, neck plate and heal plate at least printed by end of this week, which will be tight, but lets see. The headless bridge adds about 30mm extra behind the bridge, hence the design needs tweaking a little. The upside is that I now can easily create SVG files for the outline as I spent some time understanding outline tracing and upgraded my Affinity Designer to V2.
-
Not your fault. It sounded good from the car park. My fault for leaving it too late.
-
I tried to get to the Aspinall Arms. I actually got in the car park and couldn’t find a space , tried to get out and an oil tanker was stuck as people had blocked both sides of the road. Tempers were starting to rise, so I abandoned the attempt. I could see the white marquee and hear music but couldn’t park hope the gig went well. Let me know the next time you’re playing. rob
-
3-6 month wait on Amazon. Never seen that sort of delay.
-
Oh wow, how long did that video take to make? I think that shows that you can put the pickups just about anywhere and still have a decent sound. Whether its the right sound for somebody is for them to decide. Me personally, I like the Jazz positions but I the combination of series and parallel pickups was interesting as well as split coils and reverse coils. Thats made me think. I'm so impreseed with the effort that went into that, hats off to the man for making that. Rob
-
A question to more experienced than me players, which is everyone How critical are the positions of the bass pickups in your opinion? Does it make a difference if pickups are 5mm out in different positions, or 10mm or doesn't it make a lot of difference? All views welcomed. The reason for asking is that I'm looking at a new centre plate for the bass guitar and I wanted to be able to use different bass pickups. These all require mounting holes and they start to collide. It's getting a bit crowded in there. There are holes for neck and bass jazz pickups, thunderbird style pickups and split precision pickups. Also there are backplate mounting pickups and bridge pickups. Not put on holes for the neck yet either or other mounting holes that need to go down the edge either. It does fit but I'm moving things around 2-3mm to avoid collisions.
-
Tesmart Four (three really) 4k hdmi port kvm - Gone
rwillett replied to rwillett's topic in Completed Items
Hi, did this turn up? -
Wow, thats bad...
-
But apart from that...
-
A seller sold a real, old and kind of expensive violin to a buyer, the buyer clained it was fake and PayPal told them to destroy it and refunded their money. The seller was wholly ignored in the process. https://www.cnet.com/news/paypal-dispute-ends-in-destruction-of-violin/ I would never sell anything of value on eBay though I do use it for smaller (< £200) transactions.
-
Are short scale basses really as bad as they say?
rwillett replied to Cheeto726's topic in General Discussion
Not sure why thats controversial... Looks a fabulous bass to me. I don't get all the negativity around guitars, I've a range of six strings and four strings. My daughter has just moved from a Strat type replica, to a lovely Vintage Les Paul (Vintage as in the company as opposed to the year, I can't afford anything vintage apart from the clothes I'm wearing). The LP is great as was the Hohner as is the Westone, she doesn't like playing my Squier MIK 89 Telecaster which is brilliant as I love it, but she likes the Ibanez Short Scale (24") and can;t really handle the Jazz bass. Horses for courses. I may not like the looks of some of the more extreme guitars, but thats just me. If you like them, play them and enjoy them. I am jealous of the Acinonyx though. Rob -
Are short scale basses really as bad as they say?
rwillett replied to Cheeto726's topic in General Discussion
I have the exact same MIM Mustang. I think it's a great bass, it's as good as my MIJ Jazz, a bit smaller so easy to carry round. I also have an Ibanez Mikro bass that looks like to came off a building site. I like that was well. I have zero issues going from one to the other, probably because I'm not very good. Lots of people prefer short scales as they are lighter and easier to handle. Not sure why short scales get a bad press. Just another guitar to me, with good and bad points. -
Which companies are dead to you?
rwillett replied to Jean-Luc Pickguard's topic in General Discussion
Just to pose the counter argument here, Mick the Postie is wonderful for us. He's always punctual, chats and puts things safely in porches or garages. Picks things up and is generally a top bloke. -
Which companies are dead to you?
rwillett replied to Jean-Luc Pickguard's topic in General Discussion
Thanks for the update. For some reason I thought it was a longer coach journey. She wanted to do things herself so I didn't get too involved. I feel a bit happier now. -
Which companies are dead to you?
rwillett replied to Jean-Luc Pickguard's topic in General Discussion
Spot on. RyanAir is only cheaper if you don't value your own time as anything above 1p per hour. I now factor in around £30/hour as "my time", so would I pay an extra £30 per hour to avoid something. such as a three hour coach trip. I would and I do. My daughter is going to the Monaco Grand Prix, to save money she's flying Manchester to Brussels, long lay over, Brussels to somewhere like Nice and then a longish coach journey. She apparently thinks a 15 hour journey is worth it to save £100 as its her money. Everybody values their time differently. RyanAir values my time as nothing -
Good question that. I suspect it's a flexible answer. Is my 97 MIJ Jazz "Vintage" or is a 79 but not an 80 vintage?
-
Which companies are dead to you?
rwillett replied to Jean-Luc Pickguard's topic in General Discussion
I remember flying to Oslo Torp airport with RyanAir. Three sodding hours from Torp airport to Oslo. Thats like saying London-East Midland or London-Robin Hood Airport. They were dead to me before Michael O'Leary stuck his oar in re Rwanda. We have got to the stage that we actively avoid RyanAir and pay more to anybody else. -
Now thats just greedy
-
@Owen I thought that was just me. I have a Mod_dwarf which could probably take me to the moon and back, but it's complicated. So I go back to simple things and keep thinking I must get back to the Mod Dwarf and set it up properly. I don't.
-
Which companies are dead to you?
rwillett replied to Jean-Luc Pickguard's topic in General Discussion
And to everybody else.... -
Which companies are dead to you?
rwillett replied to Jean-Luc Pickguard's topic in General Discussion
Sony They supplied software that spied on me through their CDrom. Never brought another Sony product again. As I also used to buy large numbers of pcs, think 1000's a year, made sure Sony never supplied a single one. -
Zon Hyperbass Type II Michael Manring Signature
rwillett replied to eubassix's topic in eBay - Weird and Wonderful
I'm sure that the buyer was genuine and was alternating between working in the Shetland Isles as a lobster fisherman and a highly paid city lawyer. He probably accidentally left his ultra expensive Martin guitar as he had other legal things on his mind. These things happen, and for some reason, often on Gumtree. Perfectly innocent and believable explanation IMHO. Rob -
Good ideas. Will do so.