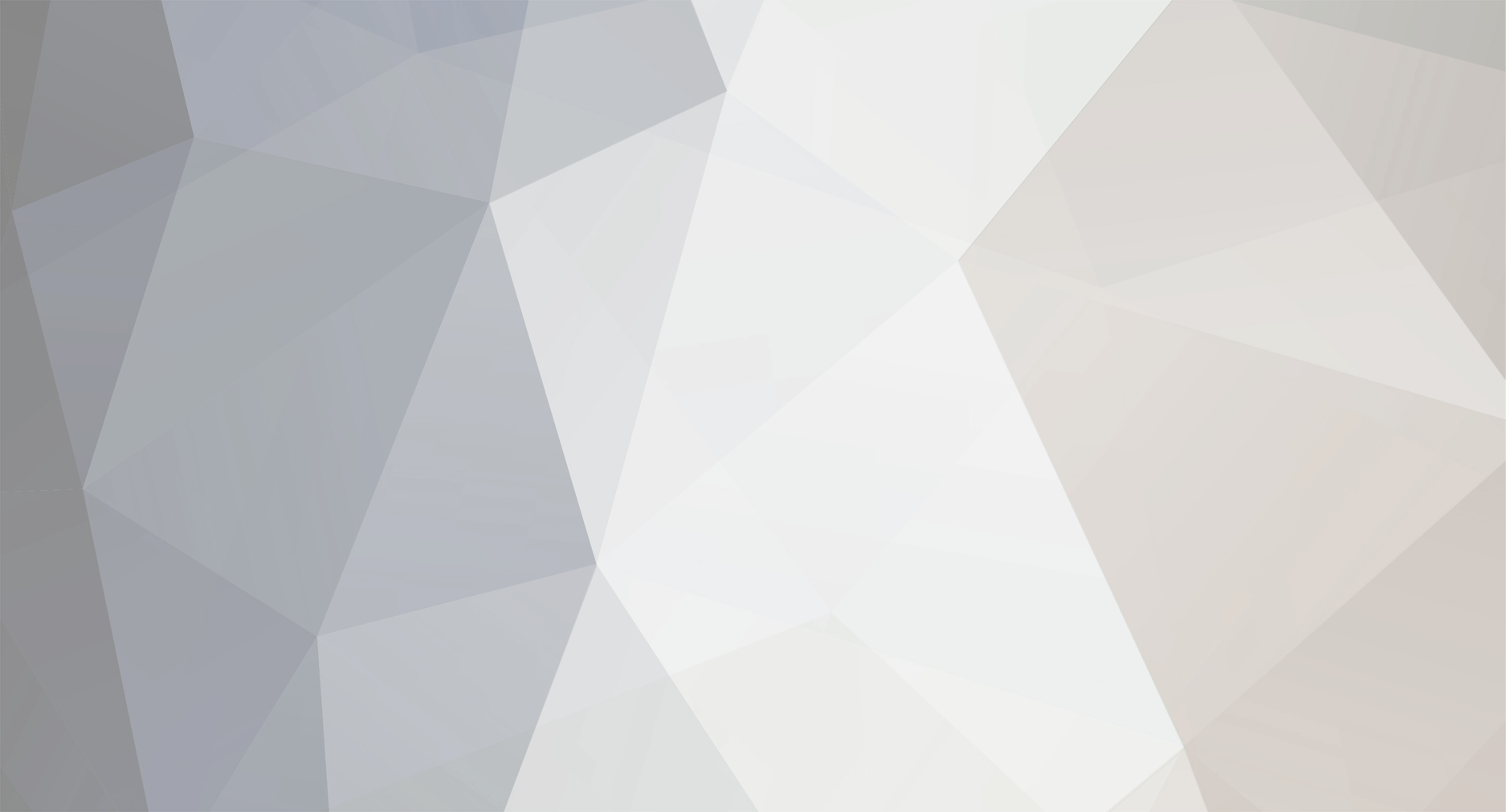
rwillett
⭐Supporting Member⭐-
Posts
1,627 -
Joined
-
Last visited
-
Days Won
6
Content Type
Profiles
Forums
Events
Shop
Articles
Everything posted by rwillett
-
Now that the mule has a 12mm aluminium backbone in, that has moved the neck into a far, far better position and it suddenly feels better to play, even if it does have tug ship cables for strings. Some lighter strings are on order as well as some more aluminium. If that doesn't work, steel starts to become the option. Am starting to think about mounting pickups and best practises. I think I have two options, I can mount the pickups downwards on the body of the guitar. I considered this in the design and have a large number of embedded nuts into which I can design a sledge to hold the pickups in exactly the right place. I can easily put the sledge and pickups in any position and move it around. I can design a basket to hold the pickups and mount them to the pickguard, this is how I did my six string. So I hang them (shooting is far too good for them). I notice that most of the bass pickups have quite stiff foam on the bottom, sometime along with springs, so I am assuming that mounting them to the body is the preferred method. I have no preference to be honest. As vertical space is limited, I would probably remove the foam and design a slightly more complex adapter that is more adjustable, I can suspend othem or fix them. I can't find anything that indicates what best practise is. If anybody has views (and can explain why they have views) on whats good, I'm happy to listen. It might well be that suspending them from the pickguard allows them to resonate or some other reason I know nothing of. Once I have finished my guitar pickup winder, on hold as I need to get this bass done, I will replace whatever that goes in with something else, or I might do a three way pickup set. Just got a few five way Fender type switches off eBay for 0.99p and might try to use a multi-coil option Any help or direction welcomed. Rob
-
Depends on the time of the works event. The M6 is 20 mins away and from there, the world is your oyster. Going the opther way is painful as the road to the M1 is slow and has lots of tractors in the way. Failing that, I can write you a sick note. Rob
-
We'll survive and make something work for us...
-
Not sure I need something that sucks quite as well, unclear as to how A&E comes into this....?
-
Just checked and the village hall is booked for this for the day. We have the whole hall. Whether we have enough people to fill it, thats adifferent story Rob
-
Definite enough that I can offer you a free room....
-
I'm looking forward to hearing the tone differences as well - One day ... Next steps are: 1. Order some lighter strings. The E string is 3mm thick, my fender Jazz is 2.75mm, my Ibanez short scale 2.4mm and my fender Mustang 2.4mm. 3mm is 0.11in according my calculator. A set of Rotosound lightweights are 0.03in, 0.05in, 0.065 and 0.08in. https://www.rotosound.com/product/rs66la/ No idea of the tension that I have on the current strings but it feels a lot, mind you, my gut feelings have been rubbish so far. 0.08/0.11 = 72% of the thickness which is quite a lot. 2. Order some 3mm aluminium so that I can make a 15mm backbone from the 12mm and the 3mm. I'm wondering if two plates making 15mm sounds different to 1x15mm, 3. Order some 15mm aluminium to check if that works much better. 4. Check on 7000 series grade aluminium. Anything that has "aerospace" attached to it will not be cheap, even if I am. 5. Readjust my pillar drill so I can clean the workstop. Swarf and cuuting fluid is horrible, already used the "kitchen" dustpan and brush and the CFO was not happy with what I brought back, so a new dustpan needed now <sigh>. 6. Check on steel plate as the next step if I can't get aluminium to stop bending. Rob
-
Yep. Does anyone have any contacts with various shops such as Promenade Music that might be interested in coming along. I can definitely offer cake now 😊
-
I have strict limits on the height of components. Total body height is 44mm, pickups are a certain height, other parts of the body have a certain size such as the mounting plate (10-11mm). Everything is a compromise, money, strength, stiffness, complexity, technical issues, weight. If I had unlimited money AND technical ability I'd go carbon fibre. Sadly I don't have either. I'll look at the calc and see if it helps though. Rob
-
If I look around me, I see a few farms, a normal garage specialising in Land Rovers and approx 10m sheep. I can't imagine the farmers having any high quality aluminium on hand, they normally reuse and reuse and reuse. Suspect the sheep aren't big users either. I might make a call and check. I might also check out carbon fibre.
-
The bar I have is apparently Grade 6082T6 (Formerly H30TF). I am taking this to mean its Grade 6000 from here https://www.1stchoicemetals.co.uk/aluminium/grades-guide/?doing_wp_cron=1710703985.3204550743103027343750 The higher grades, 7000, appear to be a whole world of cost higher. It apparently is used for defence and aerospace, guitar making doesn't appear to be an option I cannot find a supplier who puts a price up on line. It's all "ring for a price". This tends to mean, if you have to ask the price, you can't afford it. If somebody knows different please tell me. It might mean that I can't even drill the stuff with consumer drills. I used to work at BAE Subs in Barrow In Furness and I would bet a pound to a penny that they have this sort of aluminium all around the workshops. However BAE Subs has armed guards on-prem as it does have nuclear reactors there, so suspect I can't head back up, pop my head around the workshop door, and ask them for a bit. Also I caught e-coli there and almost died, so not particualarly keen to see the old Vickers place again. Rob
-
Nope. Not sure at all but so far this week have learnt : 1. Calculating stiffness is pointless unless you really know plywood and or aluminum. 2. Americans need to move to SI units. 3. Plywood is stronger than I knew 4. Aluminium isn't. 5. Pillar drills produce a low of swarf. 6. Pillar drills and cutting fluid produce a vile mixture
-
You sound like.my youngest daughter.
-
Got home after rugby and thought I have to try the 12mm aluminum backbone. I have cutting fluid and used the 6mm as a template. Didn't break the drill but the amount of swarf that comes off, use cutting fluid and it's wet swarf. Need to rethink the tool station. Anyway now have a 12mm backbone that fits, I love precision, and tuned up. There is still a little bow, in the 12mm aluminium. I reckon I must have the crappiest aluminium this side of a Soviet submarine. The bow is small, probably 1mm-2mm across 400mm if that. Massively better than before. I'm not going to 15mm aluminum at the moment. Now the neck is a little flatter, I'll follow the video links that @samiam posted to set it up. Still looks like a scrappy Steinberg, but getting there. Don't stress over some of the heights of things in the picture. Now I have a reasonable backbone I'll make the neck/bridge height the same as my Fender Jazz. This is progress though
-
You can see the bend in the 6mm aluminium plate. I'm very surprised as I thought it would be stiffer. The maths says 9x stiffer. That's proven to be a load of b0ll0cks What's interesting is that the printed stuff is holding out under the load. 40% infill seems to be ok.
-
Well I ran the maths and trusted my gut feeling and both were wrong. The 6mm aluminium bent at the same rate as the 15mm plywood. I worked out the aluminium as 9x stronger. Thankfully, I don't do any maths involving safety critical systems. I have an hour free so am drilling the 12mm aluminium and lets see how that works. Rob
-
You'd have to buy a lot to move the market this way. Whilst vintage fenders are scarce and there is demand, there are enough sellers to make cornering the market difficult. To move the market they need to be close to a monopoly and this isn't a monopoly at the moment. I'd like to be able to buy enough to move a market though. Sadly I'm no Rotheschild in the oil business
-
Well so much for maths. My calculations showed that 6mm aluminium should be significantly stronger than 15mm plywood. Rubbish. Just drilled a 6mm slab of alumimium using my nice shiny pillar drill. I made a drill guide to use as everything had to line up perfectly and surprisingly it did. Put everything back together on my test bass and it bends just the same as the 15mm plywood. Approx 2-3mm at each end. Very, very surprised so either I have poor quality aluminium or high quality plywood. Tomorrow is a girls rugby festival in Settle, I'm the organiser so I may not get time to drill the 12mm plate until later in the week. Very disappointed, but more bright paint on the learning curve. Rob
-
Even better then, 50p...
-
May I add my name to list for the next turn please? Is it like the pool table at the pub, do I need to put £1 down?
-
That looks a lot more substantial than mine but also bigger. Not sure the laser makes a massive difference to be honest. We seem to have survived for a few centuries drilling holes without one.
-
Pillar drill now here. Plugged in, turned on and tuned in. Might drop out later😊 The clamping mechanism and fence look OK but I'm not jumping up and down with joy and can see a heavy vice looming in my future. Also the laser alignment is out by about 0.3mm on one axis. This might be some sort of record of me dismantling something less than 24 hours after receiving it. No point in sending it back as the next one might be as bad. l
-
Wow, just wow Where exactly in Norfolk do you live again....? Asking for a friend.
-
Very tasty.... never seen that colour and pickguard combination. Looks great.
-
Am getting a daily digest of emails and want to turn it off
rwillett posted a question in Site Issues and Questions
Hi, I'm getting a daily digest of emails and want to turn it off as I get the immediate emails. My settings don't seem to have one for daily digest or I can't find it. Can someone point me in the right direction please? thanks Rob