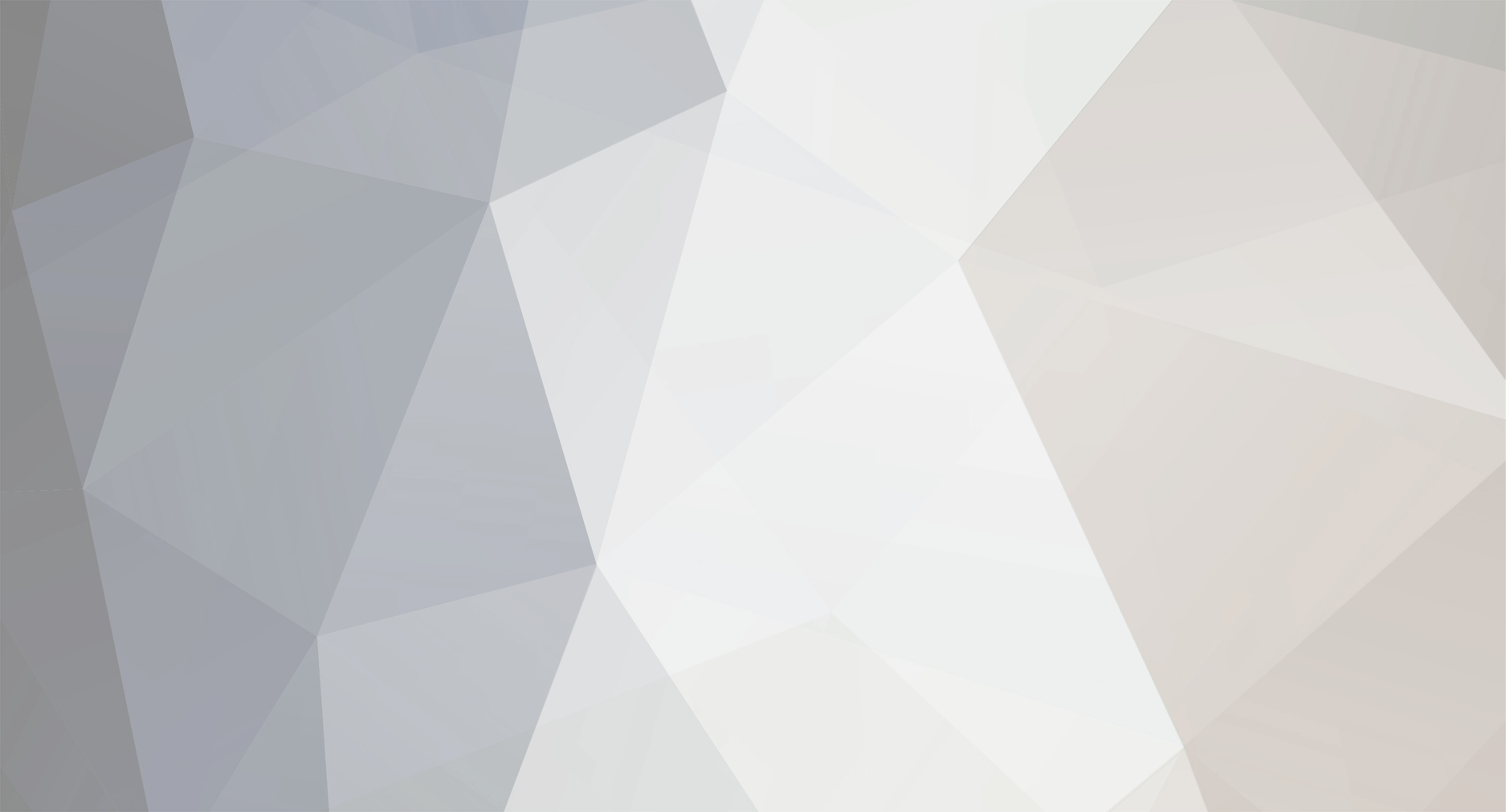
rwillett
⭐Supporting Member⭐-
Posts
1,496 -
Joined
-
Last visited
-
Days Won
5
Content Type
Profiles
Forums
Events
Shop
Articles
Everything posted by rwillett
-
It's not ready for print a neck. 1. We can't print a neck in one piece. Printers aren't big enough. 2. Structurally the material isn't strong enough. 3. No idea how it would resonate. 4. The material doesn't bend reliably to allow the neck to be tuned. Apart from that, no issues.
-
So Been in a number of boring MS Teams meetings and have used the time productively to go through a cross sectional analysis of the guitar mm by mm. The aim of this check is to ensure that where I have a bolt that links things together, there is the entrance hole, a clear pathway through the object, an exit hole, a hole for an embedded nut, there are no 'thin wall's and it's all the right level of material. This is really painful as you have to force yourself to think about every single way that things connect. Some areas require access holes to get to the bolt and these need to be checked. e.g. the thickness of the neck clamp module is longer than my longest bolt, so I have to make an access port, basically a hole around 8mm in diameter that the allen key can get into the tighten the bolt inside. You can see it below with the purple rings. This means I can't attach the neck until I attach the top right strap bit, I need to print it first and it's 5 and a bit hours. Also I've just realised my neck doesn't have a nut so thats on order as well. The work list never ends Rob
-
Just tried S739401 in https://www.guitardaterproject.org/fender.aspx and that doesn't work either Doesn't work in https://serialnumberlookup.fender.com/lookup/ either. What am I doing wrong? Thanks Rob
-
Fender Precision 1978 Rosewood Board Natural Finish £1645 - *SOLD*
rwillett replied to ash's topic in Basses For Sale
It does look nice. And it's a hell of a lot cheaper than the one on eBay and it's from someone who is known and trusted and it's local... Bloody hell it's in Lancaster, that's far too close to me. I am in Lancaster Monday night donating blood platelets but will be a little preoccupied thankfully. Otherwise I might do something stupid. -
Also the serial number doesn't pop up in Fender database. However I have had issues with that system simply not working, so who knows... Lots of red flags here. Rob
-
After a few iossues with the printers, a themistor was playing up, I managed to get a bit more done. At the moment, I'm printing to test the concept and fit. The printed parts are draft quality and will change for the better if it all works. Shouldn't make any difference to the sound but nicer to look at. This is the back of the guitar with 8 x 22mm countersunk screws attaching the bridge and neck pickup to the 15mm ply. I made a drill guide to ensure the screws all fit as the holes only go part way. You can also see the neck module and the guitar neck. This is the front of the guitar with the bridge and neck pickup in place This is the front with the neck in the neck module and slotted on. I haven't drilled the 5mm holes in the plywood yet as I wanted to check everything. The end of the plywood needs shaping but not bothered about that. Next steps are: 1. Drill holes for the neck. 2. Print the bottom control panel bits so I can have something to hold the Telecaster control panels. 3. Print a small and simple pickguard to hold the neck pickup. 4. Solder (or wrap) the wires to see if it even works. 5. Work out how to se the intonation and such. 6. .... 7. Profit!
-
I think you're all missing that this might be an ultra rare Fender that's disguised as pile of junk. Who knows what treasures lie underneath that plain and humble facade? Now the cynics amongst you may dismiss this as mere babbling, but look at Antiques Roadshow as evidence that pearls do exist in unlikely corners. This could be a chance to acquire a lost relic of Leo himself. You could be kicking yourself when it turns up at Andy Baxters with a £50k price tag. Or not.
-
Rumble by Link Wray. Saw Jimmy Page play it at the weekend (sadly not in person) and realised I knew the song from am advert. Yep, that's embarrassing. I now know it was banned even though it was an instrumental which is pretty impressive. Rob
-
And after a lot of work, I almost have a model that works. Its taken longer to work out the mass of fixing holes to connect it up than the original design. There are far, far too many bolt holes here, but the only way to know is to put too many in and then take them out and see how many are actually needed. This is 10mm down from the surface where a lot of bolt holes are, but there's just as many 10mm up from the other side. If I had a printer that was three times bigger, I could almost print this as one piece, but I don't so I can't. The advantage of this approach is that it's modular. Its relatively trivial to put a different neck on this as only one piece needs to change. Want three humbuckers, not that difficult as thats a relatively simple wiring and pickgiard change. Not convinced the control panel is big enough, BUT thats just another module. You could change the two end pieces and make it a Gibson SG like shape. Anyway, still need to check things now and thats another day or so as I have to check every hole to see if its consistent throughout.
-
I'm closer to it's date of birth than you.... Not sure I can afford it though. Rob
-
Fender FSR ELECTRON GREEN Precision Player bass VERY RARE
rwillett replied to la bam's topic in Basses For Sale
I could drop round and shout a stupid number in your ear from 10cm. Is that near enough 😊 Oddly enough I was actually near you yesterday as my u16 girls rugby team was playing in Garstang. We played Liverpool St Helens who gave us a thrashing. As they might well be best girls team in the country, we weren't too down heartened. Anyway, the CFO directly asked me how many guitars I still owned over the weekend and made the decision for me that some have to go. I'd love this one though. Perhaps I can persuade her one out/one in. GLWTS Rob -
Repairing screw holes in a guitar neck...
rwillett replied to rwillett's topic in Repairs and Technical
@Andyjr1515 Thank you for the comprehensive description. Thats a great explanation of why cross grain wood plugs are important for load bearing. I also know that there is a website dedicated to wood plugs, https://plugitwood.co.uk/ I suspect the wood is rather important in Google Search here I've just inspected the end of the neck again, and what appeared to be a right mess for the top two holes, aren't as bad as I thought. There's only a mmm or two of damage. It looked worse than I thought. So my plans are: 1. I will try normal guitar neck screws, preferably with a ferrule to spread the load. Failing that .... 2. .. I'll move to threaded inserts, which I think I can do. Failing that (and by this time I expect to have lost a finger or two) .... 3. .. I'll buy some end grain plugs from the website above and try and glue them in and move back to stage 1. 4. .. Give up. -
If you can find a model, that's the easiest. It's trivial design if I have all the dimensions and I mean every dimension down to the inside radii. Need hole size, height, internal size, external size, screw hole position etc etc etc It's easier with a model. Send me a link if you can
-
I'll print it for you and bang it in the post. It's no big deal. What exactly do you want to print though?
-
I built a CNC machine using a 3d printer. I enjoyed the 3d printing more than using the CNC machine. I did start writing my own software to drive it, as the CNC design software was a pain. I did give up though. I donated it and all the kit to the local school around a year ago.
-
A bit more progress. Have managed to work out how to drill the neck inserts in so I don't destroy the neck and accidently set off WWIII. One the side effects of that, is that I now have the right size for the neck heal module AND the bolt hole positions. So am running this test print off at 60% infill as this module needs to be as stiff as possible (cue @SpondonBassed and all Viz readers). This is not the complete component but I've cut it down just to check everything fits. To my mind the heel pocket is probably the most important bit of the guitar after the fredboard, though this is based purely on my guess @Andyjr1515 might well correct me here. Also have cut the backbone out of 15mm plywood. Despite my best efforts, whilst I managed to get a nice clean cut, one end of the ply is 86.6mm wide and the other is 88.3mm wide. So I can draw a straight line but I can't get a consistent width. I need someone with a table saw to make accurate cuts. In the interim, I'll use the plywoord as the load is along the length of the ply from the string tension, rather than the width. The plywood backbone would slot into a rebate on the back of each module and then I would anchor the plywood to each module with four screws per module. Not sure if this is a big problem or not. Will need to ponder it. You can see how it fits here, the neck pickup module went bang a few versions ago and I haven't fixed it This is without the backbone and this is with the plywood backbone. Rob
-
Whilst this is a very accurate statement, when taken slightly out of context, it sounds very odd. Well done that man for having an even smuttier mind than me Rob
-
After printing a few test pieces out, I have realised that I need to rethink the mounting holes as access is tight due to honeycombs and trying to keep the asthetic right. So the last two days, whilst in various boring video meetings, I've redone most (but not all) of the screw mounting holes. I have deliberately gone over the top for the number for mounting holes as it's a lot easier to take things out and test if the screw mount was needed, than discovering that the guitar was weak. It doesn't look any different but I feel a lot more comfortable that I can access the mounting holes and change things later. The downside to this is that to print most of the pieces I have to be there to insert nuts in at the right time. This weekend is busy, so it'll be next week before anything starts printing what I hope will be the first prototype. I'm also looking at fixing the guitar neck I brought. Its a Yamaha RGX-121DM, its thin, but two of the the heal mounting holes are a bit rough. I posted a request for help in another thread and people came through with some great ideas, the main one being to use M5 threaded inserts. I ordered some and then discovered they had a flange so they are going back and flangeless inserts are now on order I looked at the neck and wondered how I was going to drill the 10mm holes down into the neck when the front of it is curved, so keeping it steady may be an issue (it will be an issue, lets be honest). I don't have a drill press or a vice, but I do have a 3d printer, so in the best tool making traditions, I'm making a guitar neck holder that will hold the guitar firmly, but without damaging it, and allow me to make a vertical 10mm holes in exactly the right place. I'll screw the back of the neck to the top plate using the two good holes. The bottom has a slight curve to match the neck radius, it'll have a few layers of felt to proect it. The six holes on each side will be tightened finger tight to hold it all in. I can then use the drill guides, that's the vertical tubes, to make sure I have a vertical stroke on the hand drill. I don't want to use an electric drill and I don't want it to move. Printing this now then off to take the dog for a long walk to clear head.
-
Repairing screw holes in a guitar neck...
rwillett replied to rwillett's topic in Repairs and Technical
I've ordered some m5 countersunk bolts, some m5 threaded inserts and solid cup washers. £20 for 20 sets so cheaper per set than the 'dedicated' stuff. -
Repairing screw holes in a guitar neck...
rwillett replied to rwillett's topic in Repairs and Technical
Nearest IKEA is Warrington or Leeds. Each are nearly two hours each way. I can order stuff online so that's not an issue. To be honest I think I'll go with the bolts and inserts. That's an easy fix and doesn't require me to work out grain direction and avoids glue. I suspect if I use glue, I'll need to be cut out by the Fire Brigade. -
There's some really cheap deals out there at the moment running up to Xmas, it'd be a crime not to take advantage of them and you have already said how having one would play to your strengths (I paraphrase somewhat). I've got loads of spare filament that I'm happy to share with you to cut the costs down. I'll pull some links out for you to share with the CFO Rob
-
@Richard R Make t'other half a nice printed bracelet or set of ear rings in mud brown. I'm sure she'll relent. I'll print htme for nothing so you can surprise her on Xmas morning.... I have made an awfully large number of things for the house. Our house is quite old and has lath, horsehair and plaster walls. Difficult to find a celing joist, so rather than filling the holes and painting over, I printed some large black or white discs to hide my efforts. I also design and printed a rather nice frame for the Philips Hue floodlights. The Philips design is poor as it doesn't allow cable to come in from the side or top, but only from behind. A couple of hours later solved that problem. I also recall the toilet seat has a fix I made out of plastic. I do keep promising to make a proper pair of cup holders for my Seat Leon estate. It has a massive computer system, electronic this and that but can you actually put two normal (not even grande) take away coffee cups in, no. B45t4rd$ I think a cheap Ender 3 Pro V2 should be on your Xmas list or if you can sneak one in, a Prusa MKS4 Rob