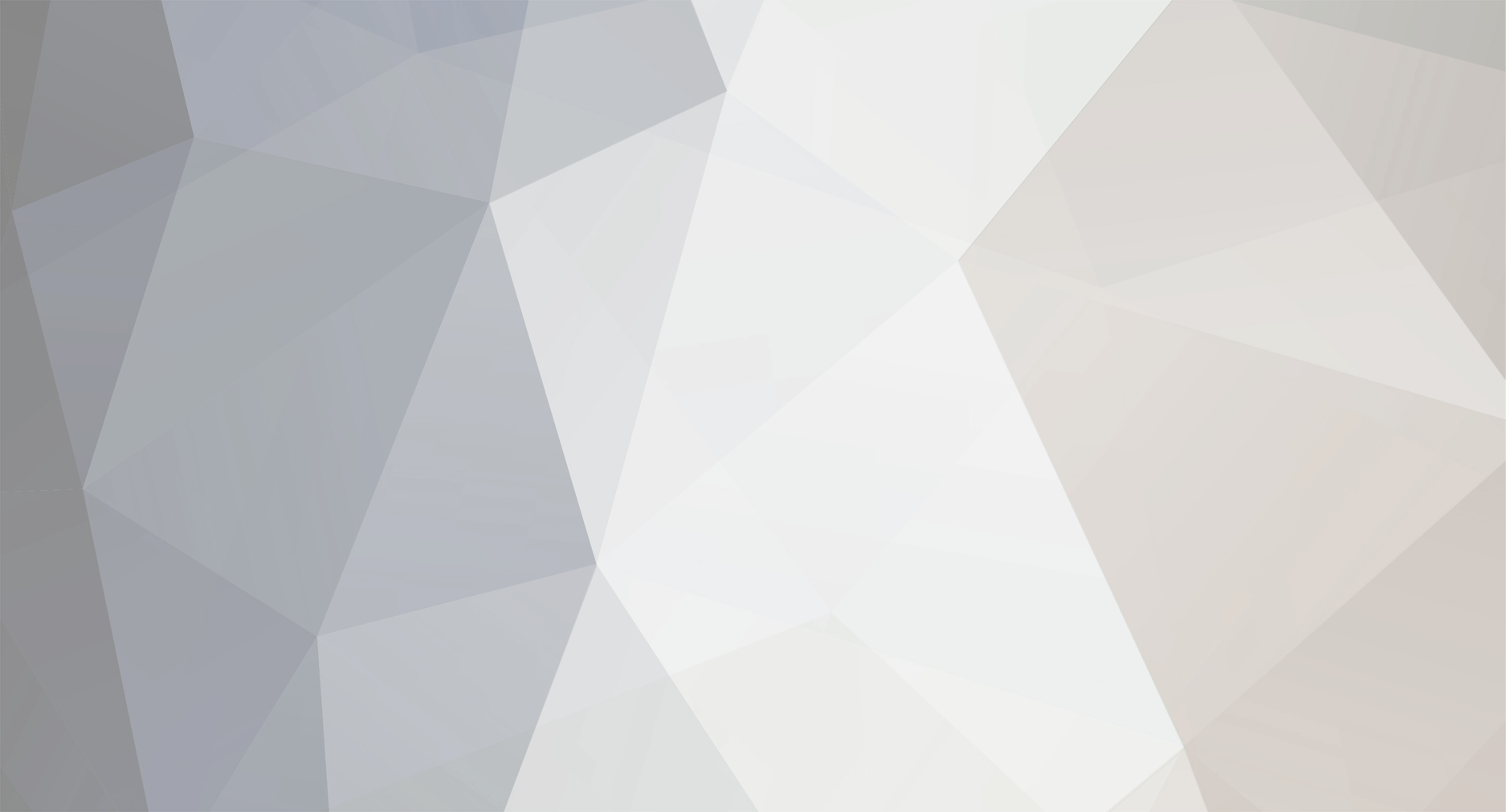
rwillett
⭐Supporting Member⭐-
Posts
1,496 -
Joined
-
Last visited
-
Days Won
5
Content Type
Profiles
Forums
Events
Shop
Articles
Everything posted by rwillett
-
Repairing screw holes in a guitar neck...
rwillett replied to rwillett's topic in Repairs and Technical
That sounds similar to what I read about the grain direction. Its not just cosmetic. I think the inserts are an easy fix. Other people seem to sell them as well, so it does appear to be a genuine solution https://graingerguitarparts.com/t/neck-ferrules--screws Thanks Rob -
Repairing screw holes in a guitar neck...
rwillett replied to rwillett's topic in Repairs and Technical
Thats a good idea, if I put the bolts through neck ferrules, then it spreads the load across the plywood back plane. -
Repairing screw holes in a guitar neck...
rwillett replied to rwillett's topic in Repairs and Technical
I thought the reason that the grain direction in the dowel to match the grain direction in the neck was due to strength, but that could be wrong. Rob -
Hi, I'm trying to reuse this Yamaha guitar neck on a 3D printed guitar. See below if you have interest in following my fumblings as I grope in the darkness to completion The current screw holes look slightly tatty, epsecially the two towards the tuners end of the neck. The heal screw holes look OK. I've been reading (or doing my own research as the flat earthers would say) about what to do. The general gist seems to be fill the tatty holes with the same material and wood glue. So hammer in small toothpick bits of maple and let it dry and then drill new screw holes. The neck appears to be maple according to https://www.axebition.com/electric-guitar/yamaha-rgx-121dm Somewhat surprisingly I don't have any maple dowels or offcuts lying around, PLA and PETG filament, yes, maple, no. So the question I have do I need maple or could I just use toothpicks and woodglue here? I do recall reading on here that people create dowel plugs that match the direction of the grain, is this necessary for this? Lots of questions and sadly not a clue from me Any help or advice welcomed. many thanks Rob
-
Day jobs pay the bills to allow me to play these sort of 3d printing games. If I relied on music to live, I'd be dead of cold and famine within two weeks Rob
-
Here's an example of how things can wrong. This is the bridge module that will hold a bridge (doh). It's designed for a Telecaster bridge and so it has three large holes in the recess to allow the bridge pickup screws to seat. That's all fine. However the back of the bridge (that's the blue area) doesn't go down to the very bottom of the module. It goes down 29mm and it should go down 44mm. There should be two rows of three screw holes for mounting purposes, however there is only one row. The module that connects to here has two rows and when I designed it, the bridge had two rows. Somewhere when I changed something, the back of the bridge 'lost' 15mm. It's trivial to just add 15mm back in, but I've got to go back and undo the screw holes (with embedded nuts in), and fix them OR I backtrack and workout what went wrong and fix it from some N steps ago, where N could be a very large number. The screw holes are important as this fixes everything together. I've gone over the top with screw holes as this is the first version and it's easier to remove them as it's too strong rather than go back and add them in. Thats my view anyway. These lost three screws may be wholly unimportant OR they may be critical. At this point in time. I've no idea so I err on the side of caution. 3D design is about telling a story and you have to get the steps in all the right place in the the right order. I seem to have a lost of page of the narrative and now have to work out how to recreate it. It could take me 10 mins or 2-3 hours to fix it. I alos have a day job to do which is nothing to do with this, so time is precious.
-
Loking for help on a Telecaster or similar....
rwillett replied to rwillett's topic in Other Instruments
No, No, No..... -
Loking for help on a Telecaster or similar....
rwillett replied to rwillett's topic in Other Instruments
I wish you hadn't posted that. Starts me thinking bad thoughts again. 😉 -
Loking for help on a Telecaster or similar....
rwillett replied to rwillett's topic in Other Instruments
I have donated the guitar kit build to the local music dept at the school. It's fine for kids to learn on and bash around. They were delighted to take it. I've now got a Yamaha neck. A 121DM neck which appears to be from the 90s. It's very thin and I'm 3d printing a body to fit it. You can see the thread here. -
It's not too expensive. 1kg of PETG or PLA is around £20. However special filaments can be a lot more. Simple things are cheap and easy. Ceiling roses are trivial to design and print. These modules are the most complex I have ever designed as: 1. There's a lot of them that have to fit together and each way they fit is unique. 2. How they bolt together is important. I don't want any screws or nuts to show. I keep saying I don't have OCD but I do wonder at times 😊 3. Access to the countersink screws using an Allen key is difficult. You have to think how long the Allen key is and how much rotation you can do. A 22mm long bolt will take a long time to screw in with a 30 degree movement. You only really find this out when you assemble things. I may have to put access holes in as it's so tricky and I don't want to do that. 4. I have a lot of embedded nuts that need to be put in. This requires every hole to be carefully designed to hold the nut. This means I have to stop the printer at certain layers to put the nuts in. If I leave it too long, the material cools down and this was probably the reason for the head crash. 5. It could also be because I'm using hardened steel nozzles as opposed to brass. Different thermal characteristics of temperature expansion of brass hot ends with steel Nozzles mean the nozzle can come loose. First job today is to replace the steel Nozzles back to brass. Then recalibrate the head level and start again. 6. The 3d design program is basically 3d maths. You build-up 2d sketches and then extrude the designs into 3d space. Some of the designs I have to 'manufacture' in the program. So you have to design and extrude and cut in a specific order to get the part you need. If you accidentally change something before these steps, it may go dramatically wrong or it might be a subtle error that you don't notice until you print or assemble. 7. I make mistakes. I forgot to put holes in to hold the pick guard so the work was useless anyway. There's a lot to remember. It's complicated at first but you learn as you go and build up the skills. I started at the beginning of lockdown and knew nothing. I had a cheap Ender 3 Pro off Amazon and built a CNC machine as pretty much my first project. All the hard design work had been done by somebody else. All I could design were simple cubes. I just kept learning and designing new stuff that got more and more complicated. It helps that I have a maths background and can think in 3 dimensions, probably due to the pure maths I did years ago. However you don't need to have these traits (not sure if they are skills), just practise and learn and except things will go wrong. I lost 16 hours of printing yesterday. That's across two printers, I'll lose more this week getting it right without a doubt. At first it's so frustrating, now I learn what went wrong, shrug my shoulders and start the following day. Hope this gives some clarity Rob
-
Are Reliced pedals a thing?
rwillett replied to Jean-Luc Pickguard's topic in eBay - Weird and Wonderful
A whole new market opens up. People will be acid dipping their Boss pedals and taking sandpaper to their Aguilers- 1 reply
-
- 1
-
-
Loking for help on a Telecaster or similar....
rwillett replied to rwillett's topic in Other Instruments
Well, my thoughts are 1. I'll wreck the neck. 2. I'll shave a lump of me down 3. It'll pop up and take my other eye out. My only decent one. 4. I might create a fire from doing it so fast and the garage burns down taking with it a row of Grade II listed cottages. 5. My insurance doesn't cover the above and I need to declare bankruptcy, my partner leaves me, takes the kids with her. I become destitute and end up living on the the streets eeking out a living on a scrappy three string bass, like Seasick Steve. -
And as I write this, I have a print head crash and have just lost 10 hours of printing on my bridge module. <sigh> Giving up for the night and going to coach Tri-Tigers girls U16 rugby union team. Big games against Liverpool St Helens on Sunday in Liverpool.
-
@Daz39 Short answer - No! Long answer A couple of reasons. 1. Holes are designed into a print. Where you see a hole, the slicing software generates extra layers around the hole. Drilling through doesn't do that. The inside of a print is air and plastic. If you drilled through it might work but its weak, but the second reason is.... 2. ... The hole contains an M3 square nut. You can see the outline in the picture below (as well as the wall layers in the hole). Plastic is not good to screw into, so I embed an M3 nut into stuff that joins together. Pulling bits of plastic together using an embedded nut, a metal bolt and plastic in between is fine. You can get quite a lot of tension before you crush the plastic. So every hole has to have the right length as the nuts are embedded. I could simply put a hole in and use a hex nut and a bolt. Dead easy, but it looks like sh1te. I do make drilling templates, so have made one for the plywood backbone, its no effort to drill through, but it simply doesn't work. Thanks Rob
-
The good news is that I have managed to work out where to put the output jack port, the bad news is that it's not a strat type port, there's not enough space. Perhaps Leo Fender knew this some 70 years ago This module has been very difficult to design. It has to bolt though to the bridge module but you don't have the hexacombs to get a bolt in. The bridge has no space either, so I ended up putting four big access holes in this module to allow me to screw things together. Also have to have a cut out for the control panel, routing ports from the neck pickup, and an output port, without it being solid and weighing a ton and taking a week to print. This is it on PrusaSlicer with a height of 32.6mm. Basically its a cut away You can see all the access slots and all the holes for embedded nuts. It's still missing the pickguard holes but this print run is to make sure it all fits. There will be another print run at higher quality and it'll be even longer There's 12 hours of printing there at 0.3mm qualify and 30% infill.
-
Just finished doing the neck pickup module. Looks really good, but I missed four screw mounting holes in the base of the module. Here they are highlighted in blue rings. The downside to 3d printing is that once its printed you can't go back and modify the print. With wood, you can keep modifying it until its right. 3d printing is very unforgiving. Took 60 secs to rectify but 8 hours of printing just down the drain.
-
ha ha, that made me laugh and I needed a laugh. I'm 3d printing a modular guitar body to hold a guitar neck, specifically a Yamaha 121DM, the controls of a telecaster/stratocaster (pickups, knobs etc). The idea is that I can change the pickups, controls and neck over as my whim takes me. This was brought about because I wanted a thin neck as my thumbs are knackered from rugby, my 89 Squier Telecaster has a weak neck pickup but lovely to play, I fancied a Tele that has humbuckers but wanted a thin neck etc etc. I want my cake and want to eat it. I was going to do a bass but the tension of the bass strings meant I thought I'd practise on a six string first. I do a lot of 3d printing so the design is done (more or less, still struggling with the output socket, I have a load of cheap bits picked up off fleaBay and am currently printing the bridge holder. This has been tailored for the cheap one I have. and the neck pickup module This leaves the five components below The various holes are mounting points for screws. There's about 30 hours of printing this lot still to go. The last piece will the bottom left one, as I'm trying to work out how to fit the output adaptor as I want it to be a strat type. I may have to give up that idea as I may not have the space. Rob
-
Turns out to be a thin Yamaha guitar neck.
-
Hi, I'm looking for a guitar neck plate for a 2nd hand guitar neck, specifically a Yamaha. Its quite a small plate and the gap between the screws doesn't fit any one I have. eBay has proved fruitless Not looking to spend a fortune here, but does anyone have any suggestions for companies or people who can machine one please? Thanks Rob
-
Something just turned up from the postie. Not sure what it is, perhaps a pick guard or perhaps a plectrum or two?
-
This is why 3d printing (and product design) can be so difficult The above shows a slot for an embedded M3 square nut with the screw channel running into it. I was out by around 0.3mm and it breaks the wall and compromises the strength of the part. Oh well, need to track it down and move it by a mm or two. It could be worse, I could have spent 20 hours printing it Rob
-
A load of Telecaster type parts have turned up. Further examination of the design, shows that the distance spacing between the hexagons wasn't enough to allow countersunk bolts and hidden nuts to smooth the design out. I want the design to be clean and fastenings to be as hidden as possible. This meant throwing away everything with a honeycomb and starting again. The joys of product design. Redone again and now printing the top left part at 0.2mm and 30% infill but with a lot of perimeter walls. This is 20 hours of printing and has circa 10 embedded nuts inside to screw things together. This allows it to be easily changed in the future. Here's in the cross sectional view in Fusion 360. The Telecaster Bridge will need far more design work now I have a telecaster bridge to use. The sketch at the left is the mounting hole for the guitar strap.
-
Is the bottom pickup something that powers most of the lights in North London or just local to you?
-
I have now taken a punt on a Yamaha neck, a separate punt on a Yamaha body (non working as it has no neck), some cheap Telecaster parts and some other odds and sods from eBay. Still would like a thin Squier or Fender Telecaster neck <hint hint santa> now printing off drill templates for the plywood backbone.