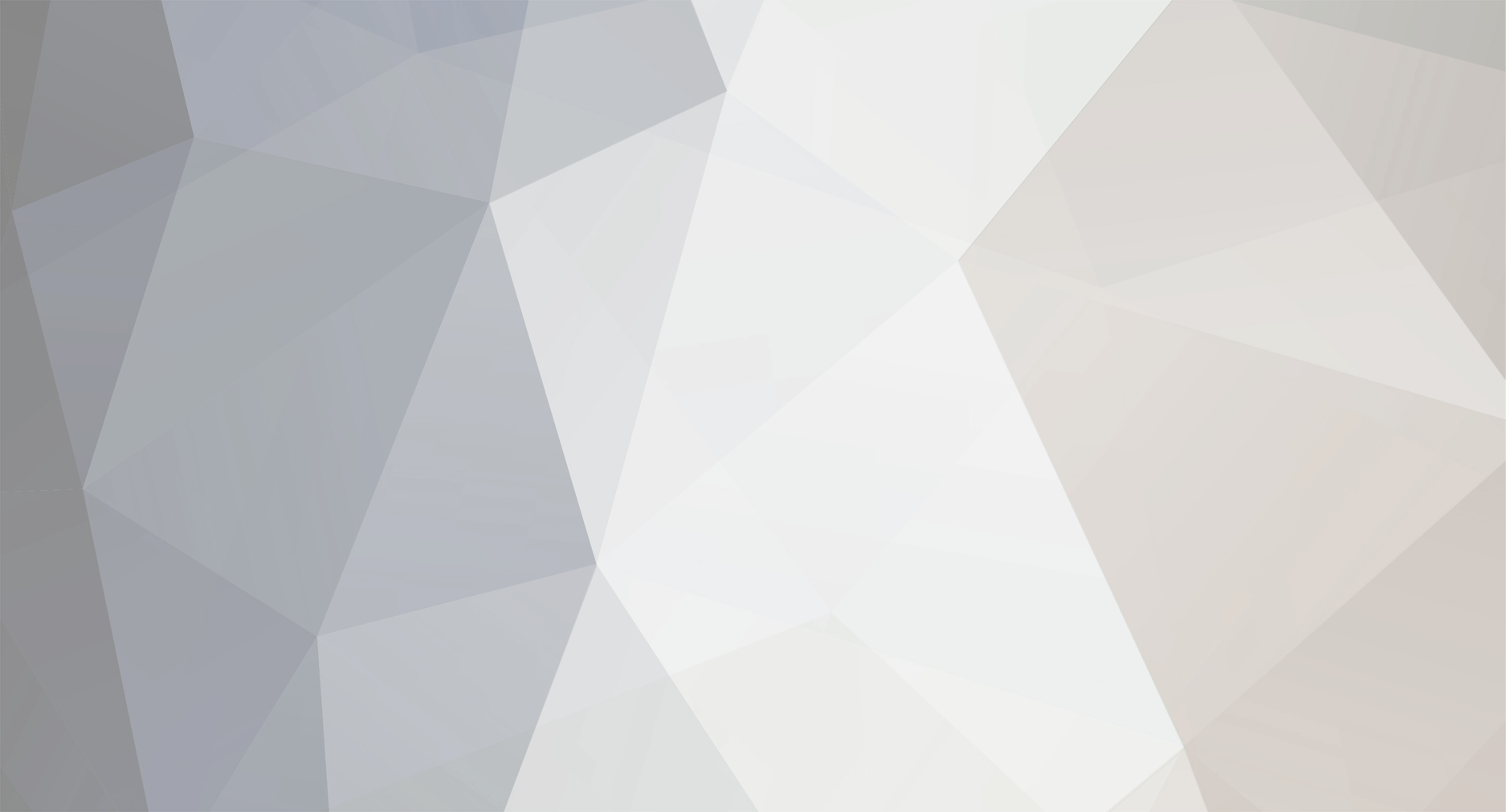
AlanP2008
Member-
Posts
83 -
Joined
-
Last visited
AlanP2008's Achievements
Rookie (2/14)
0
Total Watts
-
I'd say that if you can get rid of the problem by just operating it a few times, then do that and no more. The trouble is, the contact cleaner stuff tends to be addictive for pots. Pots usually have some form of viscous lubrication around the shaft, and using contact cleaner usually shifts this around, and a certain amount of it often ends up on the track - where it then starts collecting any dust that is going, which will straight away cause crackling again... (To start with, the track itself is usually clean and dry, just to avoid that very problem...) So IMHO, contact cleaner is best avoided unless it is the only way to cure the problem - but if it is, then fine (YMMV)... But you should then probably regard yourself as down-track towards actually replacing the pot... Alan edit: I've big issues with so-called "experts" in magazines who recommend a squirt of cleaner as "preventative maintenance", for the reasons above...
-
Remove the Head!...from an Ashdown combo?...
AlanP2008 replied to theFALLEN's topic in Amps and Cabs
[quote name='theFALLEN' post='803254' date='Apr 12 2010, 12:16 AM']Hi guys, Basically I am looking at removing the head from my Ashdown ABM500 EVO III 210 combo to use it with a different set of speaker combinations and I have some questions that I hope you can advise on. Firstly, is it difficult to remove a head from a combo casing? (guess that might be quite a subjective question) Secondly, is it difficult constructing a new amp housing? (i'm guessing that the head will be designed to go into a new "casing" rather than a rack) Any advice you give would be massively appreciated! Thanks dudes EDIT: Wasn't sure which forum this was supposed to go into, please be gentle...[/quote] As already said - 4 bolts through the top of the box - hidden under some plastic plugs. The amp in the combo is identical to the serarate heads, and I'm pretty sure that Ashdown would sell you an ABM or MAG sleeve, if that's the way you want to go. I've had a couple of issues I've taken up with them and they've allways been 100% helpful... Alan -
You are probably better off keeping the 2x10 vertical though - it will keep the dispersion more horizontal - help avoid the sound disappearing into the roof.... (Raise it by all means - although there are definitely benefits to keeping it on the floor, you being able to hear it whilst you are standing close to it, isn't one of them...) Alan
-
Absolutely buzzing - but not in a good way.
AlanP2008 replied to Owen's topic in Repairs and Technical
[quote name='owen' post='801298' date='Apr 9 2010, 09:52 PM']Now and again I do some work in a studio which is local to me. Like all of us I like to hear more of me than the communal foldback will allow me to have. I take a small mains powered desk with me, plug the cans feed into that as well as a link from the DI. I can then mix myself as loud as I like. Unfortunately this places a nasty buzz in other peoples cans. Is there some sort of isolatiing thingumywotsit-ma-bob I can get to make all this earth hum-ness go away?[/quote] This will be a good ole' earth loop problem. The most direct point to tackle this will be at the connection between the cans feed and your desk (although there will be other ways to approach it too). The problem is that the common/earth/screen wire on the cans cable is being connected to ground via your desk (and maybe via your DI cable as well - depending upon how that is organised). Without going in to why that is a problem, basically you need to break that ground connection. You could try simply disconnecting the screen on the cable you use from the cans socket to your desk - that is likely to stop the buzz in everybody else's cans, but might well end up with a worse buzz in your personal monitors. However - it might be just fine, so if "trial and error" is an option, you could try that first. A small improvement might be to use a small resistor - say 10ohms or so - instead of the original direct connection you just broke between the common/screen to your desk. That might be somewhat better, or might make no difference at all... You could try running the cans signal (signal and common) into a balanced mic input (+ and -, no connection to ground on the XLR pin 1) on your desk, but there is a good chance that the signal level will be too high, and you will need to pad it. You could try a 1k resistor in the signal lead to the + on the mic input, common to the - on the mic input, and a 100R resistor between + and -. That has an excellent chance of working - however, the odd possibility remains that the level of hum signal on the common of the cans feed is high enough to exceed the common-mode range of the mic amp input (these days, mic inputs are usually elecronically balanced, and such circuits do not have the common-mode range that a transformer-coupled input of old would have had). The final option then would be to use an isolating signal transformer between the cans feed and an unbalanced line-level input. This one: [url="http://www.maplin.co.uk/Module.aspx?ModuleNo=226569"]http://www.maplin.co.uk/Module.aspx?ModuleNo=226569[/url] is a stereo unit, and you would only need to use half of it. (You would probably need to make some adaptors for at least one of the phonos.) Hope this helps. Alan -
[quote name='chrisd24' post='798725' date='Apr 7 2010, 02:20 PM']Hmm seems to make sense then! i have a 12v amp but its mainly for a guitar as it sounds like a chorus of farts with a bass running through it! so is it possible with a different type of inverter then?[/quote] You should be fine with some kind of "pure sine wave" inverter. Most of the cheaper inverters produce square wave output, because it is easier and cheaper to do, and a lot of kit is pretty happy with that. However, there is a significant amount of stuff that needs a decent looking sine wave, and it sounds like your amp is in that class. The ironic thing is that a sine-wave inverter is itself somewhat like a power amp that runs off a 12V battery - you crank a small sine-wave up to 240VAC, then in your amp you transform it down to a lower AC voltage, rectifiy it, then use those volts to drive... a power amp... As an earlier poster said, an amp that runs directly off 12V (or whatever) would be a more efficient approach (most inverters *suck* amps from 12V in a alarming fashion), but an amp that produces, say 15W into 8R, will need +/- 18V or more (although a bridged pair of chip amps running off of two 12V batteries would work pretty well, it is diy stuff rather than off-the-shelf). I don't know if there is a bass player's version of the Roland Street Cube??? Yeah - a sine-wave inverter would probably be the easiest... Be nice to try-before-you-buy tho'. Alan
-
This idea of using super thick cable so that it will "take the power" is all in the mind of the beholder... ... you only have to look at the thickness of the wire used in the voicecoil itself to see how thick that needs to be - and that has to "take the power" too. As others have said, for the few feet of wire within the cab, wires pulled out from flexible mains cables is perfectly adequate. Alan
-
Options for wiring 2 pickups 2 volumes 2 tones?
AlanP2008 replied to richrips's topic in Repairs and Technical
Actually, looking at that diagram again, there is no *clear* connection (ground wire) between the body of the top pot and the body of the bottom pot - and there certainly should be... If there is foil on the back of the scratchplate, then that would probably serve to connect the boides of the pots together - but I wouldn't want to depend upon it, and I would certainly put an explicit ground wire in place... Hmmm... seeing the diagram like that, then it is easy to understand how a newbie might have problems re-wiring their bass. Anyone who had already done it a few times would add that wire without thinking about it - but a first-timer just wouldn't know to do that..... Alan -
Options for wiring 2 pickups 2 volumes 2 tones?
AlanP2008 replied to richrips's topic in Repairs and Technical
[quote name='richrips' post='795011' date='Apr 3 2010, 01:01 PM']Thanks obbm, that's a slightly different approach. Are there any other wildly different approaches out there? i'm keen to see if this can be done with no series resistors at all? cheers, rich[/quote] What obbm has shown you there is the "standard" way of wiring that setup. If you try to wire the volume pots in the same way as you would for a single volume pot setup - you will get exactly what you currently experience - big time interaction between the vol controls. Don't faff around with resistors - it won't work as well as this will. (There is a reason why Fender and others do it this way...) If you have separate tone & vol pots (rather than stacked, as in the diagram), then in the diagram, the vol port is the one "closest" to you (the "back" pot, as it were...) Alan -
[quote name='gafbass02' post='793219' date='Apr 1 2010, 12:50 PM']I've followed every diagram online, my father in law has tried too! It does somethnh different everytime!! But NOT the right thng! At the mo it's wired as per the fender diagram and the pots do nothing!??!?? There is a slight boost in volume halfway down the vol pots taper but that's it it sounds like I've wired to the jack but I havnt?!??!! Aaaaaaaarrrrrgggghhhhh it's a '96 squier nothing fancy pleeeeeeeeeease help me before it goes out the window, this thing has a mind of it's own! Two sets of pots tried, the pickup works, so WTF is going on??? Breath[/quote] If it is not getting quieter as you roll back the volume, make perfectly sure that you have grounded the "bottom" end of the pot (ie. connected it to the metal body of the pot, as that's usually where the ground connection is made). Check continuity with the jack plug screen with a meter if you have one - a battery and bulb if you don't (not while plugged in to the amp, obviously). Do you have any hum issues? If you do, that's a certain indication that the gounding is awry... Alan
-
[quote name='Oggy' post='792062' date='Mar 31 2010, 03:48 PM']Hi neepheid, The new bridge has arrived, nice chunky piece of kit. It came with the small key but the large one is nowhere to be seen – not a problem I have a key that will fit. I was thinking about one of the comments made regarding having the metal bridge in direct contact with the surface of the Bass. Do you think it would have a big effect on the overall tone / sustain if I were to sandwich a thin piece of felt between the underside of the bridge and the surface of the Bass? (Like a gasket) The two mounting bolts are pretty hefty affairs and I think would act as a good conductor of sound / vibration into the Bass without dampening the string vibration too much. I’m just thinking about protecting the Bass surface under the bridge. What are your thoughts? Oggy [/quote] I certainly wouldn't put anything there if I could possibly avoid it. The ideal bridge (IMHO) is light in mass, but extremely rigid (and rigid probably being the more important), so that vibrations from the string get passed into the body without let or hinderance. Putting felt between bridge and body would pretty certainly damp out a lot of what you really want to keep (and what you bought that bridge for...)
-
[quote name='Oggy' post='792062' date='Mar 31 2010, 03:48 PM']Hi neepheid, The new bridge has arrived, nice chunky piece of kit. It came with the small key but the large one is nowhere to be seen – not a problem I have a key that will fit. I was thinking about one of the comments made regarding having the metal bridge in direct contact with the surface of the Bass. Do you think it would have a big effect on the overall tone / sustain if I were to sandwich a thin piece of felt between the underside of the bridge and the surface of the Bass? (Like a gasket) The two mounting bolts are pretty hefty affairs and I think would act as a good conductor of sound / vibration into the Bass without dampening the string vibration too much. I’m just thinking about protecting the Bass surface under the bridge. What are your thoughts? Oggy [/quote] I certainly wouldn't put anything there if I could possibly avoid it. The ideal bridge (IMHO) is light in mass, but extremely rigid (and rigid probably being the more important), so that vibrations from the string get passed into the body without let or hinderance. Putting felt between bridge and body would pretty certainly damp out a lot of what you really want to keep (and what you bought that bridge for...)
-
[quote name='Toddy54' post='791481' date='Mar 31 2010, 05:45 AM']Many thanks for that, I will send him an email.[/quote] If it is a block of sliders (rather than just one), them most likely it is the circuitry behind them that is at fault (ie. a single fault affecting all of the controls, rather than the same problem with each one separately). Alan
-
[quote name='northstreet' post='770902' date='Mar 10 2010, 08:42 PM']Wondered if anyone can identify the likely cause of a problem with my amp. As briefly as possible - I buy a brand new Hartke LH500 and plug it into my (used) Hartke VX115 cab. Straight away I notice an unusual noise. As I strike a note I get a noise the cab that sounds just like a 'tick'. It's only at the start of the note, on the lower strings, with the volume & bass EQ up (but not excessively so), and when the amp's warmed up. The tick volume doesn't appear to depend on how loud the amp is - I can drown it if I play loud enough. I don't have other bits of kit to find out whether it's amp or cab, but I get the same noise with different basses. Now I know should have done something about it straight away, but soon after I used the rig at a gig and blew up the speaker. In goes a brand new Eminence Kappa Pro, but the noise is still there. So it must be the amp. Back it goes to the shop, and it comes back noise free. Hurrah. Now, I played a gig last weekend for the first time with the repaired amp, and at the end the noise is back. Grrrrrrr. So I'm taking it back to the shop at the weekend. But, if I had some idea what the problem was, I reckon I'll have more chance of getting it sorted properly (always works for me with car repairs). So is there anyone out there who has any ideas what could be wrong? Thank guys.[/quote] It is possible that the blown speaker and the ticking are completely unrelated. You might look for any airleaks (ok, I don't know whether this is a sealed cab, or ported - if ported, then ignore this comment). You might pull out the speaker and see if the internal wiring is touching the back of the cone anywhere, then check for any other loose components or "stuff" inside. You might check to see if it has been dropped, and sprung a joint or seam somewhere - is the baffle securely attached? There is reallly a limit to what it actually might be in a speaker cab - you'd like to think you could find it just by looking around, inside and out. Best of luck. Alan
-
Any idea whats wrong with my ABM Combo?
AlanP2008 replied to HarryPotter's topic in Repairs and Technical
[quote name='HarryPotter' post='784993' date='Mar 24 2010, 06:55 PM']Bit of an update and a result - spoke with Ashdown, carried out all the checks they asked me to, they decided it was broken, and although out of warranty they would repair it gratis as a good will gesture, all I had to do was ship it to them. Sent it to them Thursday, they got it Friday, I got it back Today. They'd replaced the rear PCB as it was faulty (and they have, the Speakons are diff colours and the board looks different). Works fine, fingers crossed its 'fixed' for good now. Another good result for Ashdown Customer service.[/quote] That's about as good as it gets... -
Help needed with Ashdown Electric Blue!!!
AlanP2008 replied to 40hz's topic in Repairs and Technical
[quote name='Protium' post='783696' date='Mar 23 2010, 05:15 PM']I really wouldn't know sorry, your best bet is to ask Ashdown again though they probably won't be able to quote you without knowing the exact problem.[/quote] In all probability it is the power transformer itself. I had to replace one on a Mag 400 (with identical symptoms - although it is not impossible that the troubles may run a little deeper than just the trafo...) The transformer itself was about £80 from Ashdown, and is easy to fit if you know your onions - if not, definately ship the Amp to Ashdown or to a good Amp tech (in which case there will be shipping and labour involved....) You might be able to ship just the amp chassis by itself (for the sake of pulling four bolts), which should save a few pennies - but talk to Ashdown, their tech support is responsive and very helpful.